Industrial Beer Equipment
Brewing beer on an industrial scale is an intricate process that demands specialized equipment, expertise, and careful planning. Whether you’re a seasoned brewmaster looking to expand your operations or an entrepreneur venturing into the world of craft beer, understanding the ins and outs of industrial beer equipment is critical. This guide will walk you through everything you need to know—from the different types of brewing equipment, their functions, and price ranges, to how to choose the right supplier, install your system, and maintain it for long-term efficiency.
Overview of Industrial Beer Equipment
Industrial beer equipment is used in breweries to produce large volumes of beer for commercial distribution. While home brewing might involve a few basic tools, industrial brewing systems are far more complex, involving multiple stages such as mashing, fermenting, filtering, bottling, and more. These systems include everything from mash tuns and fermentation tanks to packaging machines. The equipment varies in size, capacity, and customization options depending on the specific needs of the brewery, the type of beer being brewed, and the scale of production.
Breweries have to carefully select equipment that meets their production goals, quality standards, and budget. Each component of the brewing system is crucial to ensuring the process runs smoothly and the final product meets consumer expectations.
Key Components of Industrial Beer Equipment
Here’s a quick look at the essential components in an industrial beer brewing setup:
- Mash Tuns – Where grains and water are mixed to convert starches into sugars.
- Boil Kettles – Where the wort is boiled and hops are added.
- Fermentation Tanks – Vessels where yeast ferments sugars into alcohol.
- Bright Beer Tanks – Used to carbonate the beer.
- Cooling Systems – Essential for controlling fermentation temperatures.
- Filtration Systems – Removes unwanted particulates and impurities.
- Packaging Lines – Bottles, cans, or kegs the finished beer.
- Automation Controls – Allows brewers to monitor and control every step of the process.
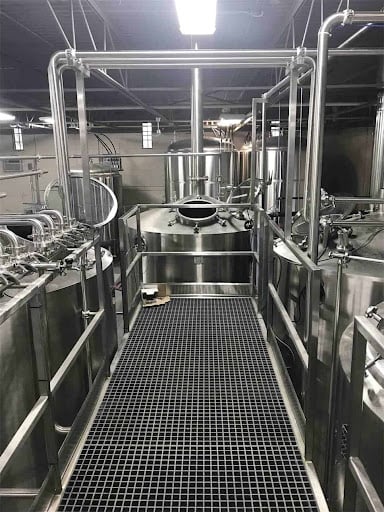
Types of Industrial Beer Equipment
Each piece of industrial beer equipment plays a distinct role in the brewing process. While some breweries operate with more manual systems, modern facilities use advanced automation to streamline processes.
Equipment Type | Function | Key Features | Importance |
---|---|---|---|
Mash Tun | Mixes crushed malt and water to convert starches to fermentable sugars | Insulated for heat retention, agitators for uniform mixing | First step in beer production |
Lauter Tun | Separates the spent grain from the liquid wort | False bottom for filtering, rakes to assist with drainage | Essential for wort clarity |
Boil Kettle | Boils wort and sterilizes the liquid | Temperature control, pressure safety systems | Hops added at this stage |
Fermentation Tanks | Converts sugars into alcohol via yeast fermentation | Sealed with pressure valves, temperature-controlled jackets | Where alcohol is created |
Bright Beer Tank | Final conditioning tank where beer is carbonated and clarified | Can be used for carbonation and storage | Readies beer for packaging |
Cooling Systems | Maintains fermentation temperatures and prevents bacterial growth | Glycol chillers, heat exchangers | Temperature control is critical |
Filtration System | Filters beer to remove yeast, hops, and other particulates before packaging | Centrifuges, plate filters, membrane filters | Improves clarity and taste |
Packaging Line | Automates bottling, canning, or kegging | Fast and accurate packaging with labeling options | Final stage before distribution |
Automation Controls | Integrates control of temperature, timing, and equipment functions | PLCs, HMIs, and sensor networks | Increases efficiency and consistency |
Choosing the right equipment mix depends on the scale of the brewery and the desired level of automation. For example, smaller craft breweries may use simpler systems, while large commercial operations require more advanced and integrated equipment to handle higher volumes.
The Industrial Brewing Process
The beer brewing process is a multi-step procedure, and each step requires specific equipment. Here’s an in-depth look at each stage of industrial beer production:
Mashing
The first stage in brewing beer is mashing. In this step, malted barley is mixed with hot water in the mash tun, where enzymes convert the starches into fermentable sugars. The mixture, known as mash, needs to be carefully monitored for temperature consistency to ensure efficient sugar conversion.
Lautering
After mashing, the wort (liquid extracted from the mash) is separated from the spent grain through a process called lautering. The lauter tun is equipped with a false bottom that filters out the grain husks while allowing the liquid to pass through. The goal here is to maximize wort extraction and clarity, which directly impacts the quality of the final product.
