5 BBL Brewing Equipment
A 5 barrel (BBL) brewhouse system allows craft brewers to scale up production while maintaining high quality and flexibility. This guide covers key 5 BBL brewery equipment including process layout, sizing, customization, suppliers, installation, operation, maintenance and more.
Introduction to 5 BBL Brewing Systems
5 BBL commercial breweries produce batch sizes of 155 gallons or 5 barrels of beer. Typical features include:
- All-grain brewhouse with 5 BBL capacity
- Manual or automated operation
- 15-30 BBL annual production capacity
- Electric or gas heating configurations
- High quality stainless steel construction
- Space efficient footprint for nano or micro breweries
- Flexible equipment for various beer recipes
A well-designed 5 BBL brew house allows craft brewers to increase production while retaining hands-on control over quality and experimentation.
This guide provides a detailed overview of selecting, integrating and running 5 BBL brewing equipment.
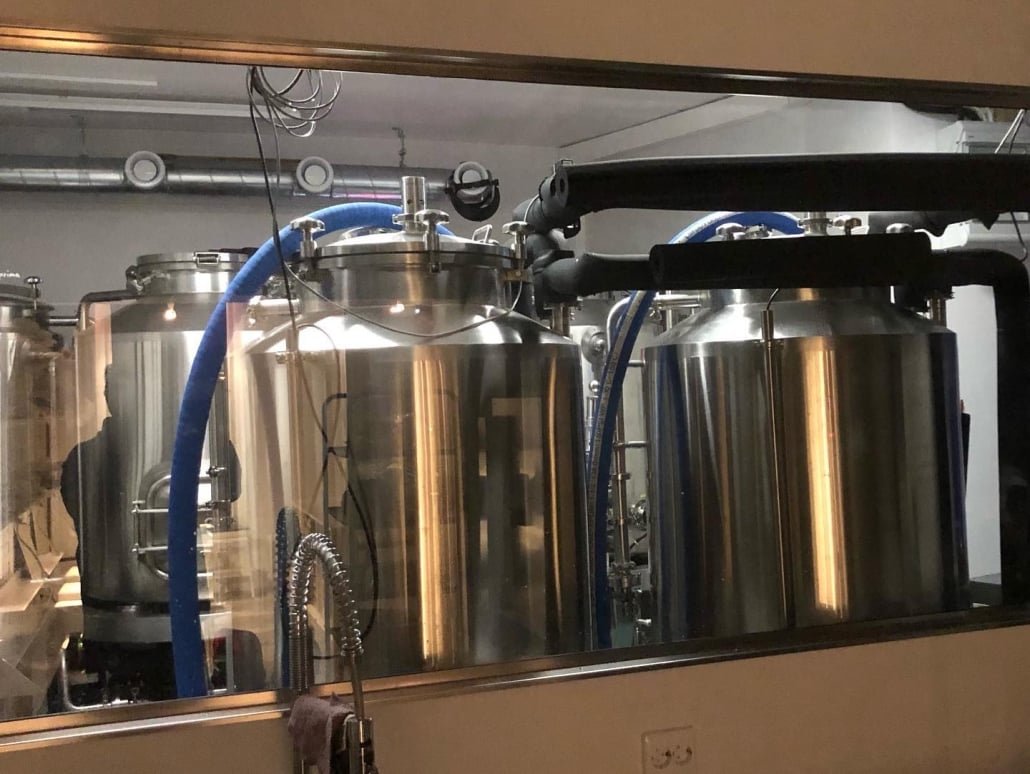
5 BBL Brewhouse Equipment Overview
A complete 5 BBL brewhouse system consists of:
5 BBL Brewery Equipment
- Milling – Roller or hammer mill
- Mash tun – Insulated stainless vessel with false bottom
- Lauter tun – For wort separation from grain
- Brew kettle – Direct or indirect heated kettle
- Whirlpool – For trub separation after boil
- Heat exchanger – Cooling wort quickly
- Fermentation tanks – Stainless conical fermenters
- Brite tanks – Carbonation and storage
- Glycol chiller – Temperature control
- Piping – Food grade stainless transfer pipes
- Automation – Level sensors, PID control
5 BBL Brewing Process Overview
The typical all-grain brewing process consists of:
- Milling – Grain is milled into grist for mashing
- Mashing – Grist is mixed with hot water for enzyme conversion
- Lautering – Sugary wort is separated from spent grains
- Boiling – Wort is boiled with hops for bitterness, aroma, sanitation
- Whirlpool – Trub proteins and hops are removed
- Cooling – Heat exchanger rapidly cools wort before fermentation
- Fermentation – Yeast converts sugars into alcohol
- Maturation – Resting improves clarity and flavor
- Filtration – If required for bright beers
- Carbonation – CO2 addition for desired volumes
- Packaging – Kegging, bottling or canning
The brewhouse equipment enables wort production, while fermenters and brite tanks condition and package the beer.
