Overview of Automated Brewing Systems
Brewing beer is as much an art as it is a science. For centuries, brewers have honed their craft, meticulously managing each stage of the brewing process to create the perfect pint. But as with many industries, technology has changed the game. Enter the automated brewing system—a technological marvel that promises to revolutionize how beer is made, whether you’re a homebrewer, running a microbrewery, or operating a large-scale brewing facility.
What exactly is an automated brewing system?
In essence, it’s a set of interconnected machines and software designed to automate various aspects of the brewing process, from mashing and boiling to fermenting and cooling. Automation ensures that each batch of beer is brewed with precision, consistency, and minimal human intervention. But why is this important?
Brewing is a delicate balance of ingredients, timing, and conditions. Even the slightest deviation can affect the flavor, aroma, and quality of the beer. Automated systems take much of the guesswork out of brewing, allowing brewers to achieve consistent results every time. This consistency is crucial for commercial brewers who need to meet customer expectations with every batch. For homebrewers, it means more successful experiments and less wasted ingredients.
Who benefits the most from automated brewing systems?
Well, the answer is everyone. Homebrewers can focus on crafting new recipes without worrying about the intricacies of temperature control or timing. Commercial brewers can scale up their operations and maintain quality across larger volumes. Industrial brewers can streamline their processes, reduce labor costs, and increase production efficiency.
In this comprehensive guide, we’ll delve into the world of automated brewing systems, exploring the different types of equipment available, the brewing process, and how to choose the right system for your needs. We’ll also compare suppliers, discuss installation and maintenance, and weigh the pros and cons of automation. Whether you’re a seasoned brewer or just starting, this guide will help you navigate the complexities of automated brewing and find the system that’s right for you.
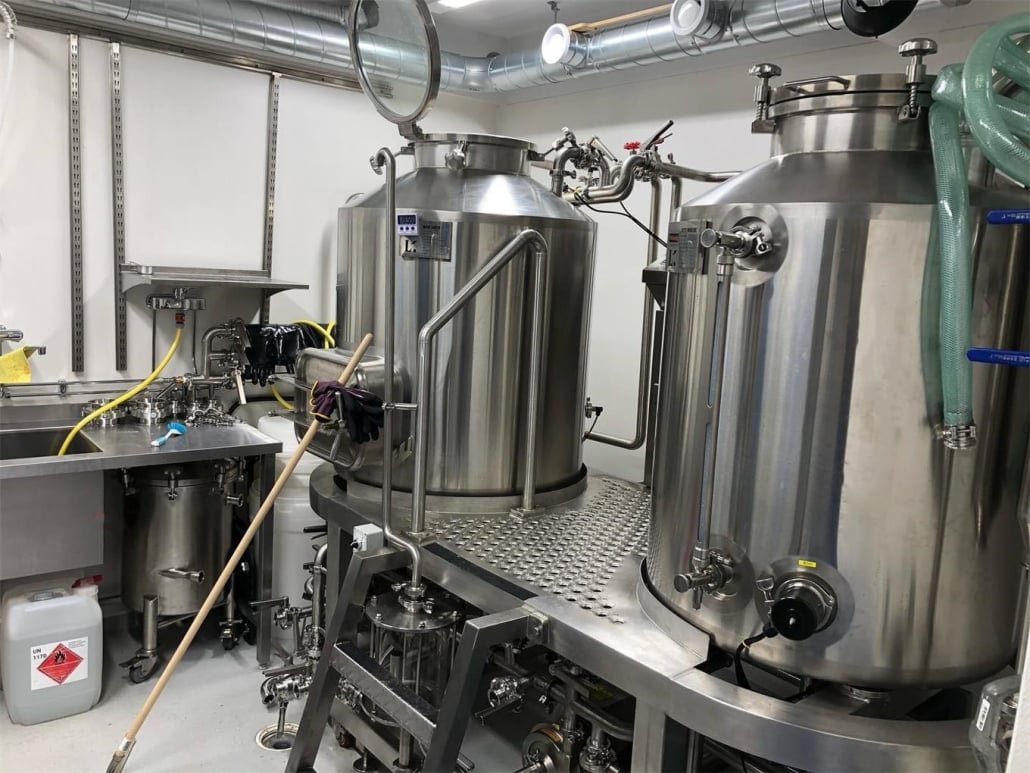
Equipment Guide: Types of Automated Brewing Systems
When it comes to automated brewing systems, there’s no one-size-fits-all solution. The right system for you will depend on your brewing goals, the scale of your operations, and your budget. Here’s an overview of the different types of automated brewing systems available, from basic home setups to industrial-scale systems.
