The Ultimate Guide to Brewery Tanks
Overview of Brewery Tanks
When it comes to brewing beer, the tanks you use are the heart of your operation. Whether you’re a seasoned brewmaster or just starting out, understanding the ins and outs of brewery tanks is essential. From fermenting your brew to conditioning it, these tanks play a crucial role in the final product. But what exactly are brewery tanks, and how do they fit into the brewing process?
Types of Brewery Tanks
Brewery tanks come in various shapes and sizes, each designed for a specific purpose in the brewing process. Here’s a detailed look at the primary types of brewery tanks:
Fermentation Tanks
Fermentation tanks are where the magic happens. These tanks allow yeast to convert sugars into alcohol, creating beer. They come in several forms, including conical fermenters, which are highly favored for their ease of use and efficiency.
Bright Beer Tanks
Bright beer tanks, also known as conditioning tanks, are used to age, clarify, and carbonate the beer before packaging. They help in achieving the perfect clarity and flavor balance.
Mash Tuns
Mash tuns are essential for the mashing process, where milled grains are mixed with hot water to convert starches into fermentable sugars. The quality of this tank can significantly affect the efficiency of the sugar extraction.
Lauter Tuns
Lauter tuns are used to separate the wort (the liquid extracted from the mashing process) from the spent grain. They are designed to allow for efficient wort collection and filtration.
Hot Liquor Tanks
Hot liquor tanks store and heat water needed for various stages of the brewing process, including mashing and sparging. They ensure a consistent water temperature, crucial for maintaining beer quality.
Cold Liquor Tanks
Cold liquor tanks store chilled water used to cool down the wort after boiling. This step is essential to halt the brewing process and prepare the wort for fermentation.
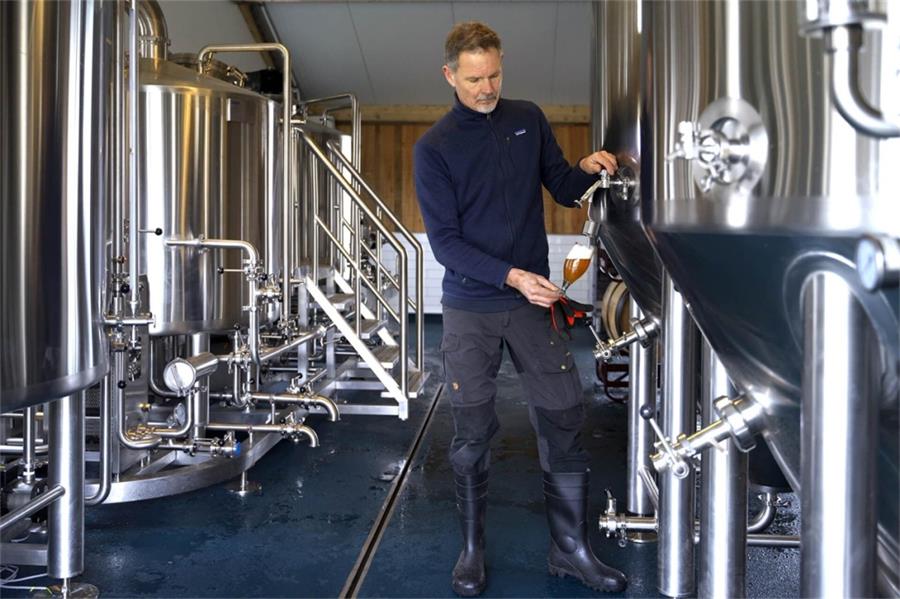
Types of Brewery Tanks and Their Uses
Type of Tank | Primary Use | Key Features |
---|---|---|
Fermentation Tanks | Fermenting wort into beer | Conical shape, temperature control |
Bright Beer Tanks | Conditioning, clarifying, and carbonating beer | Pressure-rated, often with carbonation ports |
Mash Tuns | Mixing milled grains with hot water to extract sugars | Insulated, false bottom for drainage |
Lauter Tuns | Separating wort from spent grain | Slotted plates for filtration |
Hot Liquor Tanks | Heating and storing brewing water | Temperature control, insulated |
Cold Liquor Tanks | Storing and cooling water | Temperature control, chilled |
The Brewing Process: A Step-by-Step Guide
Understanding the brewing process is crucial for selecting the right equipment. Here’s a breakdown of the steps involved:
Milling
The process starts with milling the grains to expose their starchy insides. This is typically done with a grain mill.
Mashing
Milled grains are mixed with hot water in the mash tun to convert starches into fermentable sugars.
Lautering
The mash is transferred to the lauter tun where the wort is separated from the spent grains.
Boiling
The wort is boiled and hops are added for bitterness, flavor, and aroma.
