Beer Filling Equipment
Beer brewing is an art that has evolved over centuries. As the demand for craft beers and large-scale beer production continues to grow, the need for efficient beer filling equipment becomes more crucial. Whether you’re a large brewery or a small craft brewer, understanding beer filling equipment can be a game-changer in improving production, minimizing waste, and increasing profitability.
In this guide, we’ll break down everything you need to know about beer filling equipment—from types, capacities, and brewing processes, to the design, customization, and maintenance required. So, let’s dive into the world of beer filling systems!
Overview of Beer Filling Equipment
Beer filling equipment refers to machinery designed to automate the process of packaging beer into containers such as bottles, cans, or kegs. The equipment ensures that the beer is filled efficiently, accurately, and hygienically. Choosing the right filling equipment can significantly impact the efficiency of your brewery, the quality of your beer, and the overall cost-effectiveness of your operations.
Beer filling systems come in various forms and sizes, each tailored to meet specific production needs—whether you’re running a large commercial brewery or a small artisanal operation. The critical factors to consider are filling speed, accuracy, space requirements, and cost.
Key Aspects to Consider
- Filling speed and accuracy: The speed of filling and precision plays a key role in meeting production targets while reducing waste.
- Types of beer packaging: The filling equipment must be compatible with the types of containers (bottles, cans, or kegs).
- Space and layout: The physical space required by the machine should fit within your brewery’s layout.
- Budget and customization: Equipment should be cost-effective and allow for customization to suit your unique production needs.
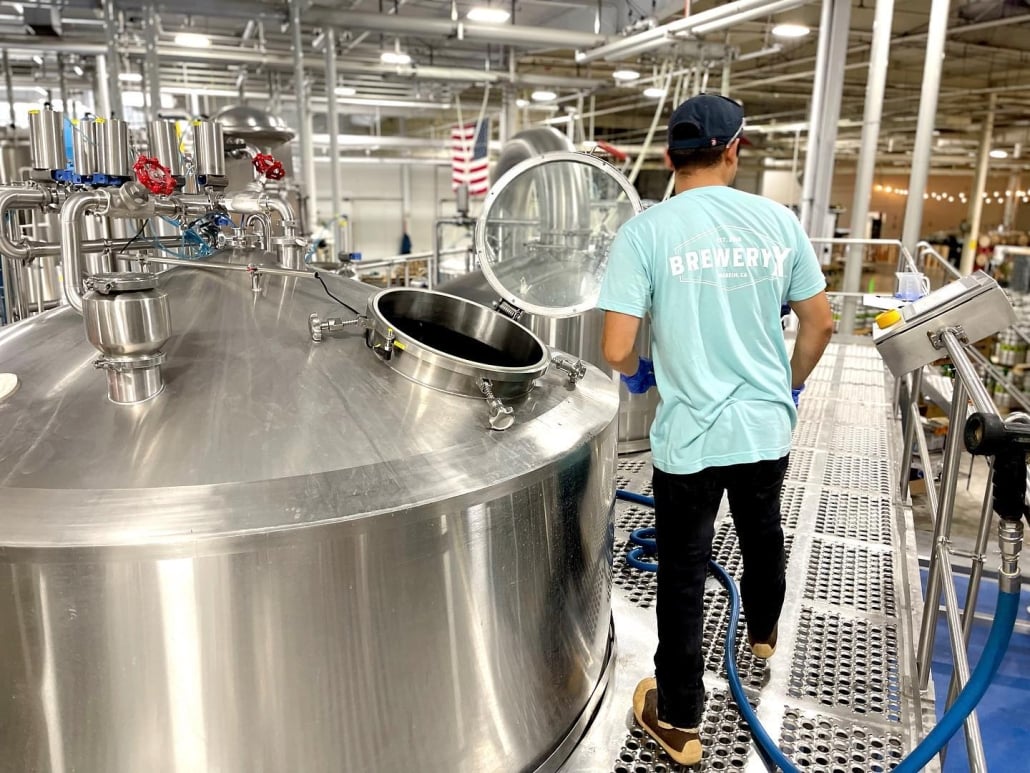
Types of Beer Filling Equipment
Beer filling machines come in a variety of styles, each designed to serve different needs and production scales. Below is a breakdown of the types of beer filling equipment commonly found in the brewing industry:
Type of Filling Equipment | Description | Application | Advantages | Disadvantages |
---|---|---|---|---|
Manual Filling Machines | Operated by hand, suitable for small batches and startups. | Small breweries, homebrewers. | Low cost, easy to operate, requires minimal space. | Slow, labor-intensive, less precise. |
Semi-Automatic Filling Machines | Combines manual input with automation. | Medium-sized breweries. | More efficient than manual, moderately priced. | Requires some manual oversight. |
Automatic Filling Machines | Fully automated system designed for high-speed production. | Large commercial breweries. | Fast, highly accurate, low labor cost. | Expensive, requires more space and maintenance. |
Counter Pressure Fillers | Designed to prevent loss of CO2, ideal for carbonated drinks. | Both small and large breweries. | Maintains carbonation, minimizes beer loss. | Complex to operate, more expensive. |
Isobaric Filling Machines | Works at equal pressure to preserve beer’s quality. | Medium to large breweries. | Ideal for canned and bottled beer. | High cost, requires trained operators. |
Beer Brewing Process Overview
The beer brewing process involves multiple stages, and beer filling is one of the final, yet crucial, steps. Let’s walk through the process from brewing to packaging.