Basic Home Brewing Systems:
Homebrewing has surged in popularity, and with it, the availability of user-friendly automated systems designed for home use. These systems typically offer a balance between automation and manual control, allowing hobbyists to fine-tune their brewing process while still enjoying the convenience of automation. Features often include automated temperature control, programmable brewing schedules, and integrated cleaning systems. Home systems are usually compact and designed to fit in a standard kitchen, making them ideal for beginners or those with limited space.
Commercial Brewing Systems:
For those looking to brew on a larger scale, commercial automated systems offer a significant upgrade in terms of capacity and functionality. These systems are designed for microbreweries or small craft breweries that need to produce consistent, high-quality beer in larger quantities. Commercial systems typically include advanced features such as multi-stage mashing, automated grain handling, and sophisticated monitoring software. These systems require more space and a higher initial investment but offer greater scalability and efficiency.
Industrial-Scale Brewing Systems:
At the top of the spectrum are industrial-scale automated brewing systems, used by large breweries to produce massive volumes of beer with pinpoint accuracy. These systems are fully automated, with every aspect of the brewing process—from raw material handling to packaging—controlled by advanced software and robotics. Industrial systems are designed for maximum efficiency, reducing labor costs and minimizing the potential for human error. They’re also highly customizable, allowing breweries to adapt to changing market demands quickly.
Comparing Features Across Systems:
When choosing an automated brewing system, it’s essential to compare the features that matter most to your brewing operation. Home systems prioritize ease of use and affordability, while commercial and industrial systems focus on capacity, scalability, and advanced automation capabilities. Consider factors like batch size, customization options, and the level of automation when making your decision.
Pros and Cons of Each Type:
Each type of automated brewing system comes with its own set of advantages and disadvantages. Home systems are accessible and straightforward but may lack the advanced features needed for complex brewing processes. Commercial systems strike a balance between automation and control, offering the best of both worlds for small to medium-sized breweries. Industrial systems, while the most advanced, require a significant investment and are best suited for large-scale operations where consistency and efficiency are paramount.
Detailed Equipment Comparison Table
To help you better understand the different types of automated brewing systems, here’s a detailed comparison table that breaks down the key features, capacities, and customization options for each type.
Type of System | Capacity | Space Requirements | Design & Layout | Customization Options |
---|---|---|---|---|
Basic Home Brewing Systems | 5-10 gallons per batch | Compact, fits in a kitchen | Simple design, user-friendly interface | Limited, focused on ease of use |
Commercial Brewing Systems | 50-500 gallons per batch | Requires dedicated brewing space | Modular design, advanced features | High, can be tailored to specific needs |
Industrial Brewing Systems | 1000+ gallons per batch | Large-scale facility required | Fully automated, complex layout | Extensive, customizable at every stage |
Brewing Process Using Automated Systems
The brewing process, whether manual or automated, follows a series of well-established steps. However, automation introduces a new level of precision and control, making the process more efficient and consistent. Let’s walk through the brewing process as it would occur in an automated system.
Mashing:
The brewing process begins with mashing, where malted barley is mixed with hot water to convert the starches into fermentable sugars. In an automated system, the temperature and timing of the mash are controlled by the system’s software, ensuring that the optimal conditions are maintained throughout the process. This precision results in a more consistent extraction of sugars, which is crucial for achieving the desired flavor profile in the final beer.
Boiling:
After m
ashing, the wort (the liquid extracted from the mashing process) is boiled, typically with hops added to impart bitterness, flavor, and aroma to the beer. An automated system regulates the boiling time and the timing of hop additions, which is critical for developing the beer’s bitterness and aroma. Some systems even allow for multiple hop additions at different stages of the boil, all programmed in advance.
Fermentation:
Once the boiling process is complete, the wort is cooled and transferred to a fermentation vessel, where yeast is added. Fermentation is where the magic happens, as the yeast consumes the sugars in the wort and produces alcohol and carbon dioxide. Automated systems closely monitor the temperature during fermentation, as fluctuations can affect the yeast’s performance and the final flavor of the beer. Some systems also allow for automatic transfer to secondary fermentation tanks, further reducing the need for manual intervention.
