Overview of 60 Gallon Hop Back Equipment
A 60 gallon hop back is a key piece of equipment used in beer brewing systems after the wort boiler to filter and infuse hop aromas into the wort. It serves as a separator to remove hops and coagulated proteins while allowing improved hop extraction versus traditional methods.
60 Gallon Hop Back Equipment Guide
Equipment Type | Details |
---|---|
Hop Back | Vessel placed after the kettle to strain wort through whole leaf hops for aroma and flavor extraction |
60 gallon capacity | Suitable for 5-7 BBL commercial brewhouse batches |
Steel, stainless or copper material | Durable brewing equipment materials |
Cylindrical or rectangular | Typical shapes for efficient flow dynamics |
False bottom | Perforated plate to spread wort flow evenly over hops |
Input and output connections | For closed transfer to fermenter |
Canister or cartridge style | To contain hops and allow easy change outs |
Integrated sight glass | Visual wort flow and hop debris monitoring |
One-piece or modular | More compact or customizable options |
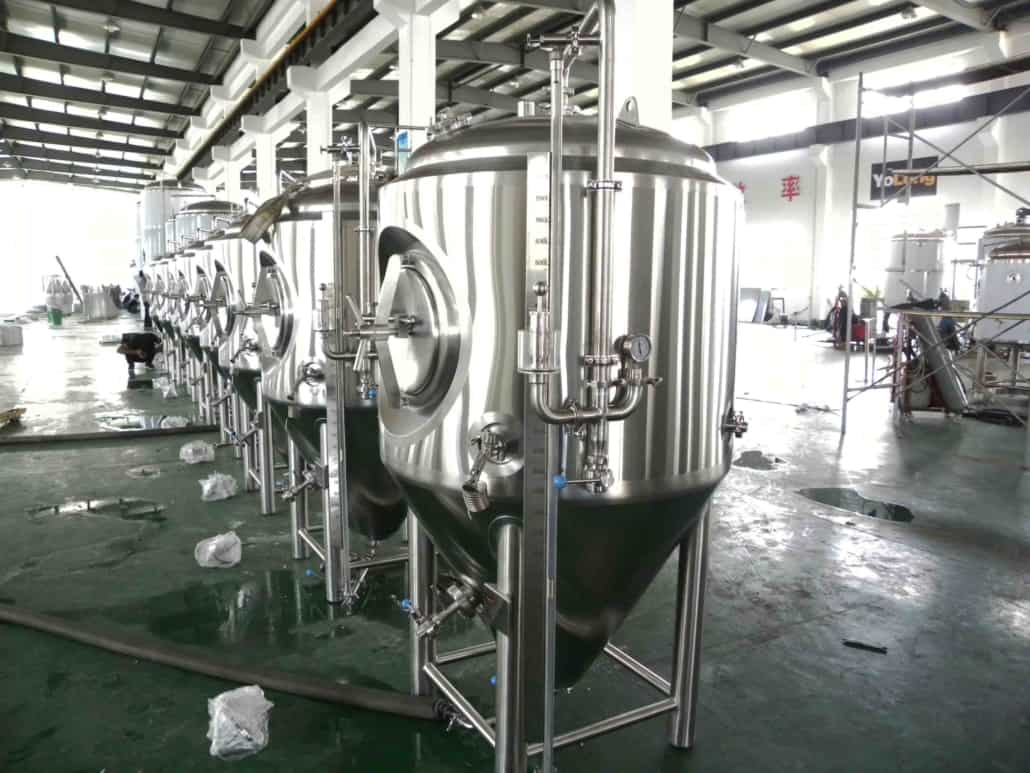
Brewing Process with 60 Gallon Hop Back
The 60 gallon hop back is ideally installed after the wort kettle to filter and infuse hop flavors into the hot wort flow. Models with input and output connections allow closed transfers to the fermenter or heat exchanger next in the sequence.
Whole leaf hops loaded into the vessel provide more aroma oils versus pellet hops. The false bottom spreads the wort stream to maximize exposure. This provides cleaner bitterness versus kettle hopping.
Integrated sight glasses on some units allow monitoring flow rate and removal of coagulated proteins and hop debris at a glance. Drain valves underneath simplify flushouts between batches.
60 Gallon Hop Back Design and Customization
Parameter | Details |
---|---|
Capacity | 50-70 gallons working volume typical |
Construction | Stainless steel or copper – durable, brew-safe metals |
Dimensions | 24-36″ diameter, 36-48″ height common |
Flow dynamics | Inlet at top, down flow through hop bed, outlet at bottom |
Modularity | Standalone or integrated multi-vessel brewhouses |
Customization | Embossed logos, sight glass, hop screening, input/output connections |
Automation | Electric actuated valves and switches available |
The 60 gallon capacity makes this size hop back well-matched for typical 5-7 barrel commercial brewery batches. Construction is commonly stainless steel for durability and brewing compatibility.
Cylindrical and rectangular shapes are both used, depending on space constraints and customization requirements. Dimensions are usually 24-36″ in diameter and 36-48″ tall. Multi-vessel brewhouse configurations allow the hop back to integrate modularly between the kettle and fermenters or heat exchanger.
Custom features like logos, sight glasses, input/output connects and hop screening mechanisms help tailor the hop back to specialized process needs. Electric actuated valves and switches automate several functions.
60 Gallon Hop Back Suppliers and Prices
Manufacturer | Price Range |
---|---|
JV Northwest | $3,500 – $6,000 |
Ss Brewtech | $3,200 – $5,500 |
Spike Brewing | $2,800 – $4,500 |
Craftwerk | $4,000 – $7,000 |
Stout Tanks | $3,000 – $5,000 |
Psycho Brew | $3,500 – $6,000 |
There are several equipment manufacturers serving the craft and mid-size commercial brewery markets with 60 gallon hop back solutions in the $3,000 to $6,000 price range. More customization, features and premium construction increase costs. Smaller scale models also available.
