7 BBL Brew Kettles
A 7 BBL Brew Kettle is a large brewing vessel used by commercial craft breweries to make beer. With a capacity of 7 barrels or 217 gallons (820 liters), a 7 BBL kettle allows small to mid-sized breweries to produce batches to fill fermenters and serve taproom customers. This guide covers key details on 7 barrel kettles.
Types of 7 BBL Brew Kettles
There are two main types of 7 BBL brew kettles:
Kettle Type | Details |
---|---|
Direct Fire Kettles | Heated directly by natural gas or propane burners. Lower cost, manual operation. |
Steam Jacketed Kettles | Heated indirectly through a steam jacket. Higher precision, automated process. |
Direct Fire Brew Kettles
Direct fire brew kettles feature burner heads installed underneath the kettle to provide direct heat. They are manually operated and lower cost. But they offer less temperature control compared to steam jackets.
Table 1: Direct Fire 7 BBL Brew Kettle Features
Feature | Details |
---|---|
Heating Method | Direct natural gas or propane burners |
Temperature Control | Manual via adjustable burners and lid |
Cost | Lower, $20,000 to $50,000 |
Automation | Minimal, manual operation |
Direct fire offers a simple, affordable brew kettle for new breweries with taproom sales. But temperature fluctuations can affect beer quality for distribution. Upgrading to steam heating later may be an option.
Steam Jacketed Brew Kettles
Steam jacketed brew kettles feature an outer shell that circulates steam to precisely control temperatures. Automated controls enable exact mashing, boiling, and knockout.
Table 2: Steam Jacketed 7 BBL Brew Kettle Features
Feature | Details |
---|---|
Heating Method | Indirect steam heat via jacket |
Temperature Control | Automated, precision sensors |
Cost | Higher, $80,000 to $150,000 |
Automation | Fully automated process |
While more expensive initially, steam jacketed kettles offer superior process control and repeatability for packaged beer sales. Their automation also improves safety. Many growing craft breweries invest in these systems.
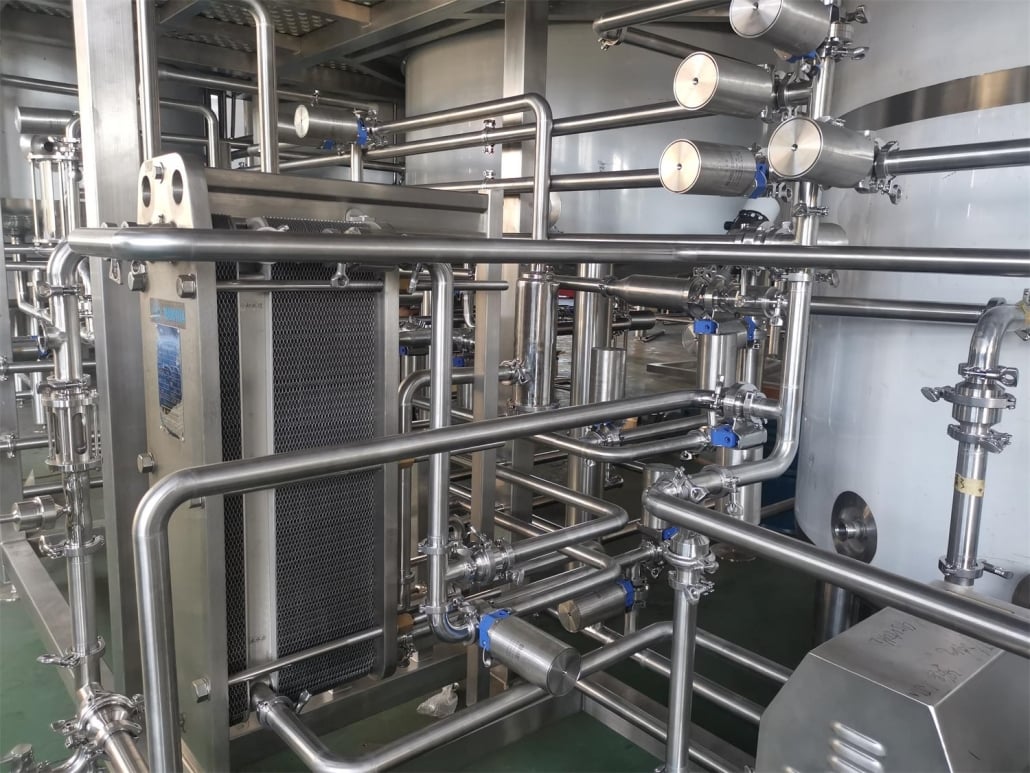
7 BBL Brewing Process
The typical brewing process in a 7 BBL kettle involves these key steps:
Table 3: 7 BBL Brewing Process Steps
Step | Purpose |
---|---|
Milling | Crack malt kernels to extract sugars |
Mashing | Mix milled grains with hot water, extract sugars |
Lautering | Separate sweet wort from spent grains |
Boiling | Concentrate wort, extract aromas, sterilize |
Whirlpooling | Rotate wort, collect trub at center |
Knockout | Pump clear wort to fermenter |
Fermentation | Yeast converts sugars to alcohol |
Maturation | Develop flavor compounds over weeks |
The wide, open shape of a brew kettle promotes effective mixing during mashing. Stronger direct fire or steam heating boils wort vigorously for hop isomerization. And rounded walls plus a whirlpool outlet concentrate solid particles for clean knockout to the fermenter.
