Choosing the Best Beer Canning Equipment for Your Brewery
Overview of Beer Canning Equipment
Crafting the perfect beer goes beyond brewing—it’s about presentation and preservation. Enter beer canning equipment: the unsung hero of modern breweries. Whether you’re a craft brewery owner or a homebrewing enthusiast ready to scale up, understanding the nuances of canning equipment can be the game-changer.
This guide unpacks everything from equipment types and features to maintenance tips and industry trends, ensuring you’re fully equipped to make the right choice.
What Is Beer Canning Equipment?
Beer canning equipment refers to the machinery designed to fill, seal, and package beer into cans. This equipment ensures that beer is preserved in airtight, lightweight, and transport-friendly containers. Over the years, canning has emerged as a superior packaging method due to its cost-effectiveness, sustainability, and ability to block out harmful light and oxygen.
Canning equipment ranges from small-scale manual machines perfect for budding brewers to high-speed automated systems tailored for large-scale operations. Regardless of size, the goal is the same: maintain the beer’s quality while enhancing its shelf appeal.
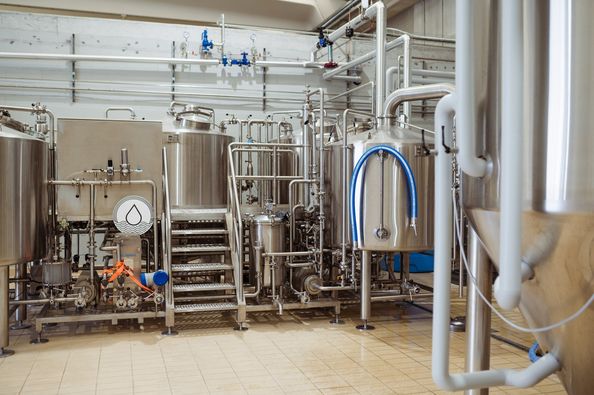
Types of Beer Canning Equipment
Understanding the various types of beer canning equipment can help tailor the perfect solution for your brewery. Let’s break it down:
1. Manual Beer Canning Machines
Ideal for hobbyists or small-scale brewers, manual systems require human operation to fill and seal cans. These machines are cost-effective but slower, making them perfect for limited production runs.
2. Semi-Automatic Canning Systems
A step up from manual systems, semi-automatic machines automate certain processes like sealing while still requiring some manual oversight. They strike a balance between affordability and efficiency.
3. Fully Automatic Beer Canning Machines
These are the big guns of the industry, designed for high-speed operations. Fully automated systems handle everything—from filling and sealing to labeling and packaging. They are a significant investment but indispensable for larger breweries.
4. Mobile Beer Canning Units
For breweries on the go, mobile canning units bring the equipment to your location. They’re perfect for small to medium-sized breweries looking to scale without committing to in-house machinery.
Key Features to Look for in a Beer Canning Machine
Investing in beer canning equipment requires careful consideration. Here are the must-have features to look for:
1. Production Speed
Consider your brewery’s output. Small-scale machines might process 10-15 cans per minute, while industrial systems can handle up to 500 cans per minute.
2. Can Size Versatility
Look for equipment that accommodates various can sizes, from sleek 250ml options to classic 16-ounce cans.
3. Oxygen Reduction
Keeping oxygen out is crucial to preserving beer’s freshness. Choose machines with advanced CO2 purging systems.
4. Compact Design
Space is often a premium in breweries. Opt for equipment with a compact footprint without compromising on functionality.
5. Durability and Build Quality
High-quality stainless steel components resist corrosion and ensure longevity.
