Understanding Large Fermentation Tanks
Overview of Large Fermentation Tanks
Fermentation is one of the critical stages in many industries, particularly in the production of beverages like beer, wine, and spirits. A large fermentation tank is an essential piece of equipment in this process, designed to house large volumes of liquid that undergoes fermentation. Whether you are a microbrewery scaling up or a large-scale industrial producer, large fermentation tanks play a key role in improving efficiency and ensuring consistency in production.
So, what exactly is a large fermentation tank? In simple terms, it’s a specially designed container that allows controlled fermentation of various products. It’s where yeast or bacteria interact with sugars to produce alcohol and carbon dioxide in the case of alcoholic beverages. Depending on the industry, the design, size, and materials of these tanks may vary significantly.
Key Details About Large Fermentation Tanks
- Material Composition: Typically made from stainless steel, ensuring durability and resistance to corrosion.
- Capacity: Ranges from a few hundred liters to thousands, depending on the scale of production.
- Design: Includes features such as temperature control, insulation, pressure resistance, and ease of cleaning.
- Industries: Widely used in the food, beverage, pharmaceutical, and chemical industries.
- Customization: Tanks can be custom-built to meet specific production requirements, offering flexibility to manufacturers.
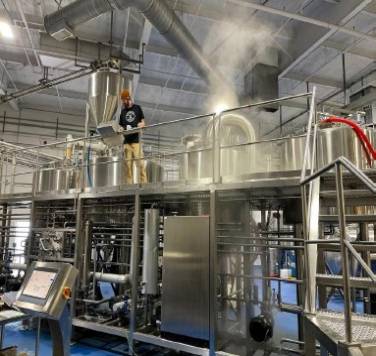
The Basics of Large Fermentation Tanks
Large fermentation tanks come in various forms, depending on the production scale and the product being made. The key considerations when choosing a tank include size, material, and features like cooling jackets, pressure controls, and cleaning systems. Stainless steel is the material of choice due to its non-reactive nature, ensuring that it doesn’t interact with the fermenting product.
When deciding on the right tank, you also need to consider whether it will be used for anaerobic or aerobic fermentation, as the design can vary significantly. Tanks designed for anaerobic fermentation (used in brewing beer or making wine) are sealed to maintain the absence of oxygen, while those for aerobic fermentation (used in some chemical or pharmaceutical processes) often include features for aeration.
Types of Large Fermentation Tanks
Tank Type | Description | Common Use | Pros | Cons |
---|---|---|---|---|
Cylindrical-Conical Tanks (CCTs) | These tanks are the standard in brewing, with a cone at the bottom for yeast collection. They allow easy removal of yeast and are perfect for large-scale beer production. | Beer and alcohol production. | Easy yeast collection, clean design. | More expensive due to complexity. |
Open Fermentation Tanks | These tanks have no lid and allow open exposure to the air. The fermentation is naturally aerated and creates a distinct flavor. | Small batch beer or wine production. | Promotes unique fermentation characteristics. | Greater risk of contamination, requires careful management. |
Horizontal Fermentation Tanks | Shaped horizontally, these tanks are used for storage and secondary fermentation processes. | Post-fermentation storage for wine or beer. | Saves vertical space, great for aging. | Requires more ground space, harder to stack. |
Aseptic Fermentation Tanks | These tanks are designed for sterile conditions and are equipped with rigorous sealing and cleaning systems. | Pharmaceutical and biotechnology industries. | Sterile, highly controlled environment. | Higher operational costs, requires more maintenance. |
Choosing the Right Type of Fermentation Tank
When selecting a tank, consider the type of fermentation you require, the scale of your operation, and the level of control you need over the process. Cylindrical-conical tanks, for example, are ideal for large-scale breweries due to their easy yeast collection and cleaning features, while open fermentation tanks are more suited for artisanal brewers seeking distinct flavors.
Understanding the Brewing Process with Large Fermentation Tanks
1. The Role of Large Fermentation Tanks in Brewing
Fermentation tanks are a crucial part of the brewing process, as this is where the magic happens. In beer production, the fermentation tank is where the yeast consumes the sugars in the wort and turns them into alcohol and carbon dioxide, alongside various flavor compounds. The efficiency of this process is heavily dependent on the control you have over the tank’s temperature, pressure, and oxygen levels.
The size of the fermentation tank directly impacts the time it takes for the yeast to fully ferment the batch. In large-scale brewing, tanks can hold thousands of liters of wort, reducing the number of fermentation cycles required to meet production targets.
