Complete Guide to Understanding Vessel Brewhouse Systems
Overview of Vessel Brewhouse Systems
In the dynamic world of beer brewing, the vessel brewhouse stands as the heart and soul of the process. Whether you’re a homebrewer aspiring to take your craft to the next level or a commercial brewery aiming to scale operations, understanding the intricacies of a vessel brewhouse is crucial. This article is designed to provide an exhaustive overview of vessel brewhouse systems, touching upon everything from the types of equipment you’ll need to the brewing process, costs, installation, and maintenance. By the end of this guide, you’ll have a solid grasp of how to choose the right brewhouse for your needs, the costs involved, and how to operate and maintain it effectively.
Equipment Guide: Essentials of a Vessel Brewhouse
A vessel brewhouse is a complex system that brings together several key pieces of equipment. These vessels work in harmony to transform raw ingredients into beer, each playing a specific role in the brewing process. Here’s a breakdown of the essential equipment involved:
- Mash Tun: The mash tun is where the magic begins. Grains and water are mixed and heated to convert starches into fermentable sugars. This is the first step in creating the wort, the sweet liquid that eventually becomes beer.
- Lauter Tun: After mashing, the mixture is transferred to the lauter tun. Here, the wort is separated from the grain husks. The lauter tun has a slotted bottom, which allows the wort to drain through while holding back the solid grains.
- Brew Kettle: The brew kettle is where the wort is boiled, and hops are added. This step not only sterilizes the wort but also extracts bitterness, flavor, and aroma from the hops.
- Whirlpool: After boiling, the wort is transferred to the whirlpool vessel. This step helps to separate the solid particles (trub) from the liquid. The wort is spun rapidly, causing the solids to gather in the center, making it easier to separate them from the clear wort.
- Fermenter: Once the wort is cooled, it’s transferred to the fermenter, where yeast is added. Fermentation is the stage where sugars are converted into alcohol and CO2, turning wort into beer.
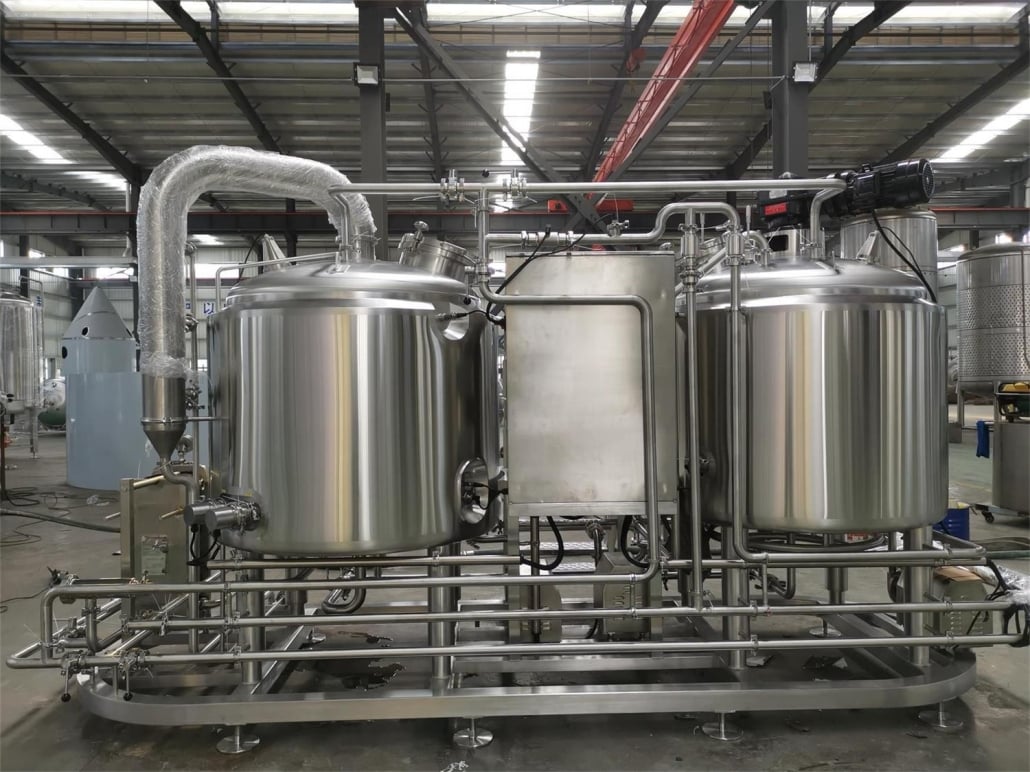
Brewing Process Explained: From Grain to Glass
The brewing process in a vessel brewhouse is both an art and a science. Each step plays a vital role in determining the final flavor, aroma, and texture of the beer. Let’s walk through the brewing process, elaborating on each stage to provide a comprehensive understanding.
