Brewery Fermentation Tanks
Overview
Welcome to the fascinating world of brewery fermentation tanks! If you’re curious about how your favorite beer gets its distinctive flavor and aroma, you’re in the right place. Fermentation tanks are crucial in brewing, transforming wort into beer through the magical process of fermentation. This guide will cover everything you need to know about brewery fermentation tanks, from equipment types and brewing processes to choosing the right supplier and comparing the pros and cons.
What Are Brewery Fermentation Tanks?
Brewery fermentation tanks, also known as fermenters or fermenting vessels, are specialized containers where wort (unfermented beer) is transformed into beer through fermentation. This is where yeast converts the sugars in the wort into alcohol and carbon dioxide, creating the flavors and aromas that define different beer styles.
Equipment Guide
Choosing the right fermentation tank is vital for any brewery. There are various types of fermentation tanks, each with unique features and benefits. Understanding these options will help you make an informed decision that suits your brewing needs.
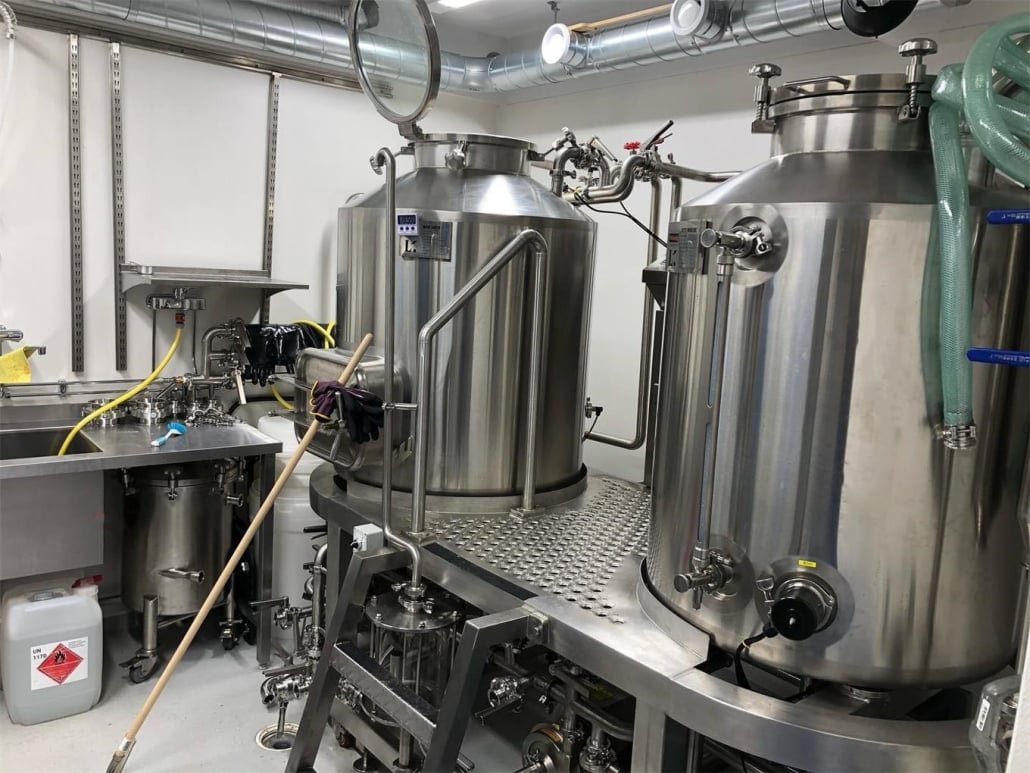
Types of Brewery Fermentation Tanks
1. Cylindroconical Fermenters (CCVs)
These are the most common types of fermentation tanks. They have a cone-shaped bottom that allows yeast and other sediments to settle at the bottom, making it easy to separate the beer from the trub (sediment).
2. Unitanks
Unitanks combine the functions of fermentation, maturation, carbonation, and aging into a single vessel. They are versatile and save space, making them ideal for smaller breweries.
3. Open Fermenters
These traditional fermentation tanks are open at the top, allowing for easy monitoring and control of the fermentation process. They are typically used for specific beer styles like Belgian ales and some German wheat beers.
