Brewery Fermenter Tanks
Craft brewing has become a booming industry, where the fermentation process plays a key role in brewing quality beer. One critical piece of equipment in any brewery is the brewery fermenter tank. These tanks are where the magic of fermentation happens—turning wort into beer. If you’re looking to understand brewery fermenter tanks, including types, equipment, capacities, processes, and the nitty-gritty details, you’ve come to the right place.
This guide will walk you through the essentials of brewery fermenter tanks, offering a deep dive into equipment types, design, operation, price ranges, and how to select the right supplier. You’ll get a comprehensive look at every aspect, from the brewing process to maintenance.
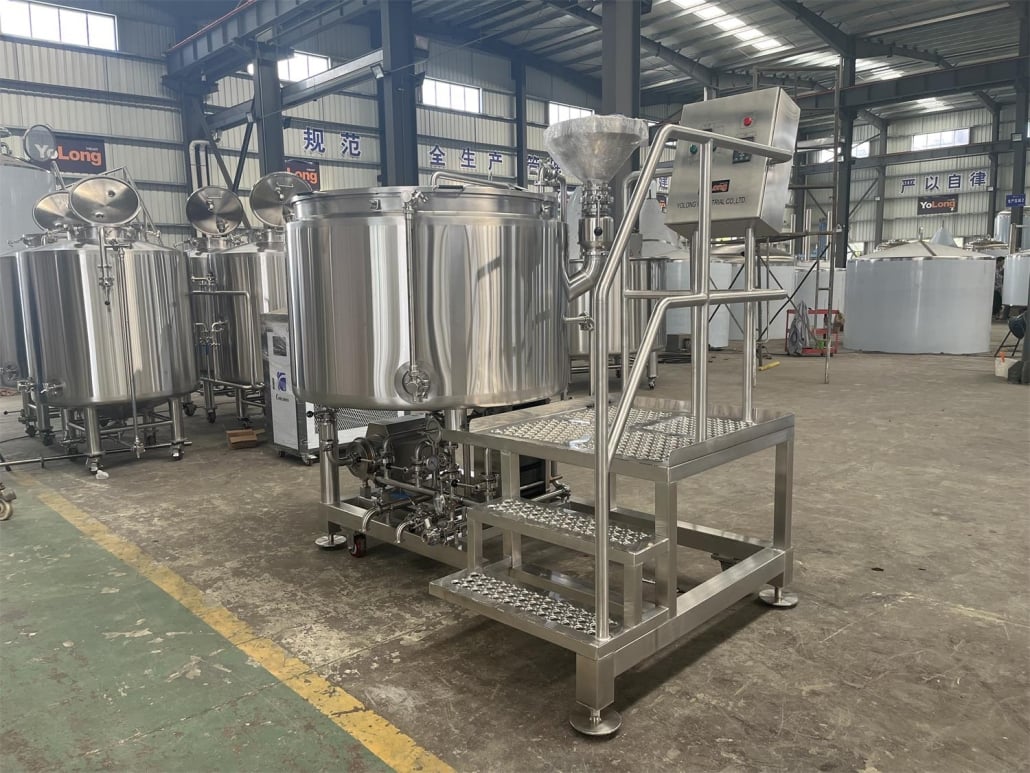
Overview of Brewery Fermenter Tanks
Fermentation is the heart of the brewing process. It’s during fermentation that yeast consumes sugars from the wort (unfermented beer) to produce alcohol and CO2, giving the beer its unique flavor and characteristics. This fermentation happens inside specially designed fermenter tanks, which are built to ensure optimal conditions for yeast activity. Brewery fermenter tanks come in various types, capacities, and designs, tailored to the size of the brewery and the specific needs of the brewer.
