5 BBL Hot Liquor Tank
A 5 BBL Hot Liquor Tank, sometimes referred to as a hot water tank, is an essential piece of brewing equipment used to heat up water for mashing and sparging during the beer production process. This equipment guide will provide a comprehensive overview of 5 barrel (BBL) hot liquor tanks, including types, design considerations, sizing calculations, customization options, top suppliers and pricing. We’ll also cover best practices for installation, operation and maintenance.
What is a Hot Liquor Tank?
A hot liquor tank holds and heats water to be used for mashing grains and sparging the mash tun. Heating water to precise temperatures is critical for optimal starch conversion and efficient sugar extraction when making beer wort.
Hot liquor tanks are insulated cylindrical vessels made using stainless steel or copper. They can be directly heated using steam, electricity or gas to accurately control and maintain strike water and sparge water temperatures throughout a brewing cycle.
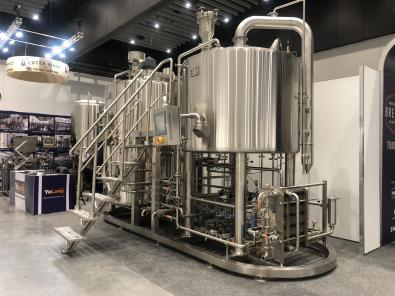
Key Functions of a Hot Liquor Tank
- Water Heating:
- The HLT is equipped with a heating element or a steam jacket to raise the temperature of water to specific levels required for various stages of the brewing process.
- Mashing:
- During the mashing process, hot water from the HLT is mixed with malted grains to convert starches into fermentable sugars. The HLT provides the necessary hot water for this step.
- Sparge Water:
- After mashing, the grains need to be rinsed to extract any remaining sugars. The HLT provides hot water for sparging, which is the process of gently washing the sugars from the grain bed.
- Temperature Control:
- The HLT helps maintain precise temperature control for different brewing steps. It ensures that the water used in mashing and sparging is at the correct temperature for enzymatic activity and sugar extraction.
- Volume Storage:
- The HLT serves as a reservoir for holding a significant volume of hot water. This is important for large-scale brewing operations where consistent hot water availability is crucial.
- Cleaning and Sanitizing:
- Hot water from the HLT is often used for cleaning and sanitizing brewing equipment, such as hoses, tanks, and pipes. High-temperature water helps eliminate bacteria and contaminants.
- Preheating:
- The HLT may be used to preheat other vessels in the brewing process, such as the Mash Tun or the Brew Kettle, by circulating hot water through them.
- Energy Efficiency:
- Some HLTs are designed with insulation to minimize heat loss, improving energy efficiency and reducing the overall energy consumption during the brewing process.
- Water Treatment:
- The HLT can be equipped with water treatment systems to adjust the pH or remove impurities from the water used in brewing, ensuring that the water meets the specific requirements for each brewing stage.
- Automated Controls:
- Modern brewing systems often have automated controls for the HLT, allowing brewers to program and monitor the temperature, water flow, and other parameters for consistent and efficient brewing.
Why Choose a 5 BBL System Size?
5 barrel (BBL) brewing systems are a popular mid-sized capacity for many craft or nano breweries producing specialty beers.
Key reasons to select a 5 BBL system:
- Production Volume – Each 5 BBL batch yields about 155 gallons or 588 liters. This allows over 6000 pints per week maximum production. Suitable for supplementing a taproom and some distribution.
- Space Efficiency – Compact enough to fit production, fermentation, storage into a 5000 sq ft brewery. Scalable later to 10-15 BBL.
- Upfront Investment – Pilot 1 BBL systems require significant plumbing and operating expenses for small volumes. At least $100,000 cost savings over a 10 BBL to get started.
- Innovation Options – Flexible to produce wide variety of styles in small batches for taproom while scaling distribution capacity slowly in response to demand.
Given these advantages, many newer breweries use 5 BBL systems to minimize risk and startup costs while maximizing creativity for specialty beer taprooms. The additional capacity helps meet distribution goals.