2. Temperature Control in Large Fermentation Tanks
Temperature control is one of the most important factors during fermentation. Different yeast strains work best at different temperatures. Large fermentation tanks are usually fitted with cooling jackets that surround the tank and allow precise temperature regulation.
3. Aeration and Oxygen Levels
While beer production generally requires anaerobic conditions, certain types of fermentation, such as vinegar production, require oxygen. Specialized fermentation tanks come with aeration systems that allow manufacturers to control the oxygen levels within the tank, ensuring optimal growth of the aerobic bacteria.
Customization and Capacity of Large Fermentation Tanks
Factor | Details |
---|---|
Tank Capacity | Ranges from 500 liters to 50,000 liters or more, depending on the production scale. |
Space Requirements | Larger tanks require significant floor space and must be installed with consideration for future expansion. |
Design and Layout | Tanks are typically cylindrical, but they can be customized based on the space available and the production process. |
Customization Options | Includes adding cooling jackets, insulation, pressure relief systems, and automated cleaning systems. |
Material | Stainless steel is the most common, though some tanks may be made of glass or specialized polymers. |
Why Customization is Important
The ability to customize large fermentation tanks means you can optimize your production process based on your specific needs. For example, if you need rapid cooling, you can have a tank fitted with extra-thick cooling jackets. If you’re producing beer in smaller batches, you might opt for multiple smaller tanks instead of one large one to provide flexibility in production.
Suppliers and Price Range of Large Fermentation Tanks
Supplier | Price Range | Country of Origin | Customization |
---|---|---|---|
Mueller Processing | $20,000 – $150,000 | USA | Full customization options |
Ziemann Holvrieka | $50,000 – $200,000 | Germany | High-end custom solutions |
JVNW | $30,000 – $120,000 | USA | Custom stainless steel tanks |
Paul Mueller Company | $25,000 – $180,000 | USA | Modular designs available |
Gpi Tanks | $35,000 – $160,000 | Netherlands | Focus on food-grade tanks |
Comparing Suppliers
When choosing a supplier, the price range of the tanks will depend on several factors, including the size, level of customization, and the materials used. Some companies focus on highly specialized tanks that meet strict industry standards for food and pharmaceutical production, while others offer more cost-effective solutions for the beverage industry.
Installation, Operation, and Maintenance of Large Fermentation Tanks
Aspect | Details |
---|---|
Installation | Requires professional installation due to the size and complexity of the tank systems. It includes plumbing, electrical, and possibly gas lines. |
Operation | Large tanks are typically fitted with automatic temperature controls, pressure gauges, and cleaning systems. |
Maintenance | Tanks require regular cleaning (automated CIP systems are common), inspection for wear and tear, and occasional repair of valves or pressure seals. |
Why Proper Maintenance is Crucial
Regular maintenance ensures that the tanks remain in good working condition and prevent contamination of the product. Many large tanks come equipped with CIP (Clean-in-Place) systems that make cleaning much easier and more efficient.
How to Choose a Supplier for Large Fermentation Tanks
Consideration | Details |
---|---|
Industry Expertise | Choose a supplier with experience in your specific industry (brewing, pharmaceuticals, etc.). |
Customization Options | Look for suppliers that offer tailored solutions to meet your production needs. |
Customer Support and Service | Ensure the supplier offers strong post-sale support, including installation and maintenance services. |
Reputation and Reviews | Check for positive reviews, industry awards, and long-standing experience in the market. |
Delivery and Installation | Make sure the supplier can deliver and install the tanks in your facility within your timeline. |
Price and Payment Options | Compare the prices and see if they offer flexible payment options to suit your budget. |
Supplier Comparison: What Really Matters
When evaluating suppliers, don’t just look at the upfront cost. Consider how well they understand your specific needs, their ability to deliver on time, and the quality of their post-sale services. Some suppliers offer excellent pricing but might fall short on customization or ongoing support, which can impact your operations in the long term.
