Ultimate Guide to Beer Canning Equipment
Beer canning equipment is crucial for breweries of all sizes, ensuring the freshness and quality of the beer. Whether you’re a homebrewer looking to upgrade your setup or a craft brewery scaling up, this guide will cover everything you need to know about beer canning equipment. We’ll explore the different types of equipment, the canning process, suppliers, and much more.
Overview of Beer Canning Equipment
Beer canning equipment is designed to automate and streamline the process of filling and sealing beer cans. The right equipment can significantly enhance production efficiency, improve beer quality, and extend shelf life. From semi-automated systems for small breweries to fully automated lines for large-scale operations, there’s a range of equipment available to meet various needs and budgets.
Beer Canning Equipment Guide
Choosing the right beer canning equipment involves understanding the different components, their functions, and how they fit into the brewing process. This section provides a detailed guide to the essential equipment for beer canning.
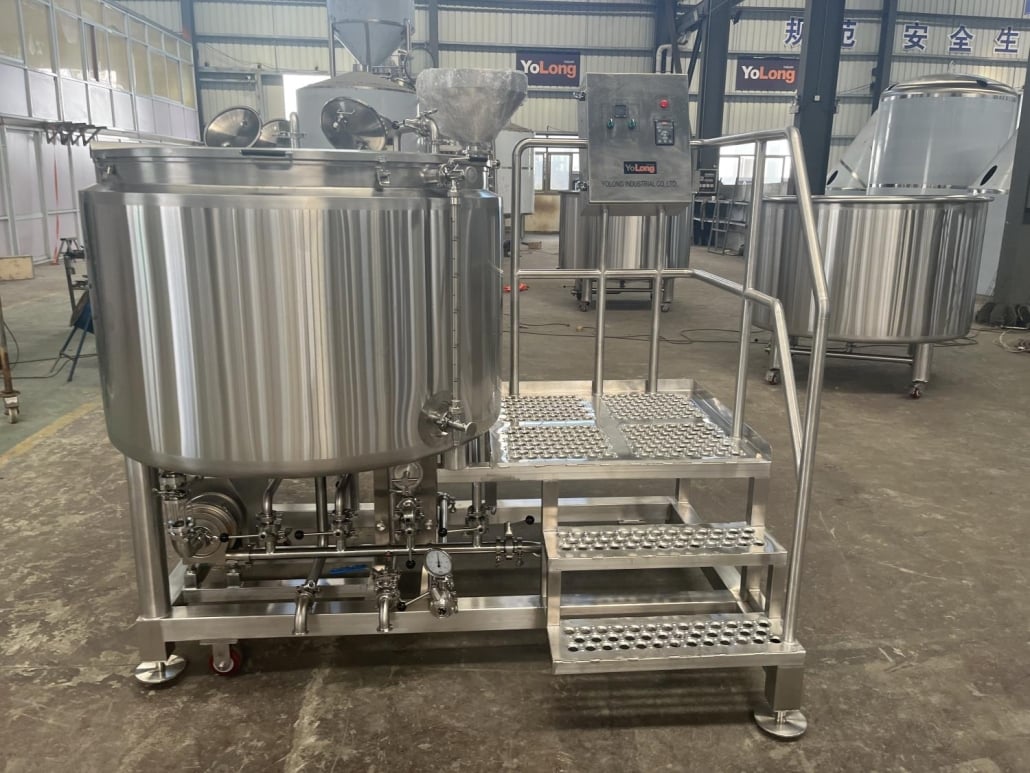
Essential Equipment for Beer Canning
- Depalletizer: Used for unloading cans from pallets and preparing them for filling. It ensures a steady supply of empty cans to the canning line.
- Rinse Station: Cleans the cans before filling to remove any contaminants.
- Filler: The heart of the canning line, this equipment fills the cans with beer. It must be accurate and efficient to minimize waste and ensure consistent fill levels.
- Seamer: Seals the filled cans with lids, ensuring they are airtight and preventing contamination.
- Labeler: Applies labels to the cans, which is crucial for branding and regulatory compliance.
- PakTech Can Carrier Applicator: Attaches handles to cans for easy carrying.
- Shrink Sleeving Machine: Applies shrink sleeves to cans, offering a cost-effective labeling solution.
- Quality Control Station: Ensures each can is properly filled and sealed, and checks for any defects.
Table of Beer Canning Equipment Types
Equipment Type | Function | Advantages | Disadvantages |
---|---|---|---|
Depalletizer | Unloads cans from pallets | Automates process, reduces labor | Initial cost |
Rinse Station | Cleans cans before filling | Ensures cleanliness, prevents contamination | Additional space required |
Filler | Fills cans with beer | High accuracy, reduces waste | Can be expensive, requires maintenance |
Seamer | Seals cans with lids | Airtight seal, preserves beer quality | Precision needed, regular checks |
Labeler | Applies labels to cans | Essential for branding, compliance | Must be compatible with can shapes/sizes |
PakTech Can Carrier Applicator | Attaches handles to cans for easy carrying | Improves convenience for consumers | Additional step in process |
Shrink Sleeving Machine | Applies shrink sleeves to cans | Cost-effective labeling | Requires heat application |
Quality Control Station | Checks filled and sealed cans for defects | Ensures product quality | Adds another step to the process |
The Beer Canning Process
Understanding the canning process is crucial for selecting the right equipment and ensuring smooth operations. Here, we break down the steps involved in canning beer.
