Vessel Brewing System
Brewing beer is both an art and a science, and the choice of equipment plays a pivotal role in the final product’s quality. Among the tools at the heart of every brewery lies the vessel brewing system, a cornerstone for creating your favorite brews. Whether you’re a craft beer enthusiast or planning to start your brewery, this guide explores everything you need to know about vessel brewing systems in a detailed, SEO-optimized, and engaging format.
Overview of Vessel Brewing Systems
A vessel brewing system refers to a set of tanks or containers used in beer production. These systems facilitate different stages of brewing, including mashing, lautering, boiling, fermenting, and conditioning. They come in various configurations, materials, and capacities, designed to meet the needs of both small craft breweries and large commercial operations.
These systems blend technology and tradition, offering automation options for efficiency while retaining the charm of hands-on brewing. Let’s dive into the equipment details, brewing processes, customization options, and more.
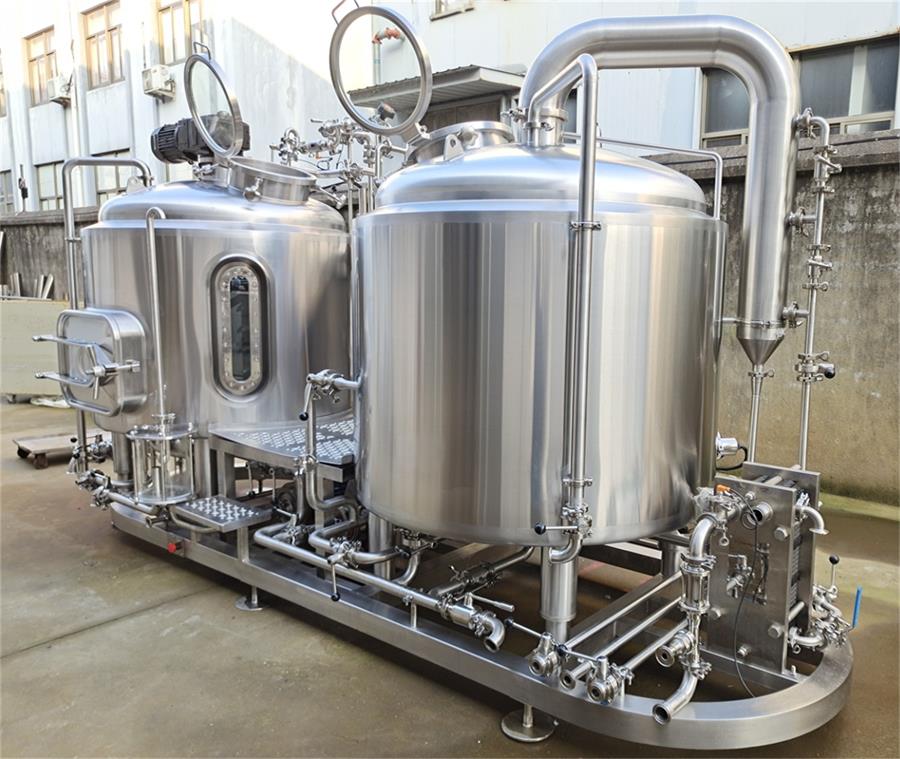
Essential Equipment in a Vessel Brewing System
A brewing system typically consists of several key components, each with a specific function. Here’s an overview:
Mash Tun
The mash tun is where the magic begins. Grains are mixed with water and heated, converting starches into fermentable sugars. Insulated or jacketed designs ensure consistent temperature control.
Lauter Tun
This vessel separates the liquid wort from the solid grain husks. Its slotted false bottom allows for efficient drainage and filtration.
Boil Kettle
The wort is boiled here, often with hops added for bitterness and aroma. These kettles are equipped with heating elements, steam jackets, or direct fire systems.
Fermenters
Fermentation vessels hold the wort while yeast converts sugars into alcohol. They come in various shapes (conical or cylindrical) and sizes, with temperature control mechanisms.
Bright Tanks
Used for conditioning, carbonation, and storage, bright tanks ensure your beer is perfectly clear and ready for packaging.
Types of Vessel Brewing Systems
Here’s a breakdown of common vessel configurations based on functionality and scale:
System Type | Description | Best For |
---|---|---|
Two-Vessel System | Combines mashing and lautering in one vessel; boiling and whirlpool in another. | Small craft breweries. |
Three-Vessel System | Separate mash tun, lauter tun, and boil kettle for better efficiency. | Medium-scale brewing operations. |
Four-Vessel System | Adds a whirlpool vessel for clarity and speed. | Large breweries with high output. |
Automated Systems | Fully integrated systems with programmable controls. | Breweries aiming for consistency. |
Modular Systems | Configurable and expandable setups. | Flexible and scalable operations. |
Brewing Process with a Vessel Brewing System
1. Mashing
The grains are soaked in hot water inside the mash tun, initiating the enzymatic breakdown of starches into sugars. Precision in temperature and timing is key to creating desired beer profiles.
2. Lautering
After mashing, the mash is transferred to the lauter tun. Here, the sugary liquid (wort) is separated from the grain solids, which are removed and often repurposed as animal feed.
3. Boiling
The wort moves to the boil kettle, where it’s heated to sterilize the liquid. Hops are added during this phase to impart bitterness, flavor, and aroma.
4. Fermentation
Cooled wort enters fermentation tanks, where yeast is added. Over days or weeks, the yeast converts sugars into alcohol and carbon dioxide, defining the beer’s flavor profile.
