Overview of 1.5 BBL Brewing Equipment
Craft breweries starting out often choose 1.5 barrel (BBL) brewing systems to pilot recipes while minimizing upfront capital investment. This capacity allows producing 465 gallons per batch for on-site tasting rooms and local sales. This guide provides a comprehensive look at 1.5 BBL brewhouse equipment, design, suppliers, pricing, installation and operations.
1.5 BBL Brewing Equipment Guide
A complete 1.5 BBL brewhouse requires various vessels and systems:
Types of 1.5 BBL Brewing Equipment
Equipment | Description |
---|---|
1.5 BBL Brew Kettle | Brews wort from mashed grains. Direct fire or steam heated. |
1.5 BBL Mash Tun | Converts grain starches to fermentable sugars via mashing. |
Hot Liquor Tank | Heats up strike and sparge water to proper temperatures. |
Wort Chiller | Cools boiled wort quickly before fermentation. Plate or immersion type. |
Fermenters | Stainless steel or plastic fermenters around 1.5 BBL. |
Brite Tank | Holds finished beer for clarifying, carbonating and storing. |
Glycol Chiller | Cools fermenters and brite tank using glycol. |
Heat Exchanger | Heats or cools liquids indirectly. Optional, but recommended. |
Piping | Food-grade stainless steel piping to transfer liquids. |
Pumps | Move liquids between vessels. Centrifugal or rotary vane. |
Grain Mill | Mills malted grain into grist for mashing. |
Control Panel | Controls pumps, temperatures, valves and more. |
1.5 BBL Brewing Process Overview
The main steps in brewing 1.5 BBL batches are:
- Milling – The grain bill is weighed out and milled into grist using the grain mill.
- Mashing – The grist is mixed with hot strike water in the mash tun to convert starches to fermentable sugars over 60-90 minutes.
- Lautering – The sweet wort is drained from the grains which are sparged to extract more wort.
- Boiling – The wort is boiled in the brew kettle for 60-90 minutes, adding hops at different stages.
- Cooling – The hot wort is rapidly chilled using a plate chiller or immersion chiller.
- Fermentation – The cooled wort goes into fermenters where yeast converts sugars to alcohol and CO2.
- Carbonation – Finished beer is carbonated in the brite tank and allowed to clarify.
- Packaging – Beer is put into kegs, cans or bottles for distribution.
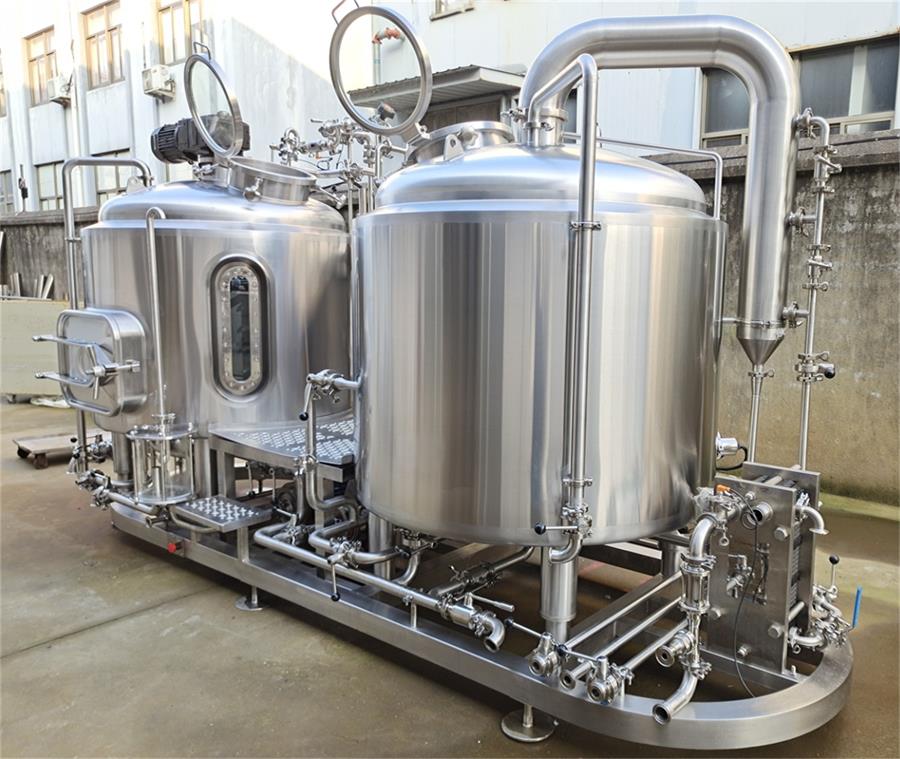
1.5 BBL Brewhouse Design Considerations
Designing an efficient 1.5 BBL brewery requires optimizing the layout and workflow:
Space Requirements
Allow approximately 800-1200 sq. ft. for a 1.5 BBL brewhouse and fermentation room. This provides space for future expansion when demand increases.
Equipment Layout
Arrange equipment in a logical workflow order from raw materials to finished packages to minimize transportation time and distances.