1. Brewing
The brewing process starts by mixing malt, hops, and water to create wort, which is then boiled. Once the boiling process is complete, yeast is added to initiate fermentation. This is where the sugars are converted into alcohol, giving beer its unique character and flavor.
2. Fermentation
After brewing, the wort is fermented in large tanks, where it develops its alcohol content and carbonation. This process can take anywhere from a few days to several weeks, depending on the type of beer being produced.
3. Filtration
Before packaging, the beer is filtered to remove any residual yeast or unwanted particles. This ensures clarity and enhances the shelf life of the beer.
4. Filling and Packaging
Once filtered, the beer is ready to be filled into bottles, cans, or kegs. The filling process must be efficient and hygienic to maintain the beer’s quality and prevent contamination. Proper beer filling equipment ensures that this step is done seamlessly.
Capacity, Space, Design, and Customization of Beer Filling Equipment
Selecting the right beer filling equipment involves evaluating several factors such as capacity, available space, design preferences, and the level of customization required.
Factor | Details |
---|---|
Capacity | Beer filling machines come with various filling capacities, typically ranging from 500 bottles/cans per hour (for small setups) to over 10,000 bottles/cans per hour (for large commercial setups). Choose equipment that matches your production volume. |
Space Requirements | Ensure the machine fits within your brewery’s layout. Compact designs are available for smaller breweries, while larger equipment might require dedicated rooms. |
Design | The design of beer filling machines can range from simple manual fillers to sophisticated automated systems with ergonomic features. The choice depends on your brewery’s needs and aesthetic preferences. |
Customization | Many manufacturers offer customization options, allowing breweries to tailor the machine’s functionality to their specific production requirements, such as handling different container sizes, integrating with other systems, or adding branding features. |
Beer Filling Equipment Suppliers and Price Range
The cost of beer filling equipment varies based on the machine’s type, capacity, and features. Here is a general overview of prices and supplier options.
Supplier | Price Range | Features |
---|---|---|
CFT Group | $50,000 – $500,000+ | High-end automated systems, customizable, ideal for large breweries. |
Krones | $100,000 – $1,000,000+ | Fully automated, suitable for mass production, highly efficient. |
Wild Goose Filling | $15,000 – $200,000 | Specializes in canning lines, great for medium-sized breweries. |
XpressFill | $4,000 – $50,000 | Affordable manual and semi-automatic options, great for startups. |
IC Filling Systems | $20,000 – $300,000 | Offers both automatic and semi-automatic systems, known for flexibility and reliability. |
Installation, Operation, and Maintenance of Beer Filling Equipment
Once you’ve chosen the right beer filling equipment, understanding its installation, operation, and maintenance will ensure its longevity and smooth function.
Aspect | Details |
---|---|
Installation | Installation can vary depending on the machine type and complexity. Larger automatic machines typically require professional installation, while manual systems are easier to set up. It’s important to work with the supplier to ensure proper setup and training. |
Operation | Operating beer filling equipment can be straightforward for manual systems, but automated machines often require operator training. Efficient operation ensures faster production with minimal errors. |
Maintenance | Regular maintenance is key to avoiding breakdowns. Most manufacturers offer maintenance packages, and it’s essential to follow the equipment’s manual for routine cleaning, lubrication, and part replacements. Maintaining hygiene is also critical to preventing contamination. |
How to Choose the Right Beer Filling Equipment Supplier
Choosing the right supplier for your beer filling equipment is as important as selecting the equipment itself. Here’s a breakdown of how to make the right choice:
Criteria | Details |
---|---|
Reputation | Research the supplier’s reputation in the industry. Look for reviews, testimonials, and case studies from other breweries. |
Experience | A supplier with extensive experience in providing equipment for breweries will understand the unique challenges of the industry. |
Customization Options | Suppliers that offer customization can provide solutions tailored to your specific production needs. |
After-Sales Support | Ensure the supplier offers strong after-sales support, including installation, training, and maintenance services. |
Price vs. Value | Balance cost with the value offered. Cheaper isn’t always better if it compromises on quality or support. |
Advantages and Disadvantages of Beer Filling Equipment
When comparing different types of beer filling equipment, it’s essential to weigh their pros and cons to choose the best option for your brewery.
