Automated Beer Brewing System
Introduction
Automated beer brewing systems are rapidly transforming the landscape of craft beer production. With the rise of technology and the growing demand for precision and efficiency, these systems are becoming essential for both large-scale breweries and homebrewers alike. But what exactly are automated beer brewing systems, and how can they revolutionize the brewing process?
In this comprehensive guide, we’ll dive deep into everything you need to know about automated beer brewing systems—from the key equipment and brewing processes to installation, operation, and maintenance. Whether you’re a seasoned brewer looking to upgrade your setup or a beginner exploring your options, this article will provide valuable insights and practical advice.
Understanding Automated Beer Brewing Systems
Definition and Purpose
At its core, an automated beer brewing system is designed to streamline the brewing process by automating various stages, from mashing to fermentation. These systems integrate advanced technology, such as sensors, control panels, and software, to monitor and adjust brewing parameters with precision. This not only ensures consistent quality in each batch but also reduces the need for manual intervention, allowing brewers to focus on creativity and innovation.
How They Differ from Traditional Brewing Methods
Traditional brewing methods often rely heavily on manual labor, with brewers having to oversee each step of the process, from mixing ingredients to controlling temperatures. While this hands-on approach has its charms, it can also lead to inconsistencies and inefficiencies, especially in larger operations.
Automated systems, on the other hand, take the guesswork out of brewing. By utilizing sensors and programmable controllers, these systems can maintain exact temperatures, monitor fermentation progress, and even adjust recipes on the fly. This level of control is particularly beneficial for breweries that produce large volumes of beer or those that want to experiment with new styles without risking quality.
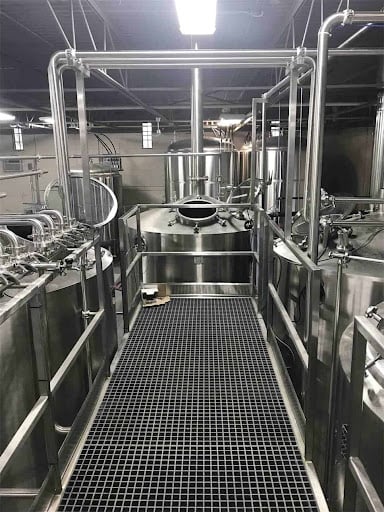
Advantages of Automated Systems
The advantages of using an automated beer brewing system are manifold. Firstly, they offer unmatched precision and consistency, which is crucial for maintaining the quality of the final product. Secondly, automation can significantly reduce the labor involved in brewing, freeing up time for brewers to focus on other aspects of the business, such as marketing and distribution.
Moreover, automated systems are scalable, meaning they can grow with your production needs. Whether you’re starting with a small setup or planning to expand to a full-scale
brewery, these systems can be customized to fit your requirements. Lastly, automation enhances safety by reducing the likelihood of human error and allowing for better control of potentially hazardous processes, such as heating and cooling.
Key Components of an Automated Beer Brewing System
An automated beer brewing system typically consists of several key components, each playing a vital role in the brewing process:
- Brewing Vessels and Fermentation Tanks: These are the core elements where the actual brewing and fermentation occur.
- Heating Elements and Cooling Systems: Essential for maintaining the right temperatures during different stages of brewing.
- Control Panels and Software Integration: The brain of the system, allowing brewers to monitor and adjust settings in real-time.
- Sensors and Automation Controls: Devices that provide data on temperature, pressure, and other critical factors to ensure the process stays on track.
- Cleaning and Maintenance Tools: Equipment designed to keep the system in optimal working condition, ensuring longevity and consistent performance.
Equipment Guide for Automated Beer Brewing
When setting up an automated beer brewing system, selecting the right equipment is crucial. Each piece of equipment plays a specific role, and understanding these roles can help you make informed decisions.
Brewing Vessels and Fermentation Tanks
Brewing vessels are where the magic begins. These large tanks are used for mashing, boiling, and fermenting the beer. The choice of material—usually stainless steel or copper—affects not only the durability of the equipment but also the flavor of the beer. Fermentation tanks, on the other hand, are designed to house the beer as it ferments. These tanks often come equipped with cooling jackets to maintain the optimal fermentation temperature.
Heating Elements and Cooling Systems
Heating elements are responsible for bringing the brew to the right temperature at various stages. Depending on your system, these can be electric or gas-powered. Efficient heating is critical for ensuring that the starches in the malt are converted to sugars during the mashing process.
