7 BBL Brewhouse Systems
A 7 BBL Brewhouse is a medium-sized professional beer brewing system with a capacity of 7 barrels or 218 gallons per batch. This system allows craft breweries to produce beer on a commercial scale to sell locally or regionally.
This guide will provide a comprehensive overview of 7 BBL brewhouses including:
- Key specifications and equipment components
- Brewing process details
- Design and layout considerations
- Suppliers, pricing, and costs
- Installation, operation, and maintenance
- How to select the right system
- Comparisons between 7 BBL and other small brewhouses
- Advantages and limitations
Follow along for everything needed to understand, purchase, and use a 7 BBL brewhouse to start or expand a craft brewery business.
7 BBL Brewhouse Equipment Components
A complete 7 BBL brewhouse package consists of several key pieces of equipment for mashing, lautering, boiling, whirlpooling, cooling, and fermenting beer.
Table 1 shows the standard equipment included:
Equipment | Function |
---|---|
Mash tun | Mixes milled grains with hot water for mash conversion |
Lauter tun | Separates sweet wort from spent grains |
Brew kettle | Boils wort with hops for aroma and bitterness |
Whirlpool | Settles out proteins and hops |
Heat exchanger | Cools hot wort quickly prior to fermentation |
Fermenters | Ferments cooled wort into beer |
Glycol chiller | Cools fermenters and bright tanks |
Piping and valves | Transfers liquids between vessels |
Control panel | Automated system operation |
Additional equipment like milling, yeast management, carbonation, filtration, and packaging systems may be added as needed.
Table 2 shows typical capacity, dimensions, and vessel counts for a 7 BBL system:
Vessel | Capacity | Quantity | Dimensions (D x H) |
---|---|---|---|
Mash tun | 10 BBL | 1 | 5’6” x 5’ |
Lauter tun | 10 BBL | 1 | 5’6” x 5’ |
Brew kettle | 10 BBL | 1 | 6’6” x 6’6” |
Whirlpool | 7 BBL | 1 | 4’6” x 4’ |
Fermenters | 7 BBL | 3-4 | 3’6” x 6’-8’ |
Dimensions may vary across suppliers but tanks are designed to facilitate operations. Quantity of fermenters allows overlapping brews.
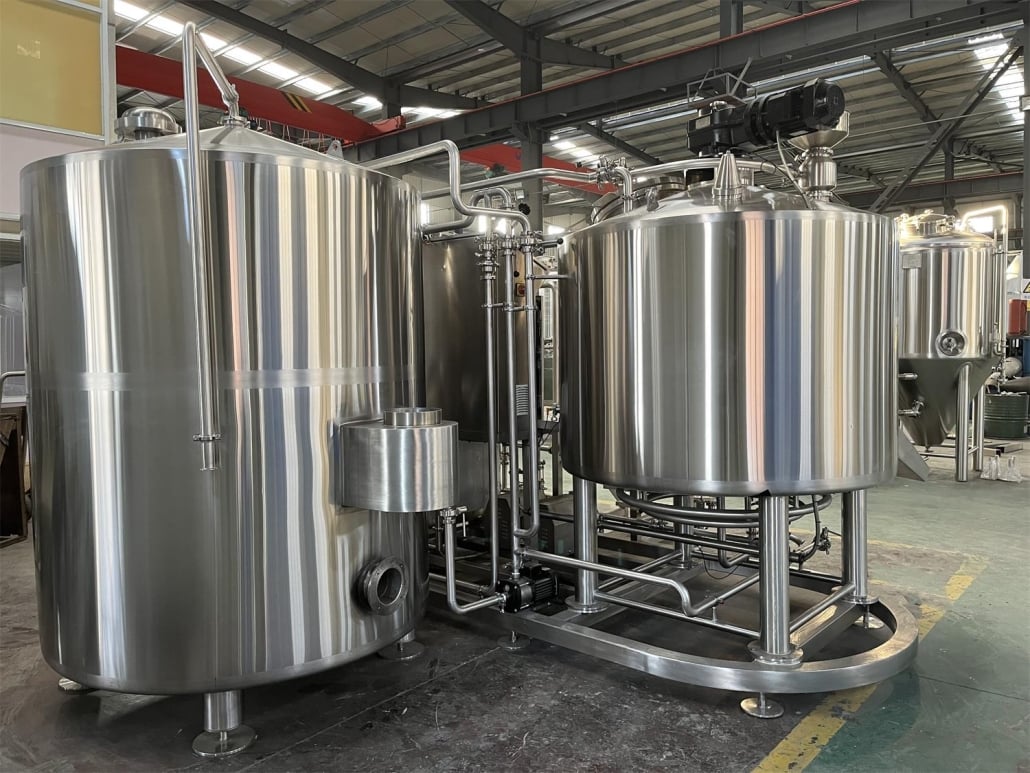
7 BBL Brewhouse Brewing Process
Figure 1 depicts the typical brewing process stages occurring within 7 BBL brewhouse equipment:
Milling – The whole malted barley grains are cracked open by roller mills to access starch.