Cooling and Conditioning:
After fermentation, the beer is cooled and conditioned, which can involve additional stages like filtration, carbonation, and aging. Automated systems ensure that these stages are carried out at the correct temperatures and durations, which is essential for achieving the desired clarity, mouthfeel, and carbonation level.
Packaging:
Finally, the beer is packaged in bottles, cans, or kegs. While packaging is often a separate process, some advanced automated systems include integrated packaging solutions, further streamlining the production process.
Challenges and Troubleshooting:
Even with automation, brewing can present challenges. Common issues include stuck mashes, boil overs, and off-flavors caused by fermentation problems. However, most automated systems come with built-in troubleshooting guides and alerts, allowing brewers to quickly identify and address issues as they arise.
Brewing Process vs. Manual Brewing
Here’s a comparison between automated and manual brewing processes, highlighting the key differences in time, precision, consistency, and effort required.
Brewing Stage | Automated Brewing | Manual Brewing |
---|---|---|
Mashing | Precise temperature control, timed automatically | Requires constant monitoring and manual adjustments |
Boiling | Automated timing and hop additions | Manual hop additions, careful timing needed |
Fermentation | Temperature regulated automatically | Requires frequent temperature checks and adjustments |
Cooling and Conditioning | Automated, consistent results | Requires manual intervention and monitoring |
Packaging | Often integrated, minimal manual effort | Entirely manual, labor-intensive |
Suppliers and Price Range for Automated Brewing Systems
Choosing the right supplier for your automated brewing system is crucial, as it directly impacts the quality, reliability, and cost of your brewing operation. Below, we’ll explore some of the top suppliers in the industry, the price range for different systems, and factors that influence these costs.
Top Suppliers Globally:
Several manufacturers stand out in the automated brewing system market, each offering unique products tailored to different segments of the brewing industry. Names like Ss Brewtech, Blichmann Engineering, Brewie, and BrauKon are well-known for their innovation, quality, and customer support.
Price Range:
The cost of an automated brewing system can vary widely depending on the type and scale of the system. Basic home brewing systems might range from $500 to $5,000, while commercial systems can range from $10,000 to $100,000. Industrial systems can easily exceed $1 million, especially when custom-built to specific requirements. Prices are influenced by factors like capacity, level of automation, customization, and brand reputation.
Factors Influencing Cost:
Several factors can drive up or lower the cost of an automated brewing system. These include the level of automation (e.g., fully automated vs. semi-automated), the materials used (e.g., stainless steel vs. aluminum), and additional features like integrated cleaning systems or advanced monitoring software. Customization also plays a significant role, as systems designed to meet specific brewing needs often come with a higher price tag.
Best Value for Money Options:
While high-end systems offer advanced features and scalability, there are also budget-friendly options that provide excellent value for money. Brands like Grainfather and Anvil Brewing offer affordable systems that still deliver reliable performance and ease of use, making them popular choices for homebrewers and small breweries alike.
Comparison of Suppliers
To help you navigate the market, here’s a comparison table of some of the top suppliers of automated brewing systems, including the price range, system types offered, and customer satisfaction ratings.
Supplier | Price Range | System Types | Customer Satisfaction |
---|---|---|---|
Ss Brewtech | $1,000 – $50,000 | Home, Commercial | High |
Blichmann | $500 – $20,000 | Home, Small Commercial | Very High |
Brewie | $2,000 – $10,000 | Home, Small Commercial | Moderate |
BrauKon | $50,000 – $500,000+ | Commercial, Industrial | Very High |
Grainfather | $700 – $3,000 | Home | High |
Anvil Brewing | $500 – $1,500 | Home | High |
Installation, Operation, and Maintenance
Installing an automated brewing system can be a significant undertaking, especially for commercial and industrial setups. However, with the right preparation and guidance, the process can be smooth and manageable. Here’s what you need to know about installation, operation, and maintenance.
Installing an Automated Brewing System:
The installation process will vary depending on the size and complexity of your system. For homebrewers, installation might be as simple as assembling the equipment and connecting it to a power source. For commercial and industrial systems, installation may require professional assistance to ensure that all components are properly connected and calibrated. It’s essential to plan for the installation in advance, considering factors like space requirements, utility connections, and ventilation.