Cooling systems are equally important. After boiling, the wort needs to be rapidly cooled to avoid contamination and prepare it for fermentation. Glycol chillers are commonly used in automated systems to achieve this rapid cooling.
Control Panels and Software Integration
The control panel is the nerve center of an automated brewing system. It allows brewers to monitor and adjust brewing parameters such as temperature, pressure, and timing. Modern systems often integrate with software, enabling remote monitoring and control. This means you can start a brew from your phone or computer, making the process more flexible and convenient.
Sensors and Automation Controls
Sensors are the eyes and ears of an automated system. They provide real-time data on various aspects of the brewing process, from temperature and pH levels to pressure and flow rates. Automation controls use this data to make adjustments as needed, ensuring that the brewing process remains within the desired parameters.
Cleaning and Maintenance Tools
Automated systems come with built-in cleaning and maintenance tools, making it easier to keep the equipment in top condition. These tools may include CIP (Clean-In-Place) systems, which allow for thorough cleaning of tanks and pipes without the need to disassemble the equipment. Regular maintenance is essential for preventing breakdowns and ensuring that the system operates efficiently.
Types of Equipment in Automated Beer Brewing
Equipment Type | Description | Common Materials | Primary Function |
---|---|---|---|
Brewing Vessels | Large tanks for mashing, boiling, and fermenting | Stainless Steel, Copper | Mix and ferment ingredients |
Heating Elements | Devices used to heat the brew at various stages | Electric, Gas-powered | Maintain optimal temperatures |
Cooling Systems | Equipment to cool the beer post-brewing | Glycol Chillers | Control fermentation temperature |
Control Panels | Interface for automating and monitoring the process | Digital Displays, Software | Monitor and control brewing parameters |
Sensors | Devices that measure temperature, pressure, etc. | Digital, Analog | Ensure brewing accuracy |
Cleaning Systems | CIP (Clean-In-Place) systems and other maintenance tools | Stainless Steel | Maintain cleanliness and operational efficiency |
The Automated Brewing Process
Now that we’ve covered the essential equipment, let’s take a closer look at the brewing process itself. Automation can streamline this process, but it’s still essential to understand each stage to make the most of your system.
Mashing
Mashing is the first step in brewing, where malted barley is mixed with hot water to convert the starches into fermentable sugars. Automated systems allow for precise control of temperature and timing during this stage, ensuring that the conversion process is efficient and consistent.
Boiling
After mashing, the wort (the liquid extracted from the mashing process) is boiled. This step sterilizes the wort and allows for the addition of hops, which contribute bitterness and aroma to the beer. Automation here can manage the timing of hop additions, ensuring that the desired flavor profile is achieved.
Cooling
Once the boiling is complete, the wort needs to be cooled rapidly to prevent contamination and to prepare it for fermentation. Automated systems often use glycol chillers to achieve rapid cooling, ensuring that the wort reaches the optimal fermentation temperature quickly.
Fermentation
Fermentation is where the magic happens—yeast is added to the cooled wort, converting the sugars into alcohol and carbon dioxide. Automated systems can monitor the temperature and pressure during this stage, making adjustments as needed to maintain a consistent fermentation environment.
Conditioning and Packaging
After fermentation, the beer is conditioned, which involves aging the beer to allow the flavors to develop fully. This stage can be automated as well, with systems monitoring the time and temperature to ensure that the beer is ready for packaging. Automated systems can also assist with the packaging process, whether you’re bottling, canning, or kegging the beer.
Brewing Process Stages
Stage | Description | Time Required | Key Considerations |
---|---|---|---|
Mashing | Mixing malt with water and heating to convert starches to sugars | 60-90 minutes | Precise temperature control |
Boiling | Heating the wort and adding hops | 60-90 minutes | Hop timing for flavor balance |
Cooling | Lowering the temperature quickly | 20-30 minutes | Avoiding contamination |
Fermentation | Yeast converts sugars to alcohol | 1-2 weeks | Consistent temperature |
Conditioning | Aging the beer to develop flavors | 1-3 weeks | Storage conditions |
Automated Beer Brewing System Design and Layout
Design and layout are critical factors in the success of any automated beer brewing system. The right design can improve efficiency, reduce waste, and make the brewing process more enjoyable.
