Overview of Beer Fermenter Tanks
Beer fermenter tanks are the heart of any brewing operation, essential for turning wort into beer through fermentation. These tanks come in a range of sizes, designs, and materials, each suited to specific brewing needs and styles. From small home breweries to large commercial setups, understanding beer fermenter tanks—how they work, their types, features, and requirements—can make a big difference in brewing quality and efficiency. Whether you’re scaling up your brewery or just getting started, this guide covers everything you need to know about beer fermenter tanks in one comprehensive overview.
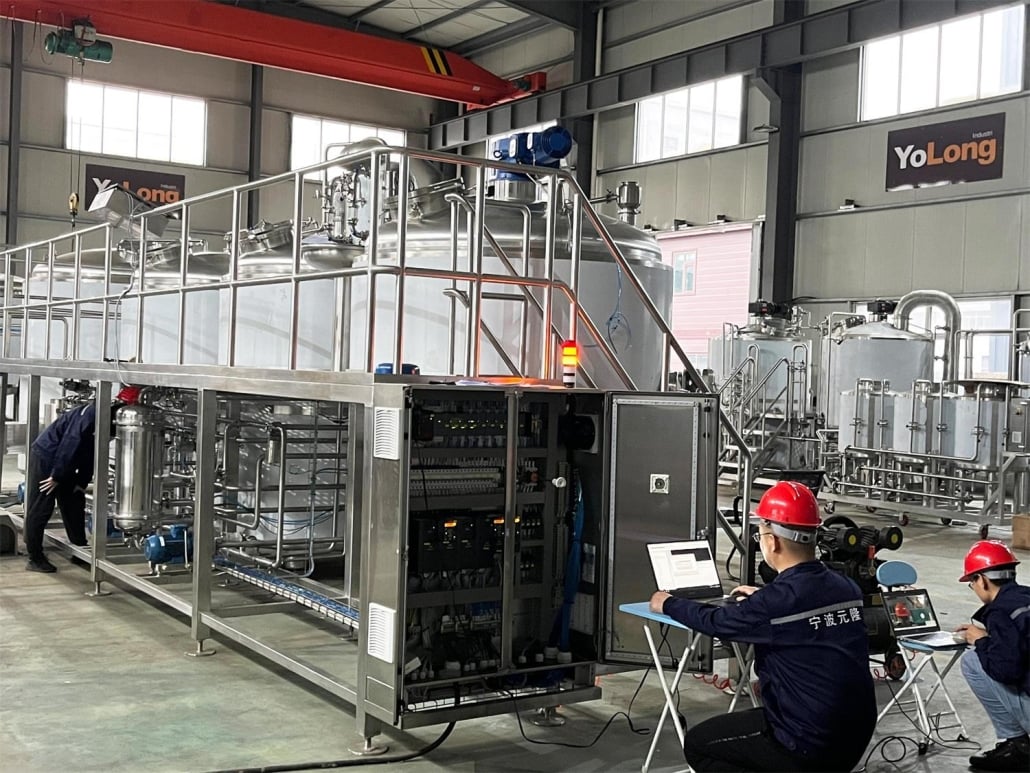
Equipment Guide to Beer Fermenter Tanks
Beer fermenter tanks are specialized containers that allow brewers to control the environment in which yeast ferments the wort into beer. This process includes managing factors like temperature, pressure, and oxygen exposure to produce the best possible flavor, aroma, and texture in the beer. Here’s a look at the types of fermenter tanks and what to consider when choosing one for your brewing needs.