Mashing in a 7 BBL Kettle
Mixing milled malt with hot water activates enzymes to convert starches to fermentable sugars. Maintaining the right temperatures in the mash maximizes sugar content.
With manual direct fire kettles, brewers monitor temperatures and adjust burner levels. Steam jackets use automated sensors and pumps to hit target temperatures precisely without scorching.
Lautering in a 7 BBL Kettle
Lautering separates sweet liquid wort from spent grains using a straining false bottom.
Manual brewers shovel out bags of grain by hand. Fully-automated kettles can self-empty grains mechanically into a waiting dump station.
Wort Boiling in a 7 BBL Kettle
Vigorously boiling wort isomerizes hop alpha acids, concentrates sugars, and sterilizes bacteria. Direct fire offers rapid heating from strong propane flames tuned by adjustable vents on each burner head.
Steam jacketed kettles use canned burners to generate 350°F+ steam which heats the entire jacket evenly. Boil intensity is controlled via variable steam pressure.
Boil duration ranges from 60 to 90 minutes depending on beer recipe. Brewers add hops at different times to impart bitter or aroma qualities.
Whirlpooling in 7 BBL
Whirlpooling uses a rotating paddle or pump to form a vortex in the wort after boiling. This concentrates solid particles and coagulated proteins (trub) in a cone at the bottom center.
Trub can lead to off-flavors during fermentation, so a strong whirlpool clears more wort. Brewers often let the whirlpool “settle” for 10-20 minutes before transferring clean wort to the fermenters.
7 BBL Brew Kettle Sizing and Capacity
When sizing a 7 barrel brew kettle system, there are several capacities to consider:
Table 4: 7 Barrel Brew Kettle Capacities
Capacity | Details |
---|---|
Total Volume | 217 gallons, 220 typical |
Working Capacity | 180 to 200 gallons |
Head Space | 15+ gallons |
Boil-Over Volume | 30+ gallons |
The total volume equals 217 gallons or 7 barrels. However most kettles are sized slightly larger at around 220 gallons to account for foam and equipment differences.
Working capacity during actual brewing operations averages 180-200 gallons accounting for grain absorption, trub loss, and other losses. This nets 5-6 barrels of sellable beer per batch.
Adequate head space above the working volume allows manual brewers to access the kettle safely. Automated kettles feature narrower heads but still require some room for sensors.
Boil over volume should handle a 30 gallon surge to contain messy foam-overs. So external height must allow this expansion.
7 BBL Brew Kettle Design and Layout
7 BBL kettles feature sturdy rounded shapes optimized for commercial brewing:
Table 5: 7 Barrel Brew Kettle Design Features
Feature | Details |
---|---|
Construction | Stainless steel, 5mm minimum |
Shape | Wide, shallow open cylinder |
Height | Typically around 84 inches |
Diameter | Approximately 5 feet |
Walls | Rounded for whirlpooling |
The open shape exposes large surface area for rapid heat transfer during boiling and knockout. Brewers can also easily access the wide top opening for cleaning and inspection.
Wall thickness over 5mm ensures durability through thousands of cycles. And electropolished interior helps prevent corrosion and bacterial growth.
Exterior height balances capacity needs vs. safe operation. Interior dimensions suit mash rakes, heating coils, plumbing, and vessels moving in and out during brewing.
Customization Options
Many kettle fabricators offer upgrades and options for added functionality:
- Insulated jacketed kettles reduce heat loss
- Integrated sight glass and tank volume markings
- Automated grain and water loading/unloading
- Integrated heating and cooling features
- Digital control panels, telemetry systems
- Casters for portable small batch kettles
7 BBL Brew Kettle Suppliers and Price Ranges
There are over a dozen brew kettle equipment suppliers across the US and internationally. Most offer direct fire and steam jacketed kettles in the 200 gallon range.
