10 BBL Brite Tank
10 barrel (BBL) brite tanks are stainless steel vessels used by craft breweries for conditioned beer storage and serving. With a capacity of 310 gallons or 43.2 kegs, these tanks allow efficient fermentation and storage before kegging or bottling beer. This guide covers key considerations when investing in 10 BBL brite tanks.
10 BBL Brite Tank Equipment Guide
Brite tanks, also called serving tanks or bright beer tanks, are pressure vessels that store filtered, carbonated beer while maintaining temperature, pressure, sanitation and gas mixes for proper conditioning. Well-designed brite tanks enable optimized beer production workflows.
Types of 10 BBL Brite Tanks
Type | Details |
---|---|
Cylindrical | Most common, horizontal orientation, efficient use of space |
Stacked | Vertical stacked tanks for smaller footprints |
Custom Shapes | Conical or special shapes for desired beer characteristics |
10 BBL Brite Tank Brewing Process
The 10 BBL brite tank is a key vessel between fermentation and packaging. After initial fermentation, beer is transferred into the brite tank for aging, clarification, carbonation and storage. Temperature and pressure are maintained prior to kegging, bottling or canning. Well-designed brite tanks simplify this process.
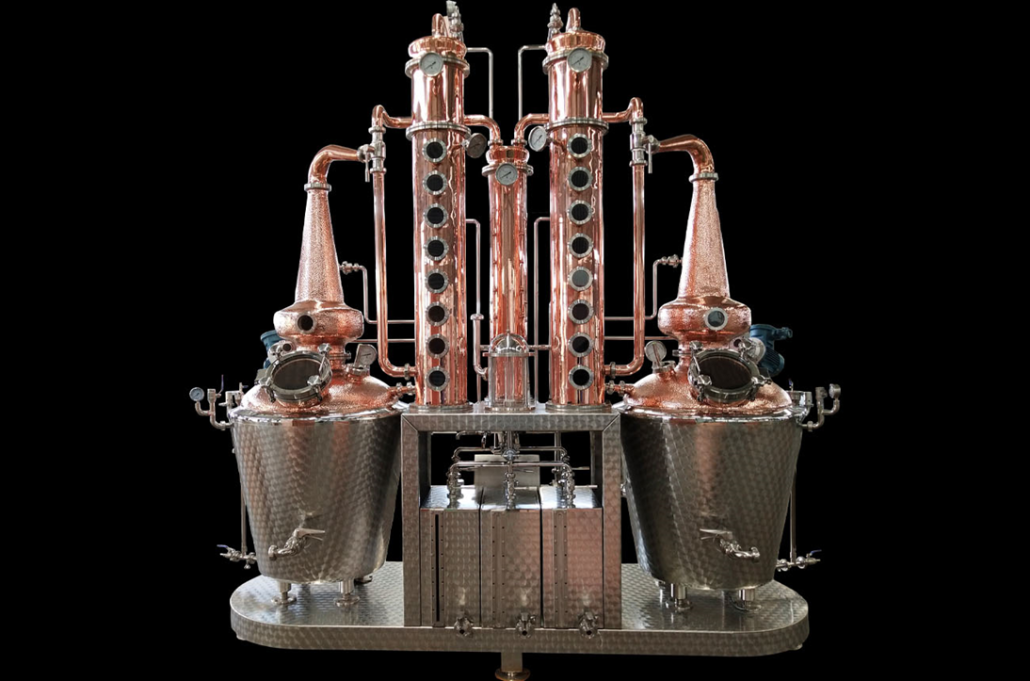
10 BBL Brite Tank Capacity, Design and Customization
Parameter | Details |
---|---|
Capacity | 10 BBL or 310 gallons or 43.2 kegs |
Construction | Stainless steel, single-walled or jacketed |
Dimensions | ~92″ tall, ~36″ diameter for cylindrical 10 BBL |
Layout | Horizontal or vertical stackable |
Design | Dish, cone or custom bottom; ports; valves; stands |
Customization | Manways, sights, insulation, glycol cooling, automation |
Tanks are customizable for desired conditioning, ease of operation and cleaning, and brewery workflow. Conical bottom tanks enhance yeast removal. Jacketing supports precise temperature control. Automated sensors monitor conditions.
