Beer Fermentation Tank
Overview of Beer Fermentation Tanks
Beer fermentation tanks are critical components in brewing systems, where the magic of transforming wort into beer occurs. This process relies on precision and quality equipment that can handle varying capacities, design configurations, and customization options, tailored to brewers’ needs. In this article, we’ll dive deep into the world of beer fermentation tanks—from equipment guides and types to essential maintenance practices, capacity considerations, and tips on selecting suppliers.
Beer Fermentation Equipment Guide
Beer fermentation tanks come in various sizes, materials, and design specifications. Choosing the right tank requires knowledge of materials, size, insulation, temperature control features, and more. The following sections will explore each of these aspects in detail to give a clearer picture of what’s best for both small-scale and large-scale brewing.
Material and Insulation
The material of a fermentation tank affects not only the durability and longevity of the tank but also the flavor profile of the beer. Stainless steel is the preferred choice in most commercial setups due to its resistance to corrosion, ease of cleaning, and excellent thermal conductivity.
- Stainless Steel: Durable, easy to clean, and non-reactive with beer ingredients, stainless steel is ideal for maintaining beer purity.
- Plastic or Glass Tanks: Often used in smaller, home-brewing setups, these options are affordable and functional but lack the industrial-grade quality that large-scale brewing demands.
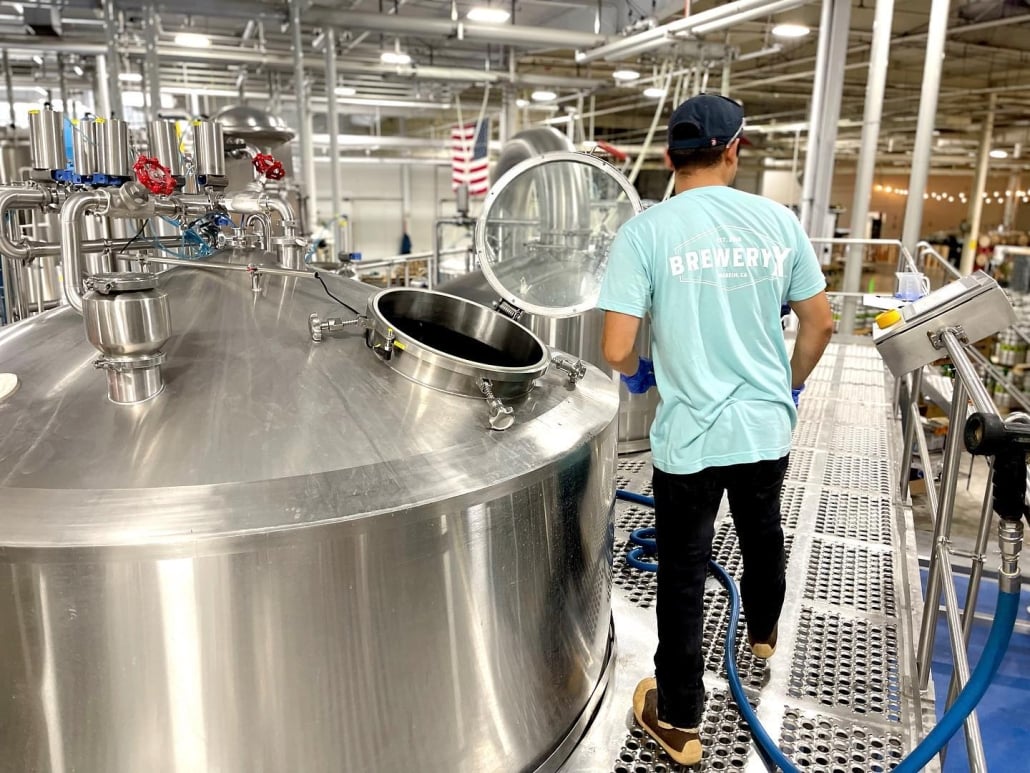
Types of Beer Fermentation Tanks
Tank Type | Description | Best For |
---|---|---|
Open Fermentation | Open tanks that allow for easy access to the beer and yeast but expose the brew to the air. | Traditional brews and unique flavors. |
Closed Fermentation | Fully enclosed tanks prevent exposure to the environment, reducing contamination risk. | Commercial breweries with high volumes. |
Unitanks | Combination tanks that handle fermentation and conditioning in the same vessel. | Breweries with limited space. |
Jacketed Tanks | Equipped with temperature control, they allow for precise fermentation temperature. | High-quality and temperature-sensitive brews. |
Each tank type brings unique qualities to the brewing process, affecting the flavor, aroma, and mouthfeel of the beer. For example, unitanks are popular in small breweries as they reduce the need for additional equipment, while jacketed tanks are essential for brewers focusing on temperature-sensitive lagers and ales.