Boiling
Next, the wort is transferred to the boil kettle where it’s brought to a rolling boil. This step serves multiple purposes, including sterilization, hop addition for bitterness and aroma, and protein coagulation, which is important for beer clarity. Boiling also concentrates the flavors, setting the foundation for the beer’s taste profile.
Fermentation
Fermentation is perhaps the most critical step in beer production. Once the boiled wort is cooled, it is transferred to a fermentation tank and yeast is added. The yeast ferments the sugars, producing alcohol and carbon dioxide. Temperature control during fermentation is crucial for maintaining the integrity of the beer’s flavor. Industrial breweries use sophisticated cooling systems to regulate fermentation conditions.
Conditioning and Packaging
After fermentation, the beer is conditioned in bright beer tanks, where carbonation occurs, and the beer is clarified for improved taste and appearance. Finally, the beer is ready for packaging. Whether bottling, canning, or kegging, industrial packaging lines ensure the beer is sealed for freshness and ready for distribution.
Factors to Consider: Capacity, Space, Design, Layout, and Customization
When investing in industrial beer equipment, there are several factors to keep in mind. These parameters influence not only the operational efficiency of the brewery but also its production capacity and overall costs.
Parameter | Details |
---|---|
Capacity | Equipment sizes range from small craft setups (10-50 hectoliters) to massive commercial plants (over 1000 hectoliters). |
Space Requirements | Brewery equipment requires significant floor space. Smaller systems can fit into tight spaces, but larger breweries need ample room for tanks and lines. |
Design & Layout | Efficient layout is crucial for maximizing production. Proper spacing between tanks, piping, and walkways must be factored in for safety and efficiency. |
Customization Options | Many industrial brewing systems are fully customizable. Breweries can choose everything from tank sizes to automation levels, creating a system that meets their unique needs. |
The customization of brewing equipment can play a big role in enhancing a brewery’s identity. For instance, you might prefer more control over fermentation time for a unique beer flavor or want customized packaging to appeal to a specific audience.
Industrial Beer Equipment Price Range and Suppliers
Price is a key consideration when choosing brewing equipment. While smaller breweries can set up with a limited budget, large commercial operations demand significant capital investment. Let’s break down typical equipment costs and suppliers in the market.
Equipment Type | Estimated Price Range (USD) | Key Suppliers |
---|---|---|
Mash Tuns | $10,000 – $100,000+ | Brewmation, Paul Mueller, Ss Brewtech |
Fermentation Tanks | $20,000 – $200,000+ | DME Process Systems, Portland Kettle Works |
Boil Kettles | $15,000 – $150,000+ | Specific Mechanical Systems, JVNW |
Bright Beer Tanks | $10,000 – $120,000+ | Criveller Group, Ager Tank & Equipment |
Packaging Lines | $50,000 – $500,000+ | Krones, Alfa Laval, ProBrew |
Installation, Operation, and Maintenance
Installing industrial beer equipment is a complex process that should be handled by professionals. From setting up tanks to connecting piping and configuring automation controls, every detail matters. Poor installation can lead to inefficiencies, safety risks, and higher maintenance costs.
Installation
- Ensure proper placement of tanks for efficient workflow.
- Install piping to support the brewing process.
- Set up electrical connections for automated systems.
- Conduct thorough testing before full-scale operation.
Operation
Operating industrial beer equipment requires training and experience. Each piece of equipment has its own set of operational protocols. Automated systems often come with user-friendly interfaces that allow operators to monitor and control each stage of brewing in real-time.
Maintenance
To keep the system running smoothly, breweries need to establish a regular maintenance schedule. This includes routine cleaning, checking for wear and tear, and replacing any faulty components. Some maintenance tasks, such as cleaning tanks and filters, need to be performed daily, while others, like inspecting valves or replacing gaskets, can be done less frequently.