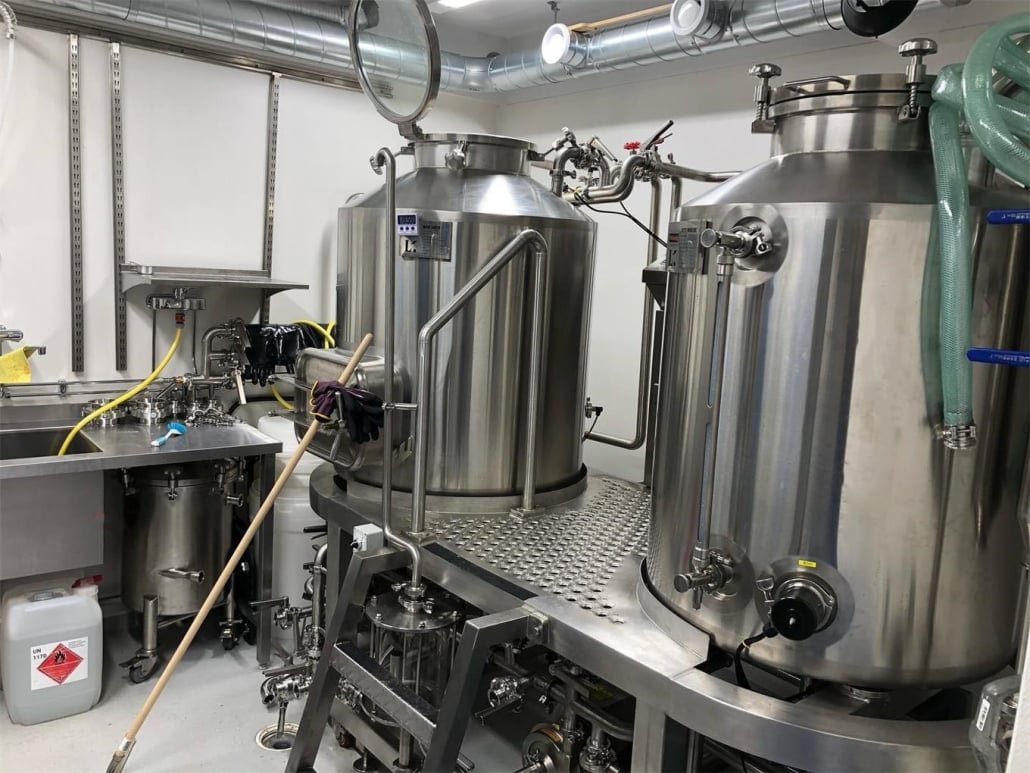
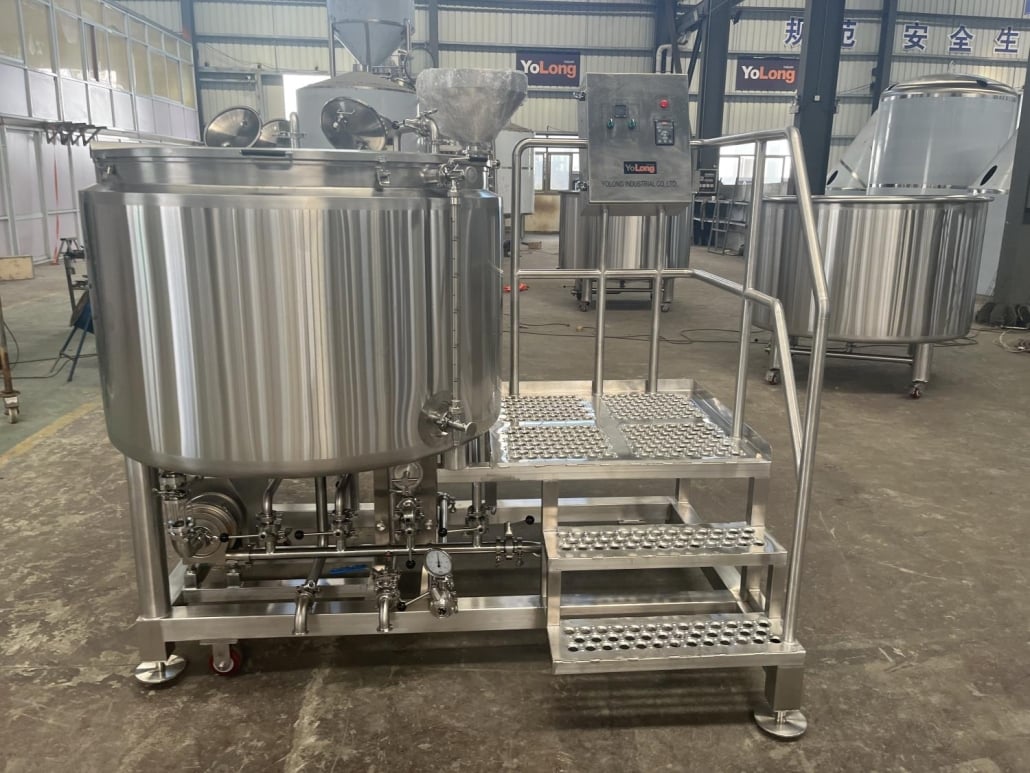
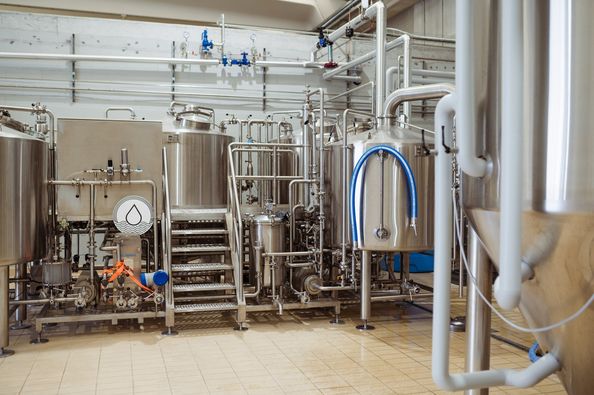
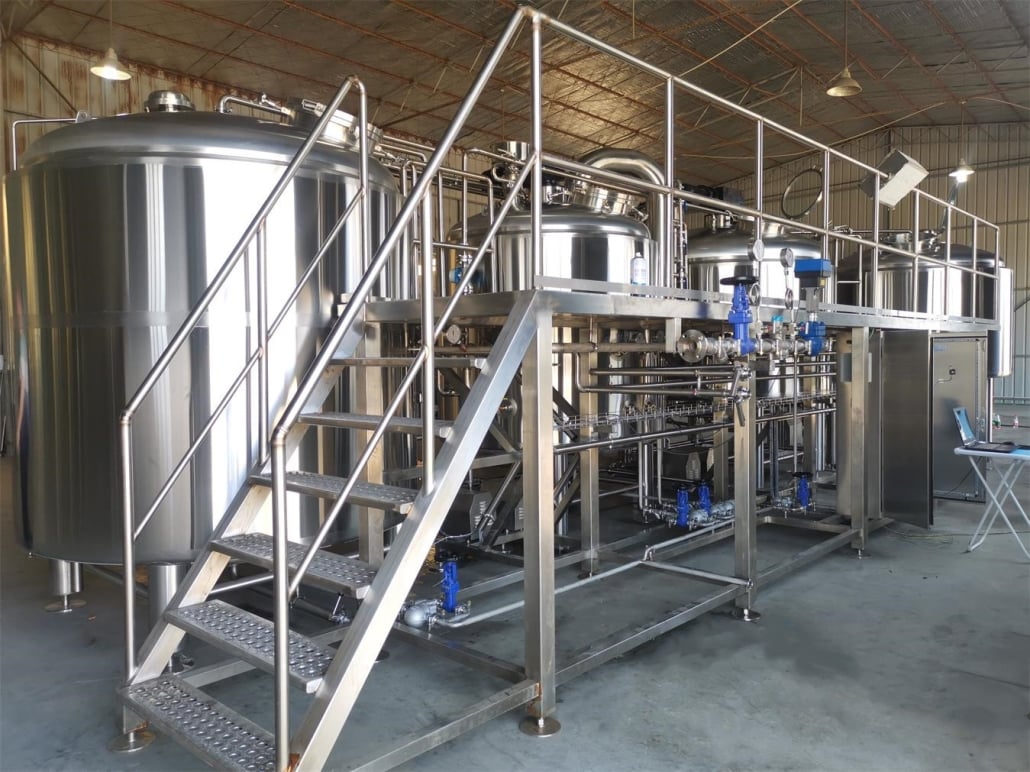
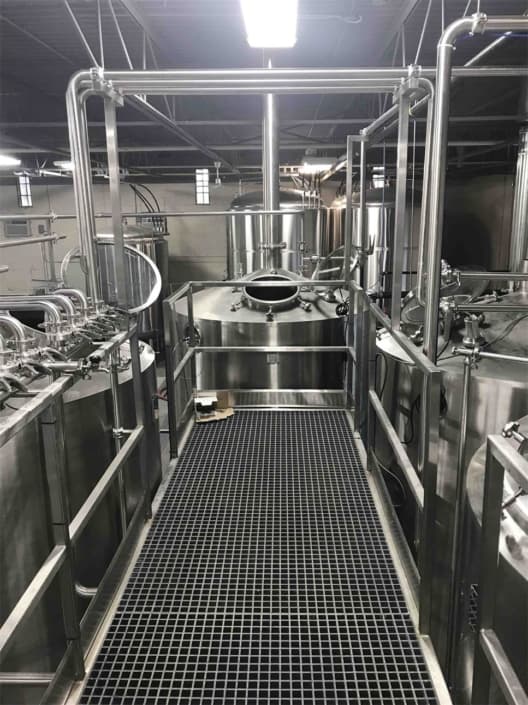
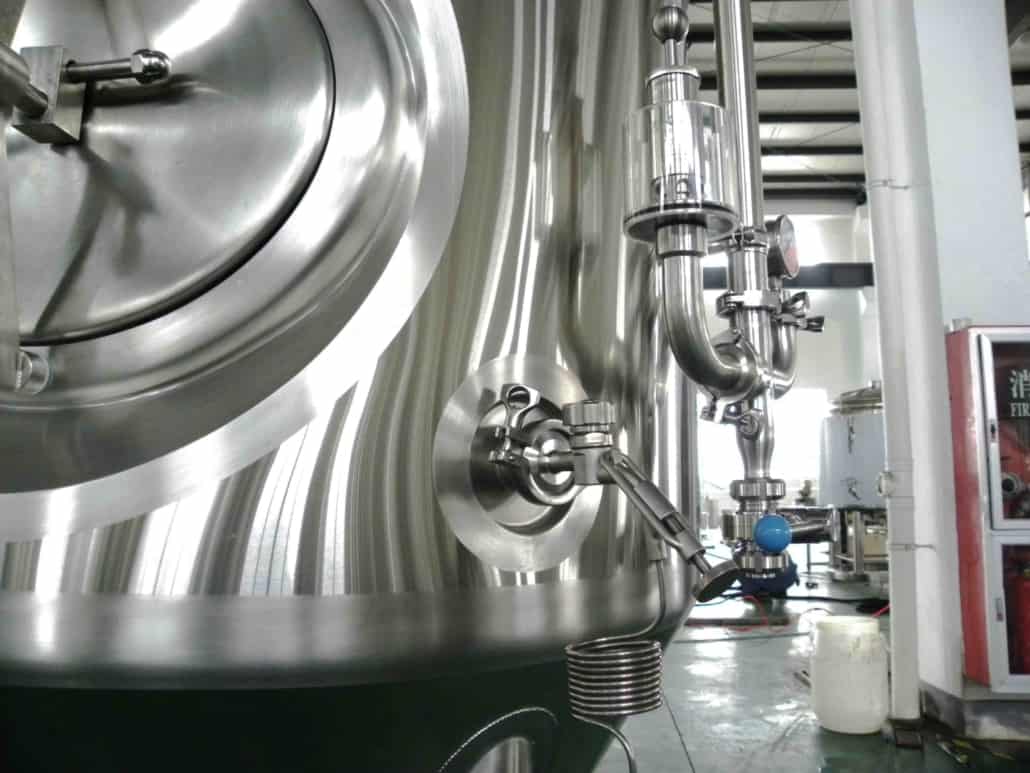
Benefits of Using Beer Canning Equipment
Benefit | Details |
---|---|
Preservation of Quality | Keeps beer fresh by reducing oxygen exposure and blocking light. |
Portability | Lightweight cans are easier to transport than glass bottles. |
Sustainability | Cans are more recyclable than other packaging options. |
Cost-Effectiveness | Cheaper to produce and transport compared to bottles. |
Enhanced Shelf Appeal | Eye-catching designs and vibrant printing attract customers on store shelves. |
How to Choose the Right Beer Canning System for Your Brewery
Choosing the right canning equipment is like picking the right brewing ingredients—it’s all about matching your needs. Here’s a guide to finding the perfect fit:
1. Assess Your Production Goals
Are you running a small-scale operation or aiming to supply regional markets? Match the machine’s capacity with your production needs.
2. Budget Considerations
From affordable manual options to high-end automated systems, costs vary widely. Balance initial investment with long-term benefits.
3. Space Requirements
Measure your available space and consider the equipment’s dimensions. Compact models are ideal for space-constrained setups.
4. Maintenance Needs
Look for user-friendly systems with readily available spare parts and support.