Mashing – The milled grain is mixed with hot water in the mash tun and held at 150-155°F to convert starch into fermentable sugar.
Lautering – The sugar rich wort is drained from the grains in the lauter tun and sparged to extract more.
Boiling – The wort moves to the brew kettle and boils for 60-90 minutes with hop additions.
Whirlpooling – The hot wort spins to settle out hops and proteins after boiling.
Cooling – The clear wort passes through a plate heat exchanger to quickly drop temperature.
Fermenting – Yeast is added to cooled wort in fermenters and beer is produced.
Maturing – Beer clarifies and flavors meld during 1-4 weeks of cold storage.
Packaging – Finished beer moves to serving tanks, kegs, or cans.
Automated systems handle transferring liquids, turning equipment on and off, monitoring times and temperatures. Brewers oversee the process via touchscreen interfaces.
7 BBL Brewhouse Design and Layout
Proper brewhouse design and layout improves efficiency, workflow, and ergonomics for operators. Here are key considerations for a 7 BBL system:
Table 3: 7 BBL Brewhouse Design Factors
Design Aspect | Details |
---|---|
Floor space | ~800-1200 sq ft |
Ceiling height | 14+ feet for tank height |
Power supply | 240-480V, 150+ amp electrical service |
Boiler | Steam or hot water boiler |
Steam venting | Hoods for steam release |
Tank stands | Custom steel stands for ergonomics |
Piping runs | Sloped for drainage; valves for control |
Grain handling | Dry grain storage; platform and conveyor |
Refrigeration | Glycol or ammonia cooling lines |
Process control | Automated brewing sequences |
Cleaning | CIP spray balls and pumps |
Figure 2 shows a sample brewhouse layout:
Mash tun, lauter tun, and kettle are centrally located for gravity flow. Cooling, fermentation, and storage tanks are grouped. Grain handling equipment and control panels are accessible. Hot side tanks are raised by stands. Walls, dividers, and piping runs maintain separation. Proper design streamlines repetitive brewing operations in a small footprint minimizing hazards.
7 BBL Brewhouse Pricing from Suppliers
Many brewhouse engineering companies offer configurable 7 BBL systems with custom options affecting price ranges.
Table 4 provides pricing estimates from major suppliers:
Company | Base Price Range |
---|---|
Specific Mechanical | $250,000-$350,000 |
JV Northwest | $275,000-$375,000 |
Premier Stainless | $300,000-$400,000 |
Psycho Brew | $350,000-$450,000 |
AAA Metal Fabrication | $375,000-$475,000 |
Base pricing includes core brewhouse vessels, stands, valves, piping, panels, engineering drawings, and basic installation assistance.
Additional costs beyond base systems:
- Grain handling – $5,000+
- Glycol chilling – $15,000+
- CO2 capture and recovery – $25,000+
- CIP systems – $5,000+
- Automation computers and software – $15,000+
- Shipping and taxes – 10-15%
- Installation and commissioning – $15,000+
- Import duties if sourced overseas – 20%+
Total turnkey costs for a full 7 BBL production solution typically range $450,000 to $600,000+. Upfront capital needed is substantial.
Pricing is set by capabilities and level of customization. Configurable options affect budgets significantly. High-end systems provide more automation and clean-in-place functions at a premium.
Installation, Operation, and Maintenance
Proper installation and routine care ensures efficient functioning and longevity of a 7 BBL system.
