Complete Brewing System
When you think about brewing your own beer, it’s like embarking on a creative journey. But just like any great adventure, you need the right tools to get started. Enter the Complete Brewing System—your one-stop solution for crafting that perfect pint right from your home or brewery. This article will dive deep into everything you need to know about complete brewing systems, from choosing the right equipment to the brewing process, and how to maintain your system to ensure every brew is as good as the last.
Overview of a Complete Brewing System
A complete brewing system is an all-in-one setup that provides all the necessary tools and equipment to brew beer from start to finish. It typically includes a mash tun, boil kettle, fermenter, chiller, and other essential components. Whether you’re a homebrewer or running a microbrewery, a complete brewing system simplifies the process, offering efficiency and consistency in your brewing.
Why Choose a Complete Brewing System?
Choosing a complete brewing system streamlines your brewing process, minimizes guesswork, and ensures that all your equipment works harmoniously together. It’s perfect for both beginners looking to start their brewing journey and seasoned brewers who want to scale up their production. But before we dive into the nitty-gritty, let’s explore the components of a brewing system and how they work together.
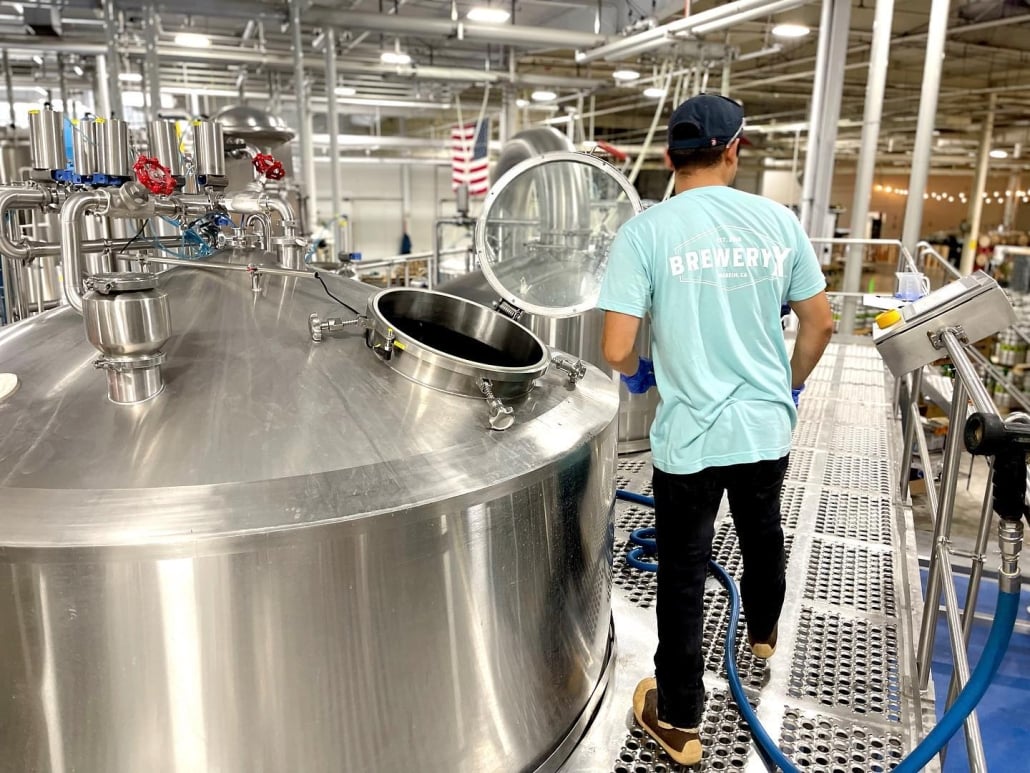
Essential Equipment in a Complete Brewing System
A complete brewing system is like a well-oiled machine, where each component plays a crucial role in the brewing process. Here’s a detailed look at the core equipment you’ll find in most complete brewing systems.
Mash Tun
The mash tun is where it all begins. This vessel is where the grains are mixed with hot water to convert starches into fermentable sugars—a process known as mashing. It usually comes with a false bottom or a filter to separate the liquid wort from the spent grains.
Boil Kettle
Once mashing is complete, the wort is transferred to the boil kettle. This is where the wort is boiled and hops are added, contributing to the beer’s bitterness, flavor, and aroma. The boil kettle is often equipped with a whirlpool system to help separate the solid particles from the liquid after boiling.
Fermenter
After boiling, the wort is cooled and transferred to the fermenter. This is where the magic happens—yeast is added, and fermentation begins, converting sugars into alcohol and carbon dioxide. Fermenters come in various sizes and can be made from stainless steel, glass, or plastic.