5. Future Scalability
Choose equipment that can grow with your brewery, allowing for upgrades or increased production capacity.
Top Beer Canning Equipment Brands in 2025
Brand | Key Features | Target Audience |
---|---|---|
Wild Goose | High-quality automated systems with customizable features. | Medium to large breweries. |
Cask Global | Innovators in compact canning systems ideal for small breweries. | Small to medium-sized operations. |
Twin Monkeys | Modular, scalable designs for growing businesses. | Breweries planning future expansion. |
American Beer | Cost-effective, durable equipment with excellent customer support. | Budget-conscious brewers. |
XpressFill | Affordable manual and semi-automatic options for entry-level users. | Hobbyists and small-scale brewers. |
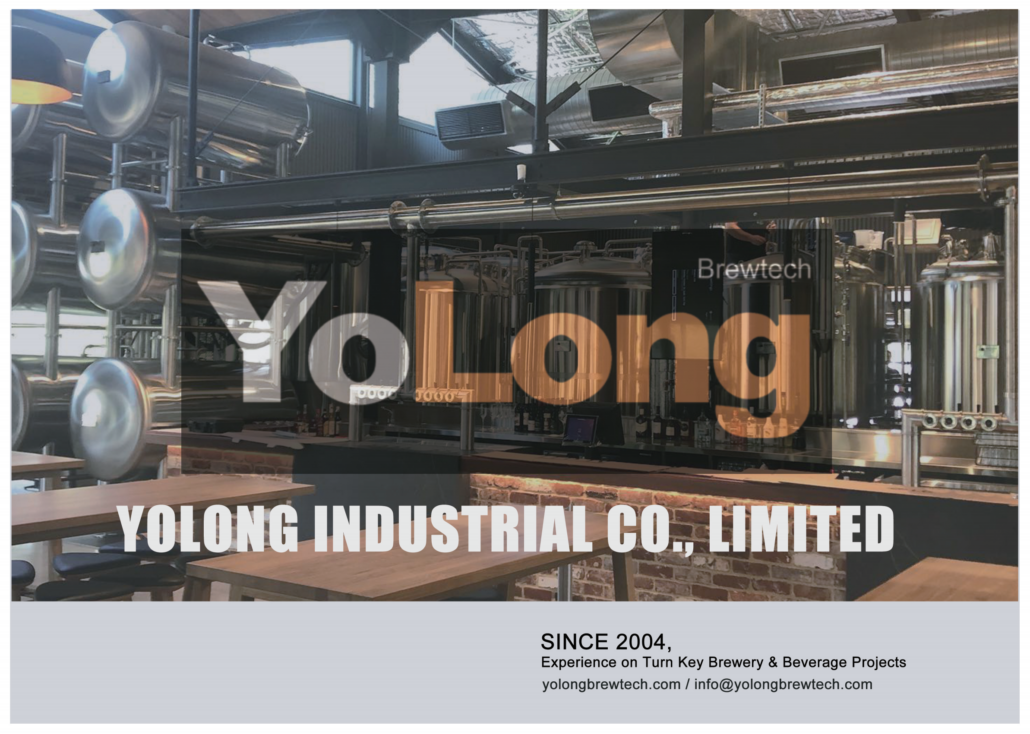
Maintenance and Troubleshooting Tips
Like brewing itself, canning requires attention to detail. Follow these tips to keep your equipment running smoothly:
- Regular Cleaning: Prevent contamination by cleaning machines thoroughly after every use.
- Inspect Seals: Check for worn-out or damaged seals to avoid leaks.
- Lubricate Moving Parts: Reduce wear and tear by keeping all components well-lubricated.
- Train Your Team: Ensure operators understand the equipment inside and out.
- Address Issues Promptly: A small problem can become a major disruption if ignored.
FAQs
Question | Answer |
---|---|
Why choose cans over bottles for beer? | Cans are lighter, more sustainable, and better at preserving beer’s freshness. |
What is the cost range of beer canning equipment? | Prices vary from $2,000 for manual systems to $200,000+ for high-end automated machines. |
Can I can other beverages using beer canning equipment? | Yes, many systems are versatile enough for soda, kombucha, and other beverages. |
How long does a typical canning machine last? | With proper maintenance, high-quality machines can last 10-15 years or more. |
Do I need special training to operate a canning machine? | Most manufacturers offer training, and modern systems are user-friendly. |