Space Requirements and Configurations
When planning your brewery, you’ll need to consider the amount of space available. Automated systems can be quite compact, but you’ll still need enough room for the brewing vessels, fermentation tanks, and associated equipment. The layout should allow for easy access to all parts of the system, with enough space for maintenance and cleaning.
Customization Options for Different Brewery Sizes
One of the great advantages of automated systems is their flexibility. Whether you’re running a small craft brewery or a large-scale operation, these systems can be customized to fit your needs. Modular designs are particularly popular, as they allow you to add or remove components as your production needs change.
Importance of Layout in Efficiency
The layout of your brewing system can have a significant impact on efficiency. A well-planned layout will minimize the distance between different stages of the brewing process, reducing the time and effort required to move ingredients and equipment. Considerations such as the placement of control panels, access to utilities, and workflow should all be taken into account when designing your layout.
Capacity, Space, Design, and Layout Considerations
Factor | Details | Recommendation |
---|---|---|
Brewing Capacity | Measured in barrels or liters | Match capacity to demand |
Space Requirements | Floor space needed for equipment and workflow | 50-100 sq ft for small systems |
Customization | Modifications for specific brewing needs | Modular designs are preferable |
Layout | Arrangement of equipment for optimal flow | Linear or U-shaped layouts work best |
Suppliers and Price Range for Automated Beer Brewing Systems
Choosing the right supplier is crucial when investing in an automated beer brewing system. The quality of the equipment, the level of support provided, and the overall cost are all factors that need to be carefully considered.
Overview of Leading Suppliers
There are several well-established suppliers in the market, each offering different strengths. Some specialize in high-end systems with advanced features, while others focus on more affordable options that still deliver reliable performance.
Price Ranges Based on System Size and Features
The cost of an automated beer brewing system can vary widely depending on the size of the system and the features included. Smaller systems designed for homebrewers or small craft breweries might start at around $8,000, while larger systems suitable for commercial breweries can exceed $60,000.
Considerations When Choosing a Supplier
When evaluating potential suppliers, it’s essential to look beyond just the initial cost. Consider the long-term value of the system, including the availability of support and spare parts, the ease of upgrading the system as your needs grow, and the reputation of the supplier within the industry.
Installation, Operation, and Maintenance of Automated Beer Brewing Systems
Once you’ve selected your system, the next step is installation. This is a critical phase that requires careful planning and execution to ensure that the system operates correctly.
Installation Process: What to Expect
Installing an automated beer brewing system typically involves setting up the equipment, configuring the software, and conducting initial tests to ensure everything is working as expected. Depending on the complexity of the system, this process can take anywhere from a few days to several weeks. It’s usually recommended to have professionals handle the installation, especially for larger systems.
Operating an Automated System: Best Practices
Operating an automated beer brewing system is relatively straightforward once you’re familiar with the controls. However, it’s important to follow best practices, such as regularly checking the system for any signs of wear and tear, ensuring that the software is up to date, and keeping detailed records of each brew. This will help you identify any potential issues early on and ensure that your system continues to operate efficiently.
Routine Maintenance and Troubleshooting
Regular maintenance is essential for keeping your automated system in top condition. This includes cleaning the equipment after each use, calibrating sensors and other instruments regularly, and replacing any worn-out parts. Troubleshooting is also a part of the maintenance process—being able to quickly identify and fix issues can prevent costly downtime and keep your brewing schedule on track.
Installation, Operation, Maintenance
How to Choose the Right Supplier for Automated Beer Brewing Systems
Selecting the right supplier for your automated beer brewing system can make a significant difference in the success of your brewing operations.
Factors to Consider: Reputation, Support, Customization
When choosing a supplier, reputation should be at the top of your list. A supplier with a strong track record of delivering high-quality equipment and providing excellent customer service is more likely to meet your needs. Additionally, consider the level of support the supplier offers, particularly in terms of training, troubleshooting, and spare parts availability.
Customization options are also crucial. Your brewing needs may evolve over time, so it’s essential to choose a supplier who can provide flexible solutions that can grow with your business.
Comparing Suppliers: What to Look for in Proposals
When comparing proposals from different suppliers, pay close attention to the details. Look for transparency in pricing, clear descriptions of the features and capabilities of the equipment, and the availability of after-sales support. Don’t hesitate to ask for references or to visit breweries that are using the systems you’re considering.
