Industrial Beer Brewing Equipment
Overview of Industrial Beer Brewing Equipment
Beer brewing has been around for centuries, evolving from small, handcrafted batches to large-scale industrial production. The equipment used in industrial beer brewing is a marvel of modern engineering, designed to produce large volumes of beer efficiently while maintaining high quality. In this article, we will delve into the various aspects of industrial beer brewing equipment, providing a detailed guide to help you understand its complexities and advantages.
Guide to Industrial Beer Brewing Equipment
Brewing beer on an industrial scale requires a range of specialized equipment, each serving a unique purpose in the brewing process. The following sections will provide an in-depth look at each type of equipment, explaining its function and importance.
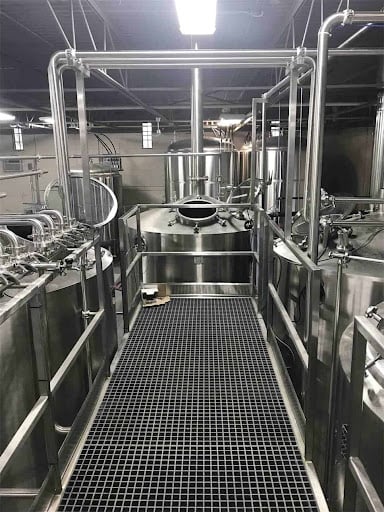
Types of Industrial Beer Brewing Equipment
Equipment Type | Description |
---|---|
Milling Equipment | Used to crush malted grains to expose the starches needed for fermentation. Essential for preparing the grains for mashing. |
Mash Tun | A vessel where milled grains are mixed with water and heated. This process converts starches into fermentable sugars. |
Lauter Tun | Separates the liquid wort from the grain husks after mashing. Crucial for ensuring a clear wort. |
Brew Kettle | Where the wort is boiled and hops are added. Boiling sterilizes the wort and extracts flavors from the hops. |
Whirlpool | Used post-boiling to separate hop particles and other solids from the wort. Ensures a clearer final product. |
Fermentation Tanks | Vessels where wort is fermented by yeast to produce alcohol and carbonation. Available in various sizes to suit production needs. |
Brite Tanks | Used for secondary fermentation and conditioning of the beer. They help in clarifying the beer and preparing it for packaging. |
Cooling Systems | Essential for maintaining the correct temperatures during various brewing stages. Includes glycol chillers and heat exchangers. |
Packaging Equipment | Includes bottling, canning, and kegging systems. Ensures that the beer is properly packaged for distribution. |
Cleaning and Sanitizing Systems | Automated systems for cleaning and sanitizing equipment, ensuring hygiene and preventing contamination. |
Control Systems | Computerized systems for monitoring and controlling various brewing parameters like temperature, pressure, and flow rates. |
The Brewing Process Explained
The brewing process is a meticulous journey from raw ingredients to the final product. Here’s a detailed look at each step involved:
1. Milling:
The process begins with milling the malted grains. Milling breaks the grains into smaller pieces, exposing the starches inside. This step is crucial because it prepares the grains for the next stage, mashing.
2. Mashing:
In the mash tun, the milled grains are mixed with hot water. This mixture, called mash, undergoes a series of temperature-controlled rests that convert starches into fermentable sugars. The result is a sweet liquid known as wort.
3. Lautering:
The mash is then transferred to a lauter tun, where the liquid wort is separated from the solid grain husks. This separation process is vital for obtaining a clear wort, which will be boiled in the next step.
4. Boiling:
The wort is boiled in the brew kettle. During boiling, hops are added at various stages to impart bitterness, flavor, and aroma to the beer. Boiling also sterilizes the wort, killing any unwanted bacteria or wild yeast.
5. Whirlpooling:
After boiling, the wort is moved to a whirlpool. Here, centrifugal forces help separate the hop particles and other solids from the wort. This step ensures a clearer final product.
6. Cooling:
The hot wort is rapidly cooled using a heat exchanger. This step is essential to bring the wort to a temperature suitable for fermentation, where yeast can be added.
7. Fermentation:
The cooled wort is transferred to fermentation tanks, where yeast is added. The yeast consumes the sugars in the wort, producing alcohol and carbon dioxide. This process can take several days to weeks, depending on the beer style.
8. Conditioning:
Once primary fermentation is complete, the beer is transferred to brite tanks for conditioning. This stage allows the beer to mature, develop flavors, and become naturally carbonated.
9. Packaging:
Finally, the beer is packaged in bottles, cans, or kegs. Packaging equipment ensures that the beer is filled, sealed, and labeled correctly for distribution.