Table 5: 7 BBL Brewhouse Installation, Operation & Maintenance
Phase | Details |
---|---|
Installation | Performed by brewhouse company reps and/or contractors Assemble tanks, stands, piping, panels, wiring to specifications Interfaces with supplied utilities – steam, water, drains, glycol, CO2, electricity Commissioning – test heating, cooling, automation, safety |
Operation | Conducted by brewers following procedures Clean and sanitize vessels between uses Prepare recipes, milled grains, yeast as inputs Monitor knockout, transfer, fermentation schedules Ensure constant utilities supply and glycol temperatures Conduct lab analysis – gravity, alcohol, microbiology etc. |
Maintenance | Both daily and periodic maintenance needed Inspect valves, seals for drips/leaks Check pump seal lubrication and circulator motors Clear grain handling obstructions Descale tanks and heating elements Replace gaskets, valves, sensors Calibrate temperature and pressure sensors |
Proactive preventative maintenance minimizes equipment downtime during peak brewing periods. Both operator experience and remote monitoring / troubleshooting support from brewhouse manufacturer may be advisable.
How to Select a 7 BBL Brewhouse Supplier
With custom 7 BBL brewhouses ranging $250,000+ in capital expenditure, selecting the ideal supplier is crucial long term.
Table 6: How to Choose a 7 BBL Brewhouse Supplier
Factor | Evaluation Criteria |
---|---|
Build quality | Reliable stainless steel vessel welds and finishes; food-grade material certificates |
Feature set | Valves, automation, glycol chilling, grain handling offered |
Customization | Flexible options – fermenter counts and heights, uniqueness |
Design services | Brewhouse layout recommendations, utility requirements |
Lead time | 10-16 weeks typical from order to delivery |
References | Call client references to learn about supplier responsiveness |
Warranties | Ensure at least 1 year workmanship warranties |
Ongoing support | Shipping, installation help offered; troubleshooting support plans |
Company stability | Research history and size to determine staying power |
Cost | Compare proposals and financing options like leasing |
Visiting existing brewhouses firsthand during the selection process is recommended to inspect build quality and see systems functioning.
Comparisons to 5 BBL and 15 BBL Systems
To determine the right brewhouse size, comparing smaller and larger systems against a 7 BBL is helpful for context:
Table 7: Comparison of 5 BBL vs 7 BBL vs 15 BBL Brewhouse Systems
Parameter | 5 BBL | 7 BBL | 15 BBL |
---|---|---|---|
Batch size | 155 gallons | 218 gallons | 465 gallons |
Annual beer output | 500 barrels | 700 barrels | 1500 barrels |
Fermenters needed | 2-3 | 3-4 | 6-8 |
Floor space | ~600 sq ft | ~800 sq ft | ~1500 sq ft |
Base price range | $175,000-$275,000 | $250,000-$350,000 | $400,000-$500,000 |
Time per batch | 4-5 hours | 5-6 hours | 8-10 hours |
Labor required | 1 brewer | 1-2 brewers | 2-3 brewers |
Target market | Taproom | Taproom + distribution | Distribution focus |
Key differences in tasks:
- 5 BBL – Mostly manual operation
- 7 BBL – Some automation assistance
- 15 BBL – Extensive automation required
As batch sizes grow, more time, labor, space, capital, and automation is required. 7 BBL systems represent a middle ground, enabling flagships and specialties to be brewed alongside core recipes for retail and moderate wholesale without excessive capacity.
Advantages of 7 BBL Brewhouses
There are several advantages to selecting a 7 barrel brewhouse system:
- Flexibility – 7 BBL is adaptable for taprooms, restaurant brewpubs, or packaging heavy production scaling up gradually without overly rapid expansion.
- Efficiency – Automated functionality improves consistency and repeatability between batches compared to small manual systems.
- Cost – Builds upon 5 BBL starter systems without 15+ barrel major investment outlays needed for packaging lines and distribution.
- Manageability – Does not require an extensive brewing team allowing staff to wear multiple hats. Head brewer can also be sales manager, cellar worker, pub manager, etc.
- Profitability – Higher revenue potential than 3-5 barrel nano setups while retaining ability to produce specialty beers without capacity constraints.
In terms of maximizing production diversity, business flexibility, product quality, and return on investment – 7 barrel brewhouse systems find an advantageous balance point accessible to many startups and growing regional craft breweries.
Potential Limitations of 7 BBL Systems
Despite significant advantages, there are still a few potential limitations to consider with 7 BBL brewhouses:
Market size – May exceed rural taproom or small pub capacity to sell all beer produced. Requires some packaging and distribution capability.
Ingredients access – Purchasing and storing large bulk grain quantities can be challenging for facilities lacking space. Requires good supplier logistics.
Brewing pace – Average 30 brews monthly is swift for a small team without extensive automation. Can be wearing over time.
Expansion barriers – Going from a 3-5 barrel system may allow simpler incremental capacity growth more easily than the larger leap to 7 barrels in volume presents.
