75 Gallon Hop Back
A 75 gallon hop back is a key piece of equipment used in the beer brewing process to infuse hop aromas and flavors into beer. It is placed after the brew kettle to filter and infuse wort with hop oils and resins as the hot wort passes through a bed of whole leaf or pelletized hops on its way to fermentation.
75 Gallon Hop Back Equipment Guide
Equipment Type | Hop Back |
---|---|
Purpose | Add hop aroma and flavor to beer through hop steeping |
Placement in Brewery | After the brew kettle, before fermentation tanks |
Typical Capacity | 75 gallons |
Construction | Stainless Steel |
Customization | Fully customizable dimensions, fittings, sight glasses, accessories |
Brewing Process with Hop Back
The 75 gallon hop back is used after the wort has been boiled and cooled down slightly from boiling point. The near-boiling wort is then transferred from the brew kettle into the hop back filled with whole leaf or pellet hops for steeping. This steeping process infuses the wort with delicate hop oils and resins while filtering out proteins and coagulants. The infused wort is then pumped to fermentation tanks for the next phase of beer production. Using a hop back ensures maximum hop utilization as compared to kettle hopping or dry hopping methods. It allows brewers to obtain desired hoppy flavors and aromas accurately and efficiently.
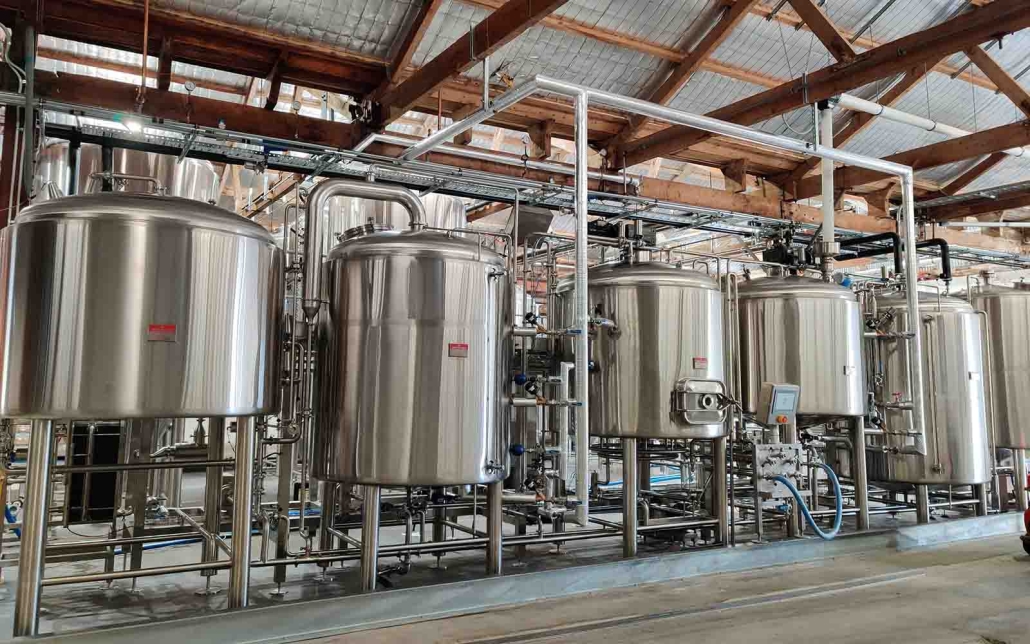
75 Gallon Hop Back Design and Customization
Parameter | Options |
---|---|
Dimensions | 2-4 feet diameter, 5-7 feet tall |
Chamber Material | Stainless Steel, Copper |
Hop Container | Stainless steel mesh cylinder with sealable openings |
Fittings & Connections | TC fittings, Tri-clamp, unions, flanged |
Sight Glasses | Single, double sight glasses |
Accessories | Casters, inlet valve, sample port, cleaning hooks |
Customization | Fully customize dimensions, capacity, accessories as per brewery requirements |
Professional breweries can get fully customized 75 gallon hop back systems designed as per their exact brew house layout, space constraints and production needs. Custom features like double isolation jackets, dual sight glasses, aseptic sample ports, CIP spray balls can be incorporated. Cylindrical and rectangular forms are both available. Portability is enabled by optional casters. They can be designed as stand-alone vessels or integrated into a brew house.