Choosing a 10 BBL Brite Tank Supplier
Considerations |
---|
Build quality and materials |
Temperature and pressure ratings |
Sanitary design and cleaning |
Valves, ports, manways |
Automation capabilities |
Lead time and shipping |
Installation requirements |
Warranties and certifications |
Supplier experience and reputation |
Leading brite tank manufacturers include JV Northwest, Premier Stainless Systems, SS Brewtech, Paco and others. Shop around for the best match to brewery needs and specifications.
10 BBL Brite Tank Pricing
10 BBL Brite Tank | Price Range |
---|---|
Cylindrical Single-Wall | $8,000 – $12,000 |
Cylindrical Jacketed | $12,000 – $18,000 |
Conical Bottom | $14,000 – $22,000 |
Prices vary based on features, customization, brand and build quality. Get quotes from multiple vendors.
10 BBL Brite Tank Installation, Operation and Maintenance
Process | Details |
---|---|
Installation | Proper anchors, seals, connections for plumbing, cooling, cleaning, automation |
Operation | Monitoring temperature, pressure, carbonation, cleaning cycles |
Maintenance | Interior and exterior cleaning, replaced seals, valve repairs, prevent leaks |
Follow all manufacturer guidelines for safe installation and operation. Maintain detailed logs and establish preventative maintenance schedules.
How to Choose the Best 10 BBL Brite Tank
Consider brewery goals, production volume, available space, budget and growth plans when selecting a brite tank model and supplier:
- Match tank size, shape, layout and count to workflow
- Prioritize ease of cleaning, filling, emptying
- Validate quality construction for safety and longevity
- Compare cooling and insulation needs
- Review automation capabilities
- Confirm pressure, temperature and process measurements
- Evaluate after-sales support and warranties
- Get input from other local brewers
Comparing 10 BBL Brite Tank Options
Tank Type | Pros | Cons | Key Differences |
---|---|---|---|
Cylindrical | Efficient use of space, easier cleaning | Limit stackability, less yeast removal | Orientation, dish bottom standard |
Conical | Enhanced yeast removal, trub separation | Higher cost, larger footprint | Conical bottom improves clarification |
Single wall | Lower cost | Temperature fluctuations, condensation | No integrated cooling channels |