5 BBL Hot Liquor Tank Design Considerations
Properly designed hot liquor tanks optimize heating efficiency, consistency and safety:
Table 1. Key Design Factors for 5 BBL Hot Liquor Tanks
Parameter | Recommendations |
---|---|
Volume | 7 BBL to account for heating losses and provide excess hot water |
Material | Stainless steel for corrosion resistance and durability |
Height to Diameter Ratio | At least 2:1 for efficient indirect heating area |
Thickness | Min 1 mm for strength, max 1.2 mm for better heat transfer |
Insulation | High grade polyurethane or glass wool insulation |
Heating System | Steam, electric or gas operated |
Temperature Gauge | Essential for monitoring strike temps up to 170°F |
Sight Glass | Required to visually inspect water levels |
Automatic Water Fill | Useful option for unattended operation |
Valves & Fittings | Smooth, easily cleanable ball valves and tri-clamp fittings |
Stand | Height for comfortable outlet valve access and pump connections |
Safety Features | Pressure relief valve, overflow pipe, low water cut-off |
Sizing a Hot Liquor Tank
The 5 BBL hot liquor tank size should provide excess capacity beyond the primary 5 BBL batch volume. This ensures ample hot water even after boiler heating losses and allows uninterrupted brewing operations.
Hot Water Volume Calculation
Table 2. Hot Water Requirements for 5 BBL Batch
Water Use Phase | Typical Volume Ratio | Gallons Needed |
---|---|---|
Initial Mash-In | 2.5 gallons water : 1 gallon capacity | 2.5 x 5 = 12.5 gallons |
Sparge Rinse | 1 gallon water : 1 gallon capacity | 5 gallons |
Total For One 5 BBL Batch | 17.5 gallons |
With 17.5 gallons hot water needed per 5 BBL batch, a 7 BBL tank size provides a 20% safety buffer, allowing over 6 back to back batches without reheating:
- 7 BBL = 28 gallons = 175 gallons total storage
- 6 batches x 17.5 gallons/batch = 105 gallons
- Leaves 70 gallons excess for losses and continuous operation
While a 5 BBL tank size may work, the extra 2 BBL volume improves flexibility and heating efficiency. The boiler only needs to reheat half as often. This saves time, energy and maintains stable strike water temperatures compared to undersized tanks.
Customization of 5 BBL Hot Liquor Tank
Table 3. Customization Options for 5 BBL Hot Liquor Tanks
Feature | Possibilities | Benefits |
---|---|---|
Height | Standard 48-60 inches or custom height | Ergonomic outlet access |
Diameter | 24-30 inches for 5 BBL capacity | Match brewery layout constraints |
Material | 100% stainless steel or copper sheathing | Better heat transfer, durability |
Heating Method | Steam, electric immersion elements, gas burner | Choose efficiency, rapid heating benefits |
Automation | Programmable controllers for temperature profiles | Precision strike temp control |
Insulation Type | Glass wool, polyurethane foam, cut to size | Max energy efficiency |
Stand Choice | Height, material, casters, ladder | Convenient access and mobility |
Fittings | Ball valve sizes, tri-clamp diameter | Compatible lines to existing pumps, pipes |
Safety Add-ons | Overflow pipe, low water cut-off | Prevent boil-over accidents |
Experienced tank manufacturers offer extensive customization options so your hot liquor tank seamlessly fits with your existing brewery layout, operations and safety needs.
Top 5 BBL Hot Liquor Tank Manufacturers
Table 4. Leading 5 BBL Hot Liquor Tank Brands
Brand | Description | Price Range |
---|---|---|
JV Northwest | Industry leaders for tanks up to 15 BBL, high quality stainless | $6000 – $8000 |
Ss BrewTech | Specialize in 1-7 BBL electric BrewBoil kettles | $8000 – $12000 |
Portland Kettle Works | Popular for steam heated copper vessels, 5 year warranty | $7000 – $14000 |
Specific Mechanical | Budget friendly tanks focused on nano systems | $5000 – $7000 |
Colorado Brewing Systems | Custom electric hot liquor tanks with optional automation | $8000 – $15000 |
When selecting a hot liquor tank supplier, consider:
- Build Quality – Tanks with durable 1mm or less stainless steel, strong Welds, stable stands support lifelong operation despite heavy daily use and repeated heating cycles. Paying more initially saves repairs down the road.
- Heating System – Your available utilities, desired heating speed and efficiency varies. Compare gas, electric and steam models on BTU transfer rate, precision and operating costs.
- Automation Extras – Programmable controllers that automatically adjust temperatures during mash saves manual monitoring. Convenient if you brew multiple times daily but adds $1500+ to costs.
- Custom Fit – Unique diameter, height, accessories options that perfectly match your production goals, energy sources and floorplan layout.