Brewing Process for Canning
- Preparation: Begin by preparing the beer and ensuring it meets the desired quality standards. This includes fermentation, carbonation, and cold crashing to clarify the beer.
- Depalletizing: Cans are unloaded from pallets using a depalletizer. This equipment is essential for automating the supply of empty cans to the canning line.
- Rinsing: The empty cans are passed through a rinse station to clean them. This step removes any dust or particles that could contaminate the beer.
- Filling: Cans are filled with beer using a filler. Accurate filling is crucial to ensure consistent product quality and minimize waste.
- Seaming: After filling, the cans are sealed with lids using a seamer. This step ensures the cans are airtight, preventing oxidation and maintaining the beer’s freshness.
- Labeling: Cans are labeled with branding and regulatory information. This can be done using a labeler or shrink sleeving machine.
- Packaging: Finally, the cans are packed into boxes or crates, ready for distribution. The PakTech can carrier applicator can be used to attach handles for easy carrying.
Table of Canning Equipment by Capacity, Space, Design, Layout, and Customization
Equipment | Capacity | Space Requirements | Design | Layout | Customization |
---|---|---|---|---|---|
Depalletizer | 60-120 cans per minute | Moderate to high | Modular | Inline or L-shaped | Custom sizes for different can types |
Rinse Station | 60-120 cans per minute | Low to moderate | Compact | Inline | Adjustable spray nozzles |
Filler | 30-200 cans per minute | Moderate to high | Multiple head designs | Inline | Adjustable fill heads |
Seamer | 30-200 cans per minute | Moderate | Rotary or inline | Inline | Custom seam rollers |
Labeler | 60-200 cans per minute | Low to moderate | Modular | Inline | Custom label sizes and shapes |
PakTech Can Carrier Applicator | 30-100 cans per minute | Low to moderate | Compact | Inline | Custom carrier designs |
Shrink Sleeving Machine | 60-120 cans per minute | Moderate | Modular | Inline | Custom sleeve designs |
Quality Control Station | 30-200 cans per minute | Low to moderate | Compact | Inline | Custom inspection parameters |
Choosing the Right Supplier for Beer Canning Equipment
Selecting the right supplier is essential to ensure you get high-quality equipment that meets your needs. Consider factors such as price, reliability, and after-sales support.
Table of Suppliers and Price Range
Supplier | Price Range | Reputation | After-Sales Support | Customization Options |
---|---|---|---|---|
Supplier A | $50,000 – $200,000 | Excellent | Comprehensive | High |
Supplier B | $40,000 – $150,000 | Good | Limited | Moderate |
Supplier C | $30,000 – $120,000 | Average | Basic | Low |
Supplier D | $60,000 – $250,000 | Excellent | Comprehensive | High |
Supplier E | $45,000 – $180,000 | Good | Moderate | Moderate |
Table for Installation, Operation, and Maintenance
Equipment | Installation | Operation | Maintenance |
---|---|---|---|
Depalletizer | Professional installation needed | Easy to operate, requires training | Regular cleaning and lubrication |
Rinse Station | Simple installation | Easy to operate | Regular nozzle checks |
Filler | Professional installation needed | Requires skilled operation | Regular calibration and cleaning |
Seamer | Professional installation needed | Requires skilled operation | Regular seam checks and maintenance |
Labeler | Simple installation | Easy to operate | Regular label alignment checks |
PakTech Can Carrier Applicator | Simple installation | Easy to operate | Regular cleaning and checks |
Shrink Sleeving Machine | Professional installation needed | Requires skilled operation | Regular sleeve alignment checks |
Quality Control Station | Simple installation | Easy to operate | Regular calibration |
How to Choose a Supplier
Selecting the right supplier involves considering several factors:
- Price: Ensure the supplier offers competitive pricing that fits your budget.
- Quality: Check the quality of the equipment and the reputation of the supplier.
- Support: Ensure the supplier provides good after-sales support and maintenance services.
- Customization: Look for suppliers that offer customization options to meet your specific needs.
- Reviews: Read reviews and testimonials from other customers to gauge satisfaction levels.