Types of Beer Fermenter Tanks
Type of Tank | Description |
---|---|
Open Fermenters | Open fermenters are shallow tanks with an open top. Used primarily in traditional ale brewing, they allow more yeast contact with air, creating unique flavors. |
Closed Fermenters | These tanks have sealed tops and controlled environments, making them ideal for consistent brewing results and maintaining beer quality, especially for lagers. |
Unitanks | Combining fermentation and maturation in one vessel, unitanks are versatile and common in modern breweries for streamlined processes and space-saving benefits. |
Conical Fermenters | Conical tanks taper at the bottom, allowing easy separation of yeast and other sediments, which helps in clearer beer and faster yeast reuse cycles. |
Horizontal Tanks | Primarily used for lagering (long-term conditioning), horizontal tanks allow for more even cooling and have larger surface areas to volume ratios, enhancing clarity. |
Beer Brewing Process Using Fermenter Tanks
The brewing process is complex, with each stage impacting the beer’s final flavor profile. Fermenter tanks play a critical role in the fermentation and maturation phases. Here’s a breakdown of how beer fermenter tanks are used throughout the brewing process:
- Primary Fermentation: The wort is pumped into the fermenter tank, where yeast is added. Here, the yeast begins to break down the sugars, producing alcohol and CO₂.
- Secondary Fermentation: Once the primary fermentation is complete, some brewers transfer the beer to another tank for a secondary phase, which helps refine flavors and clarify the beer.
- Conditioning and Maturation: Beer is often left to mature in the fermenter, allowing any remaining flavors to meld and mellow. The maturation time varies based on the beer type and brewer’s preference.
- Clarification: In conical fermenters, yeast and sediment settle at the bottom, simplifying clarification and improving the final beer’s clarity.
Capacity, Design, and Customization of Beer Fermenter Tanks
Capacity | Ideal Space and Design | Customization Options |
---|---|---|
Small-Scale (1-10 BBL) | Ideal for small breweries, requires minimal floor space. | Optional customization includes valves, sight glasses, and sampling ports. |
Mid-Scale (10-50 BBL) | Common in mid-size breweries; generally requires more structured layout planning. | Customizable features for temperature control, automated pressure relief, and cleaning systems. |
Large-Scale (50+ BBL) | Used by large breweries; dedicated fermenting space required. | High-end options include custom tank designs, specialized cooling jackets, and automatic yeast recycling systems. |
Suppliers and Price Range of Beer Fermenter Tanks
Finding the right supplier and understanding the cost range of beer fermenter tanks can help brewers make an informed purchase decision. The prices vary significantly based on the size, materials, and specific features.
Supplier | Price Range (USD) | Key Features |
---|---|---|
SS Brewtech | $500 – $15,000 | Known for high-quality stainless steel tanks, suitable for home and small breweries. |
Blichmann Engineering | $800 – $18,000 | Offers customizable fermenter tanks with a focus on thermal control and durability. |
Speidel | $1,000 – $20,000 | Specializes in closed and conical fermenters with advanced aeration options. |
Craft Kettle | $10,000 – $50,000 | High-capacity options and versatile tank designs for medium to large breweries. |
Installation, Operation, and Maintenance of Beer Fermenter Tanks
For smooth operations and longevity of equipment, understanding the installation, operation, and maintenance requirements of beer fermenter tanks is crucial.
Aspect | Details |
---|---|
Installation | Requires dedicated space, correct setup of temperature controls, and alignment with other brewery equipment. |
Operation | Regular monitoring of temperature, pressure, and yeast activity. Ensuring proper cleaning before each use. |
Maintenance | Scheduled clean-in-place (CIP) cycles, periodic pressure and temperature checks, and preventative repairs. |
How to Choose the Right Beer Fermenter Tank Supplier
Choosing the right supplier goes beyond price; it’s about assessing product quality, support, and customization options.
