The Comprehensive Guide to Bright Beer Tanks
Overview: Understanding Bright Beer Tanks
Bright beer tanks (BBTs) are an essential component in the brewing process, serving as the final stop before beer is packaged for distribution. These tanks, also known as conditioning or maturation tanks, are where beer undergoes its final clarification, carbonation, and maturation stages, ensuring it meets the desired flavor profile, clarity, and carbonation levels.
In this guide, we’ll dive into the technical aspects of bright beer tanks, exploring their design, functionality, types, and much more. Whether you’re a brewer looking to optimize your brewing process or simply curious about the science behind that perfectly brewed beer, this comprehensive guide will provide you with all the insights you need.
Bright Beer Tank Equipment Guide
Bright beer tanks are a crucial part of the brewing system, designed to hold beer after it has undergone primary fermentation and before it is packaged. These tanks are responsible for:
- Carbonation: Achieving the right carbonation level.
- Clarification: Removing remaining yeast and sediments.
- Maturation: Allowing the beer to mature, which enhances flavor.
Key Components of Bright Beer Tanks:
- Tanks: Constructed from stainless steel to ensure durability, hygiene, and resistance to corrosion. The size and shape can vary depending on the brewery’s needs.
- Pressure Control Systems: To maintain the ideal pressure within the tank, ensuring proper carbonation.
- Cooling Jackets: Wrapped around the tank to control temperature during the maturation process.
- Sampling Valves: For taking beer samples during the process to check clarity and flavor.
- CIP Systems: Clean-In-Place systems ensure the tanks remain sanitized without needing to be disassembled.
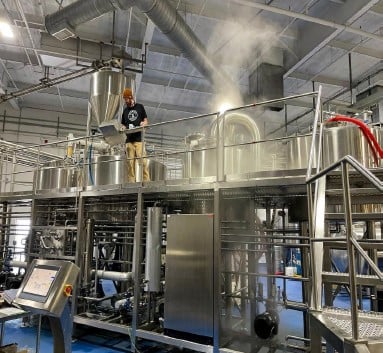
Types of Bright Beer Tanks
Bright beer tanks come in various sizes and configurations, tailored to different brewing needs. The following table provides an overview of the common types of BBTs, their features, and their applications.
Type | Description | Common Applications |
---|---|---|
Horizontal BBTs | Typically used in larger breweries, these tanks allow for a larger surface area, which can lead to faster clarification and maturation. | Large-scale commercial brewing |
Vertical BBTs | The most common type, suitable for breweries of all sizes. These tanks are space-efficient and are often used for final conditioning before packaging. | Craft breweries, microbreweries |
Stackable BBTs | Designed for breweries with limited space, these tanks can be stacked on top of one another to maximize space usage. | Small breweries, brewpubs |
Jacketed BBTs | Equipped with cooling jackets, these tanks are ideal for maintaining precise temperature control during maturation. | Breweries requiring strict temperature control during conditioning |
Non-Jacketed BBTs | More cost-effective but without built-in temperature control, making them suitable for environments with stable ambient temperatures. | Breweries in temperate climates, cost-conscious operations |
The Brewing Process and the Role of Bright Beer Tanks
The brewing process is intricate, involving several stages from mashing to packaging. Bright beer tanks come into play during the final stages:
- Post-Fermentation: After primary fermentation, the beer is transferred into bright beer tanks. Here, it undergoes secondary fermentation if needed, and the process of carbonation begins.
- Carbonation: CO2 is either naturally produced by yeast activity (secondary fermentation) or injected into the beer to achieve the desired level of carbonation.
- Clarification: During this stage, remaining yeast, hops, and other particulates settle out of the beer. This can be aided by fining agents or filtration systems integrated with the bright beer tank.
- Maturation: The beer matures over time in the BBT, developing its final flavor profile. The duration can vary from a few days to several weeks, depending on the style of beer.
- Packaging: Once the beer has reached the desired clarity, carbonation, and flavor, it is packaged directly from the bright beer tank into bottles, cans, or kegs.