Table 6: 7BBL Brew Kettle Suppliers and Price Ranges
Company | Location | Price Range |
---|---|---|
Rolec Craft Brewing | USA | $30,000 – $100,000 |
Ss Brewtech | USA | $20,000 – $60,000 |
Colorado Brew Tech | USA | $15,000 – $40,000 |
AAA Metal Fabrication | Canada | $25,000 – $125,000 |
JV Northwest | USA | $25,000 – $150,000 |
PAKTON | Poland | $30,000 – $100,000 |
Gpi | Italy | $50,000 – $250,000 |
Pricing reflects degree of automation, custom features, brand reputation, and other value-adds like multi-vessel packages and turnkey brewery integration services. In general Chinese manufacturers offer lower pricing but US and EU vendors lead in technology, especially automation.
Installation, Operation and Maintenance of 7 BBL Kettles
Installing and running a 7 BBL brew kettle requires planning for utilities, space needs, safety procedures and maintenance.
Table 7: 7 BBL Brew Kettle Installation and Operation Details
Process | Equipment/Steps |
---|---|
Installation | – Flooring – smooth, waterproof, chemical resistant  – Ventilation – fumes, steam management  – Utilities – electricity, water, drains, gas lines  – Boiler system – steam generation |
Routine Operation | – Operator training – safety, procedures  – Grain handling system  – Brewing process by batches  – Clean-in-place (CIP) circulation |
Preventative Maintenance | – Interior/exterior washdowns  – Inspect welds, gaskets, fasteners  – Test automation and controls  – Delime heating coils and jackets |
Proper utility planning during design layout prevents rework down the road. Locating kettles near grain handling and boiler equipment improves workflow.
Daily operation procedures ensure sanitary conditions and repeatable processes batch-to-batch. Preventative maintenance minimizes downtime and replacement costs over decades of service.
How to Choose a 7 BBL Brew Kettle Supplier
Choosing a quality brew kettle tailored for a brewery’s needs requires careful evaluation of several vendor criteria:
Table 8: 7 BBL Brew Kettle Supplier Selection Criteria
Consideration | Assessment Factors |
---|---|
Quality | – Construction materials  – Welding and hardware  – Internals like false bottoms  – Compliance certifications |
Configurability | – Dimension customization  – Jacketing, insulation, valves  – Instrumentation, automation package |
Price | – Base pricing with transparency  – Value relative to offerings  – Total cost including shipping |
Vendor Reputation | – Years in business  – Client reference checks  – Installations in actual working breweries |
Services | – Quote and design assistance  – Equipment integration  – Operator training post-sales |
Prioritizing quality and support services tends to maximize long term equipment performance versus simply choosing the lowest bidder. Consider visiting an actual brewery using the company’s kettles to assess real-world functionality.
Comparing Pros and Cons of 7 BBL Kettle Options
There are inherent upsides and downsides with different 7 barrel kettle configurations to weigh:
Table 9: Pros and Cons Comparison of 7 BBL Kettles
Kettle Option | ||
Direct Fire | Steam Jacketed | |
Pros – Lower upfront cost – Simple manual operation – Quick heating with burners | Pros – Precise temp control – Fully automated – Even heating method | |
Cons – Temperature fluctuations – Labor intensive – Potential scorching | Cons – Higher upfront cost – Complex system – Slow initial heat up |
In general, direct fire suits low volume brewpubs while steam jacketed matches packaging breweries. Upgrading direct fire kettles with jackets is possible later too.
Frequently Asked Questions
What size batches can a 7 barrel brew kettle produce?
With around 200 gallons working capacity and accounting for losses, a 7 BBL kettle yields roughly 5 to 6 barrels (5.5 on average) of finished beer per batch.
What throughput can a 7BBL kettle handle?
Assuming 1.5 hour boils and 5 hour turnaround between batches, a single 7 barrel kettle can produce 10 batches weekly. So around 550 barrels annually. Higher volumes require additional cellar tanks and fermentation capacity.
How much space does a 7BBL kettle system need?
Plan for a 15×15 ft footprint minimum. Ceiling height should accommodate an 8 ft tall kettle plus overhead for loading grains, installing utilities, and headspace for boil overs or automation arms.
What utilities does a 7BBL brew kettle need?
Electrical for pumps and controls, natural gas or propane for heating, steam lines for jackets, chilled water lines for wort cooling, drains below floor grade, and fresh water.
How many people does it take to brew on a 7BBL system?
From 1 to 3 depending on automation level. Direct fire kettles need 2-3 people. Fully automated computerized steam kettles may just need a single brewer overseeing the batches.