The Ultimate Guide to Craft Brewing Systems
Overview of Craft Brewing Systems
Craft brewing has transformed from a niche hobby to a booming industry, as passionate brewers increasingly seek unique, high-quality systems that cater to diverse needs. Whether you’re an aspiring home brewer or an established microbrewery owner, finding the right brewing system is essential for crafting quality beer. In this comprehensive guide, we’ll explore the intricacies of craft brewing systems, offering insights into everything from equipment selection and setup to customization options and maintenance tips. So, what exactly does it take to build your dream brewing system?
Craft Brewing Equipment Guide
Craft brewing systems can vary significantly based on scale, output, customization, and specific brewing needs. Here’s a detailed look at the primary types of equipment involved and the key considerations when selecting each component.
Key Equipment in Craft Brewing Systems
Equipment Type | Description | Usage |
---|---|---|
Mash Tun | A tank where crushed grain is mixed with water to break down starches into fermentable sugars. | Essential for the mashing stage, impacting flavor profile and efficiency of sugar extraction. |
Brew Kettle | A vessel where the wort is boiled with hops, which adds bitterness, aroma, and flavor. | Crucial for achieving the desired bitterness and aroma in the final product. |
Fermenter | An airtight tank where the wort is fermented with yeast to produce alcohol. | Determines the fermentation quality and plays a key role in temperature control and cleanliness. |
Heat Exchanger | A device that cools down the wort before it enters the fermenter. | Rapid cooling prevents bacterial contamination, protecting the wort’s flavor and quality. |
Conditioning Tank | A storage tank where beer matures and conditions before being bottled or kegged. | Ensures a stable, refined flavor and appropriate carbonation levels. |
Filtration System | Equipment used to filter beer, removing any unwanted particulates. | Key for clarity, flavor stability, and quality consistency across batches. |
CIP (Clean-in-Place) System | A system for automatic cleaning of equipment to maintain hygiene and reduce contamination risks. | Maintains cleanliness and sterility, crucial in preventing off-flavors and contamination. |
Each of these components plays an essential role in producing high-quality craft beer, so understanding how they work and choosing the right specifications is critical.
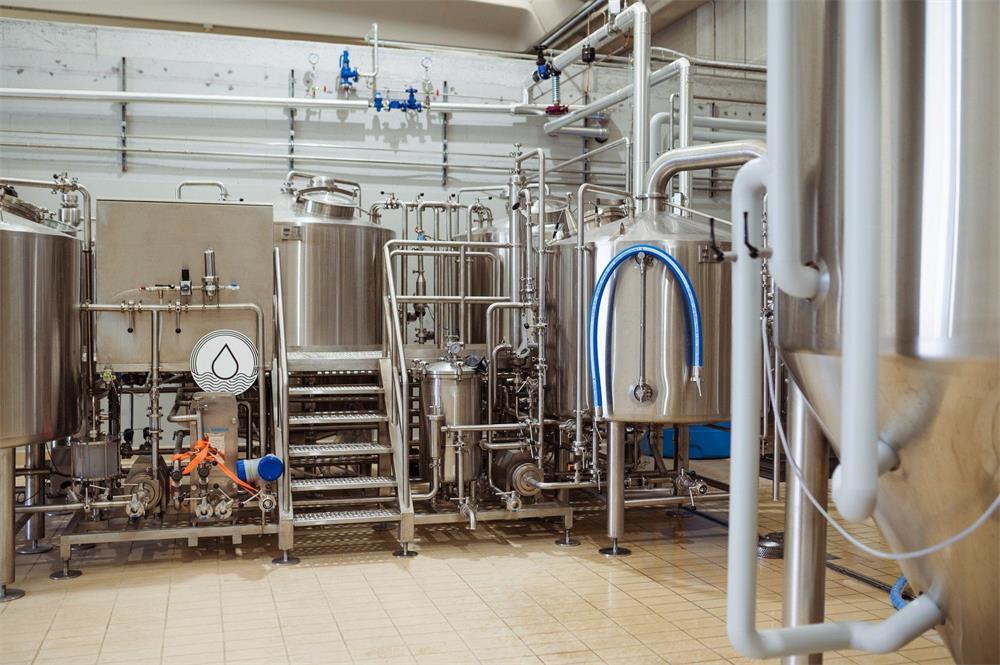
The Brewing Process Explained
The craft brewing process involves several stages, each contributing to the beer’s unique flavor and characteristics. Below, we explore the primary steps, from mashing to bottling, providing insights into each phase’s significance and impact on the final product.
