Overview of 100 Gallon Hopback
A hopback is a vessel used in brewing to filter hops and trub out of wort after the boil kettle and before fermentation. It serves as a settling tank to remove solids before the heat exchanger or chiller. A 100 gallon hopback has higher capacity for larger scale commercial brewing operations producing greater volumes of beer.
100 Gallon Hopback Equipment Guide
Equipment Type | Details |
---|---|
Hopback | Vessel used after the brew kettle to filter hops and sediment from hot wort before the heat exchanger |
Capacity | Typically 100 gallons for high volume commercial brewing |
Construction Material | Stainless steel for durability and cleaning |
Design | Cylindrical or rectangular, vertical orientation, cone bottom design allows trub to settle |
Features | Inlet and outlet connections, sight glasses, thermometer, pressure relief valve |
Optional Accessories | Spray ball CIP system, legs/casters, insulation jacket |

Types of 100 Gallon Hopbacks
There are a few design variants of 100 gallon hopbacks to consider:
Cylindrical: Classic vertical cylinder shape allows even flow distribution and sedimentation
Rectangular: Squarer tank can fit better in tight spaces but flow is not as uniform
Conical Bottom: Angled cone bottom enables easier trub removal compared to flat bottom
Closed Transfer: Special valves and ports enable closed, oxygen-free transfers to fermenter
Jacketed: Insulated outer shell allows precise temperature control with a heating/cooling jacket
Custom Fabricated: Many suppliers offer full customization of dimensions and features
100 Gallon Hopback Spaces and Sizing
Properly sizing your hopback will ensure it meets production goals.
Parameter | Details |
---|---|
Batch Size | Accommodate single batch volumes from the boil kettle; from 50-100 gallons is common |
Height/Diameter Ratio | Around 2:1 ratio for proper sedimentation |
Floor Space Needed | Approximately 4 ft x 4 ft footprint |
Vertical Clearance | Allow 7-8 ft overhead room for installation and operation |
Weight When Full | Up to 900 lb including liquid weight at 8.3 lb/gallon |
Connections | 1.5” – 2” tri-clamp connections to boil kettle, chiller lines |
100 Gallon Hopback Design and Customization
A hopback is a relatively simple cylindrical or rectangular vessel, but variables in design and functionality impact performance.
Parameters | Options | Factors to Consider |
---|---|---|
Construction | Stainless steel, aluminum | Stainless best for cleaning, durability, acid resistance |
Shape | Horizontal, vertical, rectangular, cylindrical | Vertical best for sedimentation; match kettle shape |
Fabrication | Welded, passivated | Smooth polished welds prevent bacterial collection |
Dimensions | Custom or standard sizing | Match volume; stabilize height:diameter for trub settling |
Drain Configuration | Cone or slope bottom, side drain port, racking arm | Cone bottom with center drain port ideal for trub |
Port Connections | Tri-clamp, threaded, flanged | Tri-clamp best for modular breweries,easy cleaning |
Layout | Stand-alone, inline, under brew deck | Deck integration saves space but reduces access |
Insulation | Jacketed design, steam, glycol | Improves temperature control to avoid cold side oxidation |
Configuring a Commercial 100 Gallon Hopback System
Commercial hopbacks are part of an end-to-end brewhouse system. Proper configuration ensures smooth wort transfer and production scale.
Brewing Equipment | Function With Hopback |
---|---|
Boil/Kettle | Hopped wort feedstock enters from the kettle |
Whirlpool Outlet | Optional entry point for wort depending on whirlpool usage |
Inlet Controls | Valves to regulate wort flowrate into hopback |
Sight Glass | View trub levels for drainage timing |
Outlet/Drain Port | Tri-clamp for connecting to heat exchanger or chiller |
Cleaning/Draining | Remove trub through bottom drain after batches |
Temperature Gauge | Monitor if uninsulated to avoid cold-side oxidation |
Glycol/Steam Jacket | Maintain precise temperatures for cold side transfers |
casters | Enable mobility for cleaning if jacket is not in place |
Properly integrating a hopback into the overall brewing line is critical for smooth operations and preventing downstream issues. Consulting with the manufacturer’s engineering team is advisable during the design phase.
Suppliers of 100 Gallon Hopbacks
Many brewing equipment OEMs offer standard or customizable hopback vessels across a range of capacities. Prices vary based on dimensions, materials, and features.
Company | Base Price Range | Offerings |
---|---|---|
JV Northwest | $6,500-$9,500 | Standard cylindrical & rectangular |
Spike Brewing | $7,900-$10,500 | Conical and custom options |
SS Brewtech | $7,800-$15,000 | Uni-shape, jacketed, custom |
Premier Stainless | $10,000-$30,000 | Square & cylindrical; wide customization |
Brewery Supplies Group | $8,000-$15,000 | Standard & heavy duty available |
In addition to commercial vendors, many breweries work with local metal fabrication shops to create fully customized hopback vessels. Prices will vary more widely based on specifications. Expect to pay $15,000+ for heavy duty designs with exotic alloys and precise fabrication.