Type of Equipment | Advantages | Disadvantages |
---|---|---|
Manual Filling Machines | Low upfront cost, easy to maintain, good for small batches. | Slow, labor-intensive, not scalable. |
Semi-Automatic Machines | Faster than manual, more accurate, moderate cost. | Requires more space, needs some manual input. |
Automatic Filling Machines | High-speed production, minimal labor, extremely precise. | Expensive, complex to maintain, space-intensive. |
Counter Pressure Fillers | Maintains carbonation, reduces beer loss. | More complex to use, higher cost. |
Isobaric Fillers | Ideal for cans and bottles, preserves beer quality. | High price, requires trained staff. |
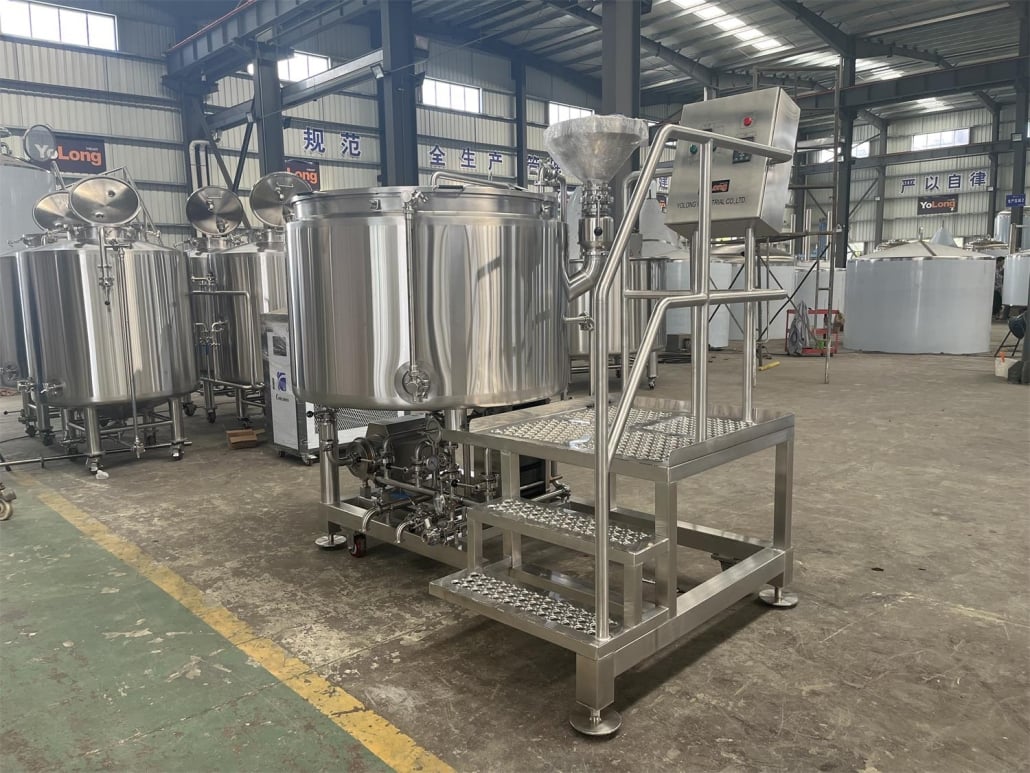
FAQs
Here are some common questions that brewers have about beer filling equipment, along with clear answers.
Question | Answer |
---|---|
What is the best filling machine for a small brewery? | Manual or semi-automatic fillers are usually sufficient for small breweries. They are cost-effective and easy to operate. |
How do I maintain hygiene in my filling equipment? | Regular cleaning with approved sanitizers, following the manufacturer’s maintenance guidelines,and ensuring the equipment is properly sealed to prevent contamination. |
What is counter-pressure filling? | Counter-pressure filling is a method that maintains the pressure inside the bottle or can to prevent beer from foaming, which helps preserve carbonation. |
How much does automatic filling equipment cost? | Prices can range from $50,000 to over $1,000,000 depending on capacity, automation level, and customization. |
Can I use the same filling machine for bottles and cans? | Some machines are designed to handle both bottles and cans, but you may need additional attachments or customizations. |
Conclusion
Choosing the right beer filling equipment is essential for any brewery’s success, whether you’re a large-scale operation or a small craft producer. The right machine can help boost efficiency, reduce costs, and maintain the quality of your beer. From understanding the types of filling equipment available, evaluating capacity and customization, to knowing how to maintain and operate your system—this guide provides the foundational knowledge you need to make an informed decision.