Nano Brewery Equipment
Starting your own nano brewery can be an exciting venture, blending passion with business in the realm of craft beer. But what exactly do you need to get started? Let’s dive into the world of nano brewery equipment, exploring every facet from the types of equipment you’ll need, the brewing process, and what to consider when choosing suppliers.
Overview of Nano Brewery Equipment
Nano breweries are small-scale brewing operations typically producing batches of beer one to three barrels at a time. This section provides an overview of the essential equipment required to set up a nano brewery, the brewing process, and practical considerations for space, design, and customization.
Essential Nano Brewery Equipment Guide
To kick things off, let’s explore the critical pieces of equipment you’ll need to start brewing.
Brewing System
At the heart of any brewery is the brewing system. This includes:
- Mash Tun: A vessel where the malt is mixed with hot water to convert starches into fermentable sugars.
- Lauter Tun: Used to separate the spent grains from the wort.
- Boil Kettle: Where the wort is boiled and hops are added.
- Whirlpool: Helps in the removal of hop residues and other solids.
- Fermenters: Vessels where wort is fermented to produce beer.
- Brite Tanks: Used for carbonation and aging the beer before packaging.
Additional Equipment
In addition to the core brewing system, you’ll need several other pieces of equipment:
- Hot Liquor Tank (HLT): Holds hot water for brewing processes.
- Cold Liquor Tank (CLT): Stores chilled water for cooling wort.
- Heat Exchanger: Cools wort after boiling.
- Glycol Chiller: Maintains the temperature of fermentation tanks.
- Kegs and Bottling Equipment: For packaging the beer.
Equipment Types and Specifications
Here’s a detailed table summarizing different equipment types and their specifications:
Equipment Type | Description | Key Specifications |
---|---|---|
Mash Tun | Vessel for mashing grains | Capacity, material, insulation |
Lauter Tun | Separates wort from grains | Capacity, false bottom design |
Boil Kettle | Boiling wort with hops | Volume, heating method |
Whirlpool | Clarifies wort post-boil | Volume, inlet design |
Fermenters | Fermentation of wort | Capacity, cooling jackets, shape |
Brite Tanks | Carbonation and aging | Capacity, pressure rating |
HLT | Stores hot water | Volume, insulation |
CLT | Stores cold water | Volume, cooling method |
Heat Exchanger | Cools wort rapidly | Plate design, cooling efficiency |
Glycol Chiller | Maintains tank temps | BTU rating, temperature range |
Kegs/Bottling | Packaging beer | Size, material, closure type |
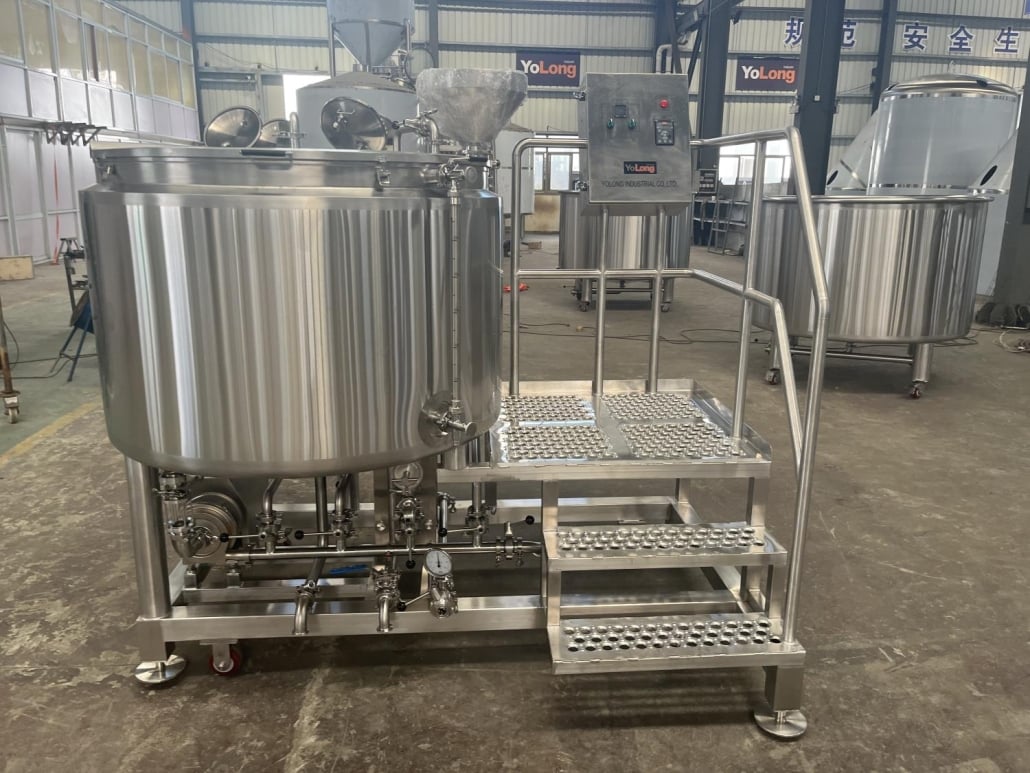
The Brewing Process Explained
Understanding the brewing process is crucial for anyone venturing into the craft beer industry. Here’s a detailed look at each step.
