Overview of 30 Gallon Hopback
A 30 gallon hopback is a piece of equipment used in breweries to filter hops and trub out of wort after the boil kettle and before fermentation. It serves as a settling tank to remove solids, utilizing the flow, gravity, and filtration to produce clearer wort.
30 Gallon Hopback Equipment Guide
Type | Description |
---|---|
Settling Tank | Cylindrical or rectangular vessel that utilizes flow control, filtration, and gravity settling to remove hops, proteins and sediment from hot wort after the boil kettle and before the fermenter. Size is typically 20-50 gallons. |
Filter Screen | Stainless steel mesh screen near the outlet to catch larger particles while allowing filtered wort to flow into the fermenter. Some models have a secondary finer filter screen. |
Inlet & Outlet | Strategically placed ports at different levels to control wort flow rate, direction and contact time with hops for more effective filtration. |
Stand | Short stand with adjustable legs to mount the settling tank at an angle and make optimum use of interior space by gravity settling. |
Cooling Coil | Some models integrate a cooling coil to help rapidly chill wort to pitching temperature as it flows through to the fermenter. |
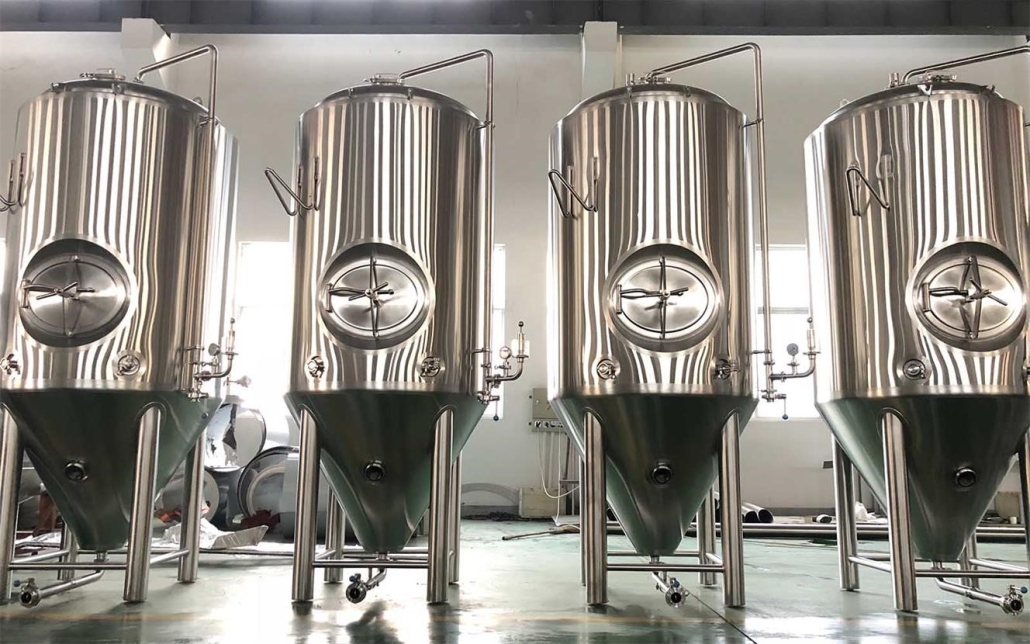
Brewing Process with 30 Gallon Hopback
The 30 gallon hopback is part of the post-boil wort clarification process in beer production:
- Wort is transferred from boil kettle through hopback inlet. Flow rate is controlled.
- As wort passes through bed of hops and narrow spaces, proteins and sediments drop out.
- Gravity settling also occurs with hopback installed at an angle to take advantage of interior space.
- Filter screens catch larger particles, producing clearer wort.
- Coarser trub settles out first, followed by finer sediment over contact time.
- More triangles and squares clarified wort passes through outlet to fermenter.
- After an entire batch runs through, hopback is cleaned and sanitized for next use.
30 Gallon Hopback Design Elements
Parameter | Options |
---|---|
Size | 20 gallons, 30 gallons, 50 gallons |
Shape | Cylindrical, Rectangular |
Material | Stainless Steel, Aluminum |
Legs | Fixed, Adjustable |
Ports | >1 inlet, >1 outlet with different diameters and placements |
Screens | Single coarse, Double with coarse & fine mesh |
Cooling Coil | Present/Absent |
Cover | Present/Absent |
Sight Glass | Present/Absent to check internal operation |
Flow Control | Butterfly valves on inlet and/or outlet ports |
Casters | Present/Absent for mobility |
Slope | Fixed or Adjustable from flat to steep angles |
Hop Addition | Top hatch for fresh/dry hop dosing |
Stand | Customizable height |
Automation | Programmable logic controllers possible |
30 Gallon Hopback Customization
30 gallon hopbacks allow a high degree of customization to suit process requirements:
- Shape and dimensions like diameter-to-height ratio can be specified
- Choice of number, placement and diameter of inlet/outlet ports
- Filter screen mesh size, single or double screen design
- Cooling coil, butterly valves, sight glass additions
- Adjustable vs fixed legs for angle and clearance
- Covered top, dry hop port, sample port options
- Mobility kit with casters – locked or swivel
- Automated cleaning and data collection abilities
Working closely with the manufacturer to discuss needs allows optimized design.