Table Comparing Pros and Cons of Beer Canning Equipment
Equipment | Pros | Cons |
---|---|---|
Depalletizer | Automates can loading, reduces labor costs | High initial cost |
Rinse Station | Ensures clean cans, prevents contamination | Requires additional space |
Filler | Accurate filling, minimizes waste | Can be expensive, requires maintenance |
Seamer | Airtight seal, preserves beer quality | Precision needed, regular checks |
Labeler | Essential for branding and compliance | Must be compatible with can shapes/sizes |
PakTech Can Carrier Applicator | Improves consumer convenience | Additional step in process |
Shrink Sleeving Machine | Cost-effective labeling solution | Requires heat application |
Quality Control Station | Ensures product quality | Adds another step to the process |
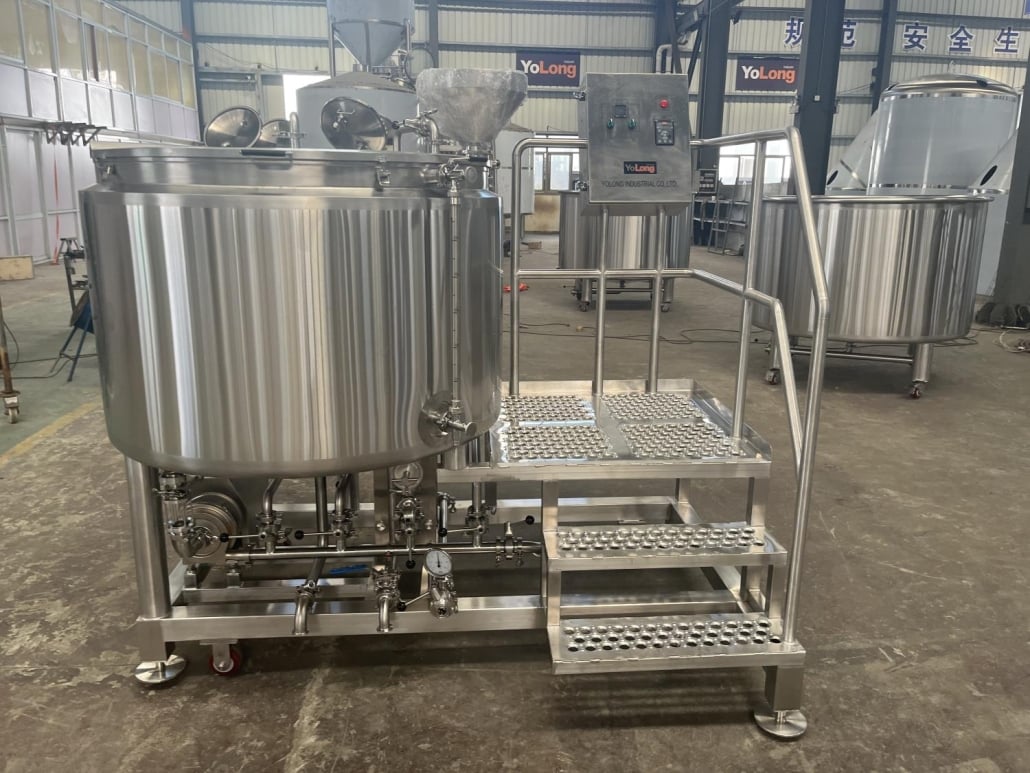
FAQ
Question | Answer |
---|---|
What is beer canning equipment? | Beer canning equipment is used to fill and seal beer cans, ensuring freshness and quality. |
Why is beer canning important? | Canning preserves the beer’s freshness, extends shelf life, and is convenient for consumers. |
What types of canning equipment are there? | Key types include depalletizers, rinse stations, fillers, seamers, labelers, and quality control stations. |
How much does beer canning equipment cost? | Prices vary widely depending on capacity and features, ranging from $30,000 to $250,000. |
What factors should I consider when choosing equipment? | Consider capacity, space requirements, design, layout, customization options, and supplier reputation. |
How do I maintain beer canning equipment? | Regular cleaning, lubrication, calibration, and checks are essential for maintaining canning equipment. |
Can I customize beer canning equipment? | Yes, many suppliers offer customization options to meet specific needs. |
Who are the top suppliers? | Top suppliers include Supplier A, Supplier B, Supplier C, Supplier D, and Supplier E. |
Conclusion
Investing in the right beer canning equipment is crucial for ensuring the quality and efficiency of your brewing operations. By understanding the different types of equipment, the canning process, and how to choose the right supplier, you can make informed decisions that will benefit your brewery. Whether you are a small craft brewer or a large-scale operation, there is a range of equipment available to meet your needs. Remember to consider factors such as capacity, space requirements, design, and customization options when selecting your equipment. With the right setup, you can ensure your beer is canned efficiently, maintaining its quality and freshness for your customers.
Share this entry
Interested in learning more about Brewing Systems including additional details and pricing information? Please use the form below to contact us!
YOLONG BREWERY EQUIPMENT FAQS
- Commercial Brewery / Craft Brewery / Microbrewery / Nanobrewery
- What is The Difference Between Craft Beer and Industrial Beer?
- The Bespoke Differences In Custom Brewing Systems
- Everything You Need to Know About Kettle Souring
- How to Choose Brewing Equipment for Your business?
- How To Choose The-Best Partner To Build Your Commercial Microbrewing System?
- Two Detection Sensors That You Need To Use In Your Brewhouse System
- Remote Control Applications in Brewing Equipment/How does it work?
- How To Clean Your Brand New Brewery Tanks?