The Beer Brewing Process with Fermentation Tanks
The brewing process can be simplified into several stages, but fermentation is where the raw wort is transformed into the flavorful beer we enjoy. Here’s a breakdown:
The Wort Preparation
Before fermentation, wort is created by mashing malted grains with hot water, followed by boiling with hops. This wort is then transferred to the fermentation tank to begin the process.
The Fermentation Phase
In the tank, yeast is added to the wort, and the fermentation process begins. Depending on the type of beer, this phase can last anywhere from several days to weeks. During this time, the yeast converts sugars into alcohol and carbon dioxide, creating beer’s distinct flavors and aromas.
Conditioning and Aging
After primary fermentation, beer may undergo secondary fermentation or conditioning, where it matures to achieve a smoother taste. Some brewers use separate conditioning tanks, while others opt for unitanks to handle both processes in one vessel.
Capacity, Space, Design, and Customization of Beer Fermentation Tanks
Specification | Details |
---|---|
Capacity | Tanks range from small 5-gallon sizes for home brewers to industrial-scale 100-barrel tanks. |
Space Requirements | Commercial tanks need larger spaces, typically in climate-controlled rooms. |
Design Features | Temperature control, pressure regulation, and specialized valves enhance functionality. |
Customization Options | Custom tank shapes, sizes, and configurations to fit unique brewing needs. |
The ideal setup depends on the brewer’s production scale, space availability, and specific brewing goals. For instance, large breweries need tanks with high-capacity outputs, while craft breweries may prioritize customizable designs for experimenting with flavors and fermentation techniques.
Leading Suppliers and Price Ranges
Supplier Name | Price Range (USD) | Specializations |
---|---|---|
Blichmann Engineering | $1,500 – $10,000 | Known for high-quality, mid-range tanks. |
Ss Brewtech | $500 – $7,000 | Affordable, versatile tanks for small brewers. |
China Brew | $2,000 – $50,000+ | Large-scale, customizable fermentation systems. |
Brewery Equipment Co. | $3,000 – $25,000 | Focuses on jacketed and unitank designs. |
These suppliers offer tanks with various features, from budget-friendly options to high-end units with advanced temperature control and durability.
Installation, Operation, and Maintenance Guide
Proper setup and maintenance are crucial to ensure that the fermentation tanks operate smoothly. Let’s break down each of these aspects:
Installation
- Space Planning: Ensure sufficient space around the tanks for cleaning, access, and ventilation.
- Temperature Control: If using a jacketed tank, connect it to a reliable glycol chiller.
- Safety Measures: Install pressure relief valves and ensure proper ventilation.
Operation
Maintaining a steady fermentation temperature and monitoring yeast activity are key. Fermentation tanks often come with temperature gauges and sampling ports, making it easier to check progress.
Maintenance
Regular cleaning with a CIP (Clean in Place) system helps prevent contamination. Using appropriate sanitizers and monitoring the tank for signs of wear can extend its life significantly.