Wort Chiller
A wort chiller is essential for quickly bringing the wort down to a temperature suitable for yeast pitching after boiling. This step is crucial to prevent contamination and ensure a healthy fermentation.
Pumps and Valves
Pumps and valves facilitate the transfer of liquids between different stages of brewing, ensuring a smooth and efficient process. They are particularly useful in larger systems where manual transfer would be cumbersome.
Control Panel
The control panel is the brain of your brewing system. It allows you to monitor and adjust various parameters such as temperature, flow rate, and timing, ensuring precise control over the brewing process.
Types of Brewing Systems
Brewing systems come in various forms, each tailored to different needs and scales of operation. Below is a comparison of different types of brewing systems available on the market:
Type of Brewing System | Description | Ideal For | Advantages | Limitations |
---|---|---|---|---|
Home Brewing Kits | Compact systems designed for small batch brewing, usually up to 5 gallons. | Hobbyists and beginners | Affordable, easy to use, space-saving. | Limited batch size, fewer customization options. |
Nano Brewing Systems | Small-scale systems, producing up to 3 barrels per batch. | Startups and small brewpubs | Allows for experimentation, relatively low cost, scalable. | Limited production capacity, may require frequent brewing to meet demand. |
Microbrewing Systems | Systems designed for microbreweries, producing up to 15 barrels per batch. | Microbreweries and brewpubs | Balanced production capacity, suitable for commercial distribution. | Requires significant space and investment, complexity in operation. |
Commercial Brewing Systems | Large-scale systems for producing over 15 barrels per batch. | Established breweries | High production capacity, advanced automation, suitable for mass distribution. | High initial investment, complex installation and maintenance, large space requirement. |
Custom Brewing Systems | Tailored systems designed to meet specific brewing requirements. | Experienced brewers and brands | Fully customizable, high efficiency, meets specific production and quality standards. | High cost, requires extensive planning and expertise to design and operate. |
The Brewing Process
Brewing is as much an art as it is a science. While the complete brewing system provides the tools, it’s the process that turns raw ingredients into delicious beer. Below is an overview of the brewing process:
1. Mashing
The brewing process starts with mashing, where malted barley is mixed with hot water in the mash tun. The heat activates enzymes that convert the starches in the grains into fermentable sugars. This mixture, known as mash, is then held at a specific temperature to ensure complete conversion.
2. Lautering
After mashing, the mash is transferred to a lauter tun, where the liquid wort is separated from the grain husks. The wort is then rinsed with additional hot water in a process called sparging, which extracts as much sugar as possible from the grains.
3. Boiling
The wort is then transferred to the boil kettle, where it’s boiled for a set period. During the boil, hops are added at different stages to impart bitterness, flavor, and aroma to the beer. Boiling also sterilizes the wort, killing any unwanted microbes.
4. Cooling
After boiling, the wort needs to be quickly cooled to a temperature suitable for fermentation. This is typically done using a wort chiller. Rapid cooling is crucial to prevent contamination and ensure that the yeast can thrive once added.
5. Fermentation
The cooled wort is transferred to a fermenter, and yeast is added. Over the next few days to weeks, the yeast ferments the sugars in the wort, producing alcohol and carbon dioxide. The fermenter is often equipped with temperature control to ensure the yeast performs optimally.
6. Conditioning
Once fermentation is complete, the beer is conditioned. This can involve aging the beer to allow flavors to develop and mellow. During conditioning, the beer may also be carbonated, either naturally or through forced carbonation.
7. Packaging
Finally, the beer is ready to be packaged. Depending on the system, this could involve bottling, canning, or kegging. Packaging is done in a way that minimizes oxygen exposure to maintain the beer’s freshness.
Choosing the Right Brewing System
Selecting the right brewing system can be a daunting task, especially with the variety of options available. To help you make an informed decision, here’s a detailed comparison table covering capacity, space requirements, design, layout, and customization options.
Brewing System Feature | Home Brewing Kits | Nano Brewing Systems | Microbrewing Systems | Commercial Brewing Systems | Custom Brewing Systems |
---|---|---|---|---|---|
Capacity | 1-5 gallons per batch | Up to 3 barrels per batch | Up to 15 barrels per batch | Over 15 barrels per batch | Variable, based on design |
Space Requirements | Compact, can fit on a kitchen counter | Requires a small dedicated space | Requires a dedicated brewing area | Requires a large industrial space | Depends on system specifications |
Design | Simple, easy to set up | More complex, often modular | Advanced, with dedicated tanks | Highly advanced, fully integrated | Tailored to specific needs |
Layout | Integrated in a single unit | Modular components | Separate components for each process | Integrated with advanced automation | Custom layout based on workflow |
Customization | Limited customization options | Some customization available | Customizable within certain limits | Highly customizable, often bespoke | Fully customizable to specific needs |
Suppliers and Price Range for Complete Brewing Systems
Understanding the cost and suppliers of brewing systems is essential for budgeting and planning. Below is a table outlining various suppliers, their offerings, and the price range for different types of complete brewing systems.
