The Ultimate Guide to Beer Canning Equipment
Overview of Beer Canning Equipment
Canning beer is an essential part of the brewing process, ensuring that your carefully crafted brews reach your audience in the freshest and most convenient form possible. Whether you’re a small craft brewer or a larger brewery, the right beer canning equipment can significantly influence your product’s quality, shelf life, and overall market appeal.
But why is beer canning so important? And how do you choose the right equipment? This guide dives deep into the world of beer canning, offering you a detailed exploration of the machinery, processes, and considerations involved in setting up or optimizing your canning line.
We’ll take you through everything from understanding the basics of beer canning equipment to selecting the perfect machinery for your brewing needs, ensuring your investment is wise and your cans are top-notch. So, grab a cold one and let’s get started!
Understanding the Importance of Beer Canning
Beer canning is more than just putting your beer into a metal container. It’s about preserving the flavor, aroma, and carbonation of your brew while providing a convenient packaging option that appeals to a broad market. Canned beer offers excellent protection against light and oxygen, two of the biggest enemies of beer quality. Moreover, cans are lighter, more environmentally friendly, and offer a larger canvas for branding compared to bottles.
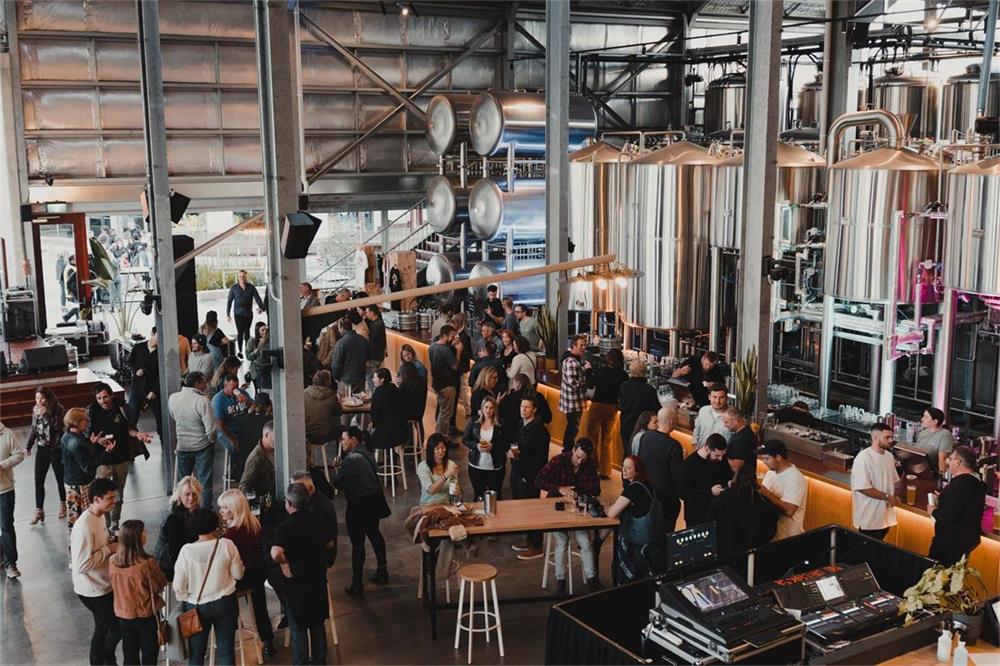
Types of Beer Canning Equipment
When setting up your canning line, you’ll encounter several types of equipment, each designed to handle different aspects of the process. Below is a detailed table outlining the various equipment types, their functions, and the considerations for each.
Equipment Type | Function | Key Considerations |
---|---|---|
Depalletizer | Automatically unloads cans from pallets and feeds them into the line. | Speed, compatibility with can sizes, ease of integration. |
Rinse Cage | Cleans cans before filling to ensure sanitation. | Water efficiency, cleaning effectiveness, maintenance needs. |
Filler | Fills cans with beer while minimizing oxygen intake. | Fill accuracy, oxygen control, speed, compatibility with can sizes. |
Seamer | Seals the can lid after filling to prevent contamination. | Seaming quality, speed, ease of operation and maintenance. |
Labeler | Applies labels to the cans for branding. | Labeling accuracy, flexibility for different label sizes, speed. |
Date Coder | Prints production dates or batch numbers on cans. | Print clarity, speed, compatibility with canning line. |
Paktech Applicator | Applies plastic handles or carriers to multiple cans for easy transport. | Speed, compatibility with different can sizes, ease of operation. |
Palletizer | Stacks finished cans onto pallets for distribution. | Stacking precision, speed, ease of use, compatibility with different pallet sizes. |
Detailed Beer Canning Process
Now that we’ve covered the equipment, let’s walk through the beer canning process from start to finish.
