Commercial Beer Equipment for Sale
Overview
Starting a brewery is an exciting venture, but it’s crucial to understand the ins and outs of commercial beer equipment for sale. This guide will walk you through everything you need to know, from the different types of equipment available to the brewing process, and how to choose the best supplier for your needs. We’ll cover key details in an engaging, conversational style to make your journey into the brewing world as smooth as a perfectly poured pint.
Equipment Guide for Commercial Beer Brewing
When it comes to commercial beer brewing, the equipment you choose can make or break your brewery. Let’s dive into the essential equipment you’ll need to get started.
Brewhouse System: The heart of any brewery, the brewhouse system, includes mash tuns, lauter tuns, kettles, and whirlpool systems. These components work together to create the wort, the sugary liquid that will eventually become beer.
Fermentation Vessels: After the wort is cooled, it’s transferred to fermentation vessels where yeast is added. This is where the magic happens as yeast ferments the sugars into alcohol and carbon dioxide.
Bright Beer Tanks: These tanks are used to clarify and carbonate the beer after fermentation. They are essential for the final steps before packaging.
Packaging Equipment: This includes bottling lines, canning lines, and kegging systems. Packaging equipment ensures your beer is safely and efficiently transported to consumers.
Quality Control Tools: Essential for maintaining the consistency and quality of your beer. This includes hydrometers, pH meters, and CO2 testers.
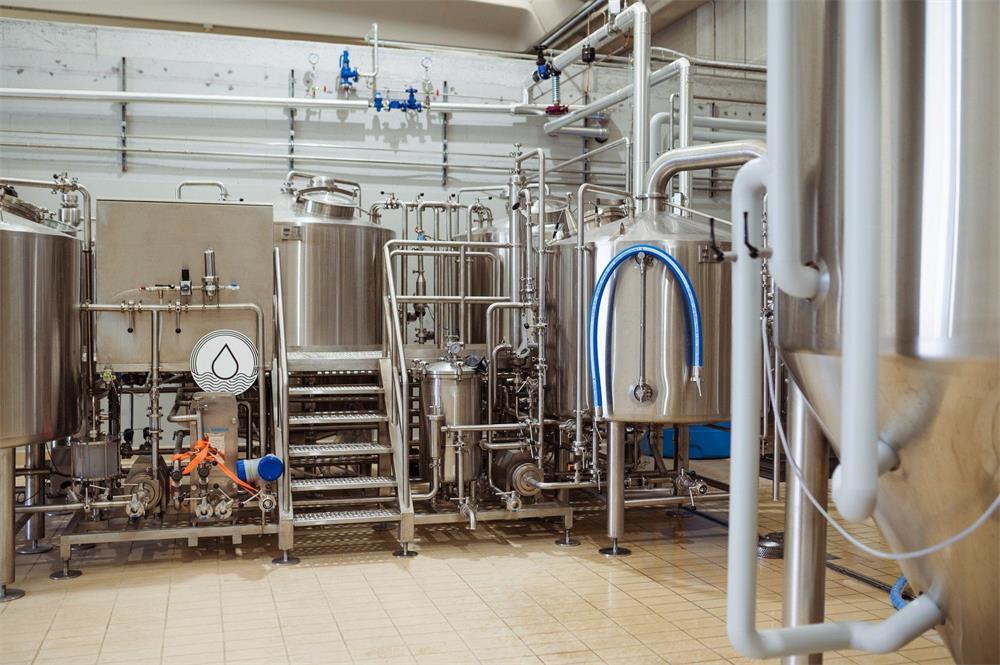
Types of Commercial Beer Equipment
Here’s a detailed look at the types of equipment you need to consider when setting up your brewery:
Equipment Type | Description |
---|---|
Brewhouse System | Comprises mash tuns, lauter tuns, kettles, and whirlpool systems. |
Fermentation Vessels | Tanks where wort is fermented with yeast to produce alcohol. |
Bright Beer Tanks | Used for clarifying and carbonating beer before packaging. |
Packaging Equipment | Includes bottling, canning, and kegging systems for distributing the beer. |
Quality Control Tools | Instruments like hydrometers, pH meters, and CO2 testers to ensure beer quality. |
The Brewing Process Explained
Brewing beer is a blend of art and science. Here’s a breakdown of the brewing process:
- Mashing: The process begins in the mash tun, where milled grain (malt) is mixed with hot water. This activates enzymes in the malt to convert starches to sugars, creating a sugary liquid called wort.
- Lautering: The wort is then separated from the grain husks in the lauter tun. This step ensures a clear wort is produced for boiling.
- Boiling: The wort is boiled, and hops are added at various stages. This step sterilizes the wort and extracts flavors and bitterness from the hops.
- Whirlpool: Post-boil, the wort is spun in a whirlpool to remove hop particles and other solids.
- Cooling: The wort is quickly cooled to a temperature suitable for fermentation.
- Fermentation: The cooled wort is transferred to fermentation vessels where yeast is added. The yeast ferments the sugars into alcohol and carbon dioxide.
