6 BBL Brewery Equipment Guide
6 BBL Brewing Equipment is a common starter size for small commercial breweries looking to sell beer locally or self-distribute. With approximately 180 gallons per batch capacity, it enables efficient production while retaining flexibility to produce multiple styles.
6 BBL Brewing Equipment Guide
This section provides an equipment guide for key components in a 6 BBL Brewing Equipment.
Equipment | Description and Functions |
---|---|
Brew Kettle | The brew kettle is the vessel for mashing grains and wort production. A 7-8 BBL unit allows room for vigorous boils. |
Lauter Tun | This tank with a false bottom and raking system filters sweet wort from spent grains for sparging. |
Whirlpool | The whirlpool unit uses centrifugal force to separate hop particulates and coagulated proteins from clear wort. |
Heat Exchanger | A high efficiency heat exchanger rapidly cools hot wort to pitching temperatures before the fermenter. |
Fermentation Tanks | Multiple 7-8 BBL fermenters allow simultaneous fermentation of different beer varieties under control of temperature, pressure and yeast handling. |
Brite Tanks | Brite tanks store and carbonate finished beer. 6 BBL units can hold 1-2 batch volumes. |
Filtration | Whole house filters remove yeast, hop haze and solid particles for clear, stable beer. |
Transfer Pumps | Hygienic stainless pumps seamlessly transfer liquids between vessels. |
CIP Systems | Automated clean-in-place setup circulates hot caustic and acid solutions to sanitize all equipment. |
Control Panel | The control panel houses computer automation for about brewery operation parameters and data capture. |
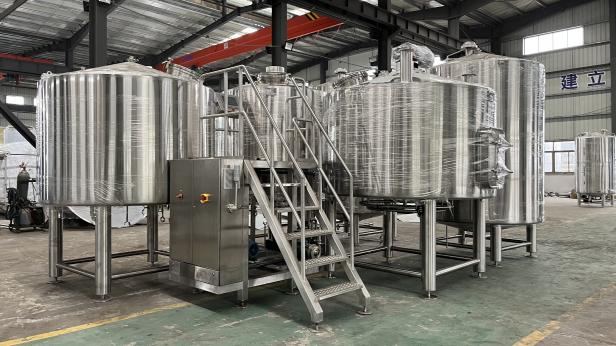
6 BBL Brewing Equipment Design and Customization
Key considerations for custom 6 BBL Brewing Equipment layout and functionality:
Element | Details |
---|---|
Production Scale | Batch size, annual output, peak capacity inform equipment sizing |
Facility Space | Optimized floorplan for 1000-1500 sq. ft. footprint with room for expansion |
Process Flow | Efficient worker and ingredient movements between brewing, fermenting, packaging, storage areas |
Budget | Balance production quality and automation levels based on capital expenditure budgets |
Timelines | Equipment lead times, permitting, installation schedule impact startup |
Safety and Regulations | Guarding, emergency stops, ventilation, licences, and brewery compliance |
6 BBL System Suppliers and Pricing
Supplier | Price Range | Offerings |
---|---|---|
Specific Mechanical Systems | $250,000 – $450,000 | Turnkey setups |
Portland Kettle Works | $200,000 – $350,000 | Custom fabrication |
Rolec | $180,000 – $280,000 | Flexible designs |
AAA Metal Fabrication | $150,000 – $250,000 | Value equipment |
Maverick Stainless Tanks | $300,000 – $500,000 | Premium systems |
*Pricing is indicative only; gets highly customized
Selecting a 6 BBL Brewing Equipment Supplier
Criteria | Considerations |
---|---|
Brewing Experience | Proven expertise in medium-scale brewhouse design and engineering |
Custom Fabrication | Ability to accommodate specialized layout or functionality requests |
Consultation Process | Guidance on equipment sizing, capacities, site considerations |
Build Quality and Materials | High-grade stainless steel, precision welding, reliability |
Production and Delivery Lead Times | Equipment availability and order fulfillment timelines |
Commissioning Support | Installation coordination, startup assistance, training |
Post-sales Service | Response time, availability of support crews and parts |
Budget and Value | System configurations matching capital expenditure budget |
Operating and Maintaining 6 BBL Systems
This section provides 6 BBL operation, cleaning and maintenance best practices:
Activity | Guidelines |
---|---|
Brewhouse Installation | Flooring, drainage, power, piping and ancillary capabilities must be ready before staging tanks. |
Safety Procedures | Staff training, emergency stops, equipment guarding and signage. |
Initial Production | Brewer assistance during first few batch process flows. |
Cleaning and Sanitation | Follow CIP protocols as per supplier manual for wash cycles and chemical use. |
Preventative Maintenance | Schedule periodic parts replacement, equipment lubrication, control panel backups as required. |
Annual Servicing | Installation company technicians conduct full brewhouse inspection, calibration, upgrades if needed. |
Key Pros and Cons of 6 BBL Brewing Equipment
Pros | Cons |
---|---|
Optimal flexibility and quality before large automated systems | Relatively high equipment cost per barrel of output |
Batch size fuels local taproom and distribution scale | Additional complexity from mixing, transferring, cleaning functions |
Supports a portfolio of specialty and seasonal offerings | 6-12 month lead time for custom fabrication and site preparation |
Preferred system for expanding brewpubs | May eventually need upgraded production capacity |
Customization for unique beer styles or branding | Requires significant brewing experience and training |
FAQs
Q: How much does a 6 BBL brewhouse cost?
A: The total equipment capital expenditure ranges from $200,000 to $500,000+ for a complete 6 BBL system. Costs vary widely based on customization and automation levels.
Q: What size space does a 6 BBL brewhouse require?
A: Plan for an approximately 1000 – 1500 sq. ft. brewhouse facility. The overall brewery size including fermentation room, cold storage etc. needs about 3000 sq. ft.
Q: How many people are needed to operate a 6 BBL setup?
A: Typically 1-2 skilled brewers can handle the semi-automated process. Additional staff helps with packaging and taproom operations as production scales up.
Q: What is the best 6 BBL turnkey supplier?
A: Leading options are Specific Mechanical Systems, Portland Kettle Works, Rolec and AAA Metal Fabrication – evaluate based on customization needs and budget.