1 BBL Brewing Equipment Guide
1 barrel (BBL) brewing systems are popular among craft and microbreweries looking to expand production beyond pilot batches. This comprehensive guide provides everything you need to know about selecting, installing, and operating 1 BBL brewing equipment.
Overview of 1 BBL Brewing Systems
A 1 BBL brewhouse produces about 31 gallons or 117 liters per batch. This capacity is suitable for microbreweries seeking to grow from homebrew or pilot systems up to a few hundred BBLs annual production.
Key features of 1 BBL breweries:
- All-grain brewing capability
- Automated process control
- Space-saving design
- Options for steam or electric heating
- Modular, customizable setup
- Brew 60-100 BBLs monthly
- Expandable to 3-5 BBLs
With a properly configured 1 BBL brewhouse, microbreweries can efficiently produce distinctive craft beers on a commercial scale while maintaining quality and consistency.
Types of 1 BBL Brewing Equipment
A complete 1 BBL brewery consists of the following major equipment:
1 BBL Brewing Equipment Types
Equipment | Description |
---|---|
Mash tun | Mixes milled grains with hot water for mash conversion |
Lauter tun | Separates sweet wort from spent grains |
Brew kettle | Boils wort and facilitates hop additions |
Whirlpool | Settles trub and hop debris |
Heat exchanger | Cools hot wort quickly prior to fermentation |
Fermenters | Ferment beer under controlled conditions |
Brite tanks | Carbonate and clarify beer before packaging |
Piping | Transfers wort and beer between vessels |
Control panels | Automate equipment with timers and sensors |
Additional equipment like grain mill, keg washer, filtration system, and cooling towers may be incorporated as per production needs.
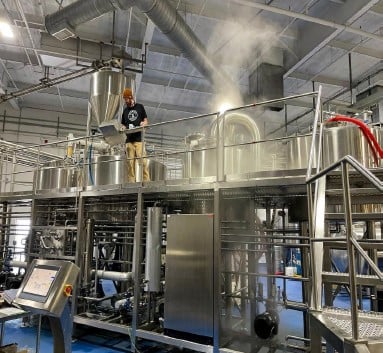
1 BBL Brewing Process
A typical all-grain brewing process using a 1 BBL system involves:
1 BBL Brewing Process
- Milling – Crush malt grains to specific coarseness
- Mashing – Mix crushed malt with hot water in mash tun at 150-160°F to convert starches to fermentable sugars
- Lautering – Recirculate wort through grain bed then sparge to extract sugars from grains
- Boiling – Boil wort at 212°F in brew kettle and add hops for bitterness, flavor, and aroma
- Whirlpooling – Create a vortex to settle trub and hops in center of kettle
- Wort cooling – Pass hot wort through plate chiller to rapidly cool to pitching temperature
- Fermentation – Pitch yeast into cooled wort in fermenter and allow 1-2 week primary fermentation
- Maturation – Transfer to brite tank for clarifying, carbonating, and cold conditioning
- Packaging – Transfer bright beer into kegs, cans, or bottles
Automated systems make it easy for a small team to brew consistently good beer each batch.
1 BBL Brewery Design and Layout
A 1 BBL brewhouse requires proper design and layout for an efficient process flow:
1 BBL Brewery Design Considerations
- Linear layout from raw materials to packaged product
- Ergonomic vessel heights and clearances
- Sloped floors with drains for cleaning
- Overhead pipe runs to avoid clutter
- Easy access doors and removable panels
- Open floorplan allows flexibility
- Room to expand tanks as production increases
Poor layout creates bottlenecks. A good design allows a smooth workflow and supports increased production in the future.
Customization Options
1 BBL systems can be customized to match brewery requirements:
1 BBL Brewery Customizations
- Electric vs steam heating
- Automatic vs manual operation
- Gas vs electric burners
- Jacketed vs conical fermenters
- 2-3 vessel vs 4-5 vessel brewery
- Fermentation temperature control
- Addition of brite tanks, filters, CIP
- Glycol vs refrigeration cooling
- Grain handling options – silo, auger, grist case
Working with a supplier to customize the system prevents issues down the line. Flexibility enables managing production variations.