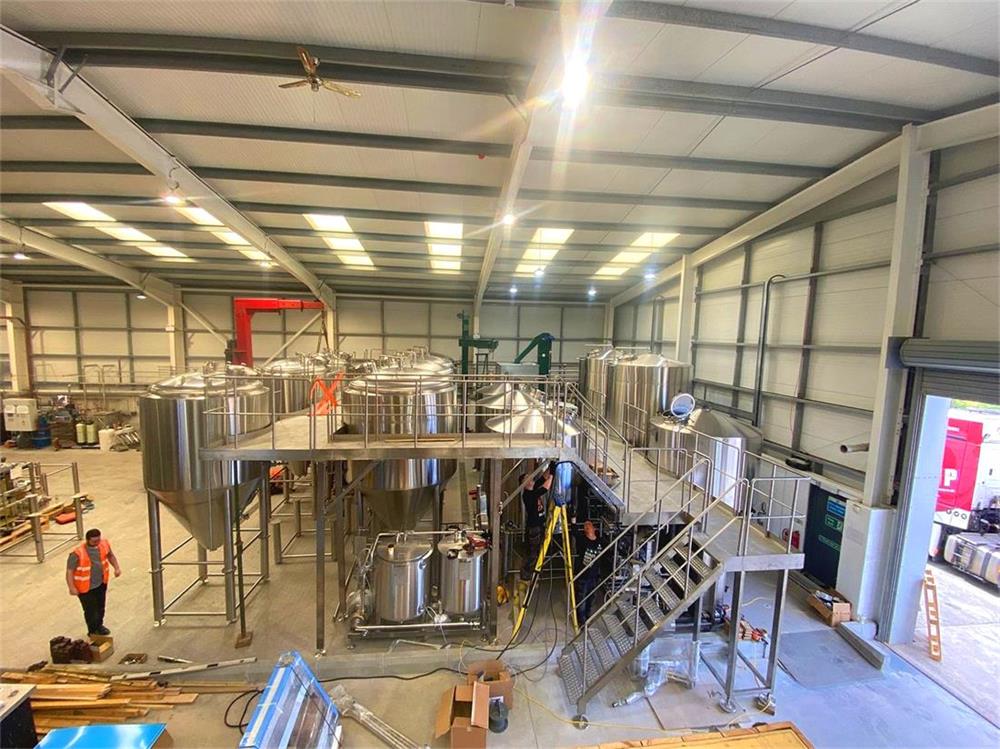
Pros and Cons of Large Fermentation Tanks
Advantages | Disadvantages |
---|---|
Increased Production Capacity | Allows for large-scale fermentation, reducing the number of batches needed to meet production goals. |
Consistent Quality | Automated systems help maintain consistent fermentation conditions, leading to uniform product quality. |
Durability | Stainless steel tanks are long-lasting and resistant to corrosion. |
Cost-Effective in the Long Term | While expensive upfront, large tanks reduce the need for frequent replacements or repairs. |
Space Requirements | Large tanks require significant space, which might not be available in all facilities. |
High Initial Investment | The upfront cost can be prohibitive for small businesses. |
Maintenance Costs | Requires regular maintenance, especially for tanks with complex systems. |
FAQ
Question | Answer |
---|---|
What materials are used in fermentation tanks? | Most large fermentation tanks are made from stainless steel, which is non-reactive and durable. |
What size fermentation tank do I need? | This depends on your production capacity. Small craft breweries might need 500-liter tanks, while large breweries could require tanks that hold 10,000 liters or more. |
How much does a large fermentation tank cost? | Prices vary widely depending on the size and customization. Basic models might start at $20,000, but specialized tanks can cost over $150,000. |
Can fermentation tanks be customized? | Yes, you can customize tanks with features like cooling jackets, insulation, pressure control, and CIP systems. |
How do you maintain large fermentation tanks? | Regular cleaning is essential, and most tanks come with CIP systems. Valves, seals, and cooling systems also need periodic checks. |
This structured content, including detailed paragraphs and tables, covers every aspect of large fermentation tanks, providing both the technical information and comparative insights that a reader would need.
Share this entry
Interested in learning more about Brewing Systems including additional details and pricing information? Please use the form below to contact us!
YOLONG BREWERY EQUIPMENT FAQS
- Commercial Brewery / Craft Brewery / Microbrewery / Nanobrewery
- What is The Difference Between Craft Beer and Industrial Beer?
- The Bespoke Differences In Custom Brewing Systems
- Everything You Need to Know About Kettle Souring
- How to Choose Brewing Equipment for Your business?
- How To Choose The-Best Partner To Build Your Commercial Microbrewing System?
- Two Detection Sensors That You Need To Use In Your Brewhouse System
- Remote Control Applications in Brewing Equipment/How does it work?
- How To Clean Your Brand New Brewery Tanks?