Jacketed | Precise temp control | Higher initial cost | Integrated cooling for consistency |
Premier Stainless | American made customizable tanks | Longer lead times, premium pricing | Broad range of config options |
JV Northwest | China produced commonly available | Quality assurance may vary, standard designs | Cost competitive import models |
SS Brewtech | Engineered drain technology | Proprietary fittings may lock in | Differentiating drain configurations |
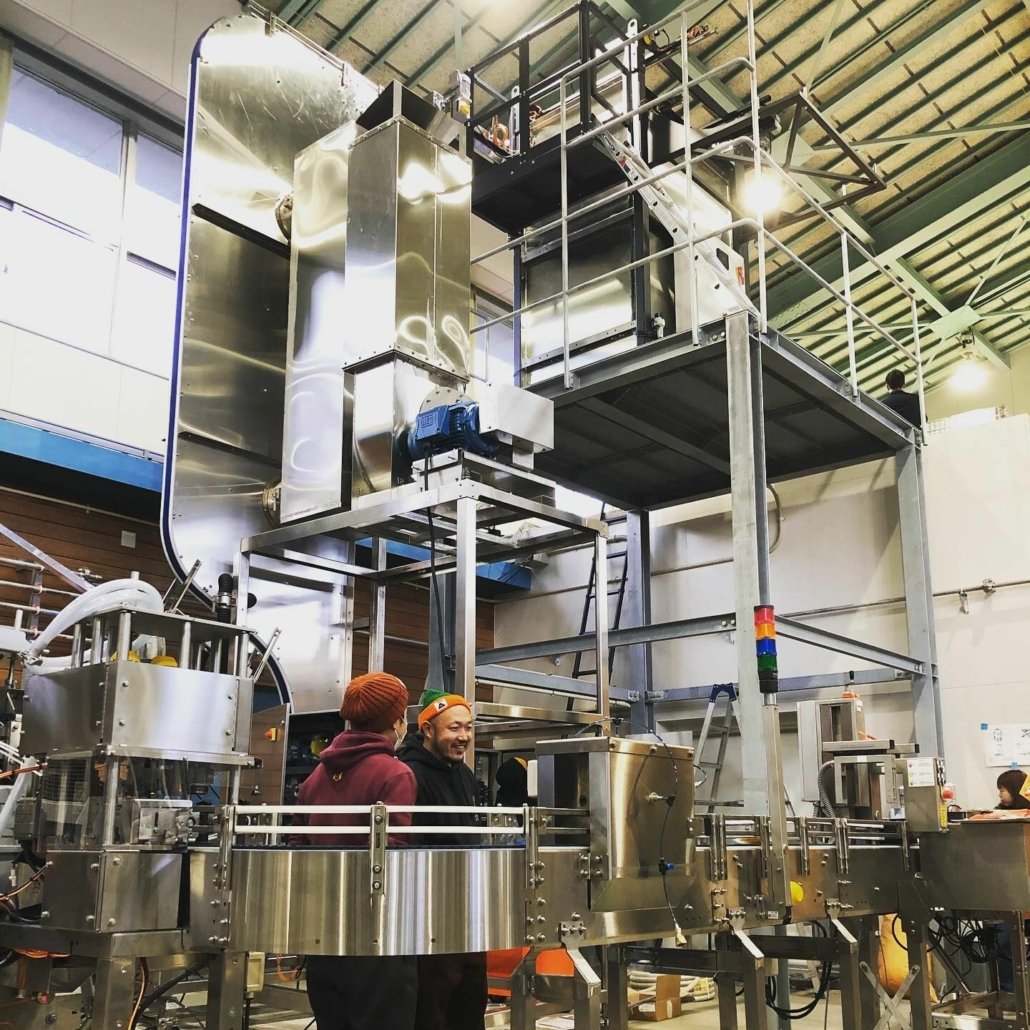
FAQ
What are the key factors that determine 10 BBL brite tank pricing?
The main factors affecting 10 BBL brite tank pricing are materials of construction (stainless steel grade), wall thickness, quality certifications, customization options selected (conical/shaped vs cylindrical; jacketed vs single wall; automation), manufacturer’s brand, reputation and manufacturing standards.
What are the optimal temperature and pressure parameters inside a 10 BBL brite tank?
Industry guidelines recommend maintaining 10 BBL brite tanks at 35-38 °F and 12-15 PSI during peak fermentation. Carbonation levels around 2.5 volumes of CO2 are preferred. Temperatures drop to 32-35°F for conditioned beer storage pre-packaging.
How often should 10 BBL brite tanks be cleaned and sanitized?
Thorough cleaning after every batch is essential – use alkaline followed by acid cleaners. For sanitization, brewers often clean daily and sanitize tanks immediately before use with chemicals like peracetic acid or phosphoric acid. Strict cleaning procedures are critical.
What are the most important criteria when selecting a 10 BBL brite tank vendor?
Key buying criteria to evaluate 10 BBL brite tank vendors on are: build quality, reliability and warranty; ease of maintenance and operation; customize configurations to meet current and future production goals; supplier experience and reputation for dependability; pricing value.
What automation capabilities help simplify 10 BBL brite tank management?
Helpful brite tank automation features include: automated temperature, pressure and level sensors; programmable logic controllers (PLCs); variable frequency drives on cooling pumps; actuated inlet/outlet valves; flow meters on transfers; raking arms if conical bottom tanks; integrated software for data tracking. Install components modularly.