Operating the System Effectively:
Operating an automated brewing system is generally straightforward, thanks to the intuitive controls and pre-programmed brewing schedules that come with most systems. However, understanding the underlying brewing process is still important, as it allows you to make adjustments and troubleshoot issues as they arise. Regular monitoring of the system’s performance, even in a fully automated setup, helps ensure that the brewing process runs smoothly and that the final product meets your expectations.
Maintenance Tips for Longevity:
Regular maintenance is crucial to keep your automated brewing system running efficiently and to extend its lifespan. This includes cleaning the system after each use, checking and replacing worn parts, and updating the software as needed. Many systems come with integrated cleaning programs, which make the maintenance process easier. However, manual cleaning and inspection are still recommended periodically to catch any potential issues before they become serious problems.
Common Operational Issues and Solutions:
Even the most advanced automated systems can encounter issues, such as clogged lines, pump failures, or software glitches. Being familiar with the most common problems and their solutions can save you time and prevent production delays. Many suppliers offer customer support and troubleshooting guides to help you address these issues quickly and efficiently.
Installation, Operation, Maintenance Comparison
Here’s a comparison of the time required, ease of operation, maintenance frequency, and common issues for different types of automated brewing systems.
Aspect | Home Brewing Systems | Commercial Brewing Systems | Industrial Brewing Systems |
---|---|---|---|
Installation Time | 1-2 days | 1-2 weeks | 1-3 months |
Ease of Operation | Very Easy | Moderate | Complex, requires training |
Maintenance Frequency | After every brew | Regular, based on usage | Continuous monitoring and maintenance |
Common Issues | Clogged lines, software updates | Pump failures, temperature control issues | Mechanical wear, software glitches |
Choosing the Right Supplier for Automated Brewing Systems
Selecting the right supplier for your automated brewing system is a critical decision that can impact the success of your brewing operation. Here’s a guide on how to choose the best supplier based on key factors like price, reliability, and customer service.
Key Factors to Consider:
When evaluating suppliers, consider factors like their reputation in the industry, the range of products they offer, and their customer service track record. It’s also important to assess the quality of the systems they provide, including the materials used, the level of automation, and the available customization options. Pricing is another crucial factor, but it should be weighed against the value you’re getting—cheaper isn’t always better if it means sacrificing quality or support.
Comparing Local vs. International Suppliers:
Local suppliers may offer faster delivery times, easier communication, and potentially lower shipping costs. However, international suppliers often provide a wider range of products and may have more advanced technology. When choosing between local and international suppliers, consider the importance of after-sales service, as well as any potential language barriers or time zone differences that could impact support.
Warranties and After-Sales Service:
A good warranty and reliable after-sales service are essential, especially for complex systems like automated brewing equipment. Look for suppliers that offer comprehensive warranties that cover both parts and labor, and inquire about the availability of technical support, spare parts, and training programs. Customer reviews and testimonials can provide valuable insights into the level of service you can expect.
Customer Reviews and Case Studies:
Before making a final decision, it’s worth researching customer reviews
and case studies to see how other brewers have fared with the supplier’s equipment. Look for feedback on the reliability of the systems, the quality of the customer service, and the overall satisfaction with the supplier. Case studies can also provide insights into how the systems perform in real-world brewing operations, helping you gauge whether they’re the right fit for your needs.
How to Choose a Supplier
Here’s a summary of the key criteria for selecting a supplier, along with questions to ask and a comparison of supplier performance.
Criteria | Key Questions | Supplier Performance |
---|---|---|
Price | Is the price competitive for the features offered? | Varies by supplier |
Reliability | How reliable are the systems? Any common issues? | Generally high, varies by system type |
Customer Service | How responsive is the supplier? | High for top suppliers, varies for smaller brands |
Warranty | What does the warranty cover? How long is it? | Comprehensive for most top suppliers |
Reviews/Testimonials | What do other customers say? | Generally positive for top-rated suppliers |
After-Sales Support | Is there adequate support for troubleshooting? | Strong for established brands |
Pros and Cons of Automated Brewing Systems
Automated brewing systems offer numerous benefits, but they also come with their own set of challenges. Here’s a closer look at the advantages and disadvantages of adopting an automated brewing system, along with examples and case studies.
Advantages of Automated Brewing Systems:
One of the biggest advantages of automated brewing systems is their ability to produce consistent results batch after batch. Automation minimizes the risk of human error, which is crucial for maintaining the quality and flavor of the beer. These systems also save time and effort, allowing brewers to focus on other aspects of their business or hobby. Additionally, automation can increase efficiency, reduce waste, and potentially lower production costs over time.
