Understanding the 10bbl Brewhouse
In the world of craft brewing, a 10bbl brewhouse stands out as a significant investment. It’s not just a piece of equipment; it’s the heart of your brewing operations. Whether you’re upgrading from a smaller system or starting fresh with a 10-barrel capacity, understanding what you’re getting into is crucial. This guide will walk you through everything you need to know—from the basics of what a 10bbl brewhouse is to detailed advice on choosing the right supplier, managing costs, and more. Let’s dive in!
Overview of a 10bbl Brewhouse
A 10bbl brewhouse, which stands for a 10-barrel brewhouse, is a brewing system designed to produce 10 barrels of beer per batch. That’s about 310 gallons or roughly 2,500 pints of beer. The 10bbl size is ideal for small to medium-sized craft breweries looking to scale up production without moving into the realm of industrial-scale operations.
What Does a 10bbl Brewhouse Include?
A typical 10bbl brewhouse includes several key components:
- Mash Tun: Where the grain is mixed with water and heated to convert starches into fermentable sugars.
- Lauter Tun: Used to separate the wort from the spent grain.
- Brew Kettle/Whirlpool: Where the wort is boiled and hops are added, then it’s spun to remove trub (solid particles).
- Heat Exchanger: Cools the wort before it moves to the fermentation tanks.
- Fermentation Vessels: Where the wort ferments into beer.
- Bright Tanks: For carbonation and storage before packaging.
Each of these components plays a critical role in the brewing process, and their quality and configuration can significantly impact the efficiency and quality of the beer produced.
Why Choose a 10bbl Brewhouse?
Choosing a 10bbl brewhouse is often a strategic decision for breweries. It strikes a balance between production capacity and operational flexibility, making it a popular choice for breweries that aim to expand their distribution without overwhelming their production staff or resources. The 10bbl size also provides enough capacity to experiment with different beer styles and recipes without the high stakes of larger batch sizes.
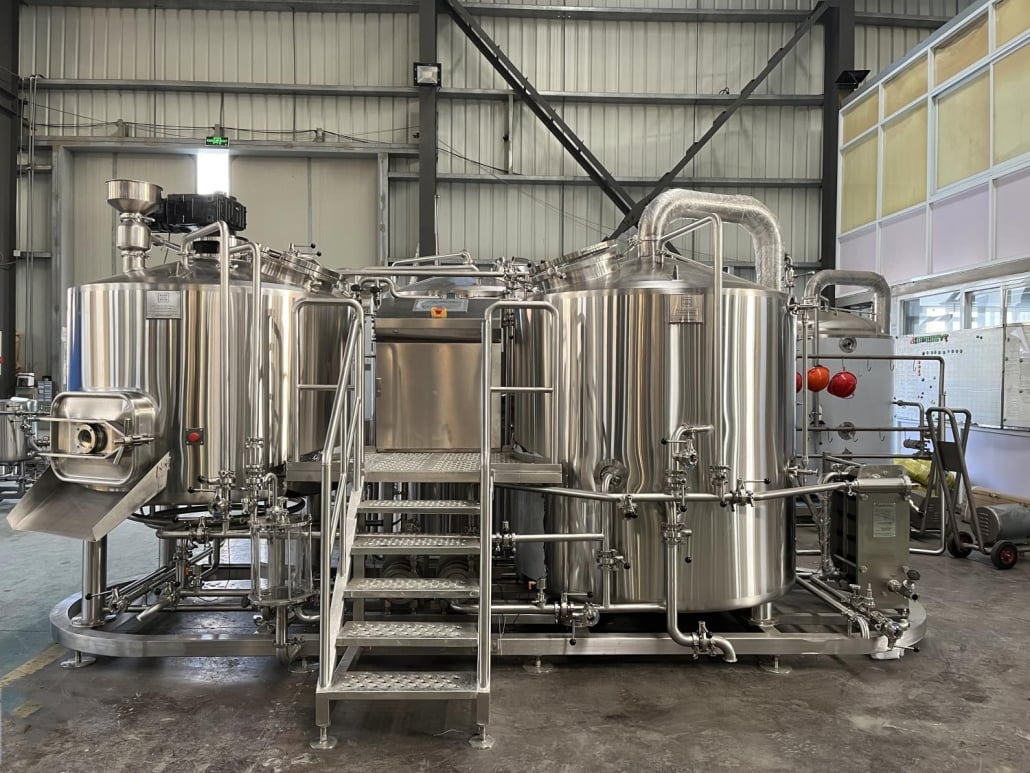
10bbl Brewhouse Equipment Guide
Understanding the equipment in a 10bbl brewhouse is essential for maximizing its potential. Below, we’ll explore each component in detail, discussing their functions and the options available to brewers.