Associated investments – Upgraded utilities, grain handling, refrigeration and wastewater infrastructure must support 7 BBL batches to unlock full advantage. Piecemeal upgrades may lag production growth.
For breweries facing any of these limitations, exploring brewhouse sizes on either side of 7 barrels may prove a better fit long term for business objectives.
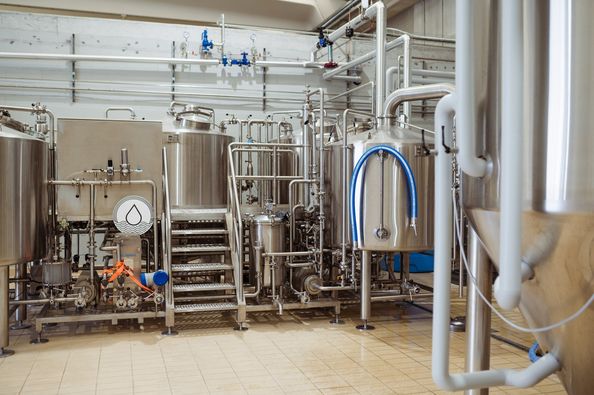
Frequently Asked Questions
What size batch can a 7 BBL brewhouse produce?
With 7 barrel (218 gallons) kettles, 6-7 barrels per batch is typical accounting for losses, trub space, and transfer. This equates to 31 batches needed monthly to produce 700 barrels annually working 5 days per week.
How much can a brewer produce annually on a 7 BBL system?
Operating 1-2 shifts daily, a single brewer can produce 500-1000 barrels annually depending on scheduling efficiency. More beers may be possible with an assistant brewer or push towards 24 hour utilization. 700 barrels balances pace appropriately.
What supplies are needed to operate a 7 BBL brewhouse?
Ongoing supply needs include: Ingredients – milled grains, hops, yeast, water treatment salts; Gases – CO2 for transfers, O2 for yeast; Consumables – cleaning chemicals, hoses, gaskets, filters; Lab supplies – testing reagents, media, glassware; Packaging – kegs, cans, bottles, labels.
How much space does a 7 barrel brewhouse require?
Approximately 800-1200 sq ft is needed for a 7 BBL brewhouse system itself. Plus additional space for grain storage and milling, fermentation cellar, cold storage, packaging lines, offices, and more. 3000+ sq ft facilities are common for long term growth.
What are the most important options to get with a 7 BBL system?
Automated glycol chilling, advanced brewing controls, and grain handling options provide the most daily operational advantages. More extensive CIP systems reduce heavy cleaning labor but increase costs.
What qualifications should brewers have for a 7 BBL system?
1+ years professional brewing experience is recommended managing comparable batch sizes. Strong capabilities in recipe development, process control, lab analysis, equipment maintenance, and managing cellar workflows separates more qualified candidates.
How many employees are needed to run a 7 BBL brewhouse?
For a taproom or brewpub selling beer on premises with limited packaging, 1 head brewer and 1 assistant can operate a 7 BBL system with occasional help from servers. Larger packaging focused breweries may engage 2 full time brewers, sales and delivery staff.
Conclusion
With capacities enabling 500-1000 barrel yearly outputs, 7 barrel brewhouses fulfill craft brewery needs to launch beyond a nano brewpub operation while avoiding excessive 15+ barrel systems solely for distribution. Sophisticated functionality improves upon manual smaller setups without over investing in space, staff, and packaging lines needed at a very large production scale.
From flexibility in recipe variations to effiencies in automated brewing – 7 BBL systems find a middle ground appealing to many regional facilities looking to grow. Their installations continue rising to fill demand between the extremes of too little capacity or too much.
Carefully weighting advantages around costs, production targets, business models and product mix leads breweries to settle on the 7 BBL brewhouse scale – not too big, and certainly not too small!
Share this entry
Interested in learning more about Brewing Systems including additional details and pricing information? Please use the form below to contact us!
YOLONG BREWERY EQUIPMENT FAQS
- Commercial Brewery / Craft Brewery / Microbrewery / Nanobrewery
- What is The Difference Between Craft Beer and Industrial Beer?
- The Bespoke Differences In Custom Brewing Systems
- Everything You Need to Know About Kettle Souring
- How to Choose Brewing Equipment for Your business?
- How To Choose The-Best Partner To Build Your Commercial Microbrewing System?
- Two Detection Sensors That You Need To Use In Your Brewhouse System
- Remote Control Applications in Brewing Equipment/How does it work?
- How To Clean Your Brand New Brewery Tanks?