1. Mashing
Mashing is the first step, where grains are steeped in hot water to convert starches into sugars. This sugar-rich mixture, or “wort,” forms the base of the beer. Mashing temperature, duration, and pH balance are all critical variables that affect the flavor profile, body, and alcohol content.
2. Boiling
Once mashing is complete, the wort is boiled, often with hops added at different stages. Boiling sterilizes the wort and releases hops’ bitterness, aroma, and flavors, allowing for a wide range of beer styles. Boiling time and hop variety significantly impact the final product’s taste.
3. Fermentation
After cooling, the wort is transferred to a fermenter, where yeast is added. The yeast consumes sugars, producing alcohol and carbonation in the process. Fermentation conditions, including temperature and duration, affect the taste, aroma, and alcohol content.
4. Conditioning and Aging
Post-fermentation, beer is transferred to a conditioning tank, where it matures, allowing flavors to blend and smooth out. This step can last from a few weeks to several months, depending on the beer style and desired flavor.
5. Filtration and Bottling
Finally, the beer undergoes filtration to remove any remaining particulates. Once filtered, the beer is carbonated and then bottled or kegged, ready for distribution or consumption.
Craft Brewing System Capacities, Spaces, and Layout
Different craft brewing setups suit different capacities, space requirements, and layouts. Below, a table details various system configurations to assist with designing a layout that maximizes efficiency and meets specific production goals.
Capacity | Space Required | Design Layout | Customization Options |
---|---|---|---|
Nano Brewery | 200-500 sq. ft. | Compact, vertical stacking | Small-scale, customizable tanks, adaptable control panels |
Microbrewery | 500-1,500 sq. ft. | Linear or modular layout | Modular tanks, semi-automated controls, customizable kettle sizes |
Brewpub | 1,000-3,000 sq. ft. | Integrated with seating space | Enhanced aesthetic, visibility options, partial automation |
Regional Brewery | 5,000+ sq. ft. | Large modular setup | Full automation, scalability features, high-volume output customization |
Layout and Space Planning Tips
When planning a craft brewing system, it’s essential to consider the operational workflow. Ensuring enough space for each brewing phase prevents bottlenecks, reduces risks of contamination, and enhances the overall efficiency of the brewing process. Additionally, strategic placement of tanks, kettles, and fermenters optimizes movement and minimizes unnecessary labor.
Supplier and Price Range Comparison for Craft Brewing Systems
Selecting the right supplier can make a significant difference in quality, cost, and customer support. Here, we present an overview of suppliers and their respective price ranges.
Supplier | Price Range ($USD) | Notable Features | Customer Support |
---|---|---|---|
BrewTech Solutions | $10,000 – $50,000 | Durable stainless steel, compact designs | 24/7 customer service |
CraftMaster Brew Systems | $20,000 – $70,000 | High customization, automated controls | Dedicated technician support |
Brauhaus Equipment | $15,000 – $60,000 | Semi-automated, modular systems | Comprehensive warranty |
MicroBrew Innovations | $12,000 – $40,000 | Scalable designs, CIP-compatible equipment | Customer training available |
Premier Brew Supplies | $25,000 – $80,000 | Advanced automation, premium-grade materials | Onsite installation and support |
How to Choose the Right Supplier
When evaluating suppliers, consider not only the price but also the reliability of materials, customization options, and after-sale support. A trusted supplier should offer high-quality stainless steel equipment, detailed installation guides, and accessible customer service for troubleshooting.
Installation, Operation, and Maintenance of Craft Brewing Systems
Proper installation, efficient operation, and regular maintenance are crucial to extending the life of brewing equipment and ensuring consistent, high-quality beer production.