Suppliers and Price Range
Manufacturer | Price Range |
---|---|
JV Northwest | $1,500 – $4,000 |
Keg King | $1,200 – $3,000 |
Ss Brewtech | $2,500 – $5,000 |
Blichmann | $2,000 – $4,500 |
Premier Stainless | $1,800 – $4,000 |
The price range covers both manual and automated models. Factors like material used, number of custom features, brand reputation contribute to costs. Premier stainless systems with minimal features start around $1,800 while fully automated Bluetooth-enabled stainless steel hopbacks from Ss Brewtech can cost over $5,000.
Installation, Operation and Maintenance
Activity | Procedure |
---|---|
Installation | Uncrate and inspect unit Assemble stand kit if required Mount hopback at appropriate angle using adjustable legs Connect to brewing equipment with process piping inlet to boil kettle and outlet to fermenter Install immersion thermometer, flow control, sensors as needed |
Operation | Monitor flow rate and adjust to 2 GPM optimal Ensure outlet valves open before inlet valves to avoid pressure buildup Maintain 65C-73C ideal temperature range Utilize sight glasses to observe filtration efficiency and sediment levels Adjust duration and hopback angle to balance clarity and contact time |
Maintenance | Clean thoroughly after each use with alkaline cleaner, scrub inside surfaces Rinse away all visible debris from screens and containment areas Sanitize with acid-based no-rinse sanitizer prior to next batch Periodically inspect screens for damage and replace filters as needed |
Choosing Hopback Suppliers
Consideration | Guidance |
---|---|
Reputation | Select established suppliers with proven records of quality equipment supply and after-sales support spanning years |
Brewery Size | Match the usual batch sizes produced by the supplier’s clientele to your scale |
Customization | Choose manufacturers open to design discussions and custom options like valve types, screens used etc. |
Budget | Get quotes from multiple vendors once parameters are set to find best match of price to features |
Reliability | Ask past customers if the equipment requires frequent maintenance interventions or break-downs |
Lead Time | Imported equipment generally has longer fulfillment timelines compared to domestic manufacturers |
Review multiple supplier options in detail before finalizing to make an optimal purchase decision.
Pros, Cons and Limitations
Category | Advantages | Disadvantages |
---|---|---|
Filtration | Effectively filters hop particles, protein coagulants, and hot break trub Filters coarser to finer particles by gravity separation over time Dual screens for boosted filtration capacity Reduces transfer of trub to fermenter improving beer quality | Mesh screens can get clogged by hop debris or small openings No filtration of cold break particles Not fine enough for sterile filtration |
Cost | Fairly affordable setup even with customizations Can be an economical solution if traditional filtration methods too expensive Low recurring expenses other than periodic screen replacements | Highly automated systems with cooling jackets, electronic controls can get pricey Need to dedicate fermenter space and tie up inventory |
Convenience | Passively works using gravity to simplify process Minimal operator attention needed during runs Easy to clean and maintain after use | Requires extra space in brewhouse layout Not as consistent filtration performance as plate filters Flow rate and hop debris handling capacity limited by screen area |
Flexibility | Customization available for tanks, screens, ports, fittings, valves etc Can use for hop stands or dry hopping if needed | Limited in terms of batch size handling unlike full clarification systems Difficult to achieve precise level of clarity every run |
In summary, hopbacks provide intermediate hop haze and trub reduction between the hot wort and fermenter in a passive, affordable manner but lack advanced control and absolute predictability. They work best for small breweries looking for supplementary filtration on a budget.
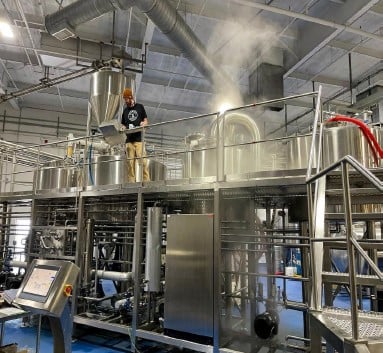
FAQ
Q: What size hopback is ideal for a 7 BBL brewhouse?
A: For a 7 BBL or 233 gallon brewery, a 30 gallon hopback is recommended to allow proper flow control and contact time. The ideal hopback size is 10-15% of brewhouse capacity.
Q: Should I get single stage or double stage filtration?
A: It depends on your clarity targets. For simpler hop particle and break material removal, a single large mesh screen like 0.079 inches (No. 7 mesh) is adequate. For finer filtration down to 100 microns, adding a second finer mesh screen like 0.047 inches (No. 16 mesh) is recommended.
Q: Where should I install the hopback in my brewery?
A: Locate the hopback close to the boil kettle outlet between the hot wort transfer lines and fermenter inlets so the hopback forms part of the cooling path. This helps utilize the thermal mass to start dropping the wort temperature prior to active chilling.
Q: How often should trub screens be changed?
A: Thorough periodic backflush cleaning after each batch can sustain filter screen performance for 6-12 months before requiring replacements. Visually inspect them during CIPs or maintenance breaks for tears, gaps or corrosionissues. Proactively swapping them out annually is also an option.
Q: Can hopbacks completely eliminate green beer syndrome?
A: While hopbacks substantially reduce transfer of debris, some very fine protein material and polyphenols can still pass through. So they mitigate rather than fully solve green beer issues. Additional techniques like silica dosing is needed for complete prevention.