The Complete Guide to Microbrewery Machines
Microbreweries have exploded in popularity over the last decade, giving beer lovers and entrepreneurs a way to craft unique, small-batch beers. But behind every successful microbrewery is a well-designed microbrewery machine, the heart of any brewing operation. This article will dive deep into everything you need to know about microbrewery machines—from equipment types and processes to pricing, suppliers, and more. Let’s explore the world of brewing!
Overview: What is a Microbrewery Machine?
At its core, a microbrewery machine is an intricate system of brewing equipment used to produce small batches of beer. These machines are designed to cater to smaller-scale beer production, typically under 15,000 barrels annually. Unlike large commercial brewers, microbrewery machines allow for greater control over brewing techniques, ingredients, and flavors, giving brewers more creativity and flexibility.
Why Microbrewery Machines are Important: They are the backbone of the craft beer movement. These machines allow for creativity, experimentation, and smaller-scale production, which means beer enthusiasts can enjoy a wide variety of flavors, styles, and brews that aren’t mass-produced.
Key Features of Microbrewery Machines:
- Customization: Most microbrewery machines can be customized to fit the brewer’s needs.
- Scalability: Microbreweries can start small and scale up as demand grows.
- Control: High precision in controlling the brewing process ensures quality and consistency in each batch.
- Space-Efficiency: Many microbrewery setups are designed to optimize space in smaller environments.
Microbrewery Machine Equipment Guide
When diving into the world of microbrewing, selecting the right equipment is crucial. The brewing process requires a mix of machinery to handle different stages—from fermenting to bottling.
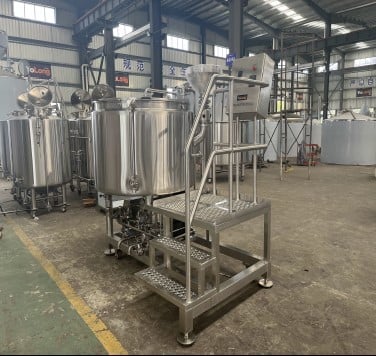
Types of Microbrewery Machines
In a microbrewery setup, different machines are designed for various parts of the brewing process. Let’s explore some of the essential components:
Equipment Type | Description |
---|---|
Mash Tun | A vessel where crushed grains and water are combined to convert starches into fermentable sugars. |
Lauter Tun | Separates the spent grain from the wort (liquid extracted from the mash). |
Fermentation Tank | Where yeast is added to the wort, turning sugars into alcohol and carbon dioxide. |
Brew Kettle | The wort is boiled here, typically with hops, to give the beer flavor and aroma. |
Heat Exchanger | Cools the wort down to the proper temperature for yeast fermentation. |
Bright Tank | A vessel used to hold beer for carbonation and maturation before bottling or kegging. |
Packaging Equipment | Machinery to bottle or keg the beer for distribution. |
The above components represent the backbone of the brewing process. Different machines serve various functions, but all are essential for brewing the perfect batch of beer.
Brewing Process in Detail
To understand how a microbrewery machine works, it’s important to look at the brewing process in detail. Brewing beer is both a science and an art. The process begins with selecting the right grains and hops, and it ends with packaging the final product. Here’s a closer look at the steps involved in beer production.
1. Milling the Grains
The process starts by crushing the malted barley (or other grains). The goal is to break the grains open, but not too finely, as that will affect the filtration process later.
2. Mashing
This step involves combining the crushed grains with water in a mash tun to convert the starches into fermentable sugars. This sugar-rich liquid is called wort.
3. Lautering
In this stage, the wort is separated from the spent grains. A lauter tun is used to allow the grains to settle while the wort is collected and moved to the next stage.
4. Boiling
The wort is boiled in a brew kettle. Hops are added at various stages during the boil, which affects the bitterness, aroma, and flavor of the beer.
5. Cooling
The wort needs to be cooled rapidly after boiling. A heat exchanger is often used to bring the temperature down to a level where yeast can be added safely.
6. Fermentation
The cooled wort is transferred into fermentation tanks, where yeast is added. Yeast consumes the sugars and converts them into alcohol and carbon dioxide. This stage can last anywhere from several days to weeks depending on the beer style.
7. Conditioning
Once fermentation is complete, the beer is transferred to a bright tank for conditioning. This allows for carbonation and maturation, ensuring the beer develops its final flavor.
8. Packaging
The final step involves bottling, canning, or kegging the beer for distribution. Packaging machinery can vary based on the production size and preferred packaging format.
