10 BBL Stackable Brite Tanks
10 barrel (BBL) stackable brite tanks are stainless steel vessels used to store, condition, clarify, and carbonate beer after fermentation and before packaging. As the name suggests, these tanks have a capacity of 10 barrels, or approximately 310 gallons (1,173 liters).
Brite tanks are an essential component of a brewery’s production and packaging line. This equipment guide covers key considerations when investing in 10 BBL stackable brite tanks, including design, construction, customization options, installation, maintenance, suppliers, pricing, and more.
Types of 10 BBL Stackable Brite Tanks
There are two main types of 10 BBL brite tanks – vertical and horizontal:
Type | Description |
---|---|
Vertical | Cylindrical tanks that stack vertically to save floorspace. Have a smaller footprint. |
Horizontal | Longer, flatter tanks that lay on their side. Take up more floorspace but easier to inspect interior. |
Key Considerations When Choosing Brite Tank Type:
- Available brewery floorspace
- Desired clarity and sedimentation
- Budget
- Production workflow and packaging line layout
Both vertical and horizontal tank styles allow modular stacking configurations.
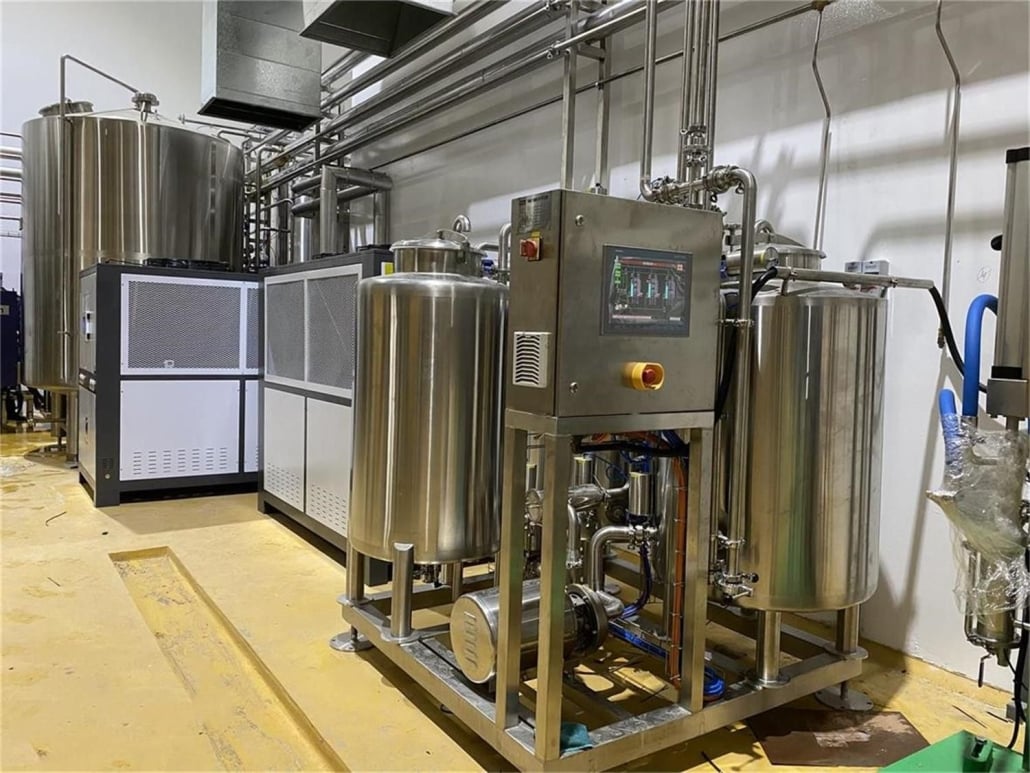
10 BBL Stackable Brite Tank Construction and Design
Component | Details |
---|---|
Vessel | Stainless steel – grade 304 or 316L. Fully welded, polished interior |
Legs/Base | Height adjustable stainless steel legs or frame. Optional casters for mobility |
Manways | 12-16” diameter ports for inspection and cleaning access |
Fittings | Sanitary stainless steel tri-clamp fittings. Optional sample valve and sight glass |
Insulation | 1-2” PU foam insulation wrapped in stainless steel |
Cooling System | Glycol cooling jacket and external heat exchanger |
Temperature Control | Digital PID controller and RTD sensor probes |
Key Design Factors:
- Number of stacked tanks
- Sanitation and ease of cleaning
- Temperature settings and insulation
- Adjustable height and mobility
- Access ports and fittings
Breweries differ on ideal brite tank configuration for their system based on these design factors. Most allow significant customization.
Customization Options for 10 BBL Stackable Brite Tanks
There are many ways breweries can customize 10 BBL stackable brite tanks:
Customization | Details |
---|---|
Stack height | From 1-5 high depending on available space |
Frame/legs | Casters, floor mounting plates, seismic anchoring options |
Manways | Size, number, positioning, special pass-through ports |
Hatch/lid | Bolt-on, davit, pneumatic, retractable lid systems |
Fittings | Sample valve, PRV, racking arm, carb stone location, CIP sprayballs |
External jacket | Half/full glycol or steam heated jacket |
Badges/logos | Custom etched or stamped branding |
Automation | Level sensors, proportional flow valves, remote telemetry |
Brewers can mix-and-match elements or create a fully customized tank set up. But more custom features increase cost.