- Mashing: The brewing process begins in the mash tun, where crushed malted grains are mixed with hot water. The temperature and duration of mashing are critical as they determine the types of sugars produced. A typical mash takes between 60 to 90 minutes and aims to create a wort rich in fermentable sugars.
- Lautering: After mashing, the wort is separated from the grain husks in the lauter tun. This process can take time, as the wort is drained slowly to ensure maximum extraction of sugars from the grains. Lautering efficiency plays a crucial role in the overall yield and quality of the beer.
- Boiling: The separated wort is then boiled in the brew kettle, usually for about 60 to 90 minutes. During this time, hops are added at various intervals to impart bitterness, flavor, and aroma to the beer. Boiling also helps to sterilize the wort and stop any enzymatic activity from the mashing stage.
- Whirlpooling: After boiling, the wort is transferred to the whirlpool vessel, where it’s spun rapidly to separate the trub. This step is essential for producing a clean beer, free from unwanted particulates that could affect flavor and clarity.
- Cooling and Fermentation: The hot wort is rapidly cooled to a temperature suitable for fermentation (typically between 65°F and 75°F). It’s then transferred to the fermenter, where yeast is added. Over the next several days to weeks, depending on the beer style, the yeast will convert the sugars into alcohol and carbon dioxide.
- Conditioning and Packaging: After fermentation, the beer is conditioned, which involves aging it to develop flavors and carbonation. Once the beer has reached the desired maturity, it’s packaged in bottles, cans, or kegs, ready to be enjoyed.
Understanding Equipment Types in a Vessel Brewhouse
Choosing the right equipment for your vessel brewhouse is critical to achieving the desired quality and scale of beer production. Below is a table that breaks down the types of equipment commonly used, along with their key features and considerations.
Equipment Type | Function | Key Features | Considerations |
---|---|---|---|
Mash Tun | Mashing | Insulated, Agitator, Temperature Control | Size, Material (Stainless Steel vs. Copper) |
Lauter Tun | Lautering | Slotted Bottom, Raking Mechanism | Efficiency, Ease of Cleaning |
Brew Kettle | Boiling | Heating Source (Direct Fire vs. Steam), Hop Addition Ports | Heating Efficiency, Capacity |
Whirlpool | Trub Separation | Rapid Spin Mechanism | Separation Efficiency, Design for Easy Trub Removal |
Fermenter | Fermentation | Temperature Control, Pressure Relief Valve | Size, Conical vs. Cylindroconical Design |
Design, Layout, and Customization of Vessel Brewhouses
When it comes to designing a vessel brewhouse, several factors must be considered to ensure the space is used efficiently and the system operates smoothly. The design and layout of your brewhouse can significantly impact productivity, ease of use, and scalability. Below is a table that outlines key aspects of design, layout, and customization.
Aspect | Details | Impact |
---|---|---|
Capacity | Measured in barrels per batch | Determines the scale of production and future scalability |
Space Requirements | Floor space, ceiling height | Affects installation feasibility and operational efficiency |
Workflow Optimization | Linear vs. Circular layout | Influences ease of movement and process flow |
Customization Options | Additional vessels, automation, aesthetics | Tailors the brewhouse to specific needs and brand image |
Cost Considerations: Price Range of Vessel Brewhouses
Investing in a vessel brewhouse requires careful financial planning. Costs can vary widely depending on the size, customization options, and supplier. Here’s a table that provides a general price range for different types of vessel brewhouses.