- Installation Support – Ability to deliver and assist installing the tank as well as after sales service support.
- Reputation – Read craft brewery reviews and talk to owners about their tank reliability, lifetime and manufacturer dealings. This helps avoid poor customer service or quality issues.
Operation and Maintenance Best Practices
Table 5. Operating a 5 BBL Hot Liquor Tank for Peak Performance
Activity | Procedure | Frequency |
---|---|---|
Heating | Slowly bring water to strike temperature, max 1.5°F per minute | Each brew day |
Sparging | Top up tank water level between brews | After every 3-4 batches |
Safety Checks | Inspect sight glass, gaskets, valves, seals | Weekly |
Drain and Clean | Remove elements, wash interior with alkaline cleaner | Monthly |
Descaling | circulate dilute phosphoric or nitric acid solution | Yearly |
Inspection | Check insulation, welds, stand integrity, leaks | Yearly |
Gaskets | Replace worn out or cracked seals | Every 2-3 years |
Following hot liquor tank manufacturer guidelines for heating, cleaning, adjustments and maintenance is vital for safety, consistency and longevity.
Some key operation tips:
- Monitor temperatures using the gauge to prevent boiling or scorching
- Top up water between batches to reduce heating cycles
- Tighten fittings, valves over time as vibrations can loosen connections
- Clean thoroughly after extended shutdowns before heating again
- Descaling annually removes mineral deposits from repeated heating
Investing in a quality hot liquor tank and keeping it well maintained ensures reliable hot strike water supply for years of beer production.
How to Choose the Right 5 BBL Hot Liquor Tank
Selecting the optimal hot liquor tank for your 5BBL brewing system is an important decision impacting productivity, efficiency and beer quality.
Follow this 6 step evaluation process to choose the best tank:
Table 6. How to Select the Right 5 BBL Hot Liquor Tank
Step | Action |
---|---|
1. Calculate Requirements | • Determine peak production batches per day<br>• Estimate total hot water volume needed <br>• Allow 20-25% extra capacity |
2. Match Dimensions | • Measure floor space and doorway constraints <br>• Specify shape and size limitations |
3. Review Heating Options | • Compare available utilities – steam, electric, gas <br>• Determine preferred heating method |
4. Select Custom Features | • Automation needs <br>• Material upgrades <br>• Valves, fittings, accessories |
5. Evaluate Suppliers | • Compare 5 quotes on cost, lead times, heating stats <br>• Verify craft brewery references <br>• Review quality guarantees and warranties |
6. Optimization | • Fine tune height, position and accessories post-installation for ideal ergonomics and workflow |
Carefully going through each step above and collecting detailed requirements minimizes costly changes later. It ensures you purchase the right sized 5 BBL hot liquor tank meeting safety regulations, production targets, efficiency needs and budget.
Key Differences – Electric vs Gas vs Steam Heating
Understanding the pros and cons of available heating methods like electric, gas or steam allows selecting the optimal energy source for your 5 BBL hot liquor tank.
Table 7. Electric vs Gas vs Steam Heating System Comparison
Parameter | Electric | Gas | Steam |
---|---|---|---|
Setup Cost | $$ | $$$ | $$$ |
Operating Cost | $$$ | $$ | $ |
Efficiency | Good, 70% | Better, 85% | Best, 95%+ |
Precision | Excellent +/- 1°F | Good +/- 3°F | Fair +/- 5°F |
Ramp Up Time | Slow, 30-60 mins | Faster, 15-30 mins | Rapid, 10-15 mins |
Consistency | Very consistent | Decent | Can fluctuate |
Safety | Low risk | Risk of leaks | Scalding risk |
Maintenance | Low, only elements | Annual tune-ups | Heat exchanger cleaning |
Key Takeaways:
- Electric offers the best precision but slowest heating
- Gas boils faster and cheaper but temperature varies slightly
- Steam is extremely fast with highest efficiency yet requires more safety diligence
Crunch the lifecycle cost and productivity numbers for your brewery based on typical energy rates, labor expenses and production schedule to determine the optimal source of heating.