Installation | Operation | Maintenance |
---|---|---|
Requires professional setup | Specialized training required | Daily cleaning and inspections are essential |
Align equipment for workflow | Automation simplifies the process | Routine checks to prevent breakdowns |
Test all systems before use | Monitoring temperature and timing | Replace worn components before they fail |
How to Choose the Right Supplier for Industrial Beer Equipment
Choosing the right supplier is crucial for obtaining high-quality brewing equipment that meets your production goals. Here’s how to evaluate potential suppliers:
Factor | Details |
---|---|
Reputation | Look for established suppliers with strong customer reviews. Ask for references from other breweries. |
Price Transparency | Ensure the supplier provides clear and detailed pricing with no hidden fees. |
Customization Options | Check whether the supplier offers customizable solutions tailored to your brewing needs. |
After-Sales Support | Evaluate the availability of support for installation, troubleshooting, and maintenance. |
Warranty | Make sure the equipment comes with a comprehensive warranty covering parts and labor. |
Advantages and Limitations of Industrial Beer Equipment
When choosing equipment for your brewery, it’s important to weigh the pros and cons of different systems. Here’s a comparison of the advantages and limitations of industrial beer equipment:
Advantages | Limitations |
---|---|
Increased production capacity | High initial investment required |
More consistency and quality control | Space requirements can be extensive |
Advanced automation improves efficiency | Requires specialized training to operate |
Customizable options for unique brewing needs | Maintenance costs can add up over time |
Energy-efficient systems available | Complexity in setup and installation |
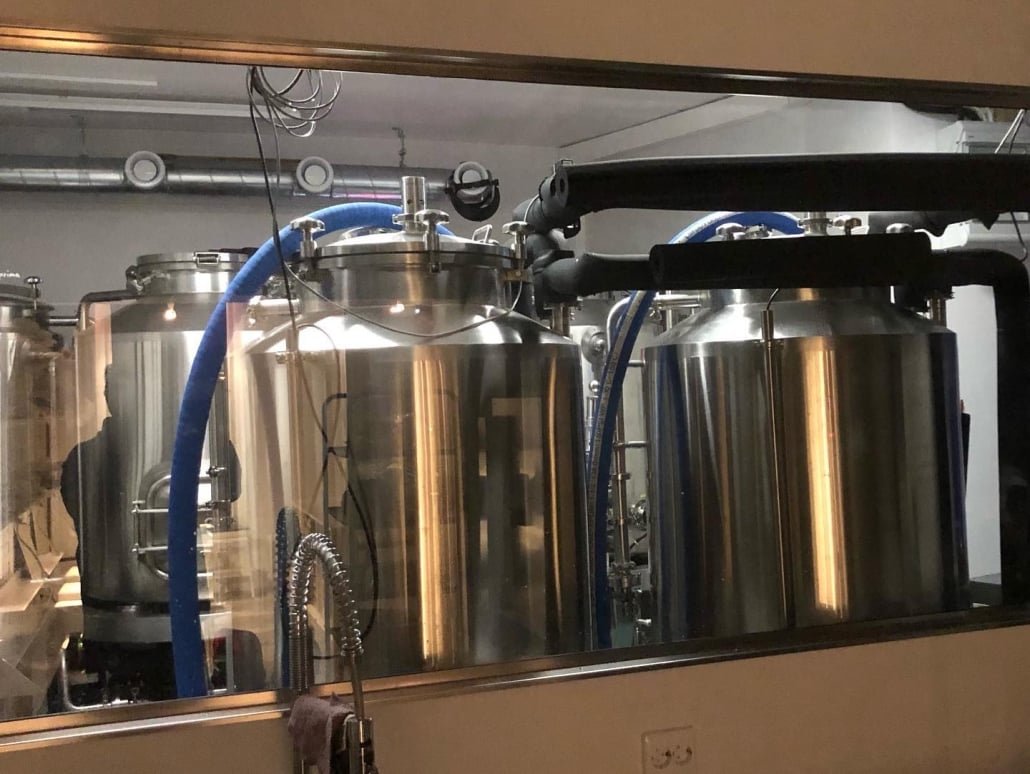
FAQs
To further help you understand the ins and outs of industrial beer equipment, here’s a FAQ section covering common questions:
Question | Answer |
---|---|
How much does it cost to start a brewery? | The cost varies widely, but a small brewery might require $500,000 to $1 million, while larger setups can exceed $5 million. |
How long does it take to brew beer commercially? | The entire process can take 2-6 weeks, depending on the type of beer and fermentation requirements. |
What is the lifespan of industrial brewing equipment? | Well-maintained equipment can last 10-20 years or more. |
Can I customize my brewing system? | Yes, many suppliers offer customization options based on your production capacity and brewing style. |
What are the most important maintenance tasks? | Regular cleaning, inspecting valves and gaskets, and checking temperature control systems are crucial. |
Conclusion
Industrial beer equipment is the backbone of any successful brewery. Whether you’re just starting out or looking to scale up your operations, having the right tools and systems in place can make all the difference in the quality of your beer and the efficiency of your process. From choosing the right suppliers to ensuring proper installation and maintenance, this guide covers everything you need to brew like a pro.
So, what’s your next step? Whether you’re dreaming of creating the next big IPA or scaling your existing operation, the right industrial beer equipment will help you achieve your goals.
Share this entry
Interested in learning more about Brewing Systems including additional details and pricing information? Please use the form below to contact us!
YOLONG BREWERY EQUIPMENT FAQS
- Commercial Brewery / Craft Brewery / Microbrewery / Nanobrewery
- What is The Difference Between Craft Beer and Industrial Beer?
- The Bespoke Differences In Custom Brewing Systems
- Everything You Need to Know About Kettle Souring
- How to Choose Brewing Equipment for Your business?
- How To Choose The-Best Partner To Build Your Commercial Microbrewing System?
- Two Detection Sensors That You Need To Use In Your Brewhouse System
- Remote Control Applications in Brewing Equipment/How does it work?
- How To Clean Your Brand New Brewery Tanks?