Brewhouse Type | Size (Barrels per Batch) | Price Range (USD) | Customization Costs |
---|---|---|---|
Small Scale | 1 – 5 barrels | $10,000 – $50,000 | $5,000 – $20,000 |
Medium Scale | 10 – 20 barrels | $50,000 – $200,000 | $20,000 – $50,000 |
Large Scale | 30+ barrels | $200,000 – $1,000,000+ | $50,000+ |
Supplier Selection: Choosing the Right Supplier for Vessel Brewhouses
Selecting the right supplier for your vessel brewhouse is just as important as choosing the right equipment. Here’s how you can evaluate potential suppliers:
Criteria | Considerations | Impact on Decision |
---|---|---|
Reputation | Reviews, industry standing | Ensures reliability and quality of service |
Customization Capabilities | Ability to meet specific design needs | Allows for tailored solutions that fit your requirements |
Support and Maintenance | Availability of support, warranty, training | Affects long-term usability and ease of maintenance |
Price | Competitive pricing, transparency | Impacts overall budget and value for money |
Installation, Operation, and Maintenance of Vessel Brewhouses
Getting your vessel brewhouse up and running is a multi-step process that requires careful planning and execution. Below is a detailed table on installation, operation, and maintenance to help guide you through the process.
Aspect | Details | Key Points |
---|---|---|
Installation | Site preparation, equipment setup | Professional installation recommended for optimal performance |
Operation | Daily operations, monitoring | Training on operational best practices is essential |
Maintenance | Regular cleaning, inspections, repairs | Preventative maintenance extends equipment lifespan |
Advantages and Disadvantages of Vessel Brewhouses
Understanding the pros and cons of vessel brewhouses is vital for making an informed decision. Here’s a comparative analysis of the advantages and limitations:
Aspect | Advantages | Disadvantages |
---|---|---|
Efficiency | High efficiency in wort production | Initial cost can be high |
Scalability | Easily scalable to meet growing demand | Requires significant space and infrastructure |
Quality Control | Allows precise control over the brewing process | Complex system may require skilled operators |
Customization | Highly customizable to fit specific brewing needs | Customization increases cost and lead time |
How to Choose the Right Vessel Brewhouse: A Step-by-Step Guide
Choosing the right vessel brewhouse involves evaluating several factors, including your brewing goals, budget, and available space. Here’s a step-by-step guide to help you make the best
decision:
- Assess Your Brewing Goals: Determine the scale of production you want to achieve. Are you brewing for a local pub, or do you plan to distribute widely? Your goals will dictate the size and type of brewhouse you need.
- Set a Budget: Brewhouses come in a wide range of prices. Determine how much you’re willing to invest upfront and what kind of financing options are available. Remember to account for customization, installation, and maintenance costs.
- Evaluate Your Space: Measure your available space and consider the layout of your brewhouse. Ensure there’s enough room for installation and future expansion. Pay attention to ceiling height, floor strength, and access for large equipment.
- Research Suppliers: Look for suppliers with a strong reputation and proven track record. Ask for references, read reviews, and consider visiting a facility to see their equipment in action.
- Consider Customization Needs: Do you need a brewhouse that’s tailored to specific brewing methods or aesthetics? Discuss customization options with potential suppliers to ensure the system meets your exact needs.
- Plan for Installation and Maintenance: Choose a supplier who offers comprehensive support, including installation and ongoing maintenance services. This ensures that your brewhouse will run smoothly and efficiently.