How to Choose the Right Supplier
When selecting a supplier, consider factors like product range, pricing, customization options, and customer support. Here’s a breakdown:
Factor | Importance |
---|---|
Product Quality | Look for durable, stainless steel tanks to avoid frequent replacements. |
Customization | Some suppliers offer custom designs—ideal for unique brewing styles. |
Pricing and Budget | Compare price ranges across suppliers to fit within your budget without compromising quality. |
Customer Support | Responsive customer service ensures smooth installation and maintenance. |
Pros and Cons of Various Beer Fermentation Tank Options
Feature | Advantages | Limitations |
---|---|---|
Open Fermentation Tanks | Unique flavors, easy to clean and access. | Higher risk of contamination. |
Closed Fermentation Tanks | Reduces contamination risk, suitable for high volume. | Harder to monitor during fermentation. |
Unitanks | Saves space, dual-purpose. | Generally more expensive. |
Jacketed Tanks | Ideal for temperature-sensitive fermentation. | Higher energy requirements. |
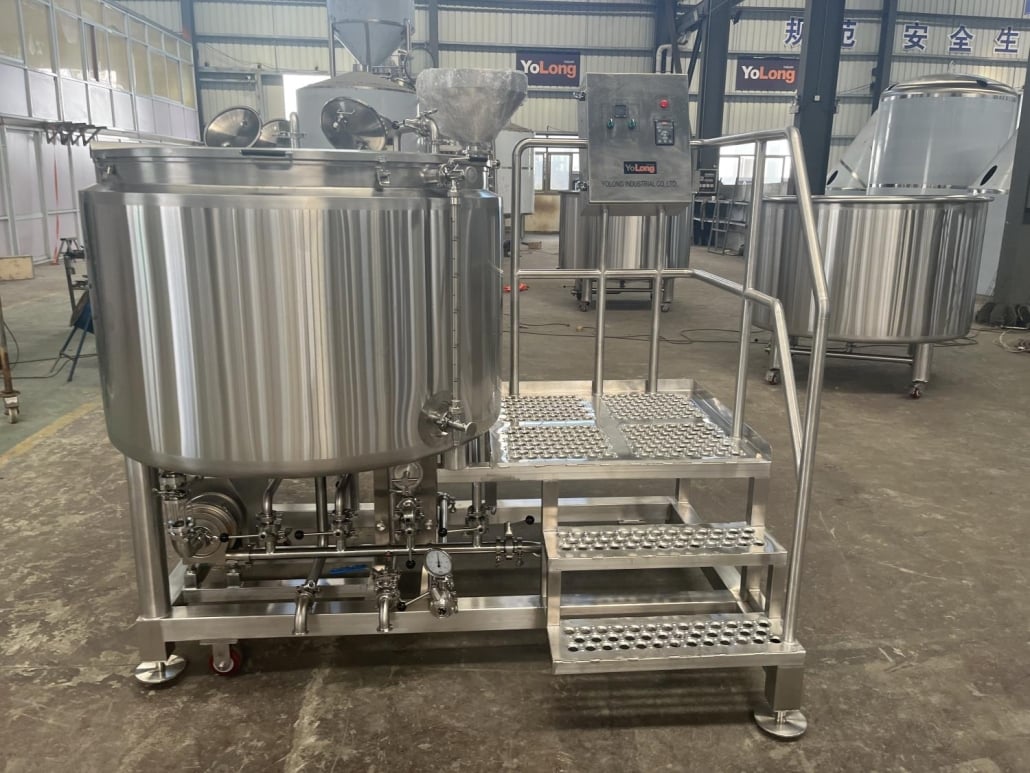
FAQs
Question | Answer |
---|---|
What size fermentation tank do I need? | This depends on production scale; home brewers might use 5-gallon tanks, while breweries may need 100+ barrels. |
Can I use a single tank for fermentation and conditioning? | Yes, unitanks are designed to handle both processes in one vessel. |
How often should I clean my fermentation tank? | Tanks should be cleaned thoroughly after each batch using CIP systems and sanitizers. |
This article would continue to expand on each section, exploring more in-depth details, comparisons, and tips. I can proceed to build the entire article step-by-step or elaborate on any specific sections first based on your preferences. Let me know how you’d like to proceed!
Share this entry
Interested in learning more about Brewing Systems including additional details and pricing information? Please use the form below to contact us!
YOLONG BREWERY EQUIPMENT FAQS
- Commercial Brewery / Craft Brewery / Microbrewery / Nanobrewery
- What is The Difference Between Craft Beer and Industrial Beer?
- The Bespoke Differences In Custom Brewing Systems
- Everything You Need to Know About Kettle Souring
- How to Choose Brewing Equipment for Your business?
- How To Choose The-Best Partner To Build Your Commercial Microbrewing System?
- Two Detection Sensors That You Need To Use In Your Brewhouse System
- Remote Control Applications in Brewing Equipment/How does it work?
- How To Clean Your Brand New Brewery Tanks?