The Ultimate Guide to Beer Brewing Vessels
Overview of Beer Brewing Vessels
Beer brewing vessels are at the heart of the brewing process, housing the essential steps that convert grains, hops, water, and yeast into the world’s beloved beverage—beer. From mash tuns to fermentation tanks, each vessel plays a unique role in developing flavor, texture, and aroma. This guide will walk you through the types of brewing vessels, their capacities, customization options, pricing, installation, operation, maintenance, and more.
Essential Brewing Equipment: Types of Beer Brewing Vessels
Understanding the types of beer brewing vessels is essential for anyone venturing into brewing. Each vessel in the brewing process serves a specific function, so selecting the right equipment is crucial. Let’s dive into the equipment used in breweries.
Equipment Guide
Brewing Vessel | Purpose | Function |
---|---|---|
Mash Tun | Mashing | Converts starches to fermentable sugars. |
Lauter Tun | Lautering | Separates the mash into clear wort and spent grains. |
Brew Kettle | Boiling | Boils wort, sterilizes, and adds hops for bitterness, flavor, and aroma. |
Whirlpool Tank | Clarifying | Separates hop particles and other solids from the wort after boiling. |
Fermentation Tank | Fermenting | Allows yeast to ferment sugars, producing alcohol and carbonation. |
Bright Beer Tank | Conditioning | Clarifies, carbonates, and stores beer before packaging. |
Each of these vessels has a specific role in creating quality beer. For example, a mash tun is designed to control temperature and has an agitation system to prevent clumping, optimizing the enzymatic conversion of starches to fermentable sugars. In contrast, a bright beer tank is designed for the final stages of conditioning, allowing brewers to carbonate and clarify the beer before it reaches consumers.
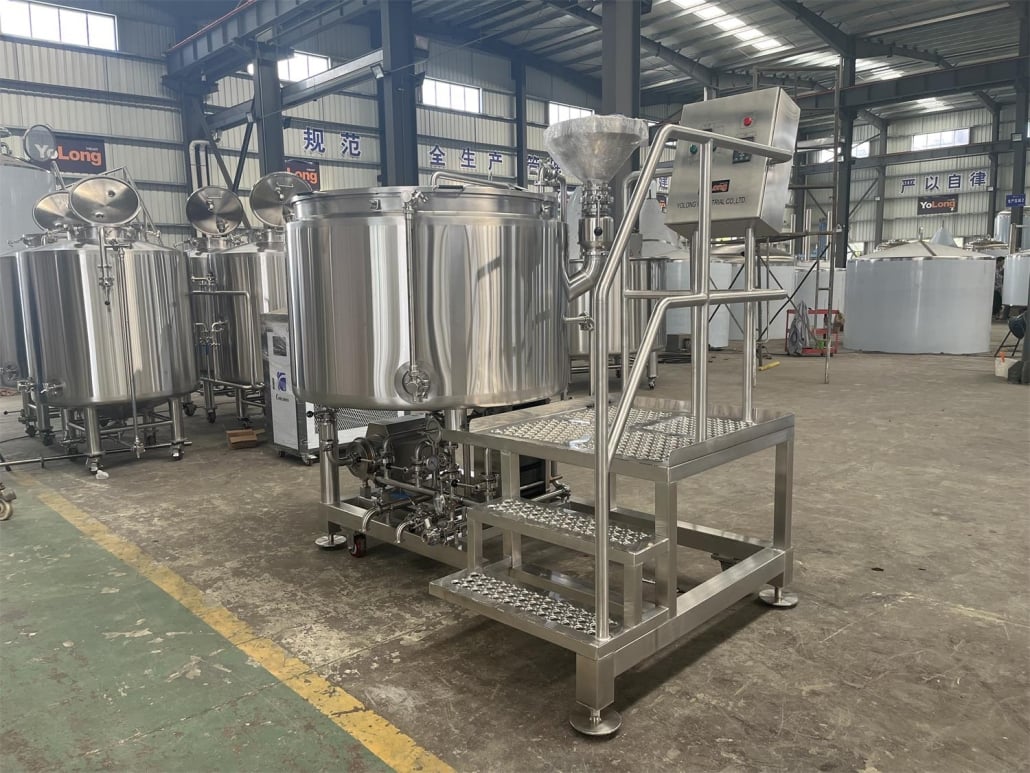
Beer Brewing Process Using Vessels
Brewing is a multi-stage process, each step building upon the last to transform raw ingredients into beer. Here’s a breakdown of the brewing stages and the vessels used:
The Brewing Steps
- Mashing: The process starts in the mash tun, where milled grains (often malted barley) are mixed with hot water. This mixture, called “mash,” undergoes a controlled temperature increase to activate enzymes that break down starches into fermentable sugars. The mash tun’s heat retention and stirring system are critical in ensuring an even conversion.