- Depalletizing and Rinsing: The process begins with depalletizing, where cans are unloaded from pallets and fed into the production line. They then enter the rinse cage to ensure any dust or contaminants are washed away, preparing them for filling.
- Filling and Seaming: After rinsing, the cans move to the filler. This is where your beer enters the cans, with precise control to ensure consistency in fill levels and minimize oxygen exposure. Immediately after filling, the cans proceed to the seamer, where lids are applied and sealed tightly to prevent contamination and maintain freshness.
- Labeling and Coding: Once sealed, the cans pass through the labeler, where your brand’s labels are applied with precision. Following this, the date coder adds essential information like production dates or batch numbers, crucial for quality control and traceability.
- Packing and Palletizing: Finally, the cans are grouped together using a Paktech applicator or similar device, and then palletized for shipping. The palletizer neatly stacks the cans on pallets, ready for distribution.
Brewing Capacity, Space, and Customization
When choosing your beer canning equipment, it’s essential to consider the capacity, the space available in your brewery, and the level of customization you might need. The table below outlines these considerations in detail.
Consideration | Details |
---|---|
Capacity | Equipment comes in various capacities, from small-scale machines handling a few hundred cans per hour to large systems capable of processing thousands. Choose based on your production volume. |
Space Requirements | Ensure your brewery has enough space to accommodate the canning line, considering both the footprint of the equipment and space for operators. |
Customization Options | Many manufacturers offer customization to tailor the canning line to your specific needs, such as can size flexibility or integration with existing equipment. |
Supplier and Price Range Overview
Selecting a supplier for your beer canning equipment is a significant decision. Below is a table summarizing key suppliers and their price ranges to help you make an informed choice.
Supplier | Price Range | Notable Features |
---|---|---|
Wild Goose Filling | $150,000 – $500,000 | Known for high-quality, reliable canning systems, excellent for craft breweries. |
Codi Manufacturing | $100,000 – $400,000 | Offers modular systems that are easy to scale as your brewery grows. |
Pneumatic Scale Angelus | $200,000 – $1,000,000 | Premium equipment with advanced automation features, ideal for larger operations. |
XpressFill | $20,000 – $50,000 | Affordable, entry-level systems suitable for small craft brewers. |
Installation, Operation, and Maintenance
Once you’ve selected your equipment, understanding the installation, operation, and maintenance requirements is crucial to ensure smooth and efficient operation.