Installation, Operation, and Maintenance of Hopbacks
Function | Key Activities | Frequency |
---|---|---|
Installation | Position hopback inline after boil kettle/whirlpool Connect inlet/outlet to valves and lines Test fittings for leaks with water | One-time setup activity |
Operation | Monitor sight glass and sample valve for trub buildup When clear, open outlet valve to transfer wort forward Potentially activate a spray nozzle to dislodge particulates if needed | Each batch/brew day |
Cleaning (CIP) | Fill with cleaner solution and agitate Use spray nozzle and recirculation pump Push cleaner through all ports | Weekly or as needed if buildup occurs |
Inspection | Check all sight glasses, valves, gaskets for wear/cracks Ensure smooth interior welds | Annual |
Maintenance | Lubricate valves; replace gaskets/seals Repair worn surfaces or fittings | As needed |
Calibration | Use sight glass markings to confirm volume Calibrate temperature and pressure sensors | Semi-annual |
Thorough cleaning and avoiding abrasion of the polished interior will maximize lifespan. Many parts are modular for easy replacement and manufacturers provide repair services.
Choosing a Commercial Hopback Supplier
With custom fabrication shops as well as vendors providing hopbacks across a wide range of configurations and budgets, selecting the ideal partner involves both technical compatibility and service factors:
Evaluation Criteria | Key Considerations |
---|---|
Technical Factors | Construction material quality and compatibility Dimensioning matches brewery scale and batches Port sizes/types integrate with existing equipment Offer full customization services |
Quality and Testing | Use proper welding methods; pressure test vessel |
Configurability | Support wide range of dimensions, connections, fittings, accessories |
Business Factors | Reasonable pricing for required customizations Responsive sales and engineering team Positive reputation based on client references |
Services | Provide installation assistance and operator training Offer ongoing maintenance and repair services |
Vetting multiple vendors using the above framework can help identify the right fit based on both brewery integration needs and long term service requirements.
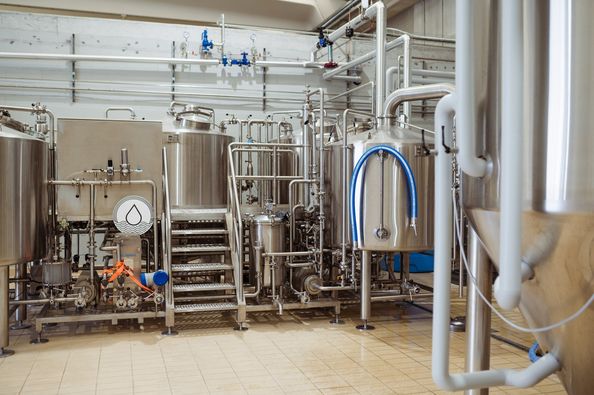
Comparing Pros and Cons of Hopback Options
Type | Advantages | Disadvantages |
---|---|---|
Cylindrical | Even sedimentation from circular flow | Limited rectangular customization |
Conical Bottom | Trub stacks for easy draining | More expensive than flat bottom |
Jacketed | Excellent temperature control | Added cost and complexity |
Bottom Drain | No need to open lid for trub removal | Can clog more easily than side port |
Casters | Portable flexibility for cleaning | Stability issues if not locked during operations |
Steam Heating | Uses readily available steam | Lacks precise control of glycol systems |
External Spray Ball | Powerful CIP cleaning | Another piece requiring maintenance |
Understanding these types of trade-offs allows configuring a balanced system matching functional priorities to the brewery’s budget. The wide range of potential accessories enables precise customization for production environment and work styles.
FAQ
What are the key differences when upgrading from a 50 gallon to 100 gallon hopback?
The main differences come down to capacity, size/weight, design constraints, and integration complexity. A 100 gallon hopback requires more vertical space, stronger structural support and connections for 2-3X weight when full, 1.5″ – 2″ ports to handle higher flow rates, and better pumping systems and controls to manage the batches.
How can I calculate the proper height:diameter ratio when custom sizing a hopback?
As a rule of thumb, use a height:diameter ratio between 2:1 and 3:1. The taller and narrower the cylinder, the more vertical room for trub to settle downward. A short wide hopback will need strong inlet flow or a raking system to prevent solids from accumulating on the sides.
Should I invest in an expensive glycol jacket or external insulation?
It depends on your climate conditions, fermentation requirements, and budget. Glycol enables dialing in precise temperatures, while insulation is cheaper but lacks precision. If you need to cool wort to pitching temps, glycol is worth it. Otherwise, insulation suffices for most small scale breweries simply avoiding cold-side oxidation.
What are the signs that wear parts like valves or seals need replacement?
Keep an eye out for wort leaks or drips, which indicate a worn gasket. Valves that become difficult to operate or need excessive force likely have internal issues. If you notice cloudier wort transfers or decreased bitterness, worn valves/seals could be allowing hop particles and sediment to pass through. Replacing regularly is good preventive maintenance.