Overview of 20 BBL Brite Tanks
A 20 BBL Brite Tank is a critical finishing and storage vessel used after fermentation to condition and clarify craft beer in a professional brewhouse. Brite tanks prepare crystal clear beer for packaging and distribution while allowing natural carbonation.
With a 20 BBL capacity, brite tanks at this scale integrate smoothly with typical microbrewery fermenter volumes. A sufficient number of these vessels provides flexibility for production planning, storage and tapping. Well-designed brite tanks ensure consistent beer quality, stability and process efficiency.
20 BBL Brite Tank Equipment Guide
20 BBL brite tanks are pressurized stainless steel vessels featuring:
Parts | Description |
---|---|
Tank body | Cone or cylinder shape. Stackable for smaller footprint. Insulated and double jacketed. |
Cooling system | Glycol chilling or integrated cooling jacket. Precise temp control. |
Sight glass | View beer line and clarity. |
Pressure rated manways | Enter tank interior for cleaning. |
Butterfly or racking valve | Move liquid out to packaging or dispensing lines. |
CIP sprayball | Clean-in-place automated spray system. |
CO2 regulation | Carbonation stone or lance adds bubbles under pressure. |
Flow control | Consistent, smooth transfer of beer. |
LCD display | Touchscreen shows tank parameters – temp, pressure etc |
Probe ports | Measures realtime beer conditions. |
Legs and plumbing | Connections for gas, glycol, beer, CIP. |
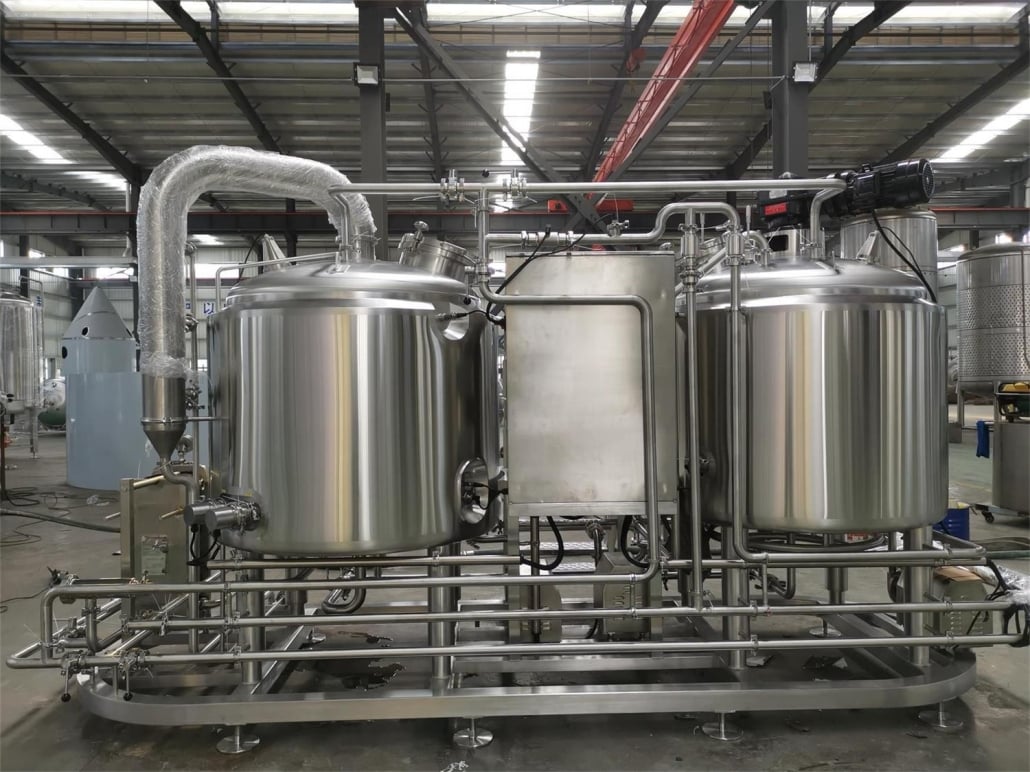
Types of 20 BBL Brite Tank Styles
20 BBL brite tanks have different design aspects to suit quality goals:
Type | Description |
---|---|
Cylindrical | Most common shape, stackable for smaller footprint. Balances volume and pressure rating. |
Conical bottom | Cone slope allows sediment to settle for clearer beer. Takes more vertical space. |
Horizontal | Long tanks placed side-by-side save headroom. Limit stacking. Better dry hopping. |
Open top | Allows easy fruit or dry hop additions. Risk of contamination. |
Closed top | Added sanitary and pressurized manway lid. Reduces oxygen intake. |
Uni-tank | Combined fermenting and conditioning in one tank. Flexibility to crash cool. |
Dual use | Designed to also function as fermenter if needed. Saves cost. |
Purpose and Function in Brewing Process
In commercial beer production, brite tanks provide vital post-fermentation processing:
- Beer transfer – Fresh beer is moved from fermenters into brite tanks after initial fermentation ends.