Comparing Bright Beer Tank Capacities, Space Requirements, and Design Customization
The design of a bright beer tank can greatly influence its performance and suitability for different brewing operations. Below is a comparison table highlighting these factors:
Parameter | Description |
---|---|
Capacity Range | Bright beer tanks can range from small 5-barrel units to large 100-barrel tanks, accommodating the needs of microbreweries to large-scale operations. |
Space Requirements | Horizontal tanks require more floor space but allow faster maturation, while vertical tanks are space-efficient but may take longer for maturation. |
Design Customization | Tanks can be customized with features like additional sampling ports, enhanced insulation, and custom dimensions to fit specific brewery layouts. |
Cooling Systems | Jacketed tanks offer precise temperature control, essential for lagers and other styles requiring cold conditioning. |
Material Quality | High-quality stainless steel (typically 304 or 316 grade) is standard, ensuring longevity, ease of cleaning, and resistance to corrosion. |
Bright Beer Tank Suppliers and Price Range
The market offers a variety of suppliers catering to different budget ranges and brewery sizes. Below is a detailed table listing some prominent suppliers, their offerings, and typical price ranges.
Supplier | Offerings | Price Range (Approximate) |
---|---|---|
Company A | Customizable BBTs, jacketed and non-jacketed options | $10,000 – $50,000 depending on size and customization |
Company B | Standard BBTs, focus on cost-efficiency | $8,000 – $30,000 |
Company C | High-end BBTs with advanced features like integrated filtration | $15,000 – $70,000 |
Company D | Compact, stackable BBTs for small breweries | $7,000 – $25,000 |
Installation, Operation, and Maintenance of Bright Beer Tanks
Operating bright beer tanks effectively requires understanding their installation, operation, and maintenance requirements. Proper setup and care are essential to ensuring the longevity and optimal performance of these tanks.
Installation Process:
- Site Preparation: Ensure the space is adequately prepared with the necessary utilities (power, water, drainage). The floor should be leveled and capable of supporting the weight of the filled tanks.
- Tank Positioning: Place the tanks in their designated positions, ensuring easy access for operation and maintenance.
- Utility Connections: Connect the necessary utilities, including CO2 lines, cooling systems, and CIP systems.
- Initial Testing: After installation, tanks should be tested for leaks, pressure integrity, and proper functioning of all systems.
Operation Tips:
- Regular Monitoring: Continuously monitor pressure levels, temperature, and carbonation to ensure consistency.
- Sampling: Regularly sample the beer to check for clarity, flavor, and carbonation levels.
- Adjustments: Make necessary adjustments to pressure and temperature settings based on the style of beer and desired outcomes.
Maintenance Guidelines:
- CIP Cleaning: Utilize the tank’s CIP system regularly to maintain cleanliness and prevent contamination.
- Pressure Checks: Regularly check and calibrate pressure gauges and safety valves.
- Inspections: Periodically inspect the tank for signs of wear, corrosion, or damage, especially around weld seams and fittings.
- Cooling System Maintenance: Ensure cooling jackets or external cooling systems are functioning properly and not leaking.
Task | Frequency | Details |
---|---|---|
CIP Cleaning | After every batch | Run a full cleaning cycle to sanitize the tank. |
Pressure Checks | Weekly | Inspect and calibrate pressure-related equipment to avoid over-pressurization. |
Cooling System Inspection | Monthly | Check for leaks or inefficiencies in the cooling system. |
Overall Inspection | Quarterly | A thorough check of all tank components for any signs of wear or damage. |
Choosing the Right Bright Beer Tank Supplier
Selecting the right supplier is critical to ensuring that your bright beer tanks meet your brewery’s needs. Consider the following factors when making your decision:
Factor | What to Look For |
---|---|
Reputation | Check reviews, testimonials, and case studies to gauge the supplier’s reputation. |
Customization Options | Ensure the supplier can tailor the tanks to your specific requirements, including size, shape, and additional features. |
Price vs. Quality | Balance your budget with the quality of materials and construction. Higher-quality tanks may have a higher upfront cost but lower long-term maintenance. |
Customer Support | Consider suppliers that offer comprehensive customer support, including installation assistance and ongoing maintenance services. |
Delivery Times | Check the supplier’s ability to deliver the tanks within your project timeline. |
After-Sales Service | Opt for suppliers who provide after-sales services like maintenance contracts or spare parts availability. |
Advantages and Limitations of Bright Beer Tanks
Understanding the pros and cons of bright beer tanks will help you determine if they are the right fit for your brewery’s production goals.
Advantages:
- Improved Clarity: Bright beer tanks facilitate the settling of yeast and other particulates, resulting in a clearer final product.
- Consistent Carbonation: These tanks are designed to achieve and maintain consistent carbonation levels, crucial for quality control.