Brewery Fermenter Tanks
When it comes to brewery fermenter tanks, there’s more to consider than just a shiny stainless steel container. The equipment guide below breaks down the key features and types of fermenter tanks:
Feature | Description |
---|---|
Material | Most brewery fermenter tanks are made from stainless steel, known for its durability and resistance to corrosion. High-grade 304 stainless steel is the most commonly used. |
Cooling System | Fermenters often come equipped with glycol jackets or external cooling systems to maintain ideal fermentation temperatures. |
Size/Capacity | Available in a wide range of capacities, from small-scale 1-barrel systems to massive 100-barrel commercial tanks. |
Pressure Rating | Some fermenter tanks are designed to handle pressure (for force carbonation) while others are built for standard atmospheric pressure. |
Accessories | Standard accessories include thermometers, pressure relief valves, sampling valves, and CIP (clean-in-place) systems. |
Shape | Cylindroconical fermenters are the most common, allowing for efficient yeast separation. Flat-bottom fermenters are also available but less popular in modern breweries. |
Manways | A top or side manway offers access for cleaning, yeast collection, or inspecting the fermentation process. |
Insulation | Fermenters may have insulation to help regulate internal temperature, reducing energy costs during fermentation. |
Customizability | Many tanks can be customized to fit the specific space, brewing process, or capacity needs of a brewery. |
The choice of fermenter tank can significantly affect the brewing process, so it’s important to choose wisely depending on the size of your brewery and the type of beer you’re making.
Types of Brewery Fermenter Tanks
Brewery fermenter tanks are not one-size-fits-all. There are different types of fermenters, each with specific use cases:
Type of Fermenter Tank | Description |
---|---|
Open Fermenters | These tanks are open at the top, allowing for easy access to the wort during fermentation. Open fermenters are rare in modern breweries but are sometimes used for specialty ales. |
Cylindroconical Fermenters | These tanks have a cone-shaped bottom, making it easier to collect yeast. They are the industry standard due to their efficiency and ease of cleaning. |
Unitanks | Unitanks are versatile fermenters that can handle both primary fermentation and conditioning in the same tank, making them a space-efficient option. |
Horizontal Fermenters | Often used for lagering, horizontal fermenters allow beer to mature slowly, offering a smooth, well-rounded flavor. |
Flat-Bottom Fermenters | These tanks are less common but are sometimes used for fermenting beers that don’t require yeast collection. |
The Brewing Process in Brewery Fermenter Tanks
The brewing process revolves around the fermenter tank, where the yeast transforms wort into beer. Here’s a step-by-step breakdown of how the process works:
- Wort Transfer: After boiling, the wort is transferred into the fermenter tank. It is crucial that the wort is cooled to the appropriate temperature before being introduced to yeast.
- Yeast Addition: Yeast is pitched (added) into the cooled wort. This is where fermentation begins.
- Fermentation: The yeast consumes sugars in the wort and converts them into alcohol and CO2, creating the desired beer characteristics. The fermentation process can take anywhere from a few days to several weeks, depending on the type of beer.
- Monitoring: Throughout fermentation, brewers monitor the temperature, pressure, and yeast activity to ensure everything is running smoothly.
- Conditioning: After fermentation, some beers are left to condition in the same tank (if using a unitank), while others may be transferred to another vessel for aging and clarification.
This process can vary depending on the beer style and the specific equipment used.