Factors like input/output connections fitted (additional $500-1,000 cost), sight glass ($350 extra), hop screening mechanisms ($450 added), digital temperature gauges (add $250-600), and logos/branding ($800+) impact pricing.
60 Gallon Hop Back Installation, Operation and Maintenance
Activity | Description |
---|---|
Installation | Secure vessel in place, connect hoses, fittings, switches |
Load hops | Fill canister/cartridge with whole leaf hops up to screen |
Begin wort flow | Start pump or gravity feed from kettle through inlet |
Monitor process | Check sight glass, make flow adjustments |
Flush clean | Clean w/ chemicals, flush with water, scrub residues |
Inspect and replace | Check for leaks, wear; replace gaskets, hoses |
Standard brewery equipment installation, safety and maintenance principles apply to installing and operating a 60 gallon hop back. Pay special attention to avoiding leaks from hoses and fittings downstream into fermentation.
Following manufacturer guidelines for cleaning chemicals and procedures ensures longevity. Regularly inspecting and replacing worn gaskets keeps efficiency and brewing performance optimal.
How to Select the Best 60 Gallon Hop Back Manufacturer
Consideration | Evaluation Criteria |
---|---|
Build quality | Material grade, welding, finishing, reviews |
Features | Screen, sight glass, valves, branding |
Customization | Fittings, dimensions, configurations |
Price value | Quote comparative models |
Lead time | Production and shipping duration |
Warranty | Years and coverage details |
Key aspects to evaluate when selecting a 60 gallon hop back equipment supplier for your brewhouse include build quality, customization options, price value comparisons, lead times and warranties.
Examine the stainless material grades used, precision welding seam appearance, surface finishing quality and online customer reviews as indicators of long term durability and brewing performance.
Consider which optional accessories serve your brewing process needs, from sight glasses to output connections. Dimensional configuration flexibility helps tailor the hop back layout. Review comparative pricing on models with similar functionality to identify deals.
Understanding lead times allows aligning equipment delivery to brewhouse commissioning schedules. Multi-year warranties provide reassurance on costly brew gear investments given intensive daily use.
60 Gallon Hop Back Pros, Cons, Advantages and Limitations
consider | Details |
---|---|
Pros | Improved hop oil extraction, wort filtration, aroma maximized versus kettle hopping, closed transfers enabled |
Cons | Added equipment expense, footprint, cleaning requirements |
Advantages | Greater process control and customization, optimizes bright hoppy styles |
Limitations | Throughput constrained by size, hop debris can clog |
Key pros of adding a 60 gallon hop back include better hop flavor and aromatic outcomes due to full immersion, along with clearer transferred wort after removing hops and coagulants. This comes at the cost of extra equipment, space requirements, and cleaning needs.
When engineered with features like a hop screen and sight glass, the process benefits outweigh the minor downsides for breweries seeking to optimize hoppy and hazy beer recipes.
The main constraints relate to the peak flow rate and batch size the vessel can handle. Clogging issues can also arise over time if hop particles accumulate or down-brew back flushing has inadequacies.
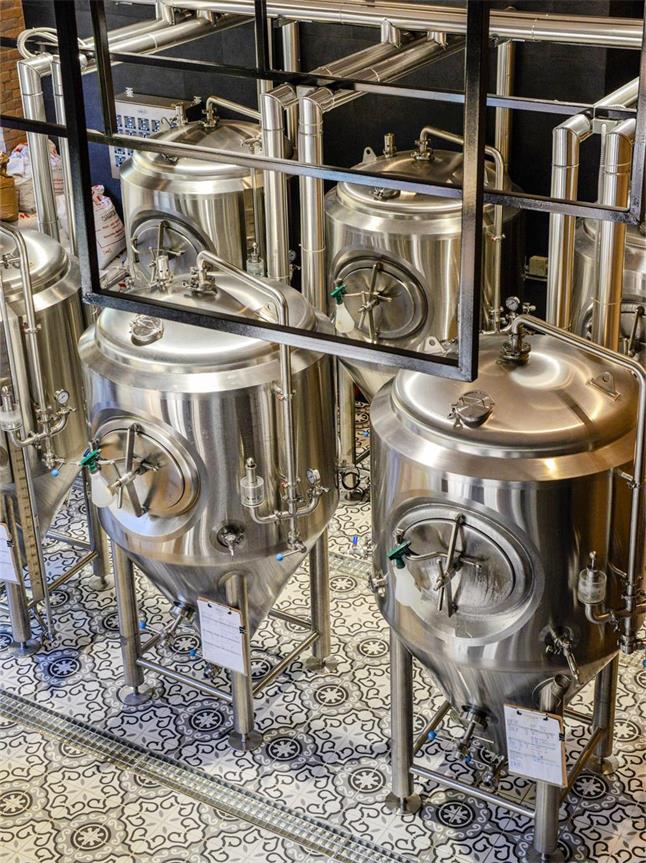
Frequently Asked Questions
Questions | Answers |
---|---|
What size batches can a 60 gallon hop back support? | Typically used for 5-7 barrel commercial batches |
What are the most important features to look for? | Hop basket screen, inlet/outlet connections, sight glass window |
Which manufacturers offer the best turnaround times currently? | Spike and Ss Brewtech have shorter lead times around 8 weeks out |
What are the optimal flow rates and contact time? | 1.5-2 GPM/ft2 flow, 20-30 min contact targets |
Does a hop back reduce brew house efficiency? | No effect if sized adequately for batch volumes |