9 Gallon Hop Backs
A 9 gallon hop back is a piece of brewing equipment used by homebrewers and craft breweries to add flavor and aroma to beer by infusing it with hops. The hop back fits inline after the brew kettle and before fermentation, acting as a filter to remove hop particulates while transferring hot wort.
9 gallon hop backs provide homebrewers with a customizable and scalable option to experiment with hopping rates and varieties for more flavorful beers. They come in stainless steel or plastic constructions with various design aspects to consider like number of compartments, ease of cleaning, durability, etc. Proper installation and maintenance is key to preventing clogs and keeping fresh hop aromas.
9 Gallon Hop Back Equipment Guide
Type | Description |
---|---|
Stainless Steel | Long lasting and easy to clean stainless construction |
Plastic | Food safe plastic hop back, more economical option |
Single Chamber | One compartment for hops |
Double/Triple Chamber | Multiple sections to separate hop varieties |
Rotating Design | Rotating core helps prevent clogging |
Removable Screen | Screen slides out for easy cleaning |
Brewing Process with Hop Back
The 9 gallon hop back is placed between the brew kettle and fermenter, in line while transferring hot wort. As wort passes through the hop chambers, essential oils and aromas are absorbed but hop particulates are filtered out. The process infuses great flavor and aroma into the beer without transferring debris into fermentation. Flow rate and hop quantity can be adjusted to fine tune saturation levels.
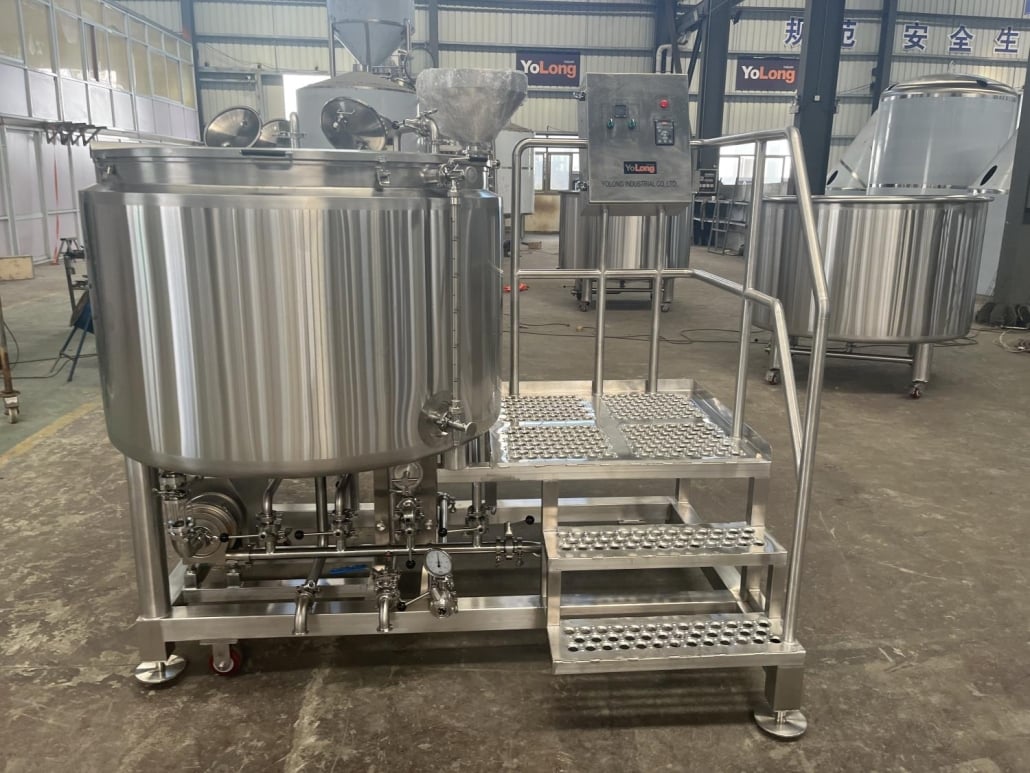
Key Specifications
Parameter | Options |
---|---|
Capacity | 5-10 gallons |
Construction | Stainless Steel, Plastic (HDPE, PP) |
Chambers | Single, Double, Triple |
Screen | Stainless steel or nylon |
Seal | Silicone gasket |
Dimensions | 10-14 inch diameter, 15-25 inch height |
Flow Rate | 1-2 GPM |
Pressure Rating | 60 psi max |
Installation | Inline with 1/2″ or 3/4″ tri-clover fittings |
Customization
Many 9 gallon hop back manufacturers offer full customization options. Brewers can choose number of chambers, connection type and size, construction material, screen type, and dimensions to meet their specific needs. Having a hop back tailored to the brew system and desired beer styles allows dialing in the perfect hop saturation.