5. Conditioning
Bright tanks are used to refine the beer, ensuring it is clear, carbonated, and shelf-stable. The final product is then packaged for distribution.
Customizing Vessel Brewing Systems
Breweries differ in their needs, and so do brewing systems. Here’s a guide to customization options:
Parameter | Customization Options |
---|---|
Capacity | Ranges from 1 barrel (31 gallons) to 100+ barrels for industrial setups. |
Material | Stainless steel is common for durability and hygiene; copper for aesthetics. |
Heating Method | Direct fire, steam jackets, or electric heating for temperature control. |
Automation | Manual systems for traditionalists; automated ones for efficiency and consistency. |
Layout Design | Compact designs for small spaces; sprawling setups for large-scale production. |
Cost of Vessel Brewing Systems
Investing in a brewing system is a significant financial decision. Prices vary based on capacity, features, and customization.
Supplier | Price Range | Specialization |
---|---|---|
ABC Brewing Systems | $10,000 – $50,000 | Small-scale systems for craft brewers. |
ProBrew Solutions | $50,000 – $250,000 | Medium and large breweries with automation options. |
MegaBrew Technologies | $100,000 – $1,000,000+ | Large-scale industrial brewing systems. |
Installation, Operation, and Maintenance
Installation
Proper installation involves setting up vessels, connecting utilities (electricity, water, gas), and ensuring compliance with local regulations. Hiring experienced technicians ensures smooth setup.
Operation
Operating a vessel brewing system requires a balance of technical know-how and creativity. Breweries must monitor temperatures, pH levels, and flow rates throughout the process.
Maintenance
Regular cleaning and maintenance are essential. Stainless steel components require periodic passivation to prevent corrosion. Inspect gaskets, valves, and seals to avoid leaks.
How to Choose a Supplier
Selecting the right supplier can make or break your brewing operation. Here’s what to consider:
Criteria | Details |
---|---|
Experience | Look for suppliers with a proven track record in the brewing industry. |
Customization Options | Ensure the supplier offers flexibility in design and features. |
Warranty | Check for robust warranties covering parts and labor. |
After-Sales Support | Opt for companies that provide training, troubleshooting, and repair services. |
Client Reviews | Research testimonials and case studies for real-world performance insights. |
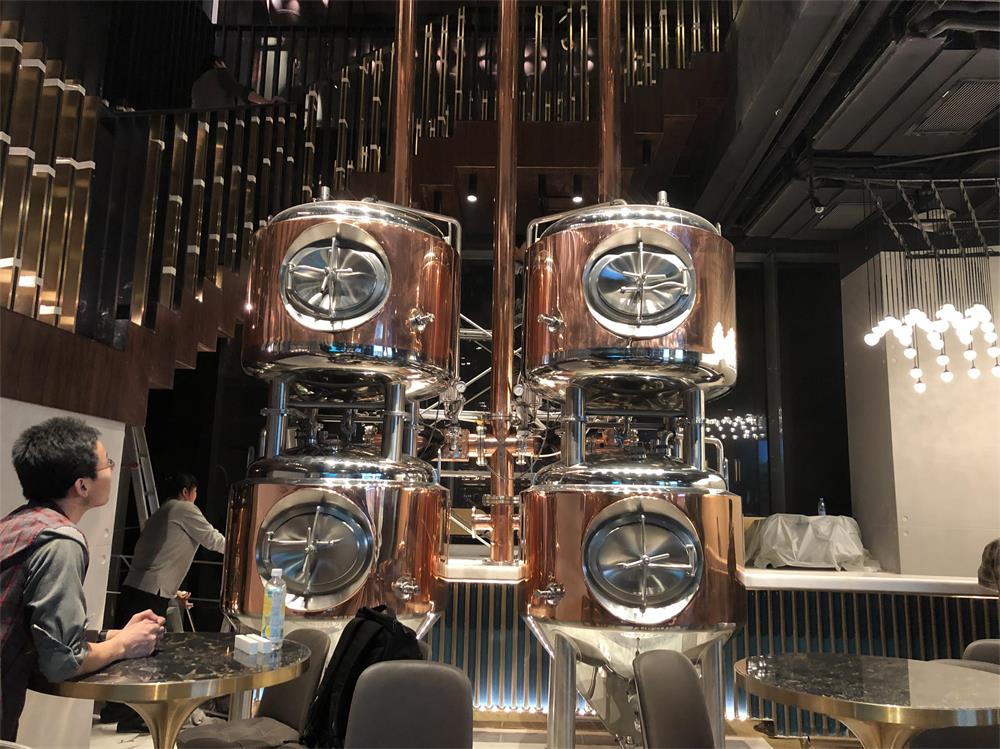
Comparing Pros and Cons of Vessel Brewing Systems
Advantages | Limitations |
---|---|
High precision in brewing processes. | High initial investment. |
Scalability to meet production demands. | Requires significant space. |
Long-lasting stainless steel construction. | Ongoing maintenance costs. |
Flexibility in customization. | Steeper learning curve for beginners. |
FAQs
Question | Answer |
---|---|
What is the ideal capacity for a small brewery? | A 3-10 barrel system is ideal for small craft breweries starting out. |
Can I upgrade my brewing system later? | Yes, modular systems allow for expansions as your brewery grows. |
How long does installation take? | Installation can take 4-12 weeks depending on system complexity. |
What is the average lifespan of a brewing system? | With proper maintenance, most systems last 10-20 years or more. |
Are there eco-friendly brewing systems available? | Yes, look for systems with energy-efficient heating and water recycling. |