Cooling
The hot wort is cooled using a heat exchanger and cold liquor tank to a temperature suitable for fermentation.
Fermentation
The cooled wort is transferred to fermentation tanks where yeast is added to ferment the sugars into alcohol and carbon dioxide.
Conditioning
After fermentation, the beer is moved to bright beer tanks for aging, clarifying, and carbonation.
Packaging
Finally, the beer is packaged into bottles, cans, or kegs for distribution.
The Brewing Process
Step | Description | Key Equipment |
---|---|---|
Milling | Crushing grains to expose starches | Grain mill |
Mashing | Mixing crushed grains with hot water to extract sugars | Mash tun |
Lautering | Separating the liquid wort from spent grains | Lauter tun |
Boiling | Boiling wort and adding hops for flavor and preservation | Brew kettle |
Cooling | Rapidly cooling the wort to fermentation temperature | Heat exchanger, cold liquor tank |
Fermentation | Fermenting the cooled wort into beer with yeast | Fermentation tanks |
Conditioning | Aging, clarifying, and carbonating the beer | Bright beer tanks |
Packaging | Filling bottles, cans, or kegs with finished beer | Bottling line, canning line, kegs |
Capacity, Space, Design, and Layout Customization
Selecting the right brewery tank involves considering several factors like capacity, space, design, and customization options. Here’s a closer look at these aspects:
Capacity
The capacity of your tanks will determine the volume of beer you can produce. It ranges from small-scale systems for craft breweries to large tanks for commercial production.
Space and Layout
Efficient use of space is crucial. Tanks should be placed in a manner that allows for smooth workflow and easy access for maintenance.
Design
Tank design can affect everything from ease of cleaning to thermal efficiency. Conical fermenters, for example, are designed to facilitate the removal of yeast and sediment.
Customization
Many manufacturers offer customization options to fit the specific needs of your brewery, from adding extra ports to selecting specific materials.
Capacity, Space, Design, and Layout
Factor | Considerations |
---|---|
Capacity | Volume of beer production, scalability |
Space | Brewery size, efficient layout, ease of access |
Design | Ease of cleaning, thermal efficiency, conical versus cylindrical shapes |
Customization | Additional ports, material selection, bespoke design features |
Suppliers and Price Range
Choosing the right supplier is essential for getting high-quality tanks at a fair price. Here’s an overview of some top suppliers and the typical price ranges:
Price Range
The price of brewery tanks can vary widely based on size, material, and customization. Here’s a general breakdown:
- Small Tanks (1-10 BBL): $2,000 – $10,000
- Medium Tanks (10-50 BBL): $10,000 – $50,000
- Large Tanks (50+ BBL): $50,000 and up
Suppliers and Price Range
Supplier | Specialty | Price Range |
---|---|---|
Supplier A | High-quality stainless steel, customization | $5,000 – $60,000 |
Supplier B | Affordable, durable tanks | $2,000 – $30,000 |
Supplier C | Advanced technology, automation | $10,000 – $100,000 |
Installation, Operation, and Maintenance
Installation
Proper installation is key to ensuring your brewery tanks function correctly and efficiently. This often involves professional setup to handle plumbing, electrical work, and calibration.
Operation
Operating brewery tanks requires understanding their controls and monitoring systems. This includes temperature control, pressure monitoring, and regular sampling to check fermentation progress.
Maintenance
Regular maintenance is crucial for longevity and efficiency. This includes cleaning, sanitizing, inspecting for wear and tear, and servicing any moving parts.
Installation, Operation, and Maintenance
Aspect | Details |
---|---|
Installation | Professional setup, plumbing, electrical work, calibration |
Operation | Temperature control, pressure monitoring, sampling |
Maintenance | Cleaning, sanitizing, inspecting, servicing moving parts |
Choosing the Right Supplier
Selecting the right supplier for your brewery tanks can make or break your brewing process. Here’s a guide on what to consider:
Reputation
Look for suppliers with a strong reputation for quality and reliability. Reviews and testimonials can provide valuable insights.
Customization Options
Ensure the supplier offers customization to meet your specific brewing needs.
Support and Service
Good suppliers offer excellent after-sales support and service. This includes installation help, maintenance guidance, and prompt response to any issues.
Cost
While cost is a significant factor, it shouldn’t be the only one. Balance the price with the quality and features offered.