Suppliers and Price Range
Brand | Price Range |
---|---|
SS Brewtech | $350-$500 |
Spike Brewing | $450-$600 |
Blichmann | $375-$475 |
MoreBeer | $300-$400 |
Choosing a Supplier
Consider lead time, budget, brand reputation, customization options and after sales support when selecting a hop back supplier. Leading homebrew brands like SS Brewtech, Spike and Blichmann offer high end constructions with maximum customizability. MoreBeer provides more economic options better suited to first-time buyers.
Installation, Operation and Maintenance
Process | Guidelines |
---|---|
Installation | Connect inline between kettle and fermenter with liquid out post on kettle. Clamp securely using tri-clover fittings with gaskets to prevent leaks. |
Filling | Add 0.5 to 1 oz hops per gallon based on desired saturation. Fill all chambers evenly for proper diffusion. |
Flow Rate | 1-2 GPM optimal for absorption without clogging. |
Cleaning | Disassemble and clean with PBW after each use. Soak removable parts in caustic solution if needed. |
Maintenance | Periodically inspect screen for tears and gaskets for wear. Replace damaged parts immediately. |
Choosing the Right Model
Consider the brew batch size, number of hop varieties, ease of operation, and maintenance requirements when selecting a 9 gallon hop back model. Brewers wanting the flexibility to design recipes with hop blends should opt for double or triple chamber designs despite the higher cost. Those focused on minimizing equipment cleaning may prefer plastic construction or removable stainless screens. Often a single chamber hop back meets the needs of most homebrewers.
Pros and Cons of 9 Gallon Hop Backs
Pros | Cons |
---|---|
Adds fresh hop aroma for flavorful beers | Requires careful cleaning to prevent clogs |
Customize hopping rates and varieties | More expensive than whole hops in fermenter |
Filters hop debris from transferring wort | Limited contact time versus hop stands |
Easy to install inline with existing system | Potential for stuck sparges if not properly maintained |
Scalable solution as batch sizes grow | Additional equipment expense for small brewers |
FAQ
Q: What are the benefits of a hop back versus dry hopping?
A: Hop backs provide hop aroma and flavor while filtering vegetative hop matter. The process lowers the risk of grassy flavors and clogs associated with dry hopping in fermenters or kegs.
Q: Can a hop back be used for cold side hopping?
A: No, hop backs are only effective for hot side hopping when transferring hot wort between the kettle and fermenter. Cold wort does not properly dissolve the hop oils.
Q: How many pounds of hops are needed per batch?
A: As a general rule of thumb, use 0.5 to 1 ounce of hops per gallon of wort when filling the hop back chambers. Adjust up or down to taste.
Q: Should hops be bagged or loose inside the chambers?
A: Flow will be hindered by putting whole cone hops in bags. Allowing loose hops maximizes extraction but requires diligent cleaning after each use to avoid clogs.
Q: Can pellet hops be used instead of whole cone hops?
A: Yes, pellet hops work equally well in hop backs and reduce the amount of vegetative matter transferred compared to cones.