Mash Tun
The mash tun is where the magic begins. It’s where the malted barley is mixed with hot water, triggering enzymatic activity that converts the starches into fermentable sugars. The design of the mash tun, including its size, shape, and the presence of additional features like rakes or agitators, can influence the efficiency of the mashing process.
Lauter Tun
After mashing, the mixture moves to the lauter tun, where the liquid wort is separated from the spent grain. A well-designed lauter tun ensures a clear wort and efficient extraction of sugars. Features like false bottoms, rakes, and sparging arms can make a big difference in the performance of this component.
Brew Kettle/Whirlpool
The brew kettle is where the wort is boiled, and hops are added. The boiling process sterilizes the wort and extracts bitterness and aroma from the hops. After boiling, the wort is transferred to the whirlpool, where centrifugal forces separate the solid particles from the liquid. This component’s design, including its heating source (direct fire, steam, or electric), can affect the brewing process’s speed and energy efficiency.
Heat Exchanger
A critical but often overlooked piece of equipment, the heat exchanger rapidly cools the wort to a temperature suitable for fermentation. The type of heat exchanger (plate, tubular, or shell-and-tube) can impact cooling efficiency and the likelihood of contamination.
Fermentation Vessels
Once cooled, the wort is transferred to fermentation vessels, where yeast is added to begin the fermentation process. These vessels must be carefully selected based on their material (stainless steel is standard), size, and additional features like cooling jackets and pressure ratings.
Bright Tanks
Bright tanks are where the beer is conditioned, carbonated, and stored before packaging. These tanks need to maintain specific pressures and temperatures to ensure the beer reaches the desired carbonation level and clarity.
Brewing Process in a 10bbl Brewhouse
The brewing process in a 10bbl brewhouse follows the same basic steps as in smaller or larger systems but on a scale that balances artisanal control with commercial production volumes. Let’s break down the brewing process step by step:
Step 1: Mashing
In the mash tun, malted grains are mixed with hot water, initiating the enzymatic breakdown of starches into sugars. This mash is held at specific temperatures to optimize sugar extraction.
Step 2: Lautering
The mash is then transferred to the lauter tun, where the liquid wort is separated from the solid grain husks. The wort is sparged (rinsed) with additional water to extract as much fermentable sugar as possible.
Step 3: Boiling
The wort is boiled in the brew kettle, during which hops are added at various stages for bitterness, flavor, and aroma. The boiling process also sterilizes the wort.
Step 4: Whirlpooling
After boiling, the wort is rapidly spun in the whirlpool to separate the solid particles (trub) from the clear wort. This step is crucial for achieving a clean, clear final product.
Step 5: Cooling
The wort is quickly cooled using a heat exchanger, bringing it to a temperature suitable for yeast activity during fermentation.
Step 6: Fermentation
The cooled wort is transferred to fermentation vessels, where yeast is added. The yeast converts the sugars in the wort into alcohol and carbon dioxide, transforming it into beer.
Step 7: Conditioning
After primary fermentation, the beer is moved to bright tanks, where it undergoes conditioning. This process may include additional aging, carbonation, and flavor adjustments.
Step 8: Packaging
Finally, the finished beer is packaged into kegs, bottles, or cans, ready for distribution and consumption.
Design, Capacity, and Layout of a 10bbl Brewhouse
The design, capacity, and layout of a 10bbl brewhouse are critical factors that affect both the brewing process and the operational efficiency of a brewery. Below is a detailed examination of these elements.
Aspect | Details |
---|---|
Design | The design of a 10bbl brewhouse typically includes a modular system that can be customized with various components such as multiple vessels, automated controls, and specialized fittings. The choice of materials, particularly stainless steel, is essential for ensuring durability and ease of cleaning. |
Capacity | A 10bbl system is designed to produce 10 barrels (or 310 gallons) of beer per batch. However, the actual yield may vary depending on factors such as the brewing method, grain bill, and system efficiency. |
Layout | The layout of a 10bbl brewhouse should be planned to maximize workflow efficiency. This involves arranging the mash tun, lauter tun, brew kettle, and fermentation vessels in a way that minimizes the movement of raw materials and finished products. Accessibility for cleaning and maintenance is also a key consideration. |
Customization Options for a 10bbl Brewhouse
Customization is a significant advantage when investing in a 10bbl brewhouse. Brewers can choose from various features and configurations to tailor the system to their specific needs. Common customization options include:
- Heating Method: Direct fire, steam, or electric heating.
- Automated Controls: Programmable logic controllers (PLCs) for automated brewing processes.
- Additional Vessels: Extra fermentation or conditioning tanks for increased production flexibility.
- Material Upgrades: Enhanced insulation, thicker stainless steel, or specialized coatings for increased durability.