Mashing
Mashing involves mixing milled grains with hot water in the mash tun. This process activates enzymes that convert starches into fermentable sugars. Temperature control is essential, typically maintained around 65°C (149°F).
Lautering
After mashing, the mixture is transferred to the lauter tun. Here, the wort is separated from the spent grains. The wort is then rinsed (sparged) with hot water to extract additional sugars.
Boiling
The wort is moved to the boil kettle, where it is boiled for around 60-90 minutes. Hops are added at various stages to impart bitterness, flavor, and aroma. This step also sterilizes the wort.
Whirlpooling
Post-boil, the wort is rapidly cooled in a whirlpool tank, which helps remove hop particles and other solids. This step is crucial for achieving a clear beer.
Fermentation
The cooled wort is transferred to fermenters, where yeast is added. Fermentation typically lasts from one to three weeks, depending on the beer style. Yeast converts sugars into alcohol and carbon dioxide, producing beer.
Conditioning
After fermentation, the beer is conditioned in brite tanks. This step can involve carbonation and aging to enhance flavor profiles.
Packaging
Finally, the beer is packaged into kegs, bottles, or cans. Proper packaging is essential for preserving quality and extending shelf life.
Considerations for Capacity, Space, Design, and Customization
Setting up a nano brewery involves more than just equipment. Here’s a table summarizing key considerations for capacity, space, design, and customization:
Aspect | Details | Considerations |
---|---|---|
Capacity | Total volume of beer produced per batch | Match production goals, balance with market demand |
Space | Physical area required for equipment and operations | Optimize layout, ensure compliance with regulations |
Design | Layout of brewing equipment and flow of brewing process | Efficiency, ease of use, workflow optimization |
Customization | Ability to modify equipment to suit specific brewing needs | Flexibility for diverse beer styles, scalability |
Suppliers and Price Range
Choosing the right suppliers is critical for quality and cost-effectiveness. Here’s a table with some reputable suppliers and their price ranges:
Supplier | Equipment Offered | Price Range (USD) |
---|---|---|
BrewBilt | Complete brewing systems, fermenters | $50,000 – $150,000 |
Stout Tanks | Fermenters, brite tanks, brewing systems | $30,000 – $100,000 |
Ss Brewtech | Home and professional brewing equipment | $10,000 – $80,000 |
Spike Brewing | Customizable brewing systems | $20,000 – $120,000 |
Blichmann | Pilot and nano brewing systems | $15,000 – $90,000 |
Installation, Operation, and Maintenance
Proper installation, operation, and maintenance of your brewing equipment are crucial for consistent beer quality and equipment longevity. Here’s a table detailing these aspects:
Aspect | Details | Considerations |
---|---|---|
Installation | Setting up brewing equipment, connecting utilities | Professional installation recommended, permits |
Operation | Daily use of brewing equipment | Training for staff, standard operating procedures |
Maintenance | Regular cleaning, servicing, and repairs | Scheduled maintenance, spare parts availability |
Choosing the Right Supplier
Selecting a supplier can be daunting. Here’s a table to help you make an informed decision:
Criteria | Details | Considerations |
---|---|---|
Reputation | Supplier’s standing in the industry | Reviews, testimonials, industry awards |
Product Quality | Materials and craftsmanship of equipment | Durability, warranty, certifications |
Customer Service | Responsiveness and support provided by supplier | Training, technical support, after-sales service |
Price | Cost of equipment and installation | Value for money, financing options |
Customization Options | Ability to modify equipment for specific needs | Flexibility, bespoke solutions |
Delivery and Lead Time | Time taken to deliver and install equipment | Project timelines, reliability |
Comparing Pros and Cons of Nano Brewery Equipment
When choosing nano brewery equipment, consider the advantages and limitations. Here’s a comparative table:
Aspect | Advantages | Limitations |
---|---|---|
Cost | Lower initial investment compared to larger systems | May require upgrades as production scales up |
Space | Requires less physical space | Limited expansion options in small spaces |
Flexibility | Easier to experiment with new recipes and small batches | May struggle to meet high demand |
Maintenance | Easier to maintain and clean | Regular upkeep needed to avoid downtime |
Scalability | Can start small and expand gradually | Scaling up might require significant reinvestment |
How to Choose a Nano Brewery Equipment Supplier
Selecting the right supplier is pivotal for the success of your brewery. Here’s a table summarizing key factors to consider:
Factor | Description | Importance |
---|---|---|
Experience | Supplier’s history and expertise in the brewing industry | Ensures reliability and industry knowledge |
Quality Assurance | Guarantees on product quality and performance | Prevents future issues, assures long-term reliability |
Customization | Ability to tailor equipment to specific brewing needs | Facilitates unique brewing processes and recipes |
Customer Feedback | Reviews and ratings from previous clients | Provides insights into supplier’s reputation |
Support Services | Availability of technical support and maintenance services | Essential for troubleshooting and ongoing operations |
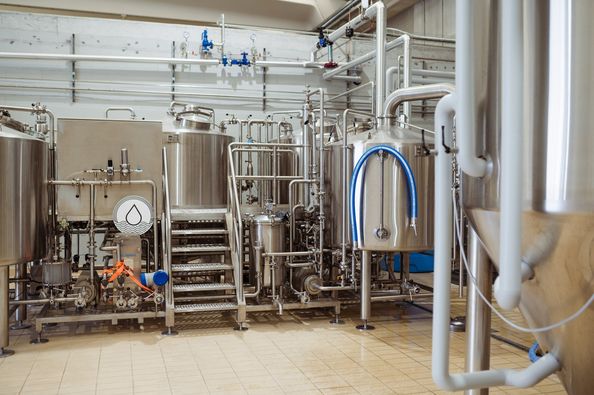
FAQ
What is Nano Brewery Equipment?
Nano brewery equipment consists of small-scale brewing systems typically producing 1-3 barrels per batch.
How does it differ from microbrewery equipment?
Nano breweries produce smaller batches compared to microbreweries, offering more flexibility for experimentation.
What is the cost range for nano brewery equipment?
Prices range from $10,000 to $150,000 depending on the equipment quality and scale.
What factors influence the cost?
Capacity, material quality, customization options, and supplier reputation all impact the cost.
What are the advantages of nano brewery equipment?
Lower initial investment, smaller space requirements, and greater flexibility for brewing different beer styles.
How often should nano brewery equipment be maintained?
Regular cleaning after each use and scheduled maintenance every few months are recommended.
What are common maintenance tasks?
Cleaning fermenters, checking seals, servicing pumps, and calibrating sensors are common tasks.
What should I look for in a supplier?
Consider reputation, product quality, customer service, and customization options.
How can I compare suppliers?
Read reviews, request quotes, visit facilities, and speak to other brewers who have used their equipment.
Conclusion
Starting a nano brewery is a journey filled with excitement, challenges, and endless possibilities. By choosing the right equipment and suppliers, understanding the brewing process, and considering practical aspects like space and maintenance, you can set the foundation for a successful craft brewery. Remember, the key is to balance quality and cost, ensuring you have the flexibility to create the unique brews that will set your brewery apart. Cheers to your brewing success!