5 BBL Brewhouse Design and Layout
A typical 5 BBL brewery layout consists of:
5 BBL Brewery Layout
- Brewhouse equipment in parallel or linear arrangement
- Centrally located mash tun and lauter tun
- Kettle with direct or indirect heating
- Whirlpool for trub separation after boil
- Glycol chilling system for wort cooling
- Fermentation room with 5-10 BBL fermenters
- Brite tanks for carbonation and storage
- Storage room for grain, hops, yeast etc.
- Packaging area for kegging, canning, bottling
- Utility connections for water, electrical, drains, ventilation
- Office space, tasting room etc. as required
Layout is optimized for workflow from raw materials to packaged beer. Space for expansion should be considered.
Customization and Options for 5 BBL Systems
Key customization options for 5 BBL equipment include:
5 BBL System Customizations
- Electric vs gas heating
- Direct vs indirect kettle firing
- Level of automation – manual valves or sensor-based
- Fermentation temperature control methods
- Number and size of fermenters, brite tanks
- Materials – stainless steel grades, coatings
- Piping dimensions and fittings
- Filtering and carbonation choices
- Milling, bottling, canning, kegging machine upgrades
- Bulk grain handling and storage
- Higher quality spotlight finishes and welding
- Utility connections and capacities
-Floor drain placement and trench drains
- Branding – custom colors, logos, design
Collaborating with the brewhouse manufacturer enables optimal customization for your space, needs and budget.
5 BBL Brewery Suppliers and Costs
Leading 5 BBL system manufacturers and sample pricing:
5 BBL Equipment Suppliers and Prices
Manufacturer | Location | Price Range |
---|---|---|
Specific Mechanical | Canada | $150,000 – $250,000 |
Portland Kettleworks | USA | $100,00 – $200,000 |
Premier Stainless | USA | $150,000 – $275,000 |
Triangles | China | $70,000 – $120,000 |
JV Northwest | USA | $100,000 – $150,000 |
- Complete 5 BBL brewhouses cost $100,000 to $275,000 on average.
- North American suppliers command higher prices but offer better quality and service.
- Imported Chinese systems are lower priced but have higher defect and rework rates.
- Factors like automation, accessories, installation etc. influence overall capital costs.
- Used equipment can provide budget 5 BBL brewhouse solutions.
Carefully weigh the upfront price versus long-term quality, production output and resale value when selecting systems.
5 BBL Brewery Installation, Operation and Maintenance
Installation Considerations
- Flooring needs – amenities like trench drains and sinks
- Utility connections for electricity, water, gas, glycol
- Optimizing layout and clearances for operation
- Testing and inspecting equipment function after connections
Operation
- Following all safety procedures
- Brewing a range of beer recipes and parameters
- Tracking brewing data for yield consistency
- Adhering to cleaning and sanitization procedures
Maintenance
- Preventative maintenance schedule
- Inspecting fittings, gaskets, electrical
- Lubricating and servicing pumps
- Tank inspections and passivation
- Replacing worn parts like seals
- Addressing issues quickly to avoid downtime
Ongoing training and documented procedures in these areas ensure smooth brewery operation and beer quality.
Selecting a Reliable 5 BBL System Supplier
Key 5 BBL brewhouse supplier evaluation criteria:
5 BBL Brewery Supplier Selection
- Experience designing and building breweries
- Breadth of equipment offerings and turnkey capabilities
- Quality of workmanship and materials
- Flexibility for customization
- Responsive customer service and communication
- Ability to stay on schedule and budget
- Installation support and operator training
- Shipping and logistics capabilities
- Range of warranties and service contracts
- References and testimonials from existing clients
- Financial stability of company
On-site visits to the supplier’s facility and existing brewery projects provide key insights on expertise. Seeking referrals ensures a qualified partner.
Pros and Cons of 5 BBL Brewing Systems
5 BBL Brewing Equipment Advantages
- Scaled capacity beyond homebrewing
- Flexibility for product experimentation
- All-grain wort production quality
- Capability for packaging in bottles, cans, kegs
- Potential for direct to consumer sales
- Capacity for taproom and local distribution
Potential Disadvantages
- Significant capital investment required
- Ongoing production and quality control demands
- Equipment maintenance requirements
- Space requirements for brewhouse layout
- Staffing requirements for brewing operations
- Planning for growth and expanded capacity
The benefits often make 5 BBL breweries an appealing starting point for commercial craft brewing ambitions.