Microbrewery Machine Design, Layout, Capacity, and Customization
Choosing the right design and layout for a microbrewery machine is vital to ensuring an efficient brewing process. Let’s break it down:
Feature | Details |
---|---|
Capacity | Microbrewery systems can range from small 2-barrel setups to larger systems capable of 15+ barrels. |
Space | The footprint of a microbrewery system varies but most machines are designed to fit smaller spaces. |
Design and Layout | A proper design ensures seamless workflow from grain milling to packaging. Customizable to fit the brewer’s needs. |
Customization | Breweries can customize the number of fermentation tanks, types of heat exchangers, and packaging options. |
A key consideration when designing your microbrewery layout is how much space you have and whether the system you choose will grow with your business.
Microbrewery Machine Suppliers and Price Range
Finding the right supplier for your microbrewery machine is essential. Pricing can vary significantly based on capacity, customization, and brand. Here’s an overview of some well-known suppliers and typical price ranges.
Supplier | Price Range (USD) | Notes |
---|---|---|
BrewBilt | $50,000 – $300,000+ | Known for premium, high-end custom systems. |
Ss Brewtech | $20,000 – $150,000 | Offers systems with an emphasis on home brewing up to small-scale commercial operations. |
PicoBrew | $10,000 – $50,000 | Offers smaller, tech-focused systems ideal for small craft brewers or experimental brewers. |
JVNW | $40,000 – $250,000 | Established supplier with a range of options for mid to larger-scale microbreweries. |
The price will largely depend on factors like capacity, customization options, and additional features such as automated controls.
How to Choose the Right Microbrewery Machine Supplier
When selecting a supplier for your microbrewery machine, several factors should be considered. Here’s a detailed guide:
Factor | What to Consider |
---|---|
Experience | How long has the supplier been in business? Do they specialize in microbreweries? |
Reputation | Check reviews, testimonials, and case studies. What do other brewers say about their systems? |
Customization Options | Can the supplier customize the system to meet your specific brewing needs? |
After-Sales Support | Will the supplier offer installation support, maintenance, and replacement parts? |
Price and Financing | Consider the price, but also ask if financing options are available. Look at long-term value over just cost. |
Installation, Operation, and Maintenance of Microbrewery Machines
Ensuring that your microbrewery machine is installed and operated correctly is critical for brewing success. Here’s what you need to know about each phase.
Aspect | Details |
---|---|
Installation | Installation involves setting up the equipment, connecting plumbing and electrical, and configuring controls. It should be done by professionals. |
Operation | Day-to-day operations involve monitoring the brewing process, maintaining correct temperatures, and ensuring the cleanliness of the equipment. |
Maintenance | Regular cleaning and sanitizing of the tanks, hoses, and other equipment are crucial to prevent contamination and prolong the machine’s lifespan. |
Maintenance is key to the longevity of your brewing system. Regularly inspecting and servicing your machine will prevent breakdowns and ensure your beer’s quality.
Advantages and Disadvantages of Microbrewery Machines
Let’s compare the pros and cons of using microbrewery machines:
Advantages | Disadvantages |
---|---|
Creative Control | Allows for flexibility in brewing styles, flavors, and experimentation. |
Cost-Effective for Small Batches | Ideal for producing small, high-quality batches, reducing waste. |
Scalable | Systems can be scaled as the business grows. |
Initial Investment | Microbrewery machines can be expensive to purchase and set up initially. |
Space Requirements | Even smaller systems require significant space, which may be a limitation in urban areas. |
Microbrewery machines offer a tremendous opportunity for creativity and profitability, but they require careful planning and investment upfront.
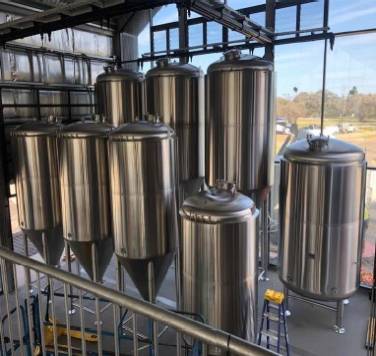
FAQ
Here’s a breakdown of common questions people have when considering microbrewery machines.
Question | Answer |
---|---|
How much space do I need for a microbrewery machine? | The space needed depends on the capacity of the system. Small systems can fit in spaces as small as 500 sq. ft. |
What’s the typical cost of a microbrewery machine? | Prices range from $10,000 to over $300,000, depending on size, customization, and features. |
How long does it take to install a system? | Installation typically takes 2 to 4 weeks, depending on the system’s complexity and the space available. |
Do I need a license to operate a microbrewery? | Yes, you’ll need proper licensing from your local and national regulatory bodies. |
Can microbrewery machines be automated? | Many modern systems offer automated features, making the brewing process more efficient and consistent. |
Conclusion
Investing in a microbrewery machine is a big step, but with the right equipment, you can turn your passion for beer into a thriving business. This guide provides the insights you need to choose the right machine, understand the brewing process, and make informed decisions along the way. Whether you’re just starting or looking to scale up, understanding these critical aspects will help you brew success!