Choosing a Supplier
Factor | Considerations |
---|---|
Reputation | Reviews, testimonials, industry standing |
Customization Options | Availability of bespoke features |
Support and Service | Installation help, maintenance guidance, issue resolution |
Cost | Balance between price and quality |
Comparing Pros and Cons
When selecting brewery tanks, it’s important to weigh the pros and cons of different options. Here’s a comparison:
Stainless Steel Tanks
Advantages
- Durability and longevity
- Easy to clean and sanitize
- Resistant to corrosion
Disadvantages
- Higher initial cost
- Heavier, requiring stronger support structures
Plastic Tanks
Advantages
- Lower cost
- Lightweight and easy to move
Disadvantages
- Less durable and prone to scratches
- Potential for chemical leaching
Pros and Cons of Different Tank Materials
Material | Advantages | Disadvantages |
---|---|---|
Stainless Steel | Durable, easy to clean, corrosion-resistant | Higher cost, heavier |
Plastic | Lower cost, lightweight | Less durable, potential for chemical leaching |
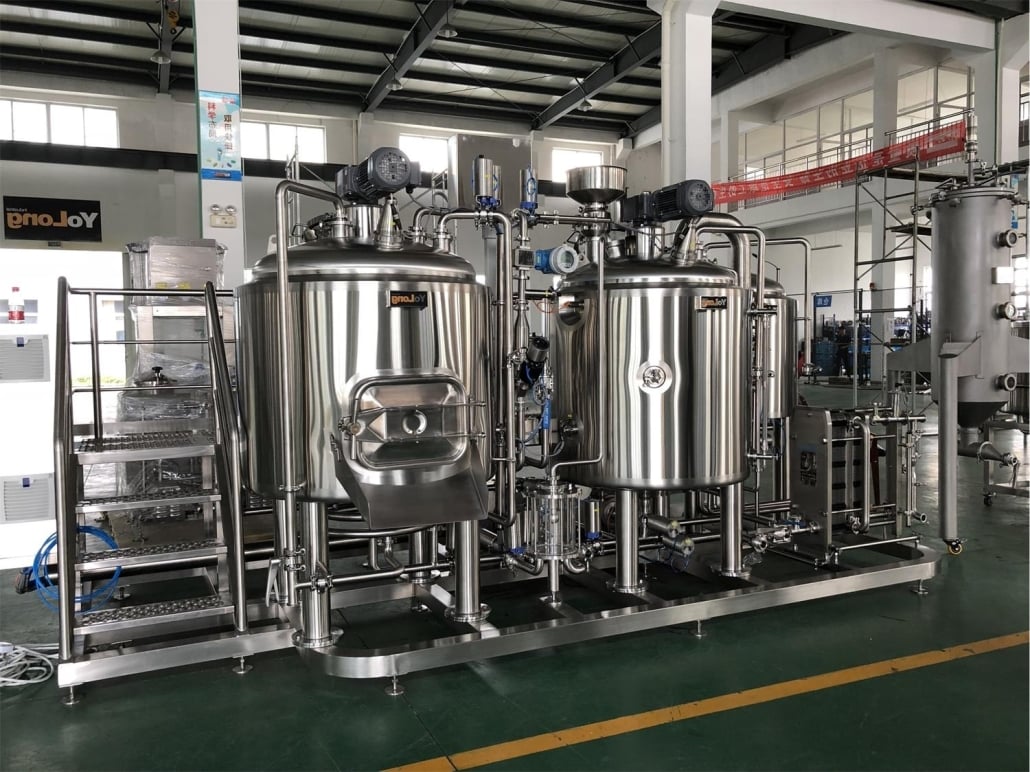
FAQ
What is the average lifespan of a brewery tank?
The average lifespan of a brewery tank can vary depending on the material and maintenance but typically ranges from 10 to 30 years for stainless steel tanks.
How often should brewery tanks be cleaned?
Brewery tanks should be cleaned after every use to prevent contamination and maintain beer quality. Regular deep cleaning and sanitization are also recommended.
Can I use plastic tanks for fermentation?
While plastic tanks can be used for fermentation, they are generally less durable and more prone to contamination compared to stainless steel tanks.
What is the average lifespan of a brewery tank?
10 to 30 years for stainless steel tanks
How often should brewery tanks be cleaned?
After every use, with regular deep cleaning and sanitization
Can I use plastic tanks for fermentation?
Yes, but they are less durable and more prone to contamination.
Share this entry
Interested in learning more about Brewing Systems including additional details and pricing information? Please use the form below to contact us!
YOLONG BREWERY EQUIPMENT FAQS
- Commercial Brewery / Craft Brewery / Microbrewery / Nanobrewery
- What is The Difference Between Craft Beer and Industrial Beer?
- The Bespoke Differences In Custom Brewing Systems
- Everything You Need to Know About Kettle Souring
- How to Choose Brewing Equipment for Your business?
- How To Choose The-Best Partner To Build Your Commercial Microbrewing System?
- Two Detection Sensors That You Need To Use In Your Brewhouse System
- Remote Control Applications in Brewing Equipment/How does it work?
- How To Clean Your Brand New Brewery Tanks?