Ergonomics
Ensure pumps, valves, kettles and other components are easily accessible for operation, cleaning and maintenance. Platforms and stairs may be needed.
Utilities
Factor in electrical, water, wastewater and ventilation requirements. 1.5 BBL electric brewhouses need ~50 amps, 240V AC power.
Cleaning
Incorporate cleaning stations, sinks and space for storing chemicals and supplies.
Expansion Capability
Consider floor space, utilities and layouts that allow economically adding more fermenters later to scale up capacity.
Customization Options
While turnkey systems provide simplicity, custom 1.5 BBL brewhouses allow optimizing for specific goals:
- Craft Brew Kettle builds customized stainless kettles based on capacity, height, diameter and fittings.
- PolarFab, AAA Metalcraft, JV Northwest offer custom mash tuns tuned for mash efficiency.
- Glycol chillers can be sized for fermenters and brite tanks needed.
- Piping, pumps, platforms and walkways are designed for ergonomic workflows.
- Control panels can incorporate desired automation features and data tracking.
- Grain handling choices like grist cases, augers and mills suit needs.
Experienced brewery engineering firms help design 1.5 BBL systems tailored for your brewhouse. Customization does have higher upfront costs versus pre-packaged equipment.
1.5 BBL Brewing Equipment Suppliers and Pricing
Reputable brewing equipment manufacturers include:
Brewhouse Equipment Suppliers and Pricing
Equipment | Suppliers | Price Range |
---|---|---|
1.5 BBL Brew Kettle | Craft Brew Kettle, JV Northwest, PolarFab | $8,000 – $12,000 |
1.5 BBL Mash Tun | PolarFab, AAA Metalcraft, JV Northwest | $6,000 – $10,000 |
Hot Liquor Tank | Blichmann, PolarFab, JV Northwest | $2,500 – $4,000 |
Wort Chiller | JV Northwest, Coldbreak, EasyCool | $1,500 – $3,000 |
Fermentation Equipment Suppliers and Pricing
Equipment | Suppliers | Price Range |
---|---|---|
Fermenters | Spike, SS Brewtech, UniTanks | $1,500 – $4,000 |
Brite Tank | Spike, SS Brewtech, UniTanks | $1,500 – $3,000 |
Glycol Chiller | Coldbreak, EasyCool, JV Northwest | $4,000 – $6,000 |
Additional Equipment Suppliers and Pricing
Equipment | Suppliers | Price Range |
---|---|---|
Piping | JV Northwest, PolarFab, BrewHardware | $1,000 – $2,500 |
Pumps | EcoBrew, Chugger, March | $350 – $1,500 |
Grain Mill | Monster Mill, Cereal Killer | $200 – $500 |
Control Panel | BrewCommander, BrewLogic | $2,000 – $5,000 |
Research multiple vendors to get quotes meeting budget and quality needs. Local dealers may provide better service support.
Installation, Operation and Maintenance
Properly installing and maintaining a 1.5 BBL system ensures smooth operations and longevity:
Equipment Installation Best Practices
- Hire contractors experienced in brewery equipment installation.
- Verify flooring can support heavy vessels filled with liquid.
- Have proper utilities in place – electricity, water, drains, ventilation.
- Inspect all equipment thoroughly before first brew day. Calibrate sensors and test valves.
- Review operating manuals and train staff on each system.
Ongoing Operation Tips
- Follow manufacturer’s instructions for equipment use.
- Monitor process parameters like mash pH and temperature.
- Use brewing logs to record each batch. Track any issues.
- Maintain clean work environment and follow all safety procedures.
Maintenance Recommendations
- Perform preventive maintenance on pumps, valves, motors per schedules.
- Verify calibrated thermometers and sensors ensure accurate control.
- Lubricate equipment regularly per manufacturer specifications.
- Inspect fittings, gaskets, o-rings for wear and proactively replace.
- Disassemble and clean equipment thoroughly after each use.
Following a robust maintenance program prevents unexpected downtime and maintains consistency.
How to Select Reliable 1.5 BBL Brewing Equipment
Choosing high quality suppliers for 1.5 BBL brew systems ensures smooth startup and operations:
- Reputation – Well known in the industry for quality and service. Check brewer reviews.
- Experience – Many years providing commercial brewery equipment. Look for 10+ years.
- Customization – Ability to customize systems to your brewhouse goals. Avoid one-size-fits-all.
- Support – Responsive technical support and service capabilities. Local is better.
- Quality – Commercial grade stainless steel construction and components. Avoid plastic.
- Sizing – Ability to scale equipment to your current and future production needs.
- Delivery – Reasonable equipment fabrication and shipping lead times.
- Customer Service – Suppliers focused on your long term success. Easy to contact.
- Training – Willingness to train staff on proper use and maintenance.
- Certifications – Look for ASME and other certifications indicating quality.
Thoroughly vet potential vendors on these criteria before purchasing 1.5 BBL systems to find the best fit.