Capacity, Space, Design, and Customization Options for Brewery Fermenter Tanks
Brewery fermenter tanks come in a wide range of sizes and designs, and customization options abound. Here’s a breakdown of the key factors to consider when choosing your tanks:
Factor | Details |
---|---|
Capacity | Ranges from small-scale 1-barrel fermenters for microbreweries to large 100-barrel tanks for commercial operations. Choose a capacity that matches your production needs. |
Space | Measure your available floor space carefully. Tanks come in various shapes (cylindrical, conical) that fit different footprints. |
Design | Cylindroconical tanks are preferred for their efficient design. Customizable features include the number of ports, insulation levels, and cooling systems. |
Customization | Many manufacturers offer custom-built tanks that can be modified for size, material, and functionality based on your brewery’s needs. |
Suppliers and Price Ranges for Brewery Fermenter Tanks
Choosing a reliable supplier is critical for obtaining high-quality fermenter tanks. Below is a table listing well-known suppliers along with their estimated price ranges:
Supplier | Price Range (Per Barrel) | Customization Options | Region |
---|---|---|---|
Blichmann Engineering | $1,000 – $1,500 | Yes | United States |
Stout Tanks and Kettles | $800 – $1,200 | Yes | United States |
Ss Brewtech | $1,200 – $1,600 | Yes | Global |
DEGONG Brewery Equipment | $600 – $1,100 | Yes | China |
Prettech Machinery | $500 – $1,200 | Yes | China |
Premier Stainless Systems | $900 – $1,400 | Yes | United States |
Price can vary significantly depending on the size, design, and level of customization. It’s essential to research and compare suppliers to get the best value for your investment.
Installation, Operation, and Maintenance of Brewery Fermenter Tanks
Installing and maintaining a brewery fermenter tank requires attention to detail to ensure smooth operation and longevity. Here’s what you need to know:
Aspect | Details |
---|---|
Installation | Tanks need to be installed by professionals to ensure proper leveling, plumbing, and connectivity with cooling systems and piping. |
Operation | Operating fermenters involves regular monitoring of temperature, pressure, and yeast health. Training staff on tank operation is essential. |
Maintenance | Tanks need regular cleaning using a CIP (clean-in-place) system to avoid contamination. Inspecting gaskets, seals, and valves is important to avoid leaks. |
Proper maintenance not only prolongs the life of the tank but also ensures the quality of the beer produced.
How to Choose a Brewery Fermenter Tank Supplier
Choosing the right supplier can make or break your brewing operation. Here’s a table to guide you through selecting a fermenter tank supplier:
Criteria | What to Look For |
---|---|
Reputation | Look for reviews and testimonials from other breweries to gauge supplier reliability. |
Quality | Check the materials used, especially the quality of stainless steel (304 vs 316) and the craftsmanship of the tank. |
Customization | Ensure the supplier offers customization options that align with your brewery’s specific needs. |
Delivery Time | Some custom tanks may take months to manufacture and deliver, so confirm the expected timeline before ordering. |