10 BBL Stackable Brite Tank Suppliers and Pricing
There are many tank fabricators to choose from when buying 10 BBL stackable brite tanks:
Supplier | Location | Price Range* |
---|---|---|
JV Northwest | Canby, OR USA | $18,000 – $25,000 |
Stout Tanks | Portland, OR USA | $16,500 – $23,000 |
Steam Brothers | Milan, Italy | $22,000 – $32,000 |
Rolec Craft Brewing | Germany | $19,000 – $29,000 |
Maverick Stainless | Colorado USA | $15,000 – $21,000 |
* Per single 10 BBL tank
Pricing varies based on:
- Quantity ordered
- Level of customization
- Quality grades of steel
- Import taxes and freight
Breweries should get multiple quotes before selecting a brite tank supplier.
Choosing a 10 BBL Stackable Brite Tank Supplier
Here are key factors in choosing a 10 BBL stackable brite tank supplier
Consideration | Details |
---|---|
Reputation | Reviews and references from other breweries |
Quality | Welds, metal grades, craftsmanship |
Customization | Flexibility for custom tank features |
Lead Times | Production schedule and inventory levels |
Customer Service | Responsiveness to inquiries and issues |
Cost | Pricing and payment terms |
Warranties | Coverage duration and limitations |
Shipping | Included or separate line item |
Get bids from 3-5 fabricators before deciding. Review sample warranties closely.
10 BBL Stackable Brite Tank Installation
Proper installation is critical for 10 BBL stackable brite tanks to function safely and efficiently:
Task | Details |
---|---|
Assemble base | Attach legs or casters for mobility |
Position tanks | Layout distancing from walls/equipment |
Level tanks | Use adjustable legs and spirit level for precise alignment |
Install glycol system | Connect to external chiller and pump |
Install CIP system | Attach spray balls and cleaning lines |
Install automation | Connect level, temperature, flow sensors |
Pressure test | Check for leaks under 1.5 times working pressure |
Passivate | Circulate citric or nitric acid interior passivation solution |
Safety check | Verify emergency venting, controls, signage is in place |
A reputable tank fabricator will provide documentation on procedures and best practices.
Operating 10 BBL Stackable Brite Tanks
Day-to-day operation of 10 BBL brite tanks involves:
Activity | Procedure |
---|---|
Filling | Pump finished beer from fermenter through 0.5 micron filter |
Monitoring | Use level sensors and sight glass to track volume |
Temperature control | Set glycol system to 34-38°F for lagering/ clarifying |
Carb stone use | Diffuse CO2 into beer to reach target volumes of CO2 |
Emptying | Use sterile piping to transfer bright beer to packaging |
Cleaning | Clean with caustic/acid solutions using spray balls |
Sanitation | Final pass with sanitizer like peracetic or quat solution |
Record keeping | Note production volumes, dates, cleaning, conditions |
Following standard operating procedures ensures beer quality and safety.
Maintenance for 10 BBL Stackable Brite Tanks
Regular preventative maintenance is required to sustain performance and longevity of 10 BBL brite tanks:
Task | Frequency | Details |
---|---|---|
Interior Inspection | Quarterly | Check for corrosion, deposits, or biofilm buildup |
Gasket Replacement | Annually | Replace lid, hatch, manway gaskets |
Transition Rebuild | Every 5 years | Disassemble and rebuild piping transitions |
Passivation | As needed | Re-passivate corrosion prone welds |
Leg/Frame Adjustment | As needed | Re-level tanks if uneven settlement occurs |
Cooling Loop Leak Checks | Monthly | Monitor glycol system for tiny leaks |
Maintenance helps minimize beer loss and prevents equipment failures.
Pros and Cons of 10 BBL Stackable Brite Tanks
Here is a comparison of the advantages and limitations when using 10 BBL stackable brite tanks:
Pros | Cons |
---|---|
Stackable – Smaller footprint | Difficult interior access once stacked |
Modular expandability | Condensation dripping between stacked tanks |
Lower capital costs | Increased risk of oxygen exposure |
Mobile flexibility | Complex automation and controls |
Easier to maintain insulation | Heavy to ship and install |
The pros of efficiency and expandability often outweigh the cons for most breweries.
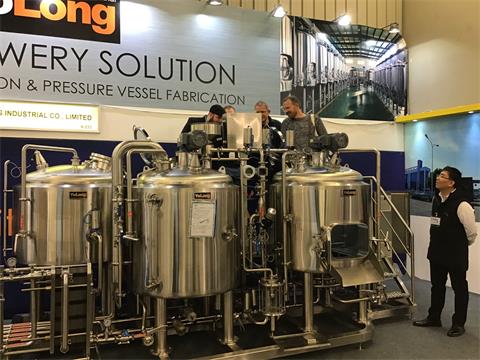
FAQ
Question | Answer |
---|---|
How many barrels in 10 BBL? | 10 BBL = 310 gallons or 1,173 liters |
What psi rating should brite tanks have? | Minimum 15 psi rating, 30 psi recommended |
What are brite tanks made of? | Tanks made from stainless steel – usually grade 304 or 316L |
Can brite tanks be repaired? | Yes, repairs possible but can be expensive if significant |
Do brite tanks require ASME certification? | Not mandatory but ASME stamp signifies quality standards met |
Conclusion
This structured content guide covered key considerations around 10 BBL stackable brite tanks – from construction, customization, installation to operation and maintenance procedures. Feel free to provide suggestions to add further details or improve the information provided!