4. Horizontal Fermentation Tanks
These tanks are designed for lagering (cold conditioning) beer. Their horizontal design provides a larger surface area for the yeast to settle, which helps in creating a smoother, cleaner beer.
5. Plastic Fermenters
Often used by homebrewers, plastic fermenters are affordable and lightweight but may not be suitable for larger, professional breweries due to durability concerns.
Equipment Comparison Table
Type | Features | Advantages | Limitations |
---|---|---|---|
Cylindroconical Fermenters | Cone-shaped bottom, stainless steel | Easy yeast separation, efficient fermentation | Higher cost, requires cleaning equipment |
Unitanks | All-in-one function (fermentation, maturation, carbonation) | Space-saving, versatile, efficient | Expensive, requires precise temperature control |
Open Fermenters | Open top, traditional design | Easy to monitor, traditional flavor profiles | Risk of contamination, requires more space |
Horizontal Fermentation Tanks | Horizontal design, larger surface area for yeast | Ideal for lagers, smoother beer | Space-consuming, harder to clean |
Plastic Fermenters | Lightweight, affordable, various sizes | Cost-effective, easy to handle | Less durable, potential for off-flavors |
Brewing Process
Now that we’ve covered the types of tanks, let’s dive into the brewing process itself. This section will explore the journey from raw ingredients to the finished beer, highlighting the role of fermentation tanks along the way.
1. Mashing
The brewing process starts with mashing, where malted grains are mixed with hot water to extract fermentable sugars. This creates a sweet liquid called wort.
2. Boiling
The wort is then boiled, and hops are added to provide bitterness and aroma. Boiling also sterilizes the wort, ensuring that unwanted bacteria are killed off.
3. Cooling
After boiling, the wort is rapidly cooled to a temperature suitable for fermentation. This is usually done using a heat exchanger.
4. Fermentation
The cooled wort is transferred to the fermentation tank, where yeast is added. Over the next several days to weeks, the yeast ferments the sugars in the wort, producing alcohol, carbon dioxide, and a range of flavors and aromas.
5. Conditioning
After primary fermentation, the beer is often transferred to a conditioning tank or left in the same tank (in the case of unitanks) for maturation. This step allows the flavors to meld and mature, producing a more balanced beer.
6. Packaging
Once the beer has reached the desired flavor profile, it is carbonated (if not already done during fermentation) and packaged into bottles, cans, or kegs for distribution.
Brewing Process and Fermentation Tanks Table
Brewing Step | Description | Role of Fermentation Tank |
---|---|---|
Mashing | Mixing malted grains with hot water to extract fermentable sugars | N/A |
Boiling | Boiling the wort and adding hops | N/A |
Cooling | Rapidly cooling the boiled wort to fermentation temperature | N/A |
Fermentation | Yeast ferments the sugars in the wort, producing alcohol and CO2 | The tank provides an environment for fermentation, allowing for temperature control and yeast separation |
Conditioning | Maturation of the beer to allow flavors to meld | Can occur in the same tank (unitanks) or separate conditioning tanks |
Packaging | Carbonating and packaging the finished beer | N/A |
Capacity, Space, Design, Layout, Customization
Fermentation tanks come in various sizes and designs, tailored to different brewery needs. This section explores the considerations regarding capacity, space requirements, design, layout, and customization options for fermentation tanks.
Capacity
The capacity of fermentation tanks can range from a few gallons for homebrewers to thousands of gallons for large commercial breweries. The size you choose depends on your production scale and future growth plans.
Space Requirements
Space is a crucial factor in any brewery setup. Cylindroconical fermenters and unitanks are space-efficient, while open and horizontal fermenters require more floor space. Vertical tanks save floor space but need sufficient ceiling height.
Design and Layout
The design and layout of fermentation tanks affect the workflow and efficiency of your brewery. Consider factors like ease of access for cleaning and maintenance, proximity to other brewing equipment, and the ability to expand.
Customization
Many manufacturers offer customization options for fermentation tanks, including additional ports for sampling, sensors for monitoring temperature and pressure, and specific finishes for aesthetic appeal. Customization can enhance the functionality and appearance of your brewery.