- Lautering: In the lauter tun, the mash separates into liquid wort and spent grain. This vessel has a false bottom, allowing liquid wort to be drained while the grain bed filters out particulates.
- Boiling: The wort is transferred to a brew kettle, where it’s boiled to sterilize the liquid and break down unwanted proteins. During boiling, hops are added to provide bitterness, flavor, and aroma. This kettle is designed for high heat and is often fitted with a steam jacket.
- Whirlpooling: Post-boiling, the wort is rapidly swirled in a whirlpool tank, causing solids to settle in the center, making the liquid clear and preparing it for fermentation.
- Fermentation: The wort is transferred to fermentation tanks, where yeast is added. These tanks are specially designed to regulate temperature, ensuring the yeast efficiently ferments sugars into alcohol and carbon dioxide.
- Conditioning and Packaging: The bright beer tank is where beer undergoes final conditioning, carbonation, and clarification before packaging. This step readies the beer for distribution and consumption.
Comparison of Brewing Vessel Capacities, Design, and Customization
Choosing the right size and design is essential. Breweries vary from small-scale craft setups to large-scale industrial plants, and so do their equipment requirements.
Brewing Vessel Capacity and Design Options
Brewing Vessel | Capacity Range (liters) | Space Requirements | Design Options | Customization |
---|---|---|---|---|
Mash Tun | 50 – 30,000 | Compact to large | Insulated, Jacketed | Temperature control, agitator, insulation |
Lauter Tun | 50 – 30,000 | Compact to large | False Bottom | Rake arms, slotted plates for filtration |
Brew Kettle | 50 – 50,000 | Medium to large | Direct or Indirect Heating | Heating source customization |
Whirlpool Tank | 50 – 30,000 | Small to medium | Swirl Inlet | Vortex design for solid separation |
Fermentation Tank | 100 – 100,000 | Large | Cylindroconical | Cooling jackets, pressurized, CIP spray balls |
Bright Beer Tank | 50 – 50,000 | Medium to large | Pressurizable | Carbonation stone, sanitary fittings |
Beer Brewing Vessel Suppliers and Price Range
Selecting a supplier is a vital step in sourcing high-quality brewing vessels. Various suppliers specialize in different scales of brewing, offering diverse pricing models. Here’s an analysis of popular suppliers, their specialties, and price ranges.
Supplier Name | Product Specialization | Price Range (USD) | Region |
---|---|---|---|
BrewTech | Small to mid-scale equipment | $5,000 – $20,000 | North America |
Alpha Brewing Operations | Large-scale industrial vessels | $20,000 – $200,000 | North America, Europe |
Ss Brewtech | Nano to microbrewery systems | $2,000 – $15,000 | Worldwide |
Tiantai | Complete brewery setups | $8,000 – $100,000 | Asia |
Prettech | Custom stainless steel equipment | $10,000 – $80,000 | Global |
Installation, Operation, and Maintenance of Beer Brewing Vessels
Proper installation, smooth operation, and regular maintenance are key to ensuring longevity and efficiency of brewing vessels.
Aspect | Description |
---|---|
Installation | Requires professional assembly, often done by the supplier. Proper placement is essential for optimal workflow. |
Operation | Each vessel has specific operational guidelines. Mash tuns require consistent temperature control, while fermentation tanks demand regular COâ‚‚ checks. |
Maintenance | Vessels need regular cleaning, often through a CIP (Clean-in-Place) system. Fermentation tanks need additional sanitization to prevent contamination. |
Choosing the Right Supplier for Beer Brewing Vessels
Selecting the ideal supplier involves assessing multiple factors beyond price. Quality, service, support, and reputation are equally crucial.
