2 BBL Brewhouse Brewing Systems
A 2 barrel (BBL) brewhouse is a common small-scale commercial brewing system with a capacity of about 250 liters or 66 gallons per batch. 2 BBL systems are popular for nano and microbreweries looking to produce craft beer on a pilot system before scaling up. This article provides a complete guide to 2 BBL brewhouses including types of systems, design considerations, sizing calculations, equipment sourcing, installation, operation, maintenance and more.
Types of 2 BBL Brewhouse Systems
Type | Description |
---|---|
Turnkey | Pre-designed, pre-fabricated brewhouse unit with all vessels and piping integrated |
Modular | Customizable brewhouse with ability to select individual vessels and layout |
Electric | Heating elements used to heat water and wort |
Gas-Fired | Uses natural gas burner for heating |
Steam-Jacketed | Steam circulated through jackets on vessels for heating |
Direct-Fire | Burner fires directly into kettle bottom for heating |
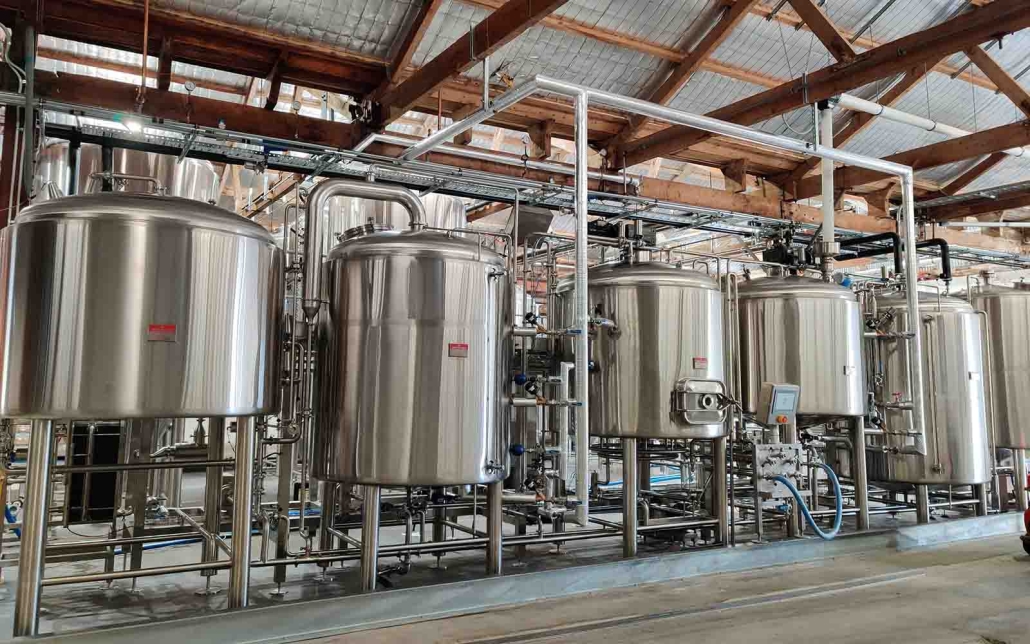
2 BBL Brewhouse Sizing Considerations
When selecting a 2 BBL brewhouse system, it is important to consider sizing based on required batch size, production volume and growth plans. Key factors influencing sizing:
- Target batch size – 2 BBL (250 liters or 66 gallons) is a typical small pilot system size
- Annual production capacity needed – number of batches per week/month/year
- Peak demand capacity – maximum batches per day/week
- Space available – floorspace and height
- Growth plans – Size for current needs or leave room to scale up later
Appropriately sizing the system is crucial to avoid losing capability or requiring expensive retrofits later. An adjustable, modular brewhouse allows starting small and adding tanks/vessels as needed.
2 BBL Brewhouse Vessels and Components
A complete 2 BBL brewhouse features multiple vessels and components for moving, heating and processing water, malt, hops and yeast to produce crafted beer.
Vessel/Component | Function |
---|---|
Mash tun | Mixes hot water with milled grains to extract sugars |
Lauter tun | Separates sweet wort from spent grains |
Brew kettle | Boils wort with hops for aroma and bitterness |
Whirlpool | Settles hops and coagulants via swirling flow |
Heat exchanger | Cools hot wort quickly before fermentation |
Fermenter | Allows yeast to convert sugars into alcohol and CO2 |
Brite tank | Carbonates, clarifies and stores beer |
Piping | Transfers liquids between vessels |
Pumps | Moves liquids through pipes |
Valves and fittings | Controls flow and connections |
Control panel | Allows automated or manual operation |
Gauges and sensors | Monitor process parameters – temperature, pH, density, flow |
Grain mill | Crushes malt into grist for mashing |
Keg washer | Cleans and sanitizes kegs |
Chiller | Cools water and wort |
2 BBL Brewhouse Design and Layout
Proper brewhouse design focuses on an ergonomic layout for operational efficiency. Considerations include:
- Logical flow from raw materials to finished product
- Gravity fall between vessels where possible to reduce pumps
- Easy access for cleaning and maintenance
- Compact footprint to minimize floorspace
- Future expandability and flexibility
- Operator safety
Both linear layouts with vessels in a row and compact configurations with stacked vessels are common for 2 BBL systems. Breweries often utilize an equipment supplier to custom design and build a brewhouse for their facility, objectives and budget.