75 Gallon Hop Back Suppliers and Pricing
Manufacturer | Price Range |
---|---|
JV Northwest | $8,000 – $11,000 |
Rolec Craft Brewing | $7,500 – $10,000 |
SS Brewtech | $9,500 – $12,500 |
Spike Brewing | $8,800 – $11,500 |
Ss Northern | $7,000 – $9,000 |
Pricing varies based on material grades, customization features, quality of welding and fabrication. Budget oriented China made all stainless steel hop backs start around $7000. American or German-made systems with higher end stainless steel grades range from $9000 to $12,500. Copper hop back with stainless fittings cost more. Additional charges apply for custom dimensions, fittings, accessories.
75 Gallon Hop Back Installation, Operation and Maintenance
Activity | Guidelines |
---|---|
Installation | Install securely on stable platform Connect to brew kettle with TC/tri-clamp fittings Connect output to fermentor inlet |
Filling | Fill hop basket to rim with whole leaf or pellet hops 400-800 grams per 75 gallon batch |
Process | Start recirculation when wort temp nears 170F Recirculate for 10-30 mins till hop flavor/aroma satisfaction Drain out steeped wort to fermentor |
Cleaning | Rinse with hot water after use Fill with caustic solution for overnight soak Rinse thoroughly before next use |
Maintenance | Inspect fittings, gaskets, seals periodically Replace worn out parts Check sight glass condition |
Proper cleaning and sanitation practices should be followed before and after each use to maintain hygiene and prevent growth of spoilage organisms inside the vessels over repeated usage, which can lead to contamination of beer batches.
How to Choose the Right 75 Gallon Hop Back
Criteria | Evaluation Aspects |
---|---|
Brewery Requirements | Expected production volume Floor space and layout Future expansion plans |
Build Quality | Material grade – 304 or 316 stainless steel Quality of welding and finishing Hygienic internal surface |
Feature Set | Dimensions, capacity Accessories – sight glass, sample port Modularity, ease of cleaning |
Budget | Compare pricing of basic systems vs premium grades and customization charges |
Manufacturer Reputation | Brewing industry experience Quality and reliability Warranties and service |
Professional breweries must assess their production goals, available space, budgets and in-house expertise before deciding which system configuration and supplier is ideal for their needs. Modular designs allow upgrading components like heating elements and filtration systems if needed later.
Pros and Cons of 75 Gallon Hop Back
Pros | Cons |
---|---|
Adds prominent hop flavor efficiently | Relatively expensive equipment |
Retains volatile essential oils lost in kettle hopping | Need for whole leaf hops increases raw material costs |
Isothermic design prevents degradation of aromas | Additional temperature control requirements |
Filters coagulants and proteins | Separate cleaning and sanitation requirements |
Compact and modular | Maintenance costs for gaskets, seals etc |
Fully customizable | Potential clogging issues |
The pros of excellent hop utilization and aroma/flavor precision justify the costs of buying and operating a hop back system for commercial scale 20-100 BBL breweries seeking signature hop forward beer styles. Homebrewers may find the equipment cost prohibitive.
FAQ
Q: What types of hops are best suited for hop back utilization?
A: Low cohumulone, aromatic varietals like Willamette, Saaz, Hallertau, Tettnanger, and New Zealand hops. High oil content supports efficient extraction.
Q: Does hot side hopping use more hops than hop backs?
A: No, hop back allows favorable oil extraction with lower hop weights due to full wort contact. 1.5-3 lbs per BBL is sufficient compared to kettle hopping.
Q: How long can hops remain in the hop back?
A: 10-20 minutes of contact time. Beyond 30 minutes risks undesirable polyphenol and tannin extraction affecting flavor.
Q: What maintenance is required on hop backs?
A: Gaskets, sealing surfaces should be inspected every 50 cycles or so. Replacement every 100 cycles ensures integrity and prevents leaks or contamination.
Q: Is it necessary to fill hop basket fully for every use?
A: Yes, it maximizes diffusion surface area for essential oil transfer. Voids can create preferential flow paths affecting overall utilization.