Capacity and Design Table
Factor | Description | Considerations |
---|---|---|
Capacity | Range from a few gallons to thousands of gallons | Production scale, future growth, batch size |
Space Requirements | Vertical tanks save floor space; horizontal and open tanks require more floor space | Ceiling height, available floor space, workflow efficiency |
Design and Layout | Layout affects workflow and efficiency | Ease of access, proximity to other equipment, potential for expansion |
Customization | Options include additional ports, sensors, and specific finishes | Enhanced functionality, aesthetic appeal, specific brewing needs |
Suppliers and Price Range
Choosing the right supplier is critical for getting quality fermentation tanks at a reasonable price. This section provides insights into top suppliers and the price ranges for different types of fermentation tanks.
Top Suppliers
Some well-known suppliers of brewery fermentation tanks include:
- Ss Brewtech
- Blichmann Engineering
- American Beer Equipment (ABE)
- Premier Stainless Systems
- JVNW
Price Range
The price of fermentation tanks varies based on size, material, and customization options. Here’s a general price range:
- Homebrew Fermenters: $100 – $1,000
- Small Commercial Fermenters (3-10 BBL): $5,000 – $20,000
- Medium Commercial Fermenters (10-30 BBL): $20,000 – $50,000
- Large Commercial Fermenters (30+ BBL): $50,000+
Suppliers and Price Range Table
Supplier | Specialty | Price Range |
---|---|---|
Ss Brewtech | High-quality stainless steel equipment for homebrewers | $100 – $5,000 |
Blichmann Engineering | Innovative brewing equipment | $200 – $10,000 |
American Beer Equipment (ABE) | Full-scale brewery systems | $10,000 – $100,000 |
Premier Stainless Systems | Customizable commercial brewery equipment | $20,000 – $150,000 |
JVNW | Large-scale commercial brewery solutions | $30,000 – $200,000+ |
Installation, Operation, Maintenance
Proper installation, operation, and maintenance of fermentation tanks are crucial for ensuring the quality and consistency of your beer. This section provides a detailed overview of these aspects.
Installation
Installing fermentation tanks requires careful planning and coordination. It involves positioning the tanks, connecting them to utilities (like glycol cooling systems), and ensuring they are level and secure. Professional installation is recommended to avoid issues.
Operation
Operating fermentation tanks involves monitoring and controlling fermentation parameters such as temperature, pressure, and yeast health. Automation systems can help in maintaining consistent conditions, which is crucial for producing high-quality beer.
Maintenance
Regular maintenance is
essential for the longevity and performance of fermentation tanks. This includes cleaning and sanitizing the tanks after each use, inspecting for wear and tear, and performing any necessary repairs promptly.
Installation, Operation, Maintenance Table
Aspect | Description | Considerations |
---|---|---|
Installation | Positioning tanks, connecting utilities, ensuring level and secure installation | Professional installation, planning and coordination, utility connections |
Operation | Monitoring and controlling fermentation parameters (temperature, pressure, yeast health) | Automation systems, consistent conditions, quality control |
Maintenance | Regular cleaning and sanitizing, inspecting for wear and tear, performing repairs | Longevity and performance, cleanliness, prompt repairs |
How to Choose a Supplier
Choosing the right supplier for your fermentation tanks is a critical decision that can impact your brewery’s success. This section provides tips and considerations for making an informed choice.
Factors to Consider
- Quality of Materials: Ensure the tanks are made from high-quality stainless steel or other durable materials.
- Customization Options: Look for suppliers that offer customization to meet your specific needs.
- Reputation: Research the supplier’s reputation within the industry. Check reviews and ask for references.
- Customer Support: Good customer support is essential for addressing any issues that may arise.
- Price: Compare prices from different suppliers to ensure you’re getting a fair deal without compromising on quality.
Choosing a Supplier Table
Factor | Description | Considerations |
---|---|---|
Quality of Materials | High-quality stainless steel or other durable materials | Longevity, durability, quality assurance |
Customization Options | Ability to customize tanks to meet specific needs | Enhanced functionality, specific brewing requirements |
Reputation | Supplier’s reputation within the industry | Reviews, references, industry standing |
Customer Support | Quality of support provided by the supplier | Responsiveness, problem resolution, ongoing support |
Price | Cost of fermentation tanks | Fair pricing, value for money, budget considerations |
Advantages and Limitations
Fermentation tanks have various advantages and limitations, depending on the type and design. This section explores these aspects to help you understand the best options for your brewery.