Pros and Cons of 1.5 BBL Brewing Equipment
Equipment | Pros | Cons |
---|---|---|
Direct Fire Kettles | Lower cost. Easier to repair and maintain. | Less efficient. Difficult temperature control. |
Steam Kettles | Precise temperature control. Energy efficient. | Higher upfront cost. More complex. |
Stainless Fermenters | Easy to clean and sanitize. Durable construction. | Expensive compared to plastic. |
Plastic Fermenters | Inexpensive. Lightweight. Transparent. | Scratches over time. Limited life span. |
Plate Chillers | Fast wort cooling. Compact size. | Risk of fouling or clogging channels. |
Immersion Chillers | Simple to use and maintain. No fouling issues. | Slower cooling. Open to contamination. |
Evaluate the advantages and disadvantages of each equipment option carefully before purchasing 1.5 BBL systems.
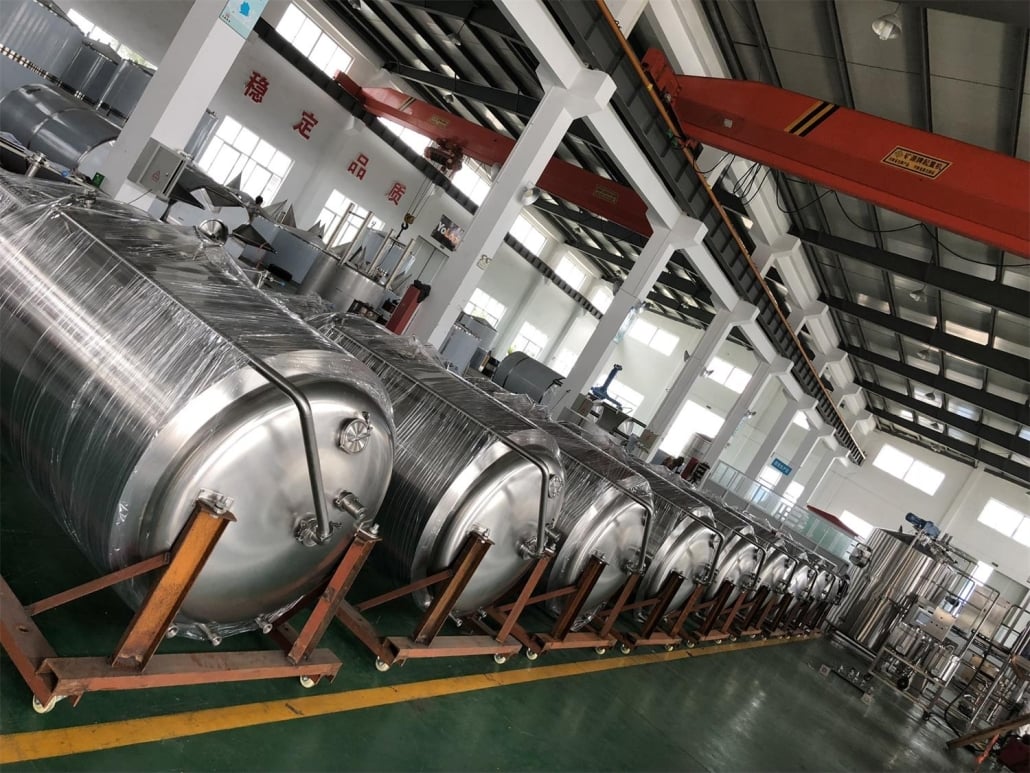
FAQ
What is the average cost of a 1.5 BBL start-up brewery?
A new 1.5 BBL electric brewhouse with fermenters, brite tank, glycol chiller, grain mill and other equipment typically costs $75,000 to $150,000. Buying used equipment or choosing simpler systems can lower startup costs.
What electrical requirements are needed?
Allow for roughly 50 amps, 240 volt AC electrical service for a basic 1.5 BBL electric brewhouse. This covers heating elements for the brew kettle and hot liquor tank. More amperage may be required based on additional equipment needs.
How much brewery space is needed for a 1.5 BBL system?
Allocate around 800-1200 sq. ft for a 1.5 BBL brewhouse and fermentation area. This allows adequate space for the equipment, storage, production workflow and room to expand fermentation tanks later.
What are the most important brewery design considerations?
- Logical workflow from grain mill to fermentation to avoid backtracking.
- Sufficient space around vessels for operation, cleaning and maintenance access.
- Flooring that can withstand heavy loads when full.
- Allowance for expansion of fermentation tanks.
- Proximity of electrical and plumbing utilities to equipment.
- Ventilation and drainage.
Should I buy new or used 1.5 BBL equipment?
Buying new equipment eliminates uncertainty about prior use and condition. But quality used 1.5 BBL systems professionally refurbished by reputable suppliers can be more economical. Inspect carefully before purchasing.
Conclusion
Starting with a pilot 1.5 BBL brewhouse allows craft brewers to test recipes on a small scale while keeping equipment costs manageable. With careful planning for the space, utilities, layout, and workflow, a 1.5 BBL system can form a solid foundation for growth. Choosing high quality equipment and keeping up with preventive maintenance avoids many headaches down the road. Partnering with experienced suppliers focused on your success provides confidence. With strategic thinking and passion, a 1.5 BBL microbrewery can turn hobby brewing into a thriving business.