Suppliers and Price Range for a 10bbl Brewhouse
Investing in a 10bbl brewhouse is a significant financial commitment. Therefore, it’s important to consider various suppliers and their offerings before making a decision. Here’s a comparison of some well-known suppliers, along with the typical price ranges for a 10bbl system.
Supplier | Price Range (USD) | Key Features |
---|---|---|
Alpha Brewing Operations | $100,000 – $250,000 | Customizable systems, high-quality stainless steel, and strong customer support. |
Blichmann Engineering | $80,000 – $200,000 | Known for innovative design, user-friendly systems, and reliability. |
Specific Mechanical Systems | $120,000 – $300,000 | Premium systems with extensive customization options and top-tier craftsmanship. |
Premier Stainless Systems | $110,000 – $275,000 | High-efficiency designs,robust construction, and excellent technical support. |
Ss Brewtech | $70,000 – $190,000 | Affordable, modular systems designed for easy expansion and scalability. |
Factors Influencing the Cost of a 10bbl Brewhouse
Several factors can influence the overall cost of a 10bbl brewhouse, including:
- Material Quality: Higher-grade stainless steel and advanced insulation increase durability and cost.
- Automation: Systems with PLCs and other automated controls typically cost more but offer greater efficiency.
- Customization: Additional vessels, unique configurations, and specialized components can raise the price.
- Brand Reputation: Established brands often charge a premium for their products due to their proven track records.
Installation, Operation, and Maintenance of a 10bbl Brewhouse
Once you’ve selected your 10bbl brewhouse, the next steps involve installation, operation, and ongoing maintenance. Proper planning and execution in these areas can prevent costly downtime and ensure a smooth brewing process.
Aspect | Details |
---|---|
Installation | Installation involves positioning the brewhouse components, connecting utilities (electricity, water, steam, etc.), and ensuring proper ventilation and drainage. Professional installation is recommended to ensure all systems function correctly. |
Operation | Operating a 10bbl brewhouse requires knowledge of brewing processes and system controls. Training from the manufacturer or a brewing consultant can be invaluable. Consider setting up standard operating procedures (SOPs) to ensure consistency in brewing. |
Maintenance | Regular maintenance is crucial to keep the brewhouse running efficiently. This includes cleaning, inspecting seals and gaskets, checking for leaks, and calibrating equipment. Scheduling routine maintenance can prevent unexpected breakdowns and extend the lifespan of the equipment. |
Preventative Maintenance Tips
- Regular Cleaning: Clean all vessels and lines after each brew to prevent contamination.
- Inspect Seals: Regularly check and replace seals to avoid leaks.
- Calibrate Sensors: Ensure all temperature and pressure sensors are correctly calibrated.
- Check Connections: Periodically inspect all connections for signs of wear or damage.
How to Choose the Right 10bbl Brewhouse Supplier
Choosing the right supplier for your 10bbl brewhouse is a critical decision that can affect your brewery’s long-term success. Here’s how to evaluate potential suppliers:
Criteria | Details |
---|---|
Reputation | Look for suppliers with strong industry reputations, positive reviews, and a history of successful installations. |
Customization Options | Ensure the supplier offers the customization options you need to meet your specific brewing requirements. |
Technical Support | Choose a supplier that provides robust technical support, including installation assistance and ongoing maintenance help. |
Pricing Transparency | A transparent pricing structure helps you avoid unexpected costs. Ask for detailed quotes that outline all expenses. |
Warranty and Service | Check the warranty terms and after-sales service options. A good warranty can save you money on repairs and replacements. |
Evaluating Supplier Credentials
- Industry Experience: Suppliers with extensive experience in the brewing industry are more likely to understand your needs and challenges.
- Portfolio: Ask to see examples of previous installations and talk to other brewers who have used their equipment.
- Customization Capabilities: Verify that the supplier can deliver on any specific customizations you require.
Comparing the Pros and Cons of a 10bbl Brewhouse
Like any brewing system, a 10bbl brewhouse has its advantages and limitations. Here’s a balanced look at the pros and cons:
Advantages | Disadvantages |
---|---|
Scalability: A 10bbl system offers enough capacity to expand production without massive overhead costs. | Initial Cost: The upfront investment is significant, which may be a barrier for smaller breweries. |
Efficiency: Allows for batch sizes that can meet moderate demand while maintaining control over the brewing process. | Space Requirements: A 10bbl system requires substantial space, which may not be available in all locations. |
Flexibility: Suitable for producing a wide range of beer styles, from small experimental batches to larger production runs. | Maintenance: More components and complexity mean more maintenance and potential for technical issues. |
Quality Control: Larger batch sizes still allow for artisanal quality control, ensuring consistent beer quality. | Learning Curve: Operating a larger system can be challenging for brewers accustomed to smaller setups. |
Is a 10bbl Brewhouse Right for Your Brewery?