Aspect | Details |
---|---|
Installation | Professional installation is recommended to ensure proper setup and integration with existing systems. Costs can vary depending on complexity and location. |
Operation | Training your staff on operating the equipment is essential. Look for systems with user-friendly interfaces and robust support from the supplier. |
Maintenance | Regular maintenance is necessary to keep the equipment running smoothly. This includes cleaning, lubrication, and periodic checks on critical components like the seamer. Most suppliers offer maintenance contracts. |
How to Choose the Right Beer Canning Equipment Supplier
Selecting the right supplier for your beer canning equipment can be the difference between seamless production and constant headaches. Consider the following factors when making your decision:
Factor | Importance |
---|---|
Reputation | Look for suppliers with a solid reputation in the industry. This can often be gauged by customer testimonials, industry awards, and longevity in the market. |
Support and Service | A good supplier offers excellent after-sales support, including training, maintenance, and readily available spare parts. |
Customization Capabilities | If your brewery has unique needs, a supplier who can customize equipment to your specifications will be invaluable. |
Price vs. Value | While price is important, it’s crucial to balance cost with the value offered by the equipment. Cheaper systems might save money upfront but could cost more in downtime and repairs over time. |
Warranty and Guarantees | Ensure the supplier provides a solid warranty, as this indicates confidence in their equipment’s durability and performance. |
Comparing Advantages and Limitations of Beer Canning Equipment
When choosing equipment, it’s essential to weigh the pros and cons to make the best decision for your brewery. Here’s a comparison of key factors:
Aspect | Advantages | Limitations |
---|---|---|
Cans vs. Bottles | Cans are more environmentally friendly, lighter, and protect beer better from light and oxygen. | Bottles may be perceived as more premium by some consumers, but they are heavier and breakable. |
Automation vs. Manual Systems | Automated systems increase efficiency, consistency, and reduce labor costs. | Higher upfront costs, more complex maintenance, and less flexibility for small batches. |
Size Flexibility | Equipment that can handle multiple can sizes offers greater flexibility for different products. | More expensive and complex to set up and switch between sizes. |
Space Requirements | Compact systems save valuable brewery space and can be more cost-effective. | May have lower capacity or require more frequent maintenance. |
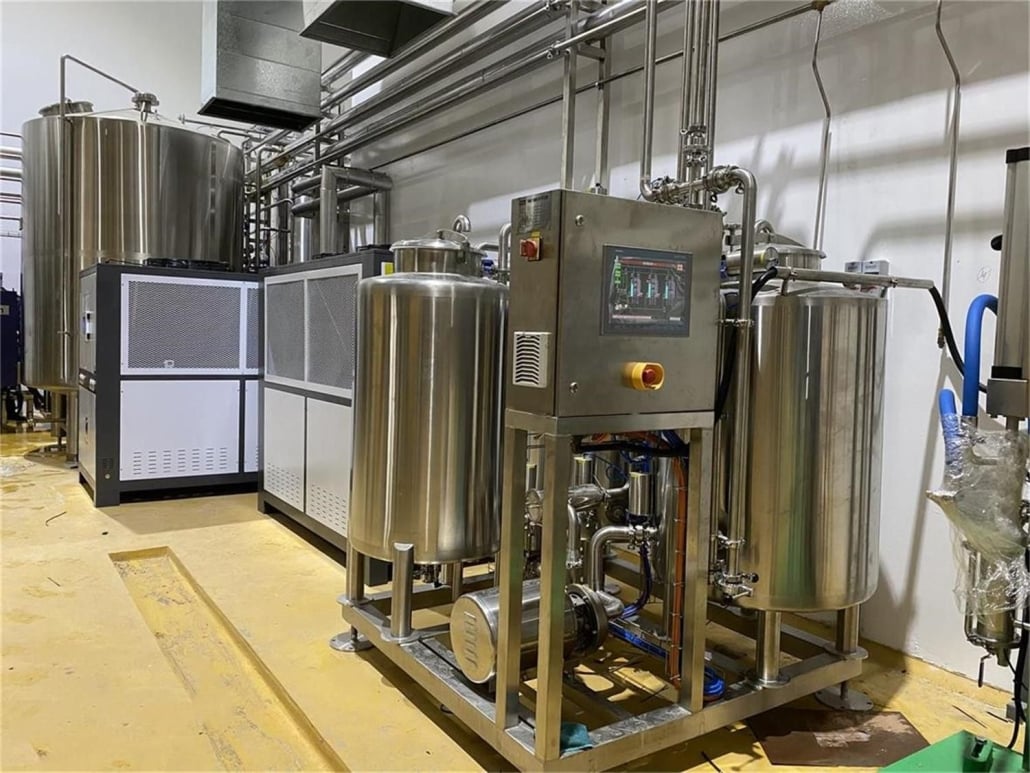
FAQ
Question | Answer |
---|---|
What is the most critical piece of equipment in a canning line? | The filler and seamer are arguably the most critical, as they directly affect the quality and integrity of the canned beer. |
How much does a small-scale canning line cost? | Prices can start as low as $20,000 for basic setups and can go up depending on capacity and features. |
How often should canning equipment be serviced? | Regular maintenance should be performed weekly, with more extensive checks monthly or quarterly, depending on usage. |
Can I customize can sizes with my equipment? | Yes, many canning lines offer flexibility in can sizes, but this may require additional investment in adaptable machinery. |