Advantages
- Efficiency: Modern fermentation tanks are designed for efficient fermentation and easy yeast separation.
- Versatility: Unitanks offer the flexibility of performing multiple functions in a single vessel.
- Space-saving: Vertical tanks save floor space, which is ideal for smaller breweries.
- Customization: Tanks can be customized with additional features to suit specific brewing needs.
Limitations
- Cost: High-quality fermentation tanks can be expensive, especially for small breweries.
- Maintenance: Regular cleaning and maintenance are essential to prevent contamination and ensure longevity.
- Space Requirements: Some tanks, like open and horizontal fermenters, require more space.
- Risk of Contamination: Open fermenters have a higher risk of contamination due to their open design.
Advantages and Limitations Table
Aspect | Advantages | Limitations |
---|---|---|
Efficiency | Designed for efficient fermentation and easy yeast separation | N/A |
Versatility | Unitanks perform multiple functions in a single vessel | Expensive |
Space-saving | Vertical tanks save floor space | N/A |
Customization | Additional features to suit specific brewing needs | Costly |
Cost | N/A | High-quality tanks can be expensive |
Maintenance | N/A | Requires regular cleaning and maintenance |
Space Requirements | N/A | Open and horizontal fermenters require more space |
Risk of Contamination | N/A | Open fermenters have a higher risk of contamination |
Choosing the Right Fermentation Tank
Selecting the right fermentation tank for your brewery involves balancing various factors such as budget, space, production scale, and specific brewing requirements. This section provides a step-by-step guide to help you make the best choice.
1. Assess Your Needs
Determine your production scale, available space, and budget. Consider the types of beer you plan to brew and any specific requirements you have.
2. Research Suppliers
Look for reputable suppliers that offer high-quality fermentation tanks. Consider their customization options, customer support, and industry reputation.
3. Compare Options
Compare different types of fermentation tanks and their features. Consider the advantages and limitations of each type and how they align with your needs.
4. Evaluate Costs
Consider the total cost of ownership, including the initial purchase price, installation costs, and ongoing maintenance expenses. Ensure that the tanks you choose fit within your budget.
5. Seek Expert Advice
Consult with brewing industry experts or other brewery owners to get insights and recommendations. Their experiences can provide valuable guidance in making your decision.
Choosing the Right Fermentation Tank Table
Step | Description | Considerations |
---|---|---|
Assess Your Needs | Determine production scale, available space, budget, and specific brewing requirements | Types of beer, production goals, space constraints, financial capacity |
Research Suppliers | Look for reputable suppliers with high-quality tanks, customization options, and good customer support | Supplier reputation, customization, customer reviews, references |
Compare Options | Evaluate different types of fermentation tanks and their features | Advantages, limitations, alignment with brewery needs |
Evaluate Costs | Consider total cost of ownership, including purchase price, installation, and maintenance | Budget, cost-effectiveness, long-term expenses |
Seek Expert Advice | Consult brewing industry experts or other brewery owners for recommendations and insights | Expert opinions, experiences, practical advice |