Customization of 2 BBL Brewhouse Systems
While pre-made turnkey brewhouse units offer simplicity, many brewers opt to customize components for unique flexibility:
- Select individual vessels from different suppliers
- Choose custom materials – stainless steel, copper, wood
- Integrate proprietary heating and cooling methods
- Design personalized pipework and layout
- Specify precise vessel sizes and dimensions
- Add specialized vessels like hybrid mash/lauter tuns
- Integrate advanced automation and controls
- Scale up/down vessel capacities for future growth
Completely customized, modular brewhouses allow brewers to differentiate through personalized equipment innovations. However they require more complex integration and testing. Turnkey systems offer streamlined implementation while limiting uniqueness. Most brewers choose a hybrid approach for balance.
Sourcing 2 BBL Brewhouse Systems
Many equipment manufacturers offer standardized and customized 2 BBL brewhouse solutions:
Company | Price Range | Offerings |
---|---|---|
Brewmation | $100,000-$350,000 | Turnkey electric and gas brewhouses |
Specific Mechanical | $150,000-$500,000 | Customizable modular brewhouses |
JV Northwest | $200,000-$450,000 | Configurable 3-vessel and 4-vessel systems |
AME | $250,000-$750,000 | Highly customized modular brewhouses |
Premier Stainless | $300,000-$1,000,000 | Custom fabrications from scratch |
Budget modular imported systems from China are available from $50,000 but may have quality issues. Explore all available options before selecting a system and suppliers for best value. Get references on manufacturers before placing an order.
Installing 2 BBL Brewhouse Systems
Proper equipment installation ensures safety, performance, efficiency and reliability:
- Review equipment drawings and manuals
- Check electrical, gas and utility requirements beforehand
- Handle vessels carefully to avoid any damage during transport and unloading using cranes/forklifts
- Set up suitable staging area and cleared route for moving equipment in place
- Ensure adequate floor thickness and drain slope; consider steel base for heavy vessels
- Retain specialist personnel for tricky rigging, connections and alignment
- Connect vessels per process flow diagrams and verifyOrientation and access
- Performpressure, leak and continuity tests on all piping and vessels
- Initialize and configure control systems and automation
- Test heating, cooling, pumping and flows with water batches
Budget 10-15% of system cost for complications requiring adjustments during installation and commissioning.
Operating 2 BBL Brewhouse Systems
Efficient operations of a 2 BBL brew system involves:
- Understand vessels/components functions and process sequence
- Follow safety procedures – PPE, confined space access, electrical safeguards
- Handle grains, adjuncts, spices, fruits; mill and weighout
- Mix mash and lauter wort, sparge grains, transfer to kettle
- Boil wortm add hops and ingredients per recipe timing
- Monitor/control temperatures, pumps, valves and flows
- Adjust steps based on measurements and visual observation
- Perform whirlpool, knockout, cooling, aeration, pitching
- Sanitize all equipment before and after use
- Track batch progress in brew logs
- Adhere to maintenance schedule – gaskets, fluids, lubrication, cleaning
- Utilize operating manuals and procedures
Adequate operator training and documented standard operating procedures are vital for repeatable quality and efficiency.
Maintaining 2 BBL Brewhouse Systems
Preventative maintenance protects system health, improves longevity and reduces downtime risks:
- Daily cleanup – rinse, flush all vessels; inspect for leaks
- Weekly – lubricate pumps/motors/bearings if needed
- Monthly – inspect/replace gaskets; verify calibration
- Quarterly/Biannual – full system audit, parts replacement
- Annual vessel inspection – x-ray for pitting/decay signs
In addition to above schedule:
- Immediately address leaks or unusual performance
- Record equipment runtime hour meters to assess wear
- Keep spare parts like seals, valves, hoses in stock
- Topup fluids – glycol, lubricants, hydraulic oils
- Descale as needed based on water chemistry
The brewhouse is the heart of any brewery. Take actions to maximize uptime and utilize warranties.