- Versatility: Suitable for various beer styles and can be used for both conditioning and carbonation.
- Space Efficiency: Vertical tanks are particularly space-efficient, making them ideal for breweries with limited space.
Limitations:
- Initial Cost: The upfront investment can be significant, especially for high-capacity, jacketed tanks.
- Maintenance: Requires regular cleaning and maintenance, which can be time-consuming and costly.
- Temperature Sensitivity: Non-jacketed tanks are less effective in environments with fluctuating temperatures, potentially affecting beer quality.
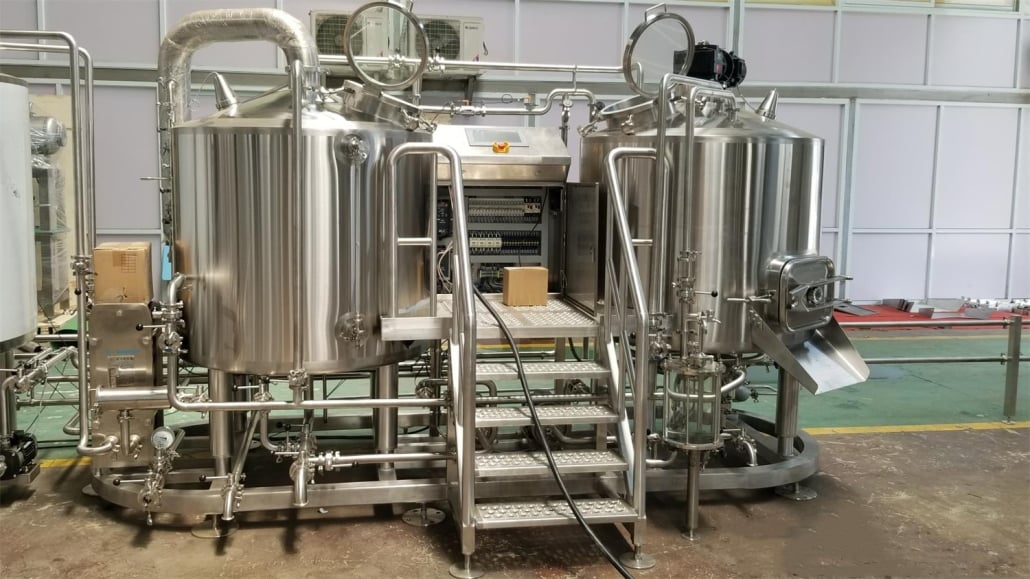
FAQ
Question | Answer |
---|---|
What is the purpose of a bright beer tank? | Bright beer tanks are used for the final clarification, carbonation, and maturation of beer before packaging. |
Can I use a bright beer tank for all beer styles? | Yes, BBTs are versatile and can be used for a wide range of beer styles, from lagers to ales. |
How do I choose the right size for a bright beer tank? | Consider your brewery’s production capacity and space availability when choosing the tank size. |
Do I need a jacketed or non-jacketed bright beer tank? | Jacketed tanks are preferred for precise temperature control, while non-jacketed tanks are more budget-friendly. |
What maintenance is required for bright beer tanks? | Regular CIP cleaning, pressure checks, and inspections are essential to maintain the tank’s performance and longevity. |
Conclusion
Bright beer tanks are a pivotal part of the brewing process, offering the final touch in producing a high-quality, well-conditioned beer. Whether you’re setting up a new brewery or expanding your operations, understanding the intricacies of BBTs—from equipment options and suppliers to installation and maintenance—will help you make informed decisions that enhance your brewing process. With this comprehensive guide, you’re well-equipped to navigate the world of bright beer tanks, ensuring your beer reaches its full potential in flavor, clarity, and carbonation.
Share this entry
Interested in learning more about Brewing Systems including additional details and pricing information? Please use the form below to contact us!
YOLONG BREWERY EQUIPMENT FAQS
- Commercial Brewery / Craft Brewery / Microbrewery / Nanobrewery
- What is The Difference Between Craft Beer and Industrial Beer?
- The Bespoke Differences In Custom Brewing Systems
- Everything You Need to Know About Kettle Souring
- How to Choose Brewing Equipment for Your business?
- How To Choose The-Best Partner To Build Your Commercial Microbrewing System?
- Two Detection Sensors That You Need To Use In Your Brewhouse System
- Remote Control Applications in Brewing Equipment/How does it work?
- How To Clean Your Brand New Brewery Tanks?