Disadvantages of Automated Brewing Systems:
On the downside, automated brewing systems can be expensive, particularly for advanced commercial and industrial setups. The initial investment can be a barrier for smaller breweries or homebrewers. Additionally, while automation reduces the need for manual intervention, it also requires a certain level of technical expertise to operate and maintain the system effectively. Finally, some brewers argue that automation takes away from the hands-on, artisanal aspect of brewing, which can be an essential part of the craft for many.
Case Studies and Examples:
Consider the case of a small craft brewery that switched from a manual brewing process to an automated system. The brewery saw a significant increase in production efficiency and a reduction in batch-to-batch variability, which helped them scale their business and meet growing demand. However, the initial cost was high, and it took time to train the staff on the new system.
Advantages vs. Disadvantages of Automated Systems
Here’s a comparison of the pros and cons of automated brewing systems, highlighting key considerations for potential buyers.
Aspect | Advantages | Disadvantages |
---|---|---|
Consistency | High consistency in beer quality | May reduce the artisanal aspect of brewing |
Efficiency | Increases production efficiency | Requires a significant initial investment |
Time Savings | Reduces time spent on manual processes | Technical expertise required for operation |
Cost Savings | Potential long-term cost savings | High upfront costs |
Customization | Systems can be customized to specific needs | Customization can add to the cost |
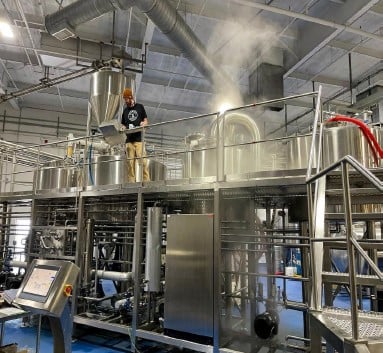
FAQ
Below is a Frequently Asked Questions (FAQ) section addressing common queries about automated brewing systems. This section is formatted in a table for easy reference.
Question | Answer |
---|---|
What is an automated brewing system? | An automated brewing system is a setup that automates key brewing processes to enhance consistency and efficiency. |
How much does an automated brewing system cost? | Prices range from $500 for basic home systems to over $1 million for industrial setups. |
Can I customize my brewing system? | Yes, many suppliers offer customization options to meet specific brewing needs. |
Is an automated system suitable for homebrewing? | Yes, there are many user-friendly systems designed specifically for homebrewers. |
What are the maintenance requirements? | Regular cleaning, software updates, and periodic inspections are essential to maintain the system. |
Do automated systems produce better beer? | Automation helps achieve consistency, but the quality also depends on ingredients and recipes. |
What are the common issues with automated systems? | Common issues include clogged lines, software glitches, and mechanical wear, all of which can be managed with proper maintenance. |
How do I choose the right system for my needs? | Consider factors like your brewing goals, budget, space, and the level of automation you require. |
Conclusion
Automated brewing systems represent the future of beer production, offering unprecedented control, consistency, and efficiency. Whether you’re a hobbyist brewing in your garage or the owner of a large brewery, there’s an automated system that can help you achieve your brewing goals. As technology continues to evolve, we can expect even more innovative solutions that make brewing easier, faster, and more enjoyable than ever before.
In choosing the right system, it’s essential to consider your needs, budget, and the level of automation you’re comfortable with. Remember, while automation can enhance your brewing process, it’s the creativity and passion you bring to the craft that will ultimately define the quality of your beer. So, embrace the technology, but don’t forget the art of brewing.
Share this entry
Interested in learning more about Brewing Systems including additional details and pricing information? Please use the form below to contact us!
YOLONG BREWERY EQUIPMENT FAQS
- Commercial Brewery / Craft Brewery / Microbrewery / Nanobrewery
- What is The Difference Between Craft Beer and Industrial Beer?
- The Bespoke Differences In Custom Brewing Systems
- Everything You Need to Know About Kettle Souring
- How to Choose Brewing Equipment for Your business?
- How To Choose The-Best Partner To Build Your Commercial Microbrewing System?
- Two Detection Sensors That You Need To Use In Your Brewhouse System
- Remote Control Applications in Brewing Equipment/How does it work?
- How To Clean Your Brand New Brewery Tanks?