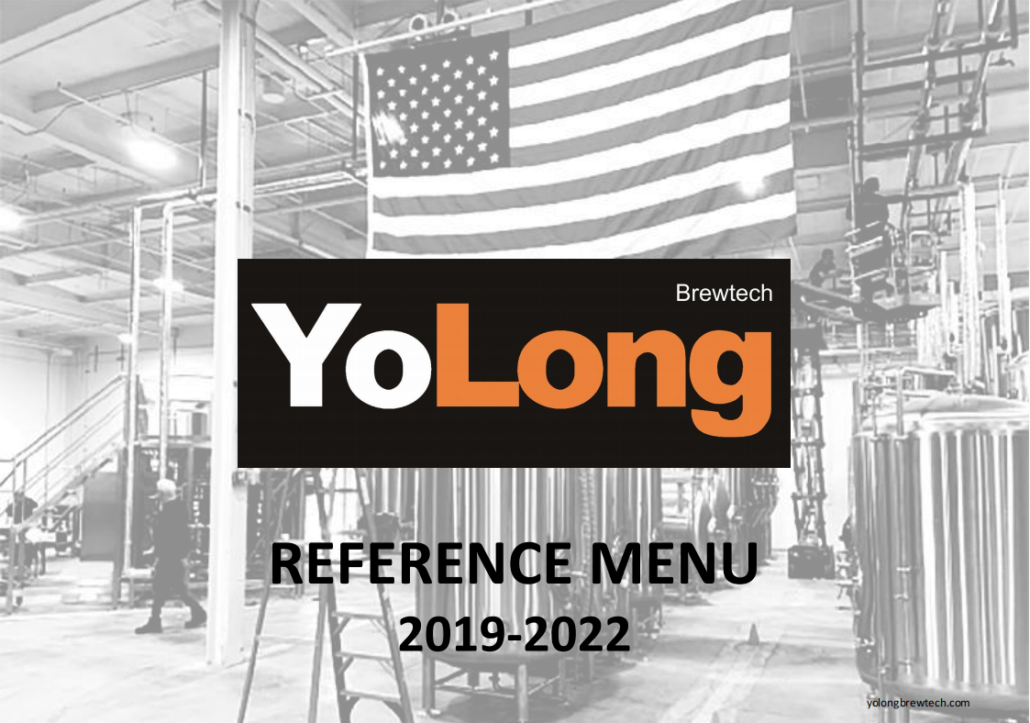
Comparing Pros and Cons
To help you make an informed decision, this section compares the pros and cons of different types of fermentation tanks, focusing on key parameters like efficiency, cost, space requirements, and versatility.
Pros and Cons Comparison Table
Type of Tank | Pros | Cons |
---|---|---|
Cylindroconical Fermenters | Efficient yeast separation, easy to clean, ideal for various beer styles | Higher cost, requires cleaning equipment |
Unitanks | Space-saving, versatile, efficient multi-function use | Expensive, requires precise temperature control |
Open Fermenters | Easy to monitor, traditional flavor profiles, simple design | Risk of contamination, requires more space |
Horizontal Fermentation Tanks | Ideal for lagers, smoother beer due to larger surface area for yeast | Space-consuming, harder to clean |
Plastic Fermenters | Affordable, lightweight, easy to handle | Less durable, potential for off-flavors |
FAQ
Question | Answer |
---|---|
What is the main purpose of a fermentation tank in brewing? | Fermentation tanks provide an environment for yeast to convert sugars in the wort into alcohol and carbon dioxide, creating beer. |
How do I choose the right size fermentation tank for my brewery? | Consider your production scale, batch size, and future growth plans. It’s essential to choose a tank that fits your brewing needs. |
What materials are commonly used for fermentation tanks? | Stainless steel is the most common material due to its durability, ease of cleaning, and resistance to corrosion. |
Can I use the same fermentation tank for different beer styles? | Yes, many fermentation tanks, especially unitanks, are versatile and can be used for various beer styles. |
How often should fermentation tanks be cleaned? | Fermentation tanks should be cleaned and sanitized after each batch to prevent contamination and ensure quality. |
What are the benefits of using a unitank? | Unitanks combine multiple functions (fermentation, maturation, carbonation) in one vessel, saving space and improving efficiency. |
Are open fermenters suitable for all types of beer? | Open fermenters are typically used for specific styles like Belgian ales and German wheat beers due to their unique characteristics. |
How much does it cost to install fermentation tanks? | Installation costs vary depending on the size and complexity of the setup. Professional installation is recommended for accuracy. |
What are the maintenance requirements for fermentation tanks? | Regular cleaning, sanitizing, and inspection for wear and tear are crucial for maintaining the performance and longevity of the tanks. |
Can I customize my fermentation tanks? | Yes, many suppliers offer customization options to meet specific brewing needs, including additional ports and sensors. |
Share this entry
Interested in learning more about Brewing Systems including additional details and pricing information? Please use the form below to contact us!
YOLONG BREWERY EQUIPMENT FAQS
- Commercial Brewery / Craft Brewery / Microbrewery / Nanobrewery
- What is The Difference Between Craft Beer and Industrial Beer?
- The Bespoke Differences In Custom Brewing Systems
- Everything You Need to Know About Kettle Souring
- How to Choose Brewing Equipment for Your business?
- How To Choose The-Best Partner To Build Your Commercial Microbrewing System?
- Two Detection Sensors That You Need To Use In Your Brewhouse System
- Remote Control Applications in Brewing Equipment/How does it work?
- How To Clean Your Brand New Brewery Tanks?