Long-term Relationship with Suppliers: Importance of After-sales Support
The relationship with your supplier shouldn’t end once the system is installed. After-sales support is vital for ensuring that your system continues to operate smoothly. This includes access to technical support, availability of spare parts, and regular updates or upgrades to the system. A supplier who offers comprehensive after-sales support can save you time and money in the long run.
How to Choose the Right Supplier
Factor | What to Look For | Why It Matters |
---|---|---|
Reputation | Positive reviews, industry experience | Trustworthiness and reliability |
Support | Availability of technical support and training | Ensures smooth operation and issue resolution |
Customization | Ability to tailor systems to specific needs | Flexibility in brewing operations |
Pricing | Transparent pricing, no hidden costs | Budget management and financial planning |
Comparing Pros and Cons of Automated Beer Brewing Systems
As with any significant investment, it’s important to weigh the pros and cons of automated beer brewing systems before making a decision.
Advantages: Efficiency, Consistency, Scalability
One of the most significant advantages of automated brewing systems is the efficiency they bring to the brewing process. Automation reduces the need for manual intervention, allowing for more consistent results and freeing up time for other tasks. This consistency is crucial for maintaining the quality of your beer, especially if you’re brewing on a large scale.
Scalability is another key benefit. Automated systems can be easily expanded or modified to meet growing production needs, making them a good investment for breweries that plan to scale up their operations in the future.
Limitations: Initial Cost, Complexity, Potential for Over-Automation
Despite their many advantages, automated systems do have some limitations. The initial cost can be a significant barrier, especially for smaller breweries or homebrewers. These systems are also more complex than traditional brewing setups, requiring a higher level of technical knowledge to operate and maintain.
There’s also the potential for over-automation, where the process becomes so automated that it loses the human touch that many craft beer enthusiasts value. It’s important to find a balance between automation and hands-on brewing to ensure that the final product retains its character and uniqueness.
Pros and Cons of Automated Beer Brewing Systems
Pros | Cons |
---|---|
Increased efficiency and consistency in brewing | High initial investment required |
Scalability for growing production needs | Complexity in setup and operation |
Precision and control over brewing parameters | Possible reduction in manual creativity in brewing |
Improved safety and reduced labor requirements | Potential for over-reliance on automation, leading to issues |
Additional Considerations: Aesthetic and Perceived Quality
While the technical aspects of an automated brewing system are critical, the aesthetic appeal and perceived quality of the equipment can also play a role in your decision.
Impact of Design on Brand Perception
The design of your brewing equipment can influence how customers perceive your brand. Sleek, modern equipment can give your brewery a cutting-edge image, while more traditional designs might appeal to those who appreciate craftsmanship and heritage.
The Role of Aesthetic Appeal in Brewery Settings
