Microbrewery Systems
Microbrewery systems have become a beacon for beer enthusiasts and entrepreneurs alike, offering a mix of artistry, science, and business opportunities. Whether you’re a craft beer lover dreaming of starting your brewery or a seasoned brewer looking to scale up, understanding these systems is key. Let’s dive into this comprehensive guide to explore everything you need to know about microbrewery systems.
What Is a Microbrewery System?
A microbrewery system refers to a compact and efficient setup used for brewing craft beer. Unlike large-scale brewing operations, microbreweries focus on producing small batches of high-quality beer, often with unique flavors and characteristics. The system includes equipment for brewing, fermenting, conditioning, and packaging beer, designed to meet the needs of small-scale operations.
The appeal of microbreweries lies in their ability to innovate, cater to niche markets, and provide local beer with a personal touch. These systems allow for experimentation and customization, making them perfect for craft beer aficionados.
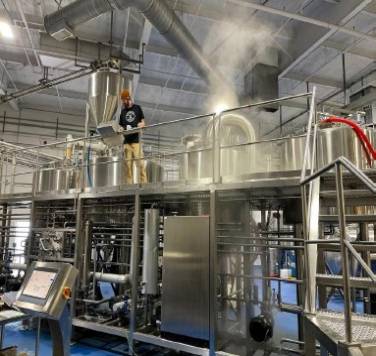
Essential Equipment in a Microbrewery System
Microbrewery systems consist of several key pieces of equipment, each playing a vital role in the brewing process. Here’s a breakdown:
Equipment Type | Function | Description |
---|---|---|
Milling Equipment | Crushes grains for brewing | Ensures a consistent grind size for efficient extraction during the mash stage. |
Mash Tun | Converts starches into fermentable sugars | A vessel where water and crushed grains mix and undergo enzymatic reactions. |
Lauter Tun | Separates wort from grain solids | A filtration system that collects the sugary liquid needed for fermentation. |
Boiling Kettle | Boils wort and incorporates hops | Essential for sterilizing the wort and extracting flavors from hops. |
Fermentation Tanks | Ferments wort into beer | Maintains controlled conditions for yeast to convert sugars into alcohol. |
Conditioning Tanks | Matures beer to improve taste and quality | Allows for flavor refinement and carbonation adjustments. |
Packaging Equipment | Bottles, cans, or kegs beer | Ensures airtight sealing for distribution and storage. |
Brewing Process in a Microbrewery
Brewing beer in a microbrewery involves multiple stages, each requiring precision and expertise. Here’s a detailed explanation:
1. Milling
The process begins with milling, where malted grains are crushed into a coarse powder called grist. The aim is to break the grain husks while preserving their integrity, facilitating efficient sugar extraction in the mash tun.
2. Mashing
In this step, grist is mixed with hot water in the mash tun. The heat activates enzymes in the grains, converting starches into fermentable sugars. This sugary liquid, known as wort, forms the base of the beer.
3. Lautering
The wort is separated from the spent grains in the lauter tun. This involves rinsing the grains with hot water to maximize sugar extraction. The collected wort is then transferred to the boiling kettle.
4. Boiling
The wort is boiled, and hops are added at various stages to introduce bitterness, aroma, and flavor. Boiling also sterilizes the wort, eliminating any unwanted microorganisms.
5. Fermentation
After cooling, the wort is moved to fermentation tanks, where yeast is added. Yeast consumes the sugars, producing alcohol and carbon dioxide. This stage can take anywhere from a few days to weeks, depending on the beer style.
6. Conditioning
Once fermentation is complete, the beer is conditioned in specialized tanks. This step refines the flavor, removes unwanted compounds, and allows for carbonation adjustments.
7. Packaging
Finally, the beer is packaged in bottles, cans, or kegs, ready for distribution. Packaging equipment ensures the beer remains fresh and is sealed properly for storage.
Capacity, Space, Design, and Layout
Selecting the right capacity and design for your microbrewery system is crucial. Consider the following:
Parameter | Details |
---|---|
Capacity | Ranges from 1 HL to 30 HL; smaller capacities are ideal for startups and experimentation. |
Space Requirements | A compact system can fit in 500–1000 sq. ft.; larger systems need more room for tanks. |
Design | Modular designs allow for scalability; stainless steel is the preferred material. |
Layout | Linear layouts are efficient for workflow; consider space for raw materials and packaging. |
Customization | Tailor systems with additional tanks, automated controls, or specific brewing styles. |
Suppliers and Price Range
Choosing the right supplier can make or break your microbrewery. Here’s an overview of options:
Supplier | Price Range | Features |
---|---|---|
ABC Brewing Systems | $30,000–$100,000 | Compact designs, customization options |
CraftPro Equipment | $50,000–$200,000 | High-quality stainless steel tanks |
NanoBrew Technologies | $40,000–$150,000 | Affordable systems for small-scale brewers |
ProBrew Solutions | $60,000–$250,000 | Advanced automation and energy-efficient designs |
Installation, Operation, and Maintenance
The lifecycle of a microbrewery system involves seamless installation, smooth operation, and regular maintenance. Let’s break it down:
Aspect | Details |
---|---|
Installation | Requires professional technicians; ensure proper drainage, electrical, and ventilation setup. |
Operation | Involves regular cleaning, monitoring fermentation, and adjusting parameters as needed. |
Maintenance | Regular cleaning of tanks and pipes, inspection of seals and valves, and equipment servicing. |
How to Choose the Right Supplier
When choosing a supplier, focus on these factors:
- Reputation: Look for suppliers with positive reviews and a proven track record.
- Customization: Ensure they offer options tailored to your brewing style and capacity needs.
- Support: Select suppliers who provide training, installation, and ongoing technical support.
- Cost Transparency: Opt for suppliers who offer clear pricing without hidden fees.
Advantages and Limitations of Microbrewery Systems
Aspect | Advantages | Limitations |
---|---|---|
Customization | Allows experimentation with unique beer styles. | Limited scalability compared to large breweries. |
Cost | Lower initial investment than industrial setups. | Equipment can still be expensive for small startups. |
Market Appeal | Attracts local customers with fresh, artisanal beer. | Requires consistent marketing to stand out in a crowded market. |
Control | Provides full control over quality and flavors. | Demands in-depth knowledge of brewing science and processes. |
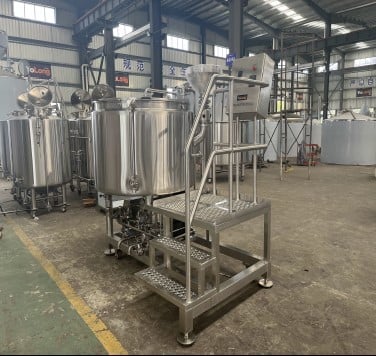
FAQs
Question | Answer |
---|---|
What is the cost of a microbrewery system? | Prices range from $30,000 to $250,000, depending on capacity and features. |
How much space do I need? | A small system can fit in 500 sq. ft.; larger setups need up to 2000 sq. ft. |
Can I brew different beer styles? | Yes, microbrewery systems are designed for versatility and experimentation. |
How long does it take to brew beer? | The brewing process takes 2–6 weeks, depending on the beer style. |
Do I need a license to operate? | Yes, brewing and selling beer require local and federal licenses. |
Conclusion
A microbrewery system is your gateway to creating craft beer that resonates with your unique vision. With the right equipment, suppliers, and knowledge, you can carve a niche in the ever-growing world of craft brewing. Whether you’re just starting or scaling up, these systems offer endless possibilities for creativity and innovation.