Factors to Consider | Importance |
---|---|
Reputation and Reviews | Look for suppliers with a strong reputation for quality and reliable after-sales support. |
Customization Options | Consider suppliers who offer customizable options to meet your brewery’s specific requirements. |
Material Quality | High-grade stainless steel or copper is preferable for durability and low maintenance. |
Delivery and Installation | Suppliers offering seamless installation services can save time and potential setup errors. |
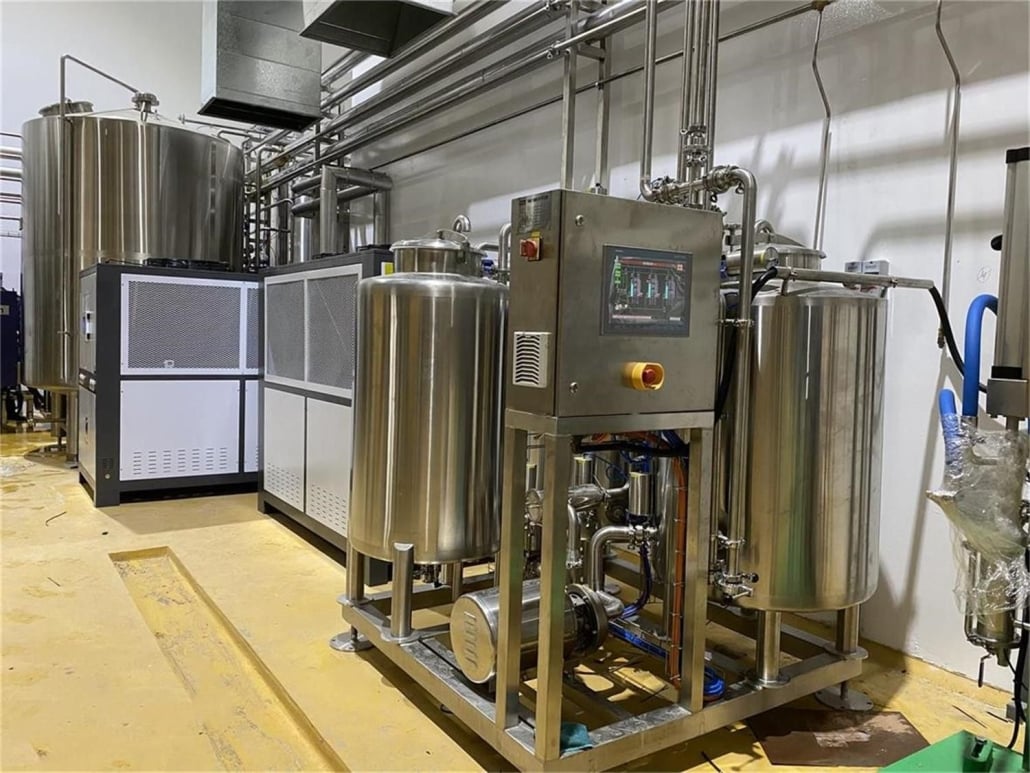
Advantages and Disadvantages of Beer Fermenter Tanks
Pros | Cons |
---|---|
Enhanced Quality Control | Higher Initial Investment |
Improved Efficiency and Productivity | Space Requirements |
Flexibility with Multiple Fermentation Stages | Complexity in Maintenance |
Increased Batch Consistency | Need for Skilled Operators |
FAQ
Question | Answer |
---|---|
What is the purpose of a fermenter tank? | Fermenter tanks allow brewers to control the environment for yeast fermentation, crucial for producing quality beer. |
How long does fermentation take in these tanks? | It depends on the beer type. Ales typically take 1-2 weeks, while lagers can take longer, up to 4-6 weeks for full maturation. |
Are conical fermenters better than open fermenters? | Conical fermenters are ideal for easy sediment removal and quicker cleanup, but open fermenters can add unique flavor profiles in traditional ales. |
Share this entry
Interested in learning more about Brewing Systems including additional details and pricing information? Please use the form below to contact us!
YOLONG BREWERY EQUIPMENT FAQS
- Commercial Brewery / Craft Brewery / Microbrewery / Nanobrewery
- What is The Difference Between Craft Beer and Industrial Beer?
- The Bespoke Differences In Custom Brewing Systems
- Everything You Need to Know About Kettle Souring
- How to Choose Brewing Equipment for Your business?
- How To Choose The-Best Partner To Build Your Commercial Microbrewing System?
- Two Detection Sensors That You Need To Use In Your Brewhouse System
- Remote Control Applications in Brewing Equipment/How does it work?
- How To Clean Your Brand New Brewery Tanks?