Capacity, Space, Design, and Customization
Parameter | Details |
---|---|
Capacity | Industrial brewing systems range from small-scale setups (10-20 barrels) to large-scale systems (100+ barrels). The capacity required depends on production needs. |
Space Requirements | Industrial breweries need ample space for equipment, storage, and operations. Layout planning is crucial to ensure efficient workflow and safety. |
Design and Layout | The design should facilitate easy movement and operation. Consideration for future expansion is also essential. |
Customization Options | Breweries can customize equipment to meet specific needs, such as adding extra tanks, advanced control systems, or specialized cleaning systems. |
Suppliers and Price Range
Supplier | Price Range | Notes |
---|---|---|
Alpha Brewing | $100,000 – $500,000 | Known for high-quality, durable equipment. Offers customization and support services. |
BrewTech | $150,000 – $700,000 | Specializes in innovative brewing technology. Provides comprehensive installation and training. |
Blichmann | $80,000 – $400,000 | Offers a range of brewing systems for different scales. Known for excellent customer service and after-sales support. |
Ss Brewtech | $90,000 – $450,000 | Focuses on precision and efficiency. Offers both standard and custom solutions. |
Installation, Operation, and Maintenance
Aspect | Details |
---|---|
Installation | Professional installation is recommended. Suppliers often provide installation services to ensure proper setup and calibration. |
Operation | Training is essential for operating complex brewing systems. Most suppliers offer training programs for brewery staff. |
Maintenance | Regular maintenance is crucial for longevity and efficiency. Automated cleaning systems can simplify routine maintenance tasks. |
Troubleshooting | Having a support contract with the supplier can be beneficial for addressing any technical issues promptly. |
Choosing a Supplier
Criteria | Considerations |
---|---|
Reputation | Look for suppliers with positive reviews and a strong industry presence. |
Support Services | Ensure the supplier offers comprehensive support, including installation, training, and maintenance. |
Customization | Choose suppliers that can tailor equipment to meet your specific needs. |
Price and Value | Compare prices but also consider the value provided, such as durability, efficiency, and support services. |
Warranty and Guarantees | A good warranty can provide peace of mind and protection against potential defects or issues. |
Advantages and Limitations of Industrial Beer Brewing Equipment
Aspect | Advantages | Limitations |
---|---|---|
Production Volume | Allows for large-scale production, meeting high demand. | Requires significant initial investment and space. |
Quality Control | Advanced systems ensure consistent quality and flavor. | Complexity may require specialized knowledge and training. |
Efficiency | Automated processes reduce labor costs and increase efficiency. | Maintenance and troubleshooting can be costly and time-consuming. |
Customization | Can be tailored to specific brewing styles and processes. | Customization options may increase costs. |
Scalability | Easily scalable to increase production capacity. | Scaling up requires careful planning and additional investment. |
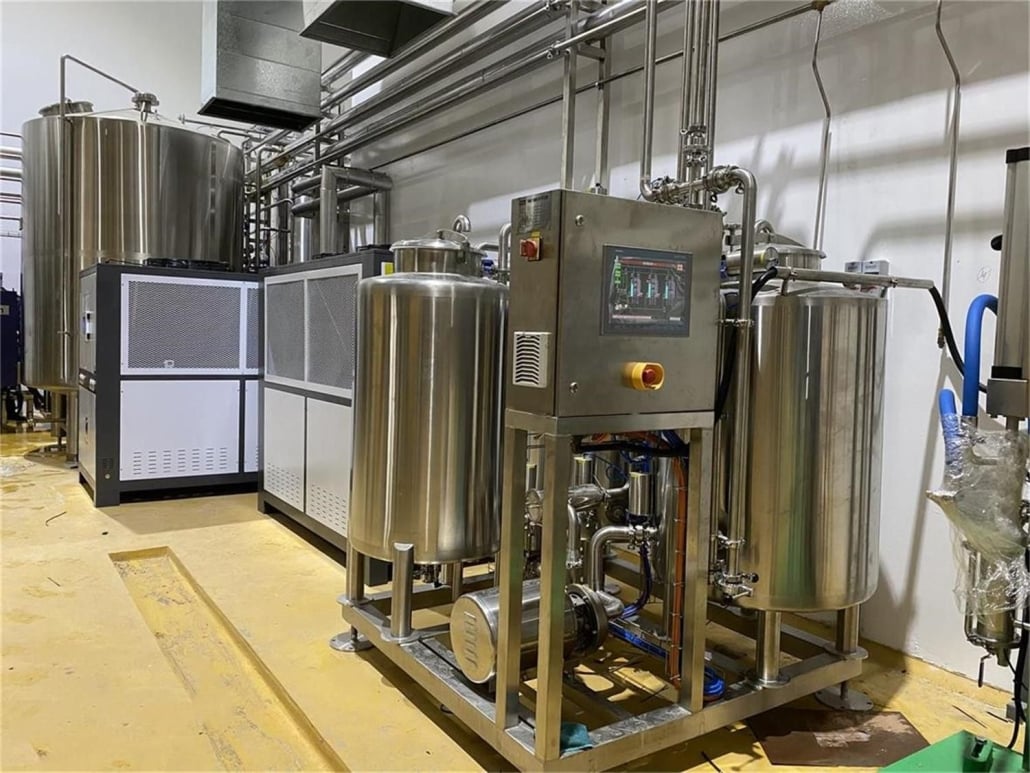
FAQs
Question | Answer |
---|---|
What is the cost of industrial beer brewing equipment? | The cost can range from $80,000 to $700,000, depending on capacity, customization, and supplier. |
How much space is needed for an industrial brewery? | Space requirements vary, but a typical medium-sized brewery might need between 2,000 to 5,000 square feet. |
What maintenance is required for brewing equipment? | Regular cleaning, inspections, and servicing of key components are essential. Automated cleaning systems can simplify these tasks. |
How long does it take to install industrial brewing equipment? | Installation time can range from a few weeks to several months, depending on the complexity and scale of the system. |
Can brewing equipment be customized? | Yes, many suppliers offer customization options to tailor the equipment to specific brewing needs and preferences. |
Share this entry
Interested in learning more about Brewing Systems including additional details and pricing information? Please use the form below to contact us!
YOLONG BREWERY EQUIPMENT FAQS
- Commercial Brewery / Craft Brewery / Microbrewery / Nanobrewery
- What is The Difference Between Craft Beer and Industrial Beer?
- The Bespoke Differences In Custom Brewing Systems
- Everything You Need to Know About Kettle Souring
- How to Choose Brewing Equipment for Your business?
- How To Choose The-Best Partner To Build Your Commercial Microbrewing System?
- Two Detection Sensors That You Need To Use In Your Brewhouse System
- Remote Control Applications in Brewing Equipment/How does it work?
- How To Clean Your Brand New Brewery Tanks?