1 BBL Brewing Equipment Suppliers
Reputable brewery equipment manufacturers offer quality 1 BBL systems:
1 BBL Brewing Equipment Suppliers
Supplier | Location | Price Range |
---|---|---|
Specific Mechanical | Canada | $100,000 – $150,000 |
Stout Tanks | USA | $80,000 – $120,000 |
JV Northwest | USA | $75,000 – $100,000 |
Premier Stainless | USA | $60,000 – $90,000 |
Rolec Prozess | Germany | $150,000 – $200,000 |
Prices vary based on features, customization, quality and brand reputation. Imported systems usually cost more.
How to Choose a 1 BBL System Supplier
Consider these factors when selecting a 1 BBL brewhouse supplier:
- Reputation and reviews
- Breadth of brewing experience
- Customization flexibility
- Equipment quality and durability
- Lead time and availability
- After-sales support and service
- Ability to handle future expansion
- Pricing and total cost of ownership
- Quick troubleshooting response
The right partner provides the best system for current needs and growth plans within budget.
1 BBL Brewery Installation
Proper installation is vital for smooth operation and maximum uptime.
1 BBL System Installation
- Check flooring, drainage, power, and utilities
- Uncrate and inspect all equipment
- Level and bolt down vessels securely
- Connect glycol, steam, and cooling lines
- Install piping runs and test for leaks
- Wire control panels and test electrical
- Program automation sequences
- Pass cleaning and calibration fluids
- Test full system operation and make tuning adjustments
Taking time to install correctly avoids issues later. Follow equipment manuals for each step.
Operating a 1 BBL Brewhouse
Follow best practices when operating a 1 BBL brewing system:
1 BBL Brewery Operation
- Control mash pH, temperature, and rest times
- Ensure vigorous boil for hop isomerization
- Carefully monitor fermentation profile
- Maintain proper pitch rate and yeast health
- Use standard operating procedures and batch records
- Take notes on taste and aroma at each stage
- Ensure consistency between batches
- Track key performance metrics
- Taste and test beer throughout process
- Fine-tune recipes and procedures
Meticulous operation and data tracking ensures quality, efficiency, and repeatability.
1 BBL Brewery Maintenance
Regular maintenance keeps the brewery running smoothly:
1 BBL System Maintenance
- Daily cleanup after brewing
- Weekly change oil and grease points
- Monthly check for leaks and unusual wear
- Quarterly validate temperature sensors
- Annual full system inspection
- Replace gaskets, hoses, and belts as needed
- Descaling and passivation of tanks
- Test electrical grounding and safety
- Confirm calibration of all instrumentation
- Check glycol and cooling loop chemistry
- Lubricate valves and moving parts
Both daily and scheduled yearly maintenance prevents unexpected downtime.
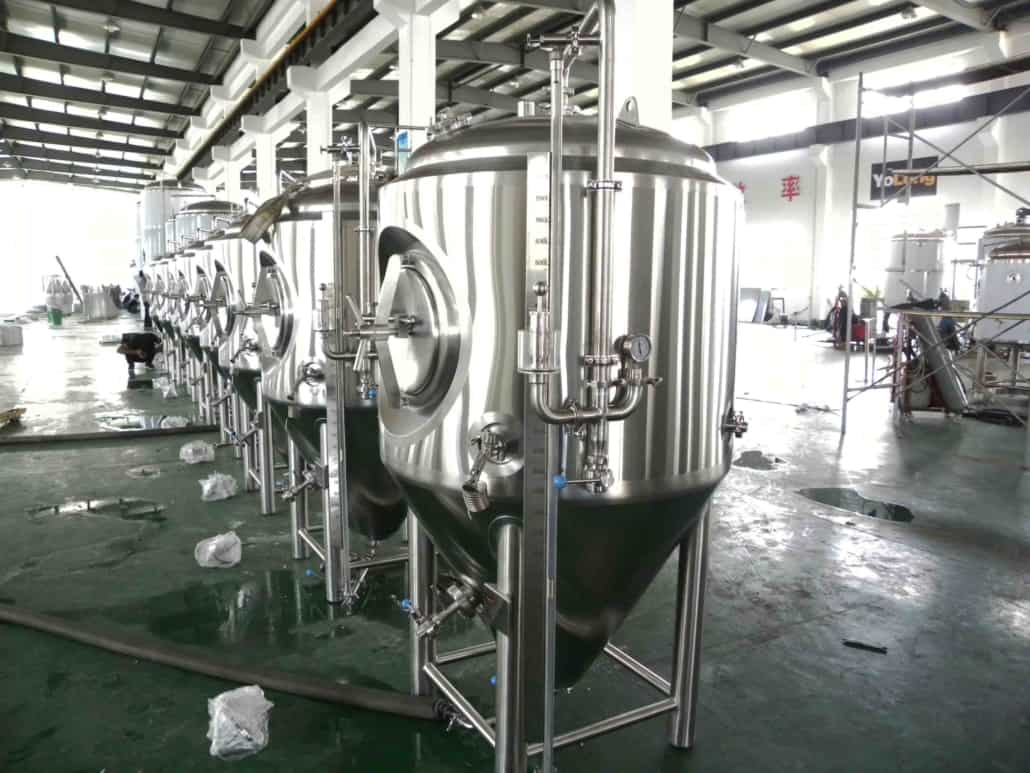