Installation Considerations | Operation Tips | Maintenance Requirements |
---|---|---|
Site Preparation | Familiarize with control systems | Regular cleaning, particularly with CIP |
Plumbing and Electrical Setup | Monitor temperature and timing | Quarterly inspections for wear and tear |
Safety and Compliance Checks | Follow standard operating procedures | Calibrate sensors and control systems |
Equipment Testing and Calibration | Maintain optimal pH and sanitation | Annual servicing and part replacement |
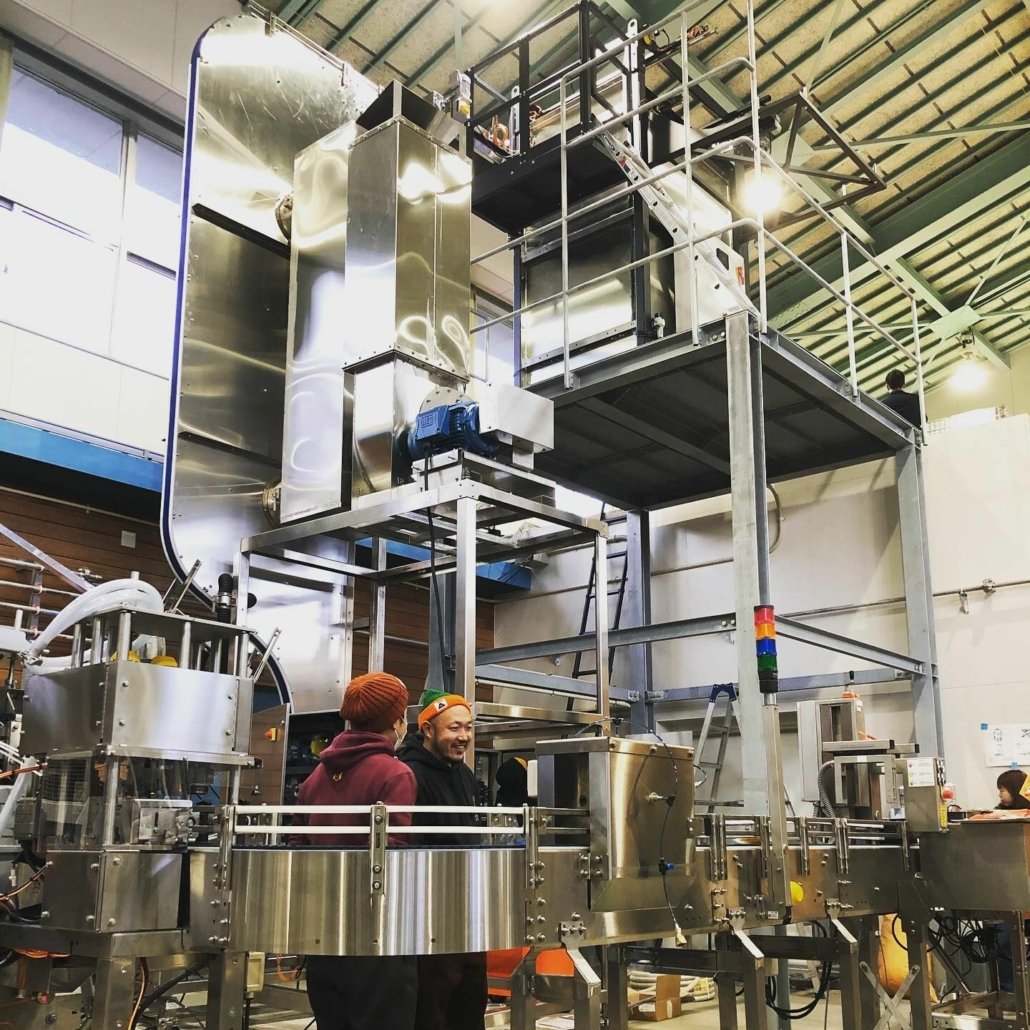
Advantages and Limitations of Different Craft Brewing Systems
Choosing between different craft brewing systems involves understanding the pros and cons associated with each option. Here’s a comparison:
System Type | Advantages | Limitations |
---|---|---|
Manual Brewing Systems | High level of control, lower upfront cost | Requires more labor, limited scalability |
Semi-Automated Systems | Balanced labor and control, moderate scalability | Higher cost, needs occasional supervision |
Fully Automated Systems | Minimal labor, consistent quality, high scalability | Expensive, less control over minor adjustments |
FAQs
Question | Answer |
---|---|
What is the ideal system size for beginners? | A nano or microbrewery setup is ideal for beginners, offering scalability and control. |
How often should a brewing system be maintained? | Regular cleanings are recommended after each use, with deeper maintenance quarterly. |
Can brewing systems be customized? | Yes, most suppliers offer customization options to suit different brewing styles and volumes. |
What is the lifespan of a typical brewing system? | With proper maintenance, systems can last between 10-15 years, depending on materials. |
|
Share this entry
Interested in learning more about Brewing Systems including additional details and pricing information? Please use the form below to contact us!
YOLONG BREWERY EQUIPMENT FAQS
- Commercial Brewery / Craft Brewery / Microbrewery / Nanobrewery
- What is The Difference Between Craft Beer and Industrial Beer?
- The Bespoke Differences In Custom Brewing Systems
- Everything You Need to Know About Kettle Souring
- How to Choose Brewing Equipment for Your business?
- How To Choose The-Best Partner To Build Your Commercial Microbrewing System?
- Two Detection Sensors That You Need To Use In Your Brewhouse System
- Remote Control Applications in Brewing Equipment/How does it work?
- How To Clean Your Brand New Brewery Tanks?