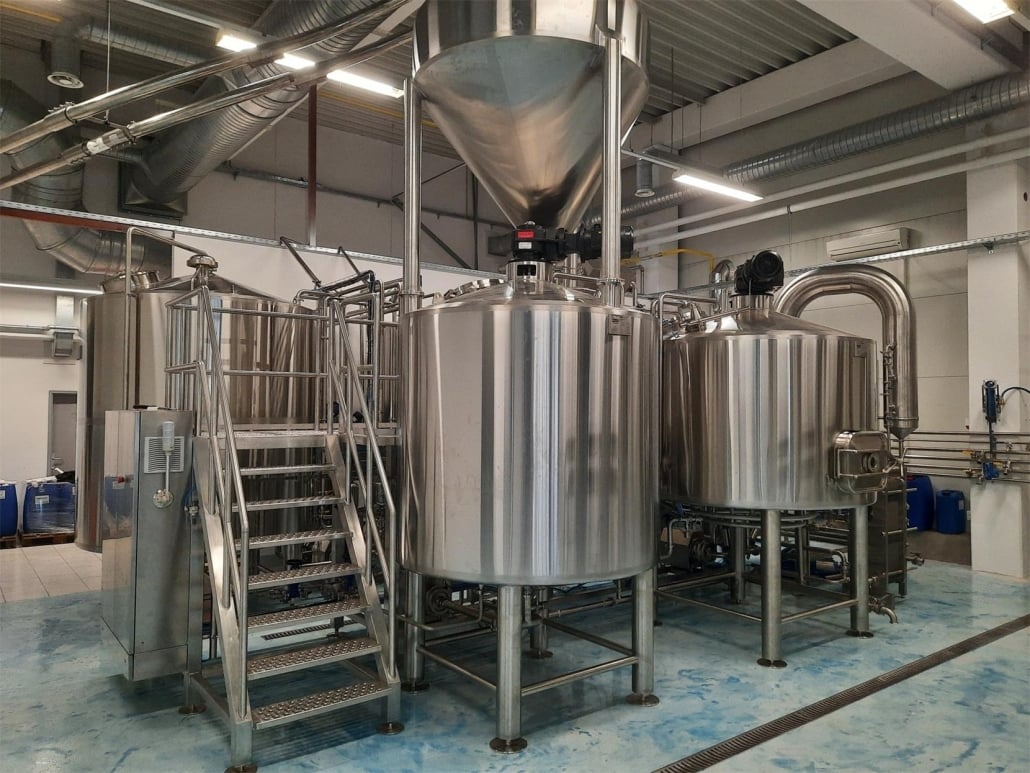
FAQs
Question | Answer |
---|---|
What is a vessel brewhouse? | A vessel brewhouse is a system of interconnected vessels used in the beer brewing process, including mashing, lautering, boiling, whirlpooling, and fermenting. |
How much does a vessel brewhouse cost? | Prices can range from $10,000 for a small-scale setup to over $1,000,000 for large-scale commercial systems. Customization adds to the cost. |
What are the benefits of using a vessel brewhouse? | It offers efficiency, scalability, precise quality control, and customization options for various brewing needs. |
How long does it take to install a vessel brewhouse? | Installation time varies based on the complexity of the system, but it typically takes several weeks to a few months. |
Can I customize my vessel brewhouse? | Yes, most suppliers offer customization options, including additional vessels, automation features, and aesthetic designs. |
What maintenance is required for a vessel brewhouse? | Regular cleaning, inspections, and preventive maintenance are essential to keep the system running smoothly. |
Conclusion
A vessel brewhouse is a cornerstone of any brewing operation, offering the tools and capabilities needed to produce high-quality beer efficiently. From understanding the equipment and brewing process to evaluating costs, suppliers, and maintenance needs, this guide provides a comprehensive overview to help you make informed decisions. Whether you’re a budding brewer or a seasoned professional, investing in the right vessel brewhouse will set the foundation for your brewing success.
So, are you ready to take the plunge and build your dream brewhouse? Happy brewing!
Share this entry
Interested in learning more about Brewing Systems including additional details and pricing information? Please use the form below to contact us!
YOLONG BREWERY EQUIPMENT FAQS
- Commercial Brewery / Craft Brewery / Microbrewery / Nanobrewery
- What is The Difference Between Craft Beer and Industrial Beer?
- The Bespoke Differences In Custom Brewing Systems
- Everything You Need to Know About Kettle Souring
- How to Choose Brewing Equipment for Your business?
- How To Choose The-Best Partner To Build Your Commercial Microbrewing System?
- Two Detection Sensors That You Need To Use In Your Brewhouse System
- Remote Control Applications in Brewing Equipment/How does it work?
- How To Clean Your Brand New Brewery Tanks?