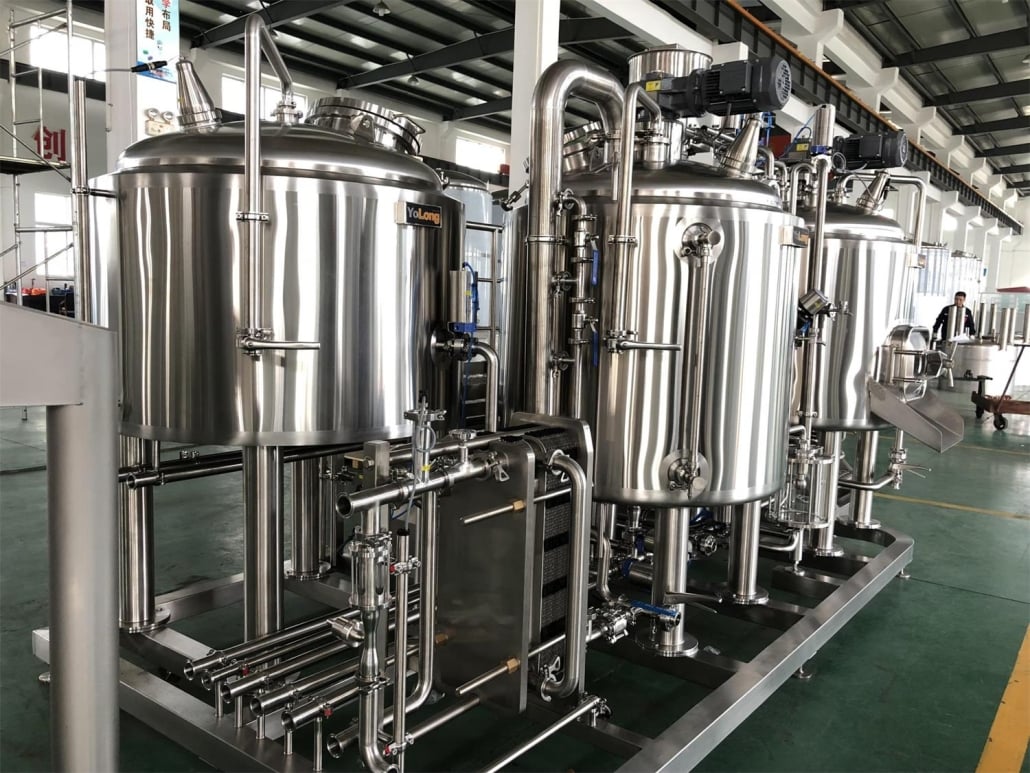
5 BBL Hot Liquor Tank Accessories
Table 8. Useful Options and Upgrades for 5 BBL Hot Liquor Tanks
Accessory | Details | Benefits |
---|---|---|
Automatic Water Fill | Float valve mechanism links to water supply | Maintains full volume between batches |
Digital Temperature Controller | Touchscreen adjustable digital thermostat | Accurate strike temp control |
Rupture Disk | Pressure activated release valve | Prevent dangerous steam buildup |
Sparge Arm | Rotating interior spray nozzle | Evenly distributes hot water over grain bed |
Secondary Heating Thermometer | Redundant analog temperature gauge | Backup if digital controller fails |
Mobile Casters | Rotate smoothly through 360° | Move tank easily for cleaning behind |
Insulation Jacket | Maximizes heat retention | Reduce energy loss by 25%+ |
Sight Glass Upgrade | Wide view plexiglass water level indicator | Enhanced visibility with backlight option |
Automatic Timer | Programmable controller | Unattended strike temp adjustment |
Consider accessories that improve efficiency, consistency and safety based on your expansion plans and budget.
FAQs
Table 9. Frequently Asked Questions on 5 BBL Hot Liquor Tanks
Question | Answer |
---|---|
What size stand height is recommended for a 5 BBL tank? | Based on outlet valve positioning, short operator have to reach higher flows. |
– | Typically 45-48 inches works for average heights to easily see sight glass. |
Should steam tanks use copper or stainless material? | Copper offers 35% faster heating than stainless. |
– | But stainless steel is more durable and corrosion resistant for longevity. |
How many immersion heating elements are ideal? | Use 2 x 4500W elements diagonally opposite for even heating. |
– | Option to add 2 more elements later to upgrade watt density for faster ramp up times. |
Is insulation mandatory for hot liquor tanks? | While insulation jackets add cost, they radically improve heating efficiency. |
– | Bare stainless tanks lose a massive 50°F over 60 minutes! Insulated only 2°F loss. |
What is the optimal thickness for hot liquor tanks? | Between 0.8mm to 1.2mm thickness balances durability and heat transfer. |
– | Over 1.5mm makes heating noticeably slower. |