- Conditioning: The beer is conditioned in bright beer tanks where it is clarified and carbonated.
- Packaging: Finally, the beer is packaged in bottles, cans, or kegs for distribution.
Capacity, Space, Design, and Customization
When planning your brewery, consider the capacity, space requirements, and design of your equipment. Customization options are also important to fit your specific needs.
Aspect | Details |
---|---|
Capacity | Determine your production goals. Equipment ranges from small-scale systems to large commercial setups. |
Space | Consider the layout and size of your facility. Ensure you have enough room for all equipment and operations. |
Design | Opt for designs that enhance efficiency and workflow in your brewery. |
Customization | Many suppliers offer customization to meet specific brewing requirements and space constraints. |
Suppliers and Price Range
Choosing the right supplier is crucial for getting high-quality equipment at a reasonable price. Here’s a guide to some of the top suppliers and their price ranges:
Supplier | Price Range (USD) | Details |
---|---|---|
BrewTech | $10,000 – $500,000 | Offers a wide range of equipment for all brewery sizes. |
PicoBrew | $5,000 – $200,000 | Known for customizable brewing systems. |
SS Brewtech | $15,000 – $400,000 | High-quality, durable equipment with excellent customer support. |
Premier Stainless | $20,000 – $600,000 | Specializes in turnkey systems for commercial breweries. |
Blichmann Engineering | $7,000 – $250,000 | Offers innovative brewing solutions with a focus on small to mid-sized breweries. |
Installation, Operation, and Maintenance
Proper installation, operation, and maintenance are vital to the smooth running of your brewery. Here’s what you need to know:
Aspect | Details |
---|---|
Installation | Professional installation ensures your equipment is set up correctly and safely. |
Operation | Training is essential. Most suppliers offer training programs to get you up and running. |
Maintenance | Regular maintenance keeps your equipment in top condition. This includes cleaning, sanitizing, and routine checks. |
How to Choose the Best Supplier
Choosing the right supplier involves several factors. Here’s a guide to help you make the best choice:
Factor | Details |
---|---|
Reputation | Research the supplier’s reputation in the industry. Look for reviews and testimonials. |
Quality | Ensure the equipment is of high quality and meets industry standards. |
Customization Options | Check if the supplier offers customization to fit your specific needs. |
Support and Service | Good customer support and after-sales service are crucial. |
Price | Compare prices to ensure you’re getting good value for your investment. |
Comparing Pros and Cons
Every piece of equipment has its advantages and limitations. Here’s a comparison to help you weigh your options:
Equipment Type | Advantages | Limitations |
---|---|---|
Brewhouse System | Efficient wort production, customizable sizes. | High initial cost, requires significant space. |
Fermentation Vessels | Essential for fermentation, available in various sizes. | Requires temperature control, can be expensive. |
Bright Beer Tanks | Necessary for beer clarification and carbonation. | Additional cost, space requirement. |
Packaging Equipment | Ensures efficient beer distribution. | High cost, complex setup. |
Quality Control Tools | Maintains beer quality and consistency. | Needs regular calibration, additional cost. |
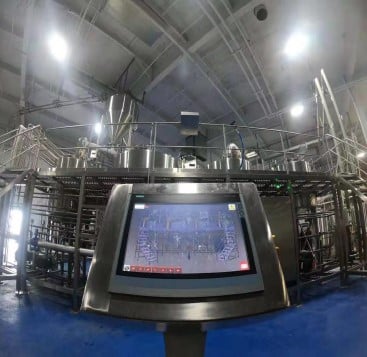
FAQ
Here are some frequently asked questions about commercial beer equipment:
Question | Answer |
---|---|
What is the most crucial piece of brewing equipment? | The brewhouse system is considered the heart of the brewery as it starts the brewing process. |
How much does it cost to start a brewery? | Costs vary widely depending on the size and scale, ranging from $100,000 to over $1 million. |
Can I customize my brewing equipment? | Yes, many suppliers offer customization options to meet specific brewing needs and space constraints. |
How often should I maintain my equipment? | Regular maintenance is crucial, with some parts needing daily cleaning and others monthly or quarterly checks. |
What are the key factors in choosing a supplier? | Reputation, quality, customization options, support and service, and price are all important factors to consider. |
Share this entry
Interested in learning more about Brewing Systems including additional details and pricing information? Please use the form below to contact us!
YOLONG BREWERY EQUIPMENT FAQS
- Commercial Brewery / Craft Brewery / Microbrewery / Nanobrewery
- What is The Difference Between Craft Beer and Industrial Beer?
- The Bespoke Differences In Custom Brewing Systems
- Everything You Need to Know About Kettle Souring
- How to Choose Brewing Equipment for Your business?
- How To Choose The-Best Partner To Build Your Commercial Microbrewing System?
- Two Detection Sensors That You Need To Use In Your Brewhouse System
- Remote Control Applications in Brewing Equipment/How does it work?
- How To Clean Your Brand New Brewery Tanks?