Customer Support | A responsive and helpful customer support team can make a big difference, especially if you encounter issues during installation or operation. |
Warranty | Ensure the tanks come with a comprehensive warranty that covers defects in manufacturing or materials. |
Pros and Cons of Different Brewery Fermenter Tank Options
Understanding the advantages and limitations of various fermenter tanks will help you make an informed decision. Here’s a comparison:
Tank Type | Advantages | Limitations |
---|---|---|
Cylindroconical Fermenters | Efficient yeast separation, easy to clean, space-saving design | Higher upfront cost |
Unitanks | Versatile, allows for both fermentation and conditioning in one tank | Can be expensive, more complex operation |
Open Fermenters | Traditional, great for specialty beers like ales | Risk of contamination, less control over fermentation |
Horizontal Fermenters | Ideal for lagering, promotes slow and even fermentation | Takes up more floor space |
Flat-Bottom Fermenters | Simple design, lower cost | Not ideal for yeast collection or certain beer styles |
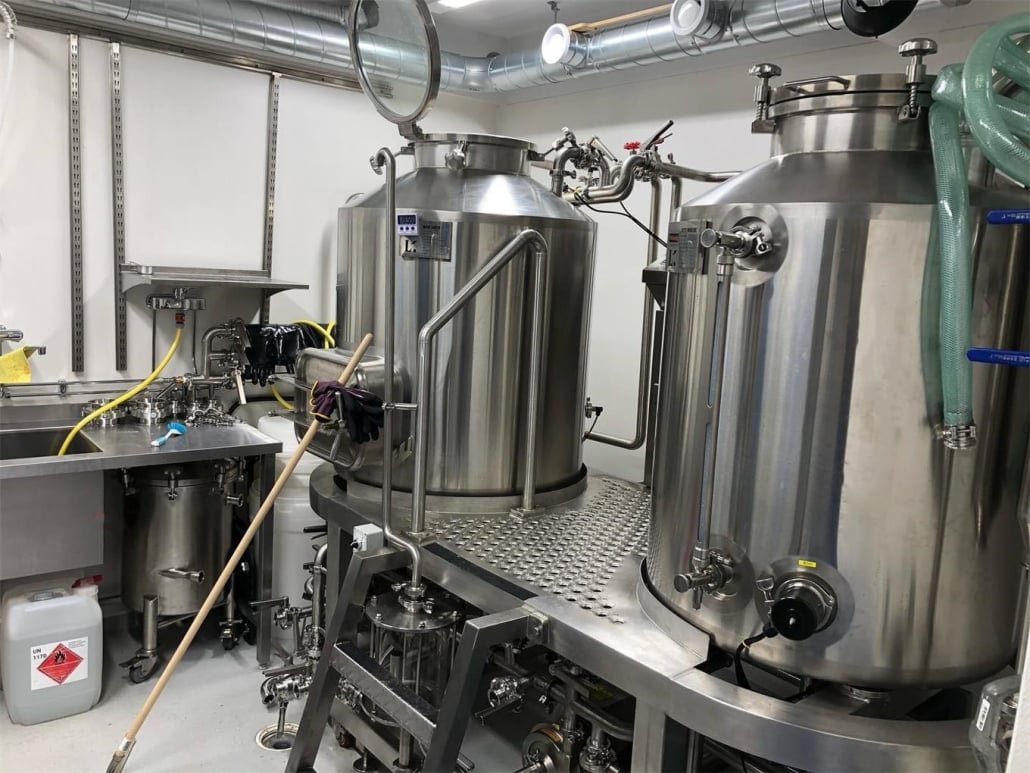
FAQ
Question | Answer |
---|---|
What size fermenter tank do I need? | It depends on the scale of your production. Microbreweries may need small 1-5 barrel tanks, while commercial breweries often require 30-100 barrel tanks. |
How do I maintain a fermenter tank? | Regular cleaning using a CIP system, inspecting seals and valves, and monitoring the cooling system are essential for maintaining a fermenter tank. |
What is a Unitank? | A Unitank is a fermentation vessel that can handle both the fermentation and conditioning processes, reducing the need for separate tanks. |
How long does fermentation take in a brewery fermenter tank? | It depends on the beer style. Ales typically ferment in 3-7 days, while lagers may take several weeks to ferment and condition. |
Can I customize a brewery fermenter tank to fit my space? | Yes, many suppliers offer custom-built fermenter tanks that can be tailored to your specific space and production requirements. |
Conclusion
Choosing the right brewery fermenter tank is crucial for any brewery looking to produce high-quality beer efficiently. From understanding the different types of tanks and how they work to knowing what to look for in a supplier, this guide has covered all the essential details. Whether you’re starting a small microbrewery or expanding a large-scale commercial operation, the right fermenter tanks can make all the difference in the quality and consistency of your beer. Make sure to assess your brewery’s unique needs carefully and invest in the best equipment to support your brewing goals.
Share this entry
Interested in learning more about Brewing Systems including additional details and pricing information? Please use the form below to contact us!
YOLONG BREWERY EQUIPMENT FAQS
- Commercial Brewery / Craft Brewery / Microbrewery / Nanobrewery
- What is The Difference Between Craft Beer and Industrial Beer?
- The Bespoke Differences In Custom Brewing Systems
- Everything You Need to Know About Kettle Souring
- How to Choose Brewing Equipment for Your business?
- How To Choose The-Best Partner To Build Your Commercial Microbrewing System?
- Two Detection Sensors That You Need To Use In Your Brewhouse System
- Remote Control Applications in Brewing Equipment/How does it work?
- How To Clean Your Brand New Brewery Tanks?