Key Considerations When Selecting a 2 BBL Brewhouse Supplier
Parameter | Description |
---|---|
Build quality | Use certified vessels; avoid thin/inferior metals |
Layout experience | Design ergonomic, efficient brewhouse layouts |
Process expertise | Understand subtleties of brewing methods |
Customization skills | Offer adaptable options and customization |
Control systems | Automated recipe programming and batch control |
Pricing | Competitive budgetary quotes and transparency |
Lead time | Swift fabrication and delivery of system |
Shipping process | Careful handling and responsiveness |
Installation support | On-site guidance for setup, calibration, testing |
Documentation | Provide diagrams, manuals, part lists |
Local presence | Closer support for supplies, service and warranty |
Brewing experience | Actually make good beer at commercial scale |
References | Multiple positive tester feedback |
Service record | Responsive support issues over long equipment lifetime |
Financial stability | Avoid vendors at risk of shutting down suddenly |
Thoroughly vet all prospective vendors across these aspects before ordering a system. Prioritize customization range, reliability and responsive support.
Comparing Pros and Cons of 2 BBL Electric vs Gas Brewhouse Systems
Parameter | Electric Brewhouse | Gas Brewhouse |
---|---|---|
Initial cost | Lower capital cost | Higher base price for burner |
Operating Cost | Higher electicity usage cost | Lower gas energy costs in most markets |
Heating Speed | Slower heating times | Very high intensity for rapid boiling |
Temperature Precision | More even, precise heating control | Higher variability with fluctuating flame |
Automation Capability | Integrates well with automated control systems | Requires specialized burner automation |
Safety considerations | Avoid electric shock hazards | Gas burner hazards requiring special operator care |
Maintenance needs | Elements replacement; minimal moving parts | Annual gas line and burner tuning/servicing |
Location flexibility | Requires adequate electrical supply; typically indoor use | Outdoor installations possible with sufficient ventilation and fire suppression; Gas supply required nearby |
Environment friendliness | Carbon-neutral if powered by renewable electricity | Carbon emissions from gas combustion; more emissions and permit considerations |
Cleanliness | No combustion particulates or exhaust fumes | Exhaust gases must be properly handled |
Noise | Quieter operation | Gas combustion noise may require mufflers |
Staff training | Simpler operator skill requirements | Special handling of gas systems and emissions permits increases training needs |
Evaluate all these factors including energy costs, production scale, location, and expansion plans when selecting electric vs gas heating.
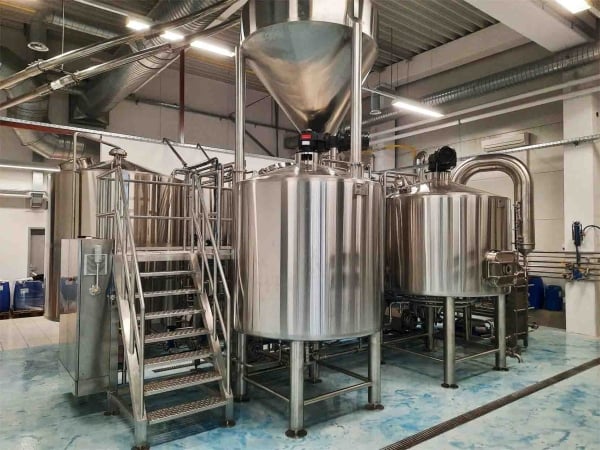
FAQ
Q: What size brewhouse do I need for a microbrewery?
A: For a smaller microbrewery with annual production under 1000 BBL, a 1-3 BBL pilot scale brewhouse is typical for cost-effectiveness. A 2 BBL system producing 250 liters (66 gallons) per batch is popular size choice in this range.
Q: How much space does a 2bbl brewhouse system require?
A: Plan for roughly a 20ft x 15ft area for a basic 2bbl brewhouse system with 3-4 vessels in linear configuration. Compact stacked systems can fit in 10ft x 15ft. Remember to account for adequate operator workspace, access paths and future expansion.
Q: How much beer can you produce on a 2 BBL system?
A: With 100% utilization a 2 BBL brewhouse can produce 500 BBL annually running 5 batches per week. Realistically expect 300-400 BBL yearly accounting for maintenance, sharing vessels across beers and human factors. Plan to scale up by adding fermenters and brite tanks as needed.
Q: What temperature can a 2bbl electric brew house achieve?
A: Electric 2bbl brew kettles can reach boiling temperature of 210-212°F (100 C) needed for hopped wort using 5500-7500W elements. If higher mash or heating temperatures are desired, consider upgrading element wattages and using supplemental steam/gas heating.
Q: How much does it cost to build a 2bbl brewery?
A: A new basic 2BBL brewhouse system costs $100,000 – $350,000. Budget $50-100k additionally for fermenters/brites/glycol plus $100-300k for the taproom. Other expenses include rent, labor, raw materials, permitting , marketing etc. So plan for around $750k total to build a functional microbrewery.
Q: What is the difference between 1BBL and 2BBL brewing systems?
A: 1BBL brewhouses produce 30-40 gallons per batch while 2BBL systems produce 60-80 gallons per batch. 2BBL systems offer economy of scale benefits for established microbreweries graduating from pilot systems. However they require more space, energy and labor. Evaluate budget and production goals before choosing between 1 vs 2BBL sizes.