Pros and Cons of 1 BBL Breweries
Advantages of 1 BBL Systems
- Suitable scale for microbrewery expansion
- All-grain brewing capability for full recipe control
- Automated process increases consistency
- Flexible modular configuration
- Compact, space-saving design
- Lower capital cost than larger systems
- Allows brewing of specialty small batches
Disadvantages of 1 BBL Systems
- Limited maximum brew size
- Require good brewing skills and knowledge
- Careful monitoring needed to meet quality standards
- Additional labor for brewing multiple batches
- May still require supplementary equipment
- Expensive shipping and installation costs
- Handling expansion requires advanced planning
For breweries seeking to grow production in their existing space, a 1 BBL brewhouse balances capacity, flexibility, automation, and budget.
FAQs
Q: What size brewery is 1 BBL suitable for?
A: 1 BBL systems are designed for microbreweries looking to expand beyond pilot systems to produce 50-200 BBLs annually. The capacity is good for taprooms, restaurants, or small distribution.
Q: What raw materials are needed for a 1 BBL brewhouse?
A: Key raw materials include malt grains (barley malt, wheat, oats etc.), hops for bittering and aroma, yeast strains, and brewing salts and minerals. Adjuncts like fruit or coffee can be added for specialty beers.
Q: What utilities does a 1 BBL brewery require?
A: The key utilities required are electricity, water, steam (depending on system), chilled water for cooling, and drainage. Natural gas or propane may be needed for gas-fired heating.
Q: How much space does a 1 BBL system need?
A: Approximately 250-400 sq. ft. is required for the brewhouse alone. More space is needed for raw material storage, fermentation tanks, and packaging. Expect 1500-2000 sq. ft. total.
Q: What is the difference between automatic and manual 1 BBL systems?
A: Automatic systems have pre-programmed recipes and control panels that automate timing, temperatures, valves and pumps. Manual systems require the brewer to manually adjust each parameter.
Q: Does a 1 BBL system require a boiler?
A: If designed for steam heating, an external boiler provides steam to the vessels. Electric-heated systems use internal elements and do not need an external boiler.
Q: What types of fermenters work with 1 BBL breweries?
A: Conical and cylindrical jacketed fermenters from 500L to 2000L are commonly paired with 1 BBL brewhouses. More are added as production increases.
Q: How many people are needed to operate a 1 BBL system?
A: For a basic brew day, 1-2 skilled brewers can handle the full process. Additional labor helps with bottling, kegging, and packaging.
Q: How much beer can be produced monthly with a 1 BBL system?
A: Assuming 3 batches per week and 85% uptime, approximately 60-100 BBLs of beer can be brewed monthly on a 1 BBL system depending on batch size and efficiency.