Supplier | System Type | Price Range | Customization Options | Support and Warranty |
---|---|---|---|---|
Blichmann Engineering | Home Brewing Kits | $500 – $2,000 | Limited to small-scale systems | 1-year warranty, tech support |
Ss Brewtech | Nano Brewing Systems | $2,000 – $10,000 | Some customization available | 2-year warranty, tech support |
Spokane Industries | Microbrewing Systems | $10,000 – $50,000 | Customizable within product range | 3-year warranty, comprehensive support |
ProBrew | Commercial Brewing Systems | $50,000 – $500,000 | High level of customization | 5-year warranty, full support |
Specific Mechanical | Custom Brewing Systems | $100,000 – $1,000,000+ | Fully customizable to client specs | Tailored support and extended warranty |
Installation, Operation, and Maintenance
A complete brewing system is an investment, and proper installation, operation, and maintenance are crucial to getting the most out of it. Here’s what you need to know:
Aspect | Details |
---|---|
Installation | Involves setting up the equipment according to the manufacturer’s guidelines. Larger systems may require professional installation, including plumbing, electrical work, and possibly even construction modifications. |
Operation | Operating a brewing system involves following specific procedures for each stage of the brewing process. Automation in larger systems can simplify operation, but a good understanding of brewing principles is still essential. |
Maintenance | Regular cleaning, inspection, and servicing of equipment are vital to maintaining efficiency and prolonging the lifespan of the system. This includes sanitizing fermenters, descaling kettles, and checking for wear and tear on pumps and valves. |
How to Choose a Supplier for Your Brewing System
Choosing the right supplier is as important as selecting the right brewing system. Below is a table that highlights the key factors to consider when selecting a supplier:
Consideration | Details |
---|---|
Reputation | Research the supplier’s reputation in the brewing industry. Look for reviews, testimonials, and case studies. A supplier with a strong track record is more likely to provide reliable products and support. |
Product Range | Ensure the supplier offers the type of system you need, whether it’s for home brewing or commercial brewing. The more comprehensive their product range, the more likely they are to have a system that fits your needs. |
Customization | If you have specific brewing needs, choose a supplier that offers customization options. This is particularly important for commercial and custom brewing systems. |
Support and Warranty | Check the level of support provided by the supplier, including technical support, training, and warranty. A strong support system can be invaluable, especially when dealing with complex equipment. |
Price vs. Value | Compare the cost of the system with the value it offers. Sometimes, a lower price might mean compromising on quality or features, so ensure you’re getting the best value for your investment. |
Lead Time and Delivery | Consider the lead time for production and delivery, especially for custom systems. Timely delivery is crucial for keeping your brewing schedule on track. |
Advantages and Limitations of Complete Brewing Systems
While complete brewing systems offer numerous benefits, they also come with some limitations. Here’s a comparative analysis to help you weigh the pros and cons:
Advantages | Limitations |
---|---|
Ease of Use: Complete brewing systems are designed to simplify the brewing process, making it easier for both beginners and experienced brewers to achieve consistent results. | Cost: Complete systems, especially commercial and custom ones, can be expensive, requiring significant upfront investment. |