In a brewery setting, especially one that is open to the public, the appearance of your equipment can contribute to the overall atmosphere. Well-designed, aesthetically pleasing equipment can enhance the customer experience and make your brewery a more attractive destination.
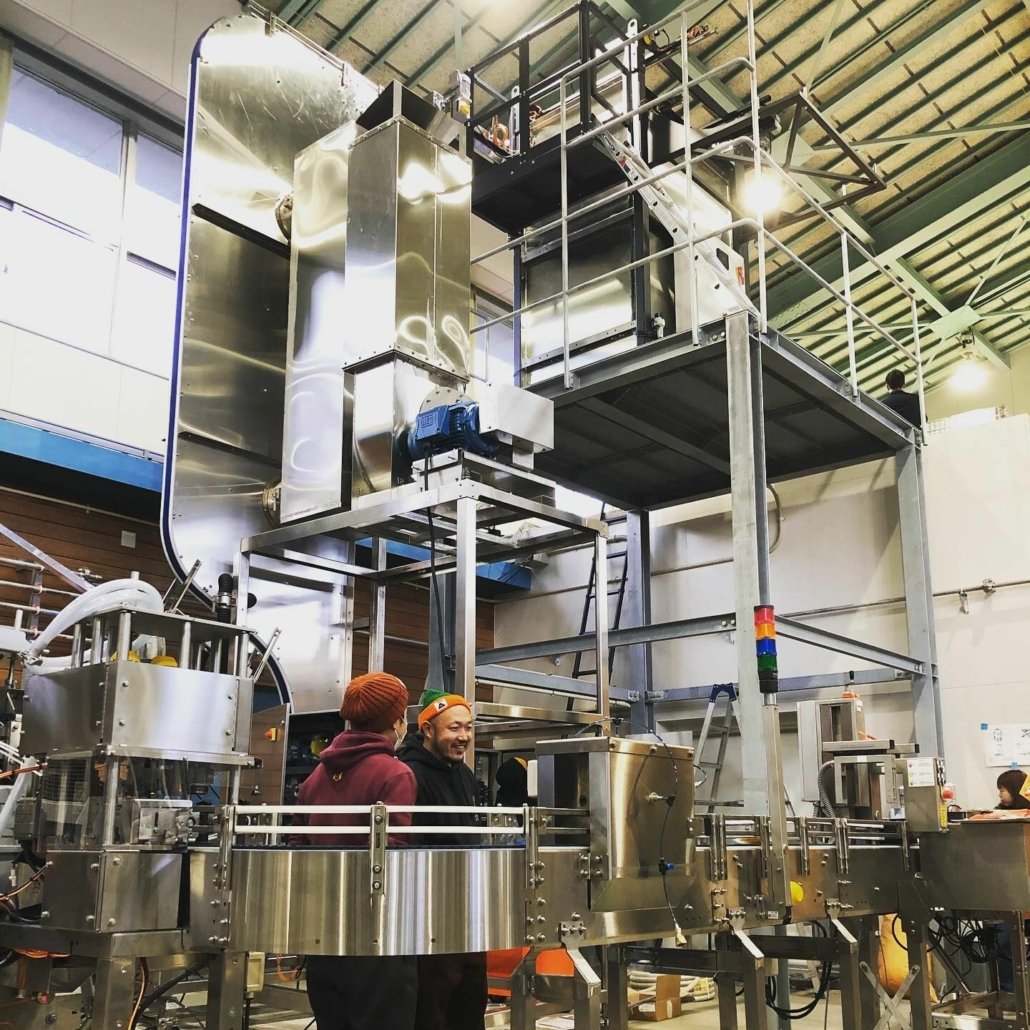
FAQs
To wrap up this comprehensive guide, here are some frequently asked questions about automated beer brewing systems:
What is an automated beer brewing system?
An automated beer brewing system is a setup that uses technology to control and monitor various stages of the beer brewing process. This includes tasks like mashing, boiling, cooling, and fermentation, which are typically managed by sensors, control panels, and software.
How does an automated brewing system work?
An automated brewing system works by integrating sensors and control panels that monitor and adjust brewing parameters like temperature, pressure, and timing. The system can be programmed to follow specific recipes, ensuring consistent results with minimal manual intervention.
What are the benefits of using an automated system?
The benefits of using an automated system include increased efficiency, consistency, and scalability. Automation also reduces the need for manual labor, enhances safety, and allows for more precise control over the brewing process.
How much does an automated beer brewing system cost?
The cost of an automated beer brewing system can vary widely depending on the size and features of the system. Prices typically range from $8,000 for small, basic setups to over $60,000 for large, advanced systems.
Can I customize my automated beer brewing system?
Yes, many suppliers offer customizable options for automated beer brewing systems. You can choose from different capacities, features, and configurations to meet your specific brewing needs.
Conclusion
Automated beer brewing systems represent a significant leap forward in brewing technology, offering a range of benefits that can help breweries of all sizes improve their efficiency, consistency, and scalability. While the initial investment and complexity may seem daunting, the long-term benefits often outweigh these challenges. By carefully selecting the right equipment, supplier, and system design, you can create a brewing setup that not only meets your current needs but also positions you for future growth.
Whether you’re a seasoned brewer looking to modernize your operations or a newcomer to the world of brewing, an automated system can be a valuable tool in your brewing arsenal. With the right approach, automation can help you produce high-quality beer more consistently and efficiently, allowing you to focus on what really matters—crafting great beer.
Share this entry
Interested in learning more about Brewing Systems including additional details and pricing information? Please use the form below to contact us!
YOLONG BREWERY EQUIPMENT FAQS
- Commercial Brewery / Craft Brewery / Microbrewery / Nanobrewery
- What is The Difference Between Craft Beer and Industrial Beer?
- The Bespoke Differences In Custom Brewing Systems
- Everything You Need to Know About Kettle Souring
- How to Choose Brewing Equipment for Your business?
- How To Choose The-Best Partner To Build Your Commercial Microbrewing System?
- Two Detection Sensors That You Need To Use In Your Brewhouse System
- Remote Control Applications in Brewing Equipment/How does it work?
- How To Clean Your Brand New Brewery Tanks?