Factor | What to Consider |
---|---|
Quality | Evaluate materials (stainless steel, insulation) and craftsmanship. |
Customer Support | Ensure responsive support for installation, operation, and maintenance. |
Customization Options | Look for suppliers who offer customizations to meet specific brewing needs. |
Lead Time | Delivery timelines can vary widely; some suppliers may offer quicker setups. |
Warranty | A solid warranty covers repair costs and assures quality. |
Comparing Pros and Cons of Beer Brewing Vessels
Not all vessels are created equal, and each type comes with its advantages and limitations.
Brewing Vessel | Advantages | Limitations |
---|---|---|
Mash Tun | High efficiency in mashing; robust temperature control | Higher initial cost for quality models |
Lauter Tun | Effective wort separation | Requires regular cleaning to avoid clogging |
Brew Kettle | Essential for sterilization; versatile | Consumes significant energy |
Fermentation Tank | Critical for fermentation quality; temperature control | Can be prone to contamination without proper cleaning |
Bright Beer Tank | Final conditioning; carbonation flexibility | Adds cost, often requiring more space |
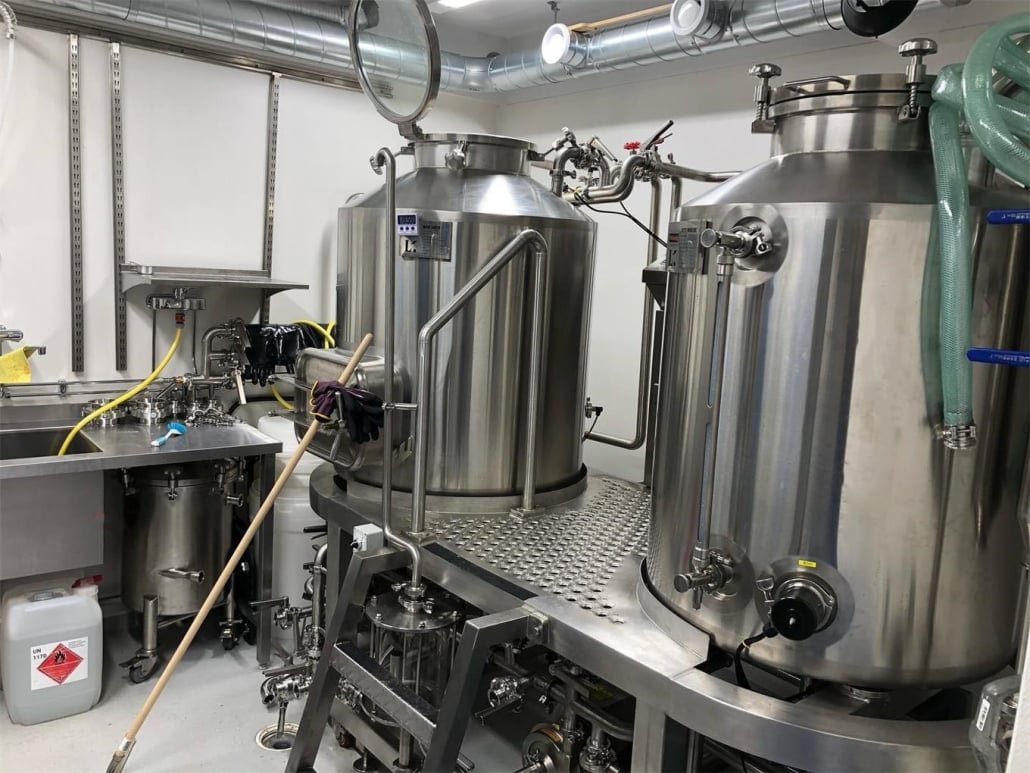
FAQ
Question | Answer |
---|---|
What’s the most important vessel in brewing? | Each vessel is essential for specific stages, but the fermentation tank holds particular importance in defining the beer’s flavor profile. |
How often should vessels be cleaned? | Generally, brewing vessels should be cleaned after each use, with deep cleaning scheduled monthly to ensure sanitary conditions. |
Are stainless steel vessels worth the cost? | Yes, stainless steel is durable, resistant to corrosion, and easy to clean, making it ideal for brewing. |
Can vessels be customized? | Many suppliers offer customization options, from adjusting capacity to adding temperature control and pressure systems. |
What’s the average lifespan of a brewing vessel? | With proper maintenance, high-quality brewing vessels can last 15–20 years or more. |
This format not only presents a comprehensive overview but also makes complex information easily accessible. Let me know if you’d like adjustments or additional sections in a similar detailed format.