Consistency: With all components working together seamlessly, these systems help ensure consistent quality in every batch. | Space Requirements: Larger systems require significant space, which might be a limitation for small breweries or home setups. |
Efficiency: Automation and integrated controls make brewing more efficient, saving time and reducing the risk of errors. | Complexity: While automation simplifies the process, it can also add complexity in terms of operation and troubleshooting. |
Customization: Many complete systems offer customization options, allowing brewers to tailor the system to their specific needs. | Maintenance: Regular maintenance is essential to keep the system running smoothly, which can be time-consuming and require technical knowledge. |
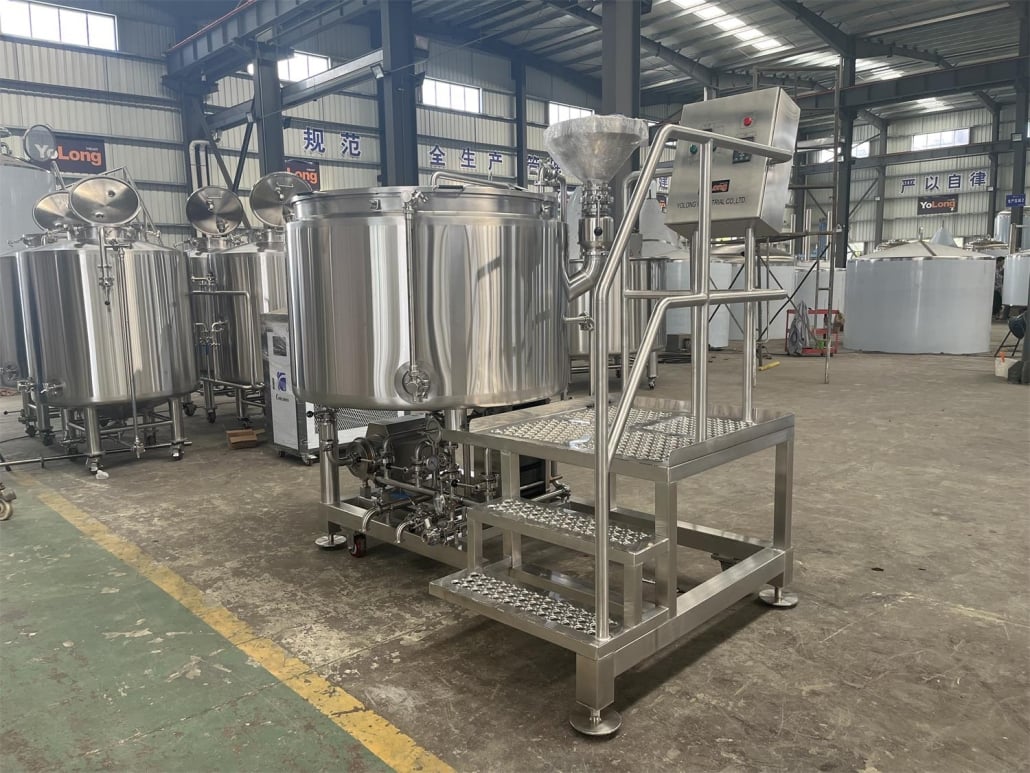
FAQs
What is a Complete Brewing System?
A complete brewing system is an integrated setup that includes all the necessary equipment for brewing beer from start to finish. This typically includes a mash tun, boil kettle, fermenter, and other components, allowing you to manage the entire brewing process in one cohesive system.
How Much Does a Complete Brewing System Cost?
The cost of a complete brewing system can vary widely depending on the type and scale of the system. Home brewing kits can start as low as $500, while commercial systems can cost upwards of $500,000 or more. Custom systems designed for specific needs can even exceed $1 million.
What Size Brewing System Do I Need?
The size of the brewing system you need depends on your production goals. Home brewers may be satisfied with a system that produces 5 gallons per batch, while microbreweries and commercial breweries will require much larger systems capable of producing 15 barrels or more per batch.
How Do I Maintain a Brewing System?
Maintaining a brewing system involves regular cleaning, inspection, and servicing of all components. This includes sanitizing fermenters, descaling kettles, checking for wear and tear on pumps and valves, and ensuring that all automated systems are functioning correctly.
Can I Customize My Brewing System?
Yes, many suppliers offer customization options for brewing systems, especially for commercial and custom systems. This allows you to tailor the system to your specific brewing process, production goals, and space requirements.
What Should I Consider When Choosing a Supplier?
When choosing a supplier, consider their reputation, the range of products they offer, customization options, support and warranty, price vs. value, and lead time for delivery. A reliable supplier will provide not just the equipment but also the support you need to succeed.
Conclusion
Investing in a complete brewing system is a significant step for any brewer, whether you’re just starting out or looking to expand your operations. By understanding the components, the brewing process, and the factors involved in choosing the right system and supplier, you can make an informed decision that will serve your brewing needs for years to come.
Share this entry
Interested in learning more about Brewing Systems including additional details and pricing information? Please use the form below to contact us!
YOLONG BREWERY EQUIPMENT FAQS
- Commercial Brewery / Craft Brewery / Microbrewery / Nanobrewery
- What is The Difference Between Craft Beer and Industrial Beer?
- The Bespoke Differences In Custom Brewing Systems
- Everything You Need to Know About Kettle Souring
- How to Choose Brewing Equipment for Your business?
- How To Choose The-Best Partner To Build Your Commercial Microbrewing System?
- Two Detection Sensors That You Need To Use In Your Brewhouse System
- Remote Control Applications in Brewing Equipment/How does it work?
- How To Clean Your Brand New Brewery Tanks?