Industrial Brewing Equipment
Overview of Industrial Brewing Equipment
Industrial brewing is a sophisticated process that involves transforming raw ingredients into large batches of beer, utilizing specialized brewing systems. The demand for high-quality beer and increasing competition in the market has made it essential for breweries to invest in the best industrial brewing equipment. Whether you’re a craft brewery looking to scale up or a larger commercial facility, selecting the right brewing equipment can make or break your success.
This guide will walk you through everything you need to know about industrial brewing equipment, from an overview of the key machines, their features, and how they work, to a detailed exploration of the brewing process, customization options, and cost comparisons.
We’ll dive into the nitty-gritty of brewing systems and examine how different machines and layouts impact the brewing process. By the end, you’ll be equipped with the knowledge to choose the best brewing equipment for your specific needs.
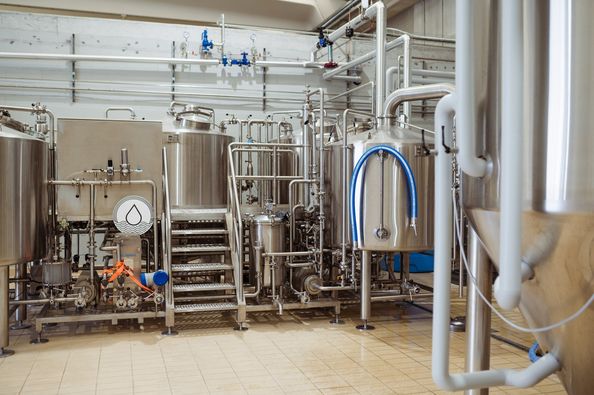
A Guide to Industrial Brewing Equipment
Selecting the right brewing equipment is the backbone of efficient and successful beer production. Depending on the scale of the operation, industrial brewing systems come with a wide range of features and complexities. Each component plays a unique role in transforming raw ingredients into your favorite beer.
Key Components of Industrial Brewing Equipment
- Mash Tun: This vessel is where the mashing process occurs. It mixes hot water with milled grains to extract fermentable sugars. The quality of the mash tun influences the consistency of the final product.
- Lauter Tun: After mashing, the grain bed separates from the wort in this vessel. Lauter tuns are essential for filtering out solids and ensuring the wort is clear.
- Boil Kettle: The wort is boiled in this kettle to sterilize it, extract flavors from hops, and stop enzyme activity. Precision in temperature control is crucial.
- Fermentation Tanks: Fermenters are where the yeast works its magic, converting sugars into alcohol. The design and capacity of these tanks can directly affect the fermentation speed and flavor.
- Bright Tanks: After fermentation, bright tanks are used to clarify and carbonate the beer, making it “bright” or clear before packaging.
- Heat Exchanger: This equipment rapidly cools the wort after boiling, helping achieve the ideal fermentation temperature.
- Control Systems: These include PLCs (Programmable Logic Controllers) and other computerized systems that automate various aspects of the brewing process, allowing for precise control over temperature, timing, and more.
Industrial Brewing Equipment Types and Functions
To help you better understand the different kinds of brewing equipment available on the market, we’ve created a table summarizing the various equipment types and their primary functions.
Equipment | Primary Function | Typical Features |
---|---|---|
Mash Tun | Converts starches in grains into fermentable sugars via the mashing process | Features like stirring paddles, insulation for temperature control, and varying capacities to suit the brewery’s needs |
Lauter Tun | Separates wort from spent grains using a filter or false bottom | Often equipped with rakes for even filtration and advanced drainage systems for efficient liquid flow |
Boil Kettle | Boils wort to extract hop flavors, stop enzyme action, and sterilize the liquid | Steam- or gas-heated, often includes whirlpool capability to collect hop debris |
Fermentation Tanks | Allows yeast to ferment sugars into alcohol under controlled conditions | Available in various sizes, typically with temperature control jackets, and designed for easy cleaning and sanitation |
Bright Tanks | Conditions the beer after fermentation, allowing for carbonation and clarification | Pressurized tanks designed to handle carbonation and retain clarity |
Heat Exchanger | Cools boiled wort quickly to the appropriate fermentation temperature | Often made of stainless steel and equipped with cold water and wort pathways for efficient heat transfer |
Control Systems | Automates brewing operations such as temperature regulation, stirring, and pressure control | Includes digital displays, PLCs, sensors, and control panels for ease of monitoring and accuracy in brewing operations |
The Brewing Process: How Industrial Brewing Equipment Works
The industrial brewing process can be broken down into several critical stages, each reliant on specialized equipment to ensure the perfect brew. Here’s a detailed breakdown of how each stage works:
1. Mashing
Mashing is the first stage in the brewing process where milled grains are combined with water in the mash tun. This mixture is heated to activate enzymes, breaking down the starches in the grains into fermentable sugars. The temperature control and duration of the mash are vital for determining the beer’s final flavor and alcohol content. Industrial mash tuns often feature stirring paddles or rakes to ensure uniform mixing.
2. Lautering
Once the mash is complete, it’s time to separate the wort from the spent grains in the lauter tun. This process involves draining the liquid through a perforated bottom, leaving the grains behind. Lauter tuns equipped with rakes help achieve even filtration, ensuring that no residual solids make their way into the wort.
3. Boiling
Next comes the boil, where the wort is transferred into a kettle and brought to a high temperature to sterilize it and extract the bitterness and flavor from the hops. Many boil kettles in industrial settings also feature whirlpool capabilities, which help collect unwanted particles and clarify the liquid.
4. Fermentation
Once the wort has been boiled and hops have been added, it’s cooled down using a heat exchanger before being transferred into fermentation tanks. Here, yeast is added, and the magic happens—sugars are converted into alcohol and carbon dioxide. Fermentation can take anywhere from a few days to several weeks, depending on the beer type and the specific fermentation strategy.
5. Conditioning
After fermentation, the beer needs time to mature, a process that takes place in bright tanks. During conditioning, the beer is carbonated and clarified. Some beers may also undergo additional filtration or fining processes during this stage to enhance clarity and taste.
6. Packaging
Once the beer has reached its final form, it’s ready to be packaged in bottles, cans, or kegs. Packaging equipment is highly automated in most industrial breweries, ensuring efficiency and consistent quality across large batches.
Industrial Brewing Equipment Capacity, Layout, and Customization
When setting up or upgrading your brewing facility, understanding the relationship between equipment capacity, layout, and design is crucial. Below is a detailed table explaining the various considerations when choosing brewing equipment and configuring your brewery’s layout.
Aspect | Details |
---|---|
Capacity | Brewing equipment can range from small 5-barrel systems for craft breweries to massive 100-barrel systems for larger commercial operations. |
Space Requirements | The layout of brewing equipment needs to account for not just the equipment footprint but also space for cleaning, maintenance, and future expansions. |
Design Considerations | Compact or vertical designs can save space, while modular systems offer flexibility for growth. Flow efficiency is vital to avoid production bottlenecks. |
Customization | Breweries often customize their systems to optimize their unique brewing processes, adding features like dual fermentation tanks or multi-stage filtration. |
Cost of Industrial Brewing Equipment and Supplier Overview
The cost of industrial brewing equipment can vary dramatically based on factors like system capacity, degree of automation, and the materials used. To help you navigate this, we’ve compiled a list of common suppliers and the typical price ranges you can expect for different types of equipment.
Supplier | Price Range | Specialties |
---|---|---|
Ss Brewtech | $50,000 – $500,000 | Specializes in stainless steel systems for small to mid-sized breweries |
Alpha Brewing Operations | $75,000 – $750,000 | Provides custom-built brewing systems with a focus on automation |
JV Northwest | $100,000 – $1,000,000 | Offers fully automated systems for large-scale commercial breweries |
BrauKon | $200,000 – $1,500,000 | Known for high-quality German-made brewing systems with advanced technology and durability |
Blichmann Engineering | $30,000 – $200,000 | Affordable brewing systems for smaller craft breweries |
Installation, Operation, and Maintenance of Brewing Equipment
Setting up and operating industrial brewing equipment involves various stages, including installation, day-to-day operation, and regular maintenance. Each phase plays an important role in ensuring that the brewing equipment runs efficiently and lasts for many years.
Stage | Details |
---|---|
Installation | Equipment setup is typically handled by professionals, especially for larger systems. Proper plumbing, electrical, and steam connections are essential. |
Operation | Training is required to operate the equipment efficiently. Brewing systems often come with automation and control panels to streamline production. |
Maintenance | Routine maintenance involves cleaning the tanks, replacing seals, and performing regular inspections to ensure everything runs smoothly. |
How to Choose the Right Industrial Brewing Equipment Supplier
Choosing the right supplier is one of the most important decisions when setting up your brewery. A good supplier will offer not only high-quality equipment but also excellent customer support and customization options to meet your specific brewing needs.
Consideration | Details |
---|---|
Quality of Equipment | Check if the supplier offers durable, stainless steel equipment that meets your brewery’s scale and quality demands. |
Support Services | Good suppliers provide installation services, training, and ongoing support for operation and maintenance. |
Customization Options | Ensure the supplier is willing to customize equipment according to your unique brewing process requirements. |
Pricing and Value | Compare quotes from different suppliers, but also weigh the long-term value of the investment based on quality and service. |
Advantages and Disadvantages of Industrial Brewing Equipment
No brewing system is perfect. Each type of equipment comes with its own set of advantages and limitations. Here’s a comparative look at the pros and cons of different industrial brewing systems.
System Type | Advantages | Disadvantages |
---|---|---|
Manual Systems | Affordable, offers more control over the process | Labor-intensive, higher chances of human error, slower production |
Semi-Automated Systems | Easier to operate, faster production than manual systems | More expensive, requires periodic supervision |
Fully Automated Systems | Highly efficient, minimal human intervention, consistent quality across large batches | Expensive upfront costs, complex to repair and maintain |
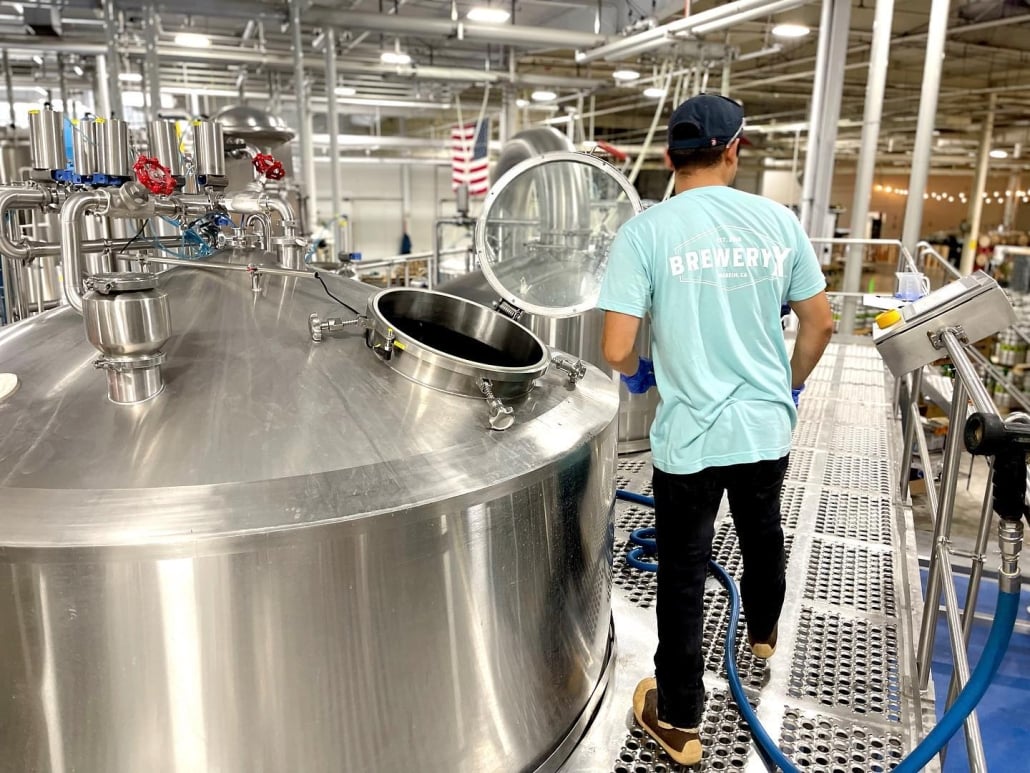
FAQ
Question | Answer |
---|---|
What size brewing system do I need for my brewery? | It depends on your production goals. A smaller craft brewery might need a 5-10 barrel system, while larger facilities require 30-100 barrels or more. |
How much does industrial brewing equipment cost? | Prices vary based on system size and complexity. A small craft brewery setup might cost $50,000, while large commercial systems can exceed $1 million. |
How long does it take to install brewing equipment? | Installation time varies but can take anywhere from a few weeks to several months, depending on system complexity and site preparation. |
What maintenance is required for brewing equipment? | Regular cleaning, inspection of seals and gaskets, and ensuring that control systems are calibrated correctly are all part of routine maintenance. |
Can I customize my brewing system? | Yes, many suppliers offer customization options such as additional tanks, automation, or specialized filtration systems. |
This guide should help you navigate the complexities of industrial brewing equipment, from selecting the right machinery to ensuring proper installation and maintenance. Whether you’re just starting out or looking to scale up, the right brewing system can elevate your production quality and efficiency.
Share this entry
Interested in learning more about Brewing Systems including additional details and pricing information? Please use the form below to contact us!
YOLONG BREWERY EQUIPMENT FAQS
- Commercial Brewery / Craft Brewery / Microbrewery / Nanobrewery
- What is The Difference Between Craft Beer and Industrial Beer?
- The Bespoke Differences In Custom Brewing Systems
- Everything You Need to Know About Kettle Souring
- How to Choose Brewing Equipment for Your business?
- How To Choose The-Best Partner To Build Your Commercial Microbrewing System?
- Two Detection Sensors That You Need To Use In Your Brewhouse System
- Remote Control Applications in Brewing Equipment/How does it work?
- How To Clean Your Brand New Brewery Tanks?