Deciding whether a 10bbl brewhouse is right for your brewery depends on your current production needs, future growth plans, and financial resources. If you’re planning to expand your market reach or increase your product range, a 10bbl system could be the perfect size to accommodate that growth without overwhelming your team.
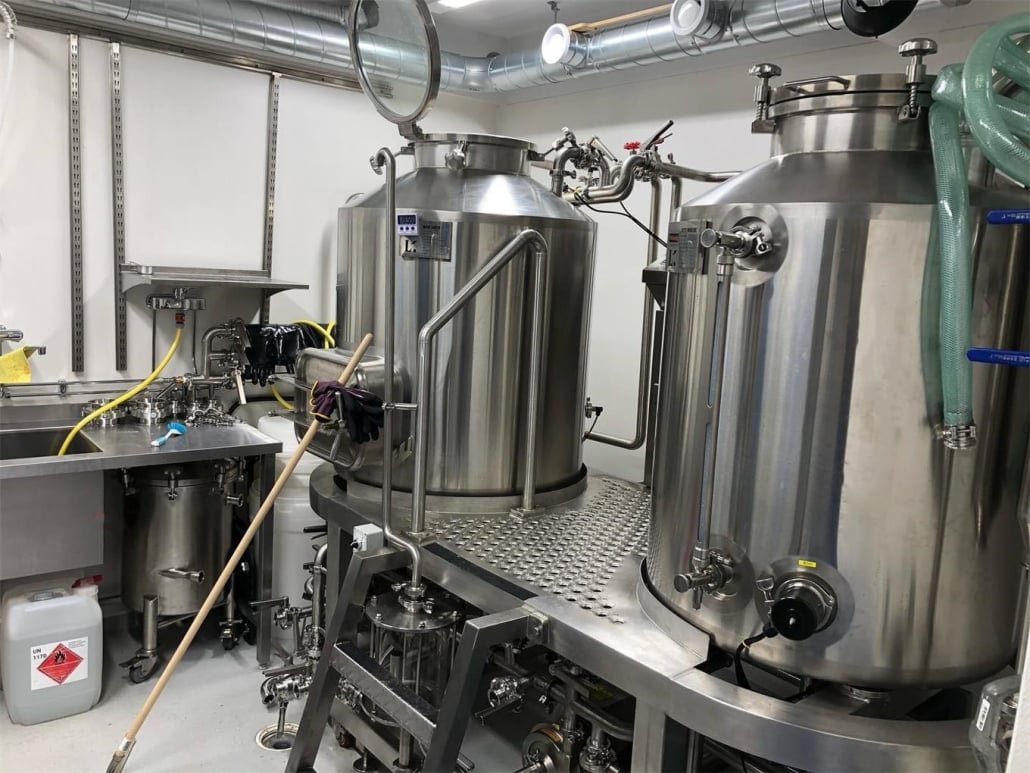
FAQ
To wrap up this comprehensive guide, let’s address some common questions about 10bbl brewhouses.
Question | Answer |
---|---|
What is a 10bbl brewhouse? | A 10bbl brewhouse is a brewing system with the capacity to produce 10 barrels (310 gallons) of beer per batch. It’s suitable for small to medium-sized craft breweries. |
How much does a 10bbl brewhouse cost? | Prices typically range from $70,000 to $300,000, depending on the supplier, customization options, and additional features. |
What are the key components of a 10bbl brewhouse? | A 10bbl brewhouse includes a mash tun, lauter tun, brew kettle/whirlpool, heat exchanger, fermentation vessels, and bright tanks. |
How long does it take to install a 10bbl brewhouse? | Installation can take several weeks to a few months, depending on the complexity of the system and the readiness of the site. |
Can I customize my 10bbl brewhouse? | Yes, most suppliers offer customization options, including additional vessels, automated controls, and specific material upgrades. |
Is a 10bbl brewhouse a good investment? | For breweries looking to expand production and distribution, a 10bbl brewhouse can be an excellent investment, balancing capacity with operational control. |
Conclusion
Investing in a 10bbl brewhouse is a significant step for any craft brewery looking to scale up. This size of system offers a balance between increased production capacity and the ability to maintain artisanal quality. From understanding the brewing process and equipment components to selecting the right supplier and managing costs, this guide has provided a thorough overview of what to expect.
As with any major investment, careful planning and research are essential. Take the time to evaluate your current needs, anticipate future growth, and choose a system that aligns with your long-term goals. With the right 10bbl brewhouse, your brewery can thrive, offering a diverse range of high-quality beers to an expanding market.