- Clarifying – Proteins and yeast settle out as beer rests cold, becoming brilliantly clear. Finings can accelerate clearing.
- Carbonating – CO2 injection under pressure dissolves bubbles. Critical for taste.
- Cold conditioning – Extended 1-6 week cold storage matures flavor compounds.
- Buffer holding – Staged inventory available for packaging, tapping or troubleshooting.
- Blending – Combine batches to achieve target qualities before releasing.
Well-managed 20 BBL brite tanks are vital for consistent brewing quality, flexibility and efficiency.
20 BBL Brite Tank Design and Layout
Optimally designing a brite tank farm requires balancing capacity, space and flexibility:
Sizing and Capacity Parameters
Details | Recommendations |
---|---|
Quantity | ≥ 2 tanks; 4+ ideal |
Individual size | 20 BBL in line with brewhouse batch volume |
Height-to-diameter ratio | 2:1 to 3:1 for conical bottom tanks |
Combined capacity | ≥ brewhouse capacity for needed buffer |
Headspace | 20-25% for dry hopping or fruit |
Facility Layout and Placement
Brite tanks need proper spacing and infrastructure:
- Close proximity to fermenters
- Accessible but low-traffic area
- Sufficient ceiling clearance
- Space between tanks for mobile operations
- Floor sloped to trench drains
- Glycol or cooling systems
- CO2 lines and tank manifolds
- Outlets to bottling or canning lines
Flexibility and Customization
20 BBL brite tanks allow options like:
- Variable pressure ratings
- Mobility: stationary or movable
- Material: stainless steel grade and finish
- Automated monitoring and controls
- Integrated labeling or date coding
- CIP configurations and sloped tank bottoms
- Special coatings like ceramic or enamel
Within infrastructure constraints, custom options address expanded needs.
Popular 20 BBL Brite Tank Manufacturers & Pricing
There are many reputable brite tank fabricators to choose from:
Company | Price Range | Offerings |
---|---|---|
JV Northwest | $25,000 – $60,000 | American made all stainless tanks with 5-year warranty |
Premier Stainless | $22,000 – $50,000 | Budget and custom tanks |
AAA Metal Fabrication | $30,000 – $65,000 | Display tanks with logos or finishes |
Pro Refrigeration | $28,000 – $55,000 | Cooling integrated or glycol systems |
Superior Tank | $35,000 – $70,000 | Custom etching and innovative features |
Pricing varies based on size, thickness, valves, branding and accessory options chosen. Best to get quotes tailored to exact specifications required.
20 BBL Brite Tank Installation, Operation and Maintenance
Proper brite tank setup and care ensures quality beer production:
Stage | Details |
---|---|
Installation | Floor anchoring, plumbing, glycol and CO2 line connections by experts |
Commissioning | Test under pressure, calibrate monitors, tune carbonation rates |
Initial use | Thoroughly CIP and passivate before filling |
Operation | Follow SOPs for transferring, carb levels, clarifying duration etc |
Cleaning | CIP sprayballs to sanitize interior regularly; exterior wipe downs |
Maintenance | Preventative – gaskets, valves, seals on schedule |
Safety | Pressure release valves, airlocks, emergency venting |
Work closely with manufacturers for installation guidance, safety procedures and maintenance best practices.
How to Select a 20 BBL Brite Tank Manufacturer
Vet potential suppliers using this criteria before purchasing:
Factor | Evaluation Aspects |
---|---|
Build quality | Durable 1.5-2 mm stainless steel grade, precise welds, quality parts |
Feature set | Needs-match for glycol, automation, wheel kits etc |
Customization | Ability to tailor tank size, fittings, accessories |
Experience | Proven reputation building brewhouse scale brite tanks |
Safety record | Pressure certification, quality inspections, safety focus |
Services | Responsive support for technical queries and issues |
Value | Price fairness for quality manufacturing |
Fully defining needs and comparing vendor capabilities lead to ideal 20 BBL brite tank selection.
The Pros and Cons of 20 BBL Brite Tanks
Advantages
- Flexible volume aligns with common microbrewery batch size
- Enables consistent finishing process compared to ferment-only
- Buffers variation between batches
- Smaller footprint than massive storage tanks
- Lower capital cost than oversized units
- Allows specialty treatments – fruit, dry hop
Disadvantages
- Multiple units take up more combined space
- Additional cleaning and process management needed
- Cooling, CO2 systems add infrastructure complexity
- Bottleneck if insufficient tanks for fermented beer
- Requires precise process control for clarity and taste
For professional scale breweries, the significant advantages of dedicated 20 BBL brite tanks make them indispensable.
Comparing Stainless Steel vs. Enamel-Lined Brite Tanks
Key performance differences:
Parameter | Stainless Steel | Enamel-Lined |
---|---|---|
Durability | Extremely durable finish | Prone to chipping over time |
Cleaning | Easy interior access | Seamless hygienic surface |
Cost | Lower material cost | Enameling adds expense |
Repairability | Weldable | Difficult to patch enamel |
Aesthetics | Industrial look | Glossy colored appearance |
While enameling looks attractive, stainless steel brite tanks offer better value and performance for serious brewers.
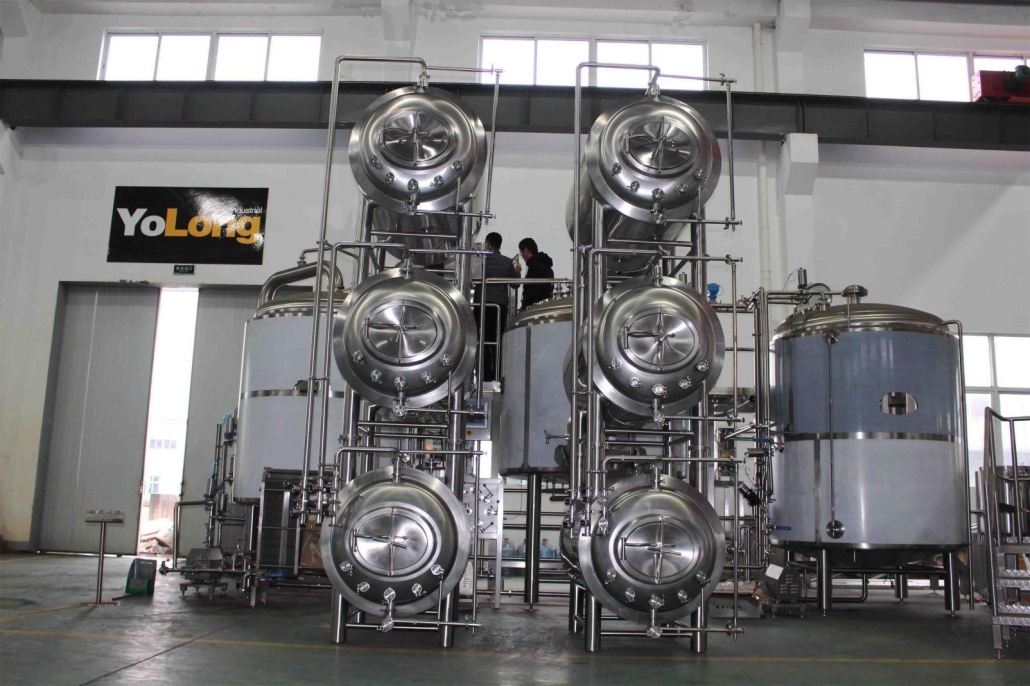
FAQ
What is the purpose of a brite tank?
Brite tanks provide vital post-fermentation processing to condition and clarify beer including settling out yeast, aerating dissloved CO2, stabilizing flavor compounds, and preparing bright clear beer for serving or packaging.
Why are they called brite tanks?
“Brite” refers to brilliantly clear beer achieved through cold conditioning in these tanks. They make beer sparkling bright through settling and chilling before serving.
How many brite tanks do I need?
Commercial guidelines recommend a minimum of 2 brite tanks, with additional units as buffer capacity allows. Ideally have enough brite volume to exceed total fermentation capacity. For a 20 BBL brewhouse, plan for 4-6 x 20 BBL brite tanks.
What is the difference between a uni and brite tank?
- Uni-tanks combine fermenting and conditioning in one vessel with temperature control. Braggots use single uni-tanks.
- Brite tanks are dedicated to cold clarifying and carbonating after initial fermentation elsewhere. Lager breweries often use separate fermenters and brite tanks.
Can you ferment in a brite tank?
While brite tanks are designed for finishing beer, in a pinch they can be used for primary fermentation if thoroughly cleaned and sanitized. Their temperature control and CO2 injection allows this flexibility. But best to use dedicated fermenters when possible.
What temperature is a brite tank kept at?
Brite tanks are kept chilled at 33-40°F to clarify and stabilize beer, which is cooler than active fermentation temperatures. Precise thermal control is maintained using integrated cooling jackets or glycol systems.