Industrial Brewing Equipment
Brewing beer isn’t just an art; it’s a science that demands precision, consistency, and the right tools. Whether you’re setting up a small craft brewery or expanding an industrial-scale operation, understanding the intricacies of industrial brewing equipment is crucial. This guide delves into the various types of equipment, the brewing process, and how to choose the right suppliers to ensure your brewing venture is a success.
Overview of Industrial Brewing Equipment
Industrial brewing equipment encompasses a wide range of machinery and tools essential for large-scale beer production. From the initial stages of milling the grains to the final packaging, each piece of equipment plays a vital role in maintaining the quality and efficiency of the brewing process.
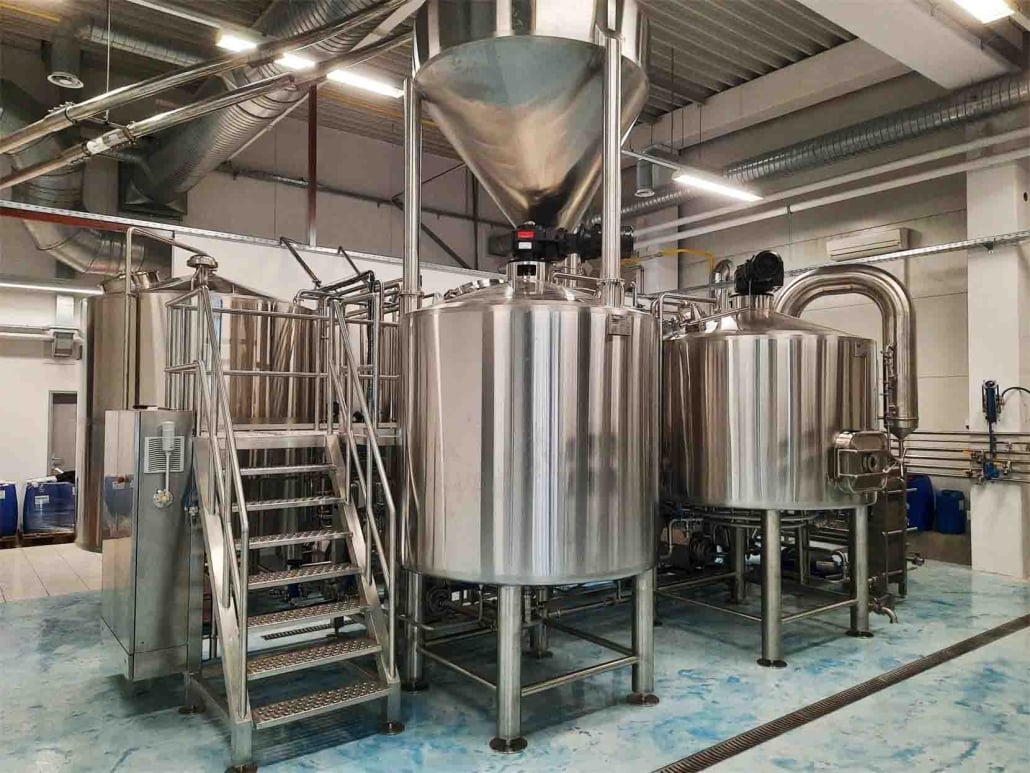
Types of Industrial Brewing Equipment
- Milling Equipment: This is where the brewing process begins. The milling equipment grinds malted barley into grist, which is then used in the mash tun. Precision in this step ensures optimal extraction of fermentable sugars.
- Mash Tuns: This vessel mixes the grist with hot water to create a mash. The temperature and duration in the mash tun affect the beer’s flavor and body.
- Lauter Tuns: Here, the mash is separated into clear liquid wort and spent grains. Proper lauter tun operation ensures efficient extraction and clarity of the wort.
- Brew Kettles: The wort is boiled in the brew kettle, where hops are added. This step is crucial for sterilization and developing the beer’s bitterness, flavor, and aroma.
- Fermentation Tanks: After boiling, the wort is cooled and transferred to fermentation tanks where yeast is added. This is where the magic happens, converting sugars into alcohol and CO2.
- Conditioning Tanks: Post-fermentation, the beer is moved to conditioning tanks where it matures and develops its final flavor profile.
- Filtration Systems: These systems remove unwanted particulates to ensure a clear final product.
- Packaging Equipment: From bottling lines to canning and kegging systems, packaging equipment ensures the beer is stored properly for distribution.
Types of Industrial Brewing Equipment
Equipment Type | Description |
---|---|
Milling Equipment | Grinds malted barley into grist. Precision is key for optimal sugar extraction. |
Mash Tuns | Mixes grist with hot water to create mash. Temperature and duration affect flavor and body. |
Lauter Tuns | Separates mash into clear wort and spent grains. Ensures efficient extraction and clarity. |
Brew Kettles | Boils wort, adds hops for bitterness, flavor, and aroma. Sterilizes wort. |
Fermentation Tanks | Where wort is cooled and yeast added. Sugars convert to alcohol and CO2. |
Conditioning Tanks | Beer matures, developing its final flavor profile. |
Filtration Systems | Removes unwanted particulates to ensure clarity. |
Packaging Equipment | Bottling, canning, and kegging systems for proper beer storage and distribution. |
The Brewing Process
The brewing process is a blend of science and art, involving several critical stages:
- Milling: The process starts with milling malted barley into grist. The consistency of the grind is vital for the next steps.
- Mashing: The grist is mixed with hot water in the mash tun, where enzymes break down the starches into fermentable sugars.
- Lautering: The mash is transferred to the lauter tun, where it is separated into liquid wort and spent grains.
- Boiling: The wort is boiled in the brew kettle. Hops are added at different stages for bitterness, flavor, and aroma.
- Cooling: The hot wort is rapidly cooled to a temperature suitable for fermentation.
- Fermentation: Yeast is added to the cooled wort in fermentation tanks, converting sugars into alcohol and CO2.
- Conditioning: The beer is conditioned in tanks where it matures and carbonates naturally.
- Filtration and Packaging: Finally, the beer is filtered and packaged into bottles, cans, or kegs for distribution.
Capacity, Space, Design, and Customization
Brewing Equipment Capacity and Space Requirements
Equipment Type | Capacity Range (Liters) | Space Requirements (Square Meters) | Customization Options |
---|---|---|---|
Milling Equipment | 500 – 10,000 | 5 – 20 | Adjustable grind settings |
Mash Tuns | 1,000 – 20,000 | 10 – 50 | Insulation, agitators |
Lauter Tuns | 1,000 – 20,000 | 10 – 50 | Automated rakes, false bottom |
Brew Kettles | 1,000 – 20,000 | 10 – 50 | Steam jackets, whirlpool inlets |
Fermentation Tanks | 1,000 – 50,000 | 15 – 60 | Cooling jackets, pressure-rated |
Conditioning Tanks | 1,000 – 50,000 | 15 – 60 | Variable pressure, carbonation |
Filtration Systems | 500 – 10,000 | 5 – 20 | Multiple filtration stages |
Packaging Equipment | 500 – 10,000 | 5 – 30 | Automated, semi-automated lines |
Design and Layout Considerations
Designing an efficient brewery layout is essential to streamline operations and maximize space. Considerations include:
- Workflow Efficiency: Arrange equipment to minimize movement and maximize productivity.
- Space Optimization: Ensure there’s ample room for movement and future expansion.
- Utility Access: Equipment should have easy access to water, power, and drainage systems.
- Safety: Incorporate safety features and emergency exits.
- Customizability: Tailor the layout to specific brewing needs and processes.
Suppliers and Price Range
Choosing the right supplier is crucial for obtaining reliable and cost-effective brewing equipment.
Suppliers and Equipment Pricing
Supplier Name | Equipment Types Offered | Price Range (USD) | Key Features and Services |
---|---|---|---|
BrewTech Industries | Full brewery setups | $50,000 – $1,000,000 | Custom design, installation, after-sales support |
ProBrew Systems | Fermentation and conditioning | $10,000 – $500,000 | Advanced control systems, high-quality materials |
Keg King | Packaging lines and kegging | $5,000 – $250,000 | Durable, efficient, semi-automated options |
Malt Mill Co. | Milling equipment | $2,000 – $50,000 | Precision milling, adjustable settings |
HopHaven Equipment | Brew kettles and lauter tuns | $20,000 – $300,000 | Efficient boiling, robust construction |
Installation, Operation, and Maintenance
Ensuring seamless installation, efficient operation, and regular maintenance is critical to the longevity and performance of brewing equipment.
Installation and Operation
Aspect | Details |
---|---|
Installation | Professional installation ensures all components are correctly integrated. Suppliers often offer on-site setup. |
Operation | User-friendly control systems and automation enhance operational efficiency. Training for staff is recommended. |
Maintenance and Upkeep
Maintenance Type | Frequency | Tasks Involved |
---|---|---|
Daily Maintenance | Daily | Cleaning surfaces, checking control systems, inspecting hoses |
Weekly Maintenance | Weekly | Deep cleaning tanks, verifying pressure levels, calibrating sensors |
Monthly Maintenance | Monthly | Inspecting for wear and tear, lubricating moving parts, updating software |
Annual Maintenance | Annually | Full system inspection, professional servicing, replacing worn parts |
How to Choose the Right Supplier
Choosing the right supplier for brewing equipment can make or break your brewery’s success. Here are some tips to help you make the right decision:
Factors to Consider
Factor | Details |
---|---|
Reputation | Research the supplier’s history and customer reviews. A good reputation often indicates reliable products and services. |
Product Range | Ensure the supplier offers all the equipment you need. It’s beneficial to have a single source for most of your equipment. |
Customization Options | Look for suppliers that offer tailored solutions to fit your specific needs. |
Support and Training | Choose suppliers that provide robust after-sales support and training programs. |
Price and Warranty | Compare prices and check warranty terms. Consider long-term value over upfront cost. |
Pros and Cons of Industrial Brewing Equipment
Understanding the advantages and limitations of industrial brewing equipment helps in making informed decisions.
Advantages
Equipment Type | Advantages |
---|---|
Milling Equipment | Ensures precise grind, enhancing extraction efficiency |
Mash Tuns | Consistent temperature control, better flavor development |
Lauter Tuns | Efficient wort separation, clarity improvement |
Brew Kettles | Reliable sterilization, enhanced hop utilization |
Fermentation Tanks | Controlled fermentation, consistent quality |
Conditioning Tanks | Optimal maturation, improved flavor profile |
Filtration Systems | Clear, polished final product |
Packaging Equipment | Efficient, consistent packaging, reduced waste |
Disadvantages
Equipment Type | Limitations |
---|---|
Milling Equipment | High initial cost, requires regular maintenance |
Mash Tuns | Requires precise temperature control, potential for inconsistent mash |
Lauter Tuns | Can be complex to operate, requires skillful management |
Brew Kettles | Energy-intensive, high upfront cost |
Fermentation Tanks | Requires strict monitoring, potential contamination risk |
Conditioning Tanks | Takes up significant space, requires careful pressure management |
Filtration Systems | Can strip out desirable compounds, requires careful balance |
Packaging Equipment | High upfront cost, requires space and skilled operation |
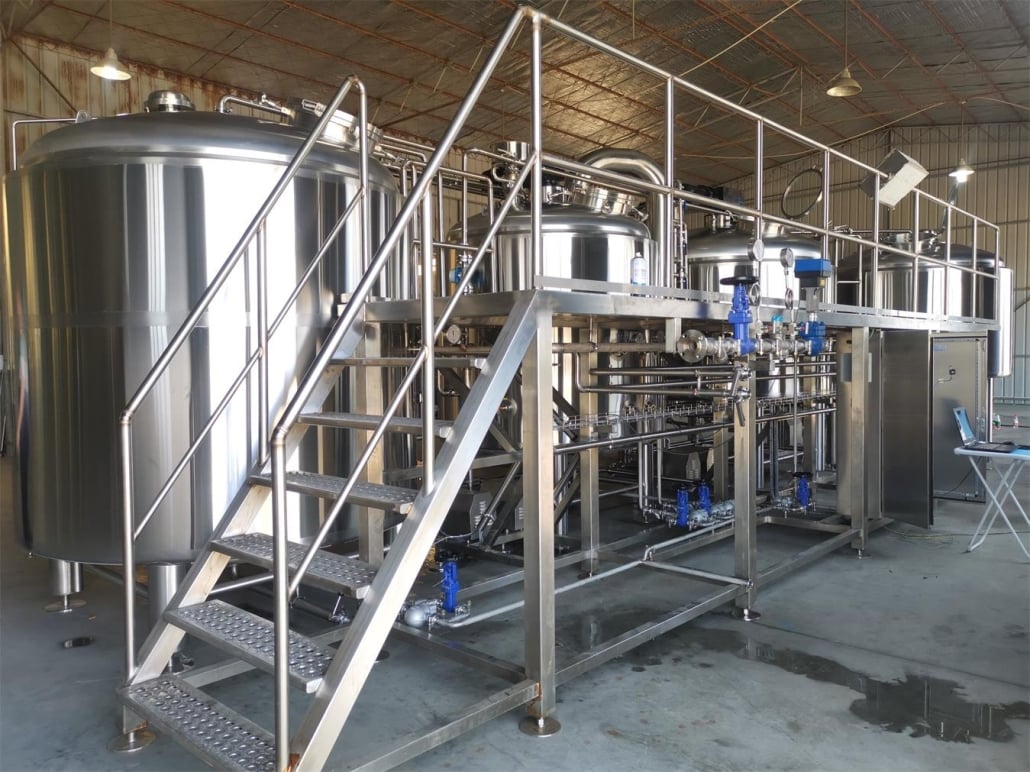
FAQ
Question | Answer |
---|---|
What is the most important piece of brewing equipment? | Each piece is crucial, but fermentation tanks are often considered the heart of the brewing process. |
How often should brewing equipment be maintained? | Daily cleaning and inspection, weekly deep cleaning, monthly calibration, and annual professional servicing are recommended. |
Can small breweries use industrial equipment? | Yes, many suppliers offer scalable solutions suitable for small to medium-sized breweries. |
How do I choose the right brewing equipment? | Consider factors such as capacity, space, customization options, supplier reputation, and cost. |
What are the main benefits of automated brewing systems? | Increased efficiency, consistent quality, reduced labor costs, and precise control over the brewing process. |
Share this entry
Interested in learning more about Brewing Systems including additional details and pricing information? Please use the form below to contact us!
YOLONG BREWERY EQUIPMENT FAQS
- Commercial Brewery / Craft Brewery / Microbrewery / Nanobrewery
- What is The Difference Between Craft Beer and Industrial Beer?
- The Bespoke Differences In Custom Brewing Systems
- Everything You Need to Know About Kettle Souring
- How to Choose Brewing Equipment for Your business?
- How To Choose The-Best Partner To Build Your Commercial Microbrewing System?
- Two Detection Sensors That You Need To Use In Your Brewhouse System
- Remote Control Applications in Brewing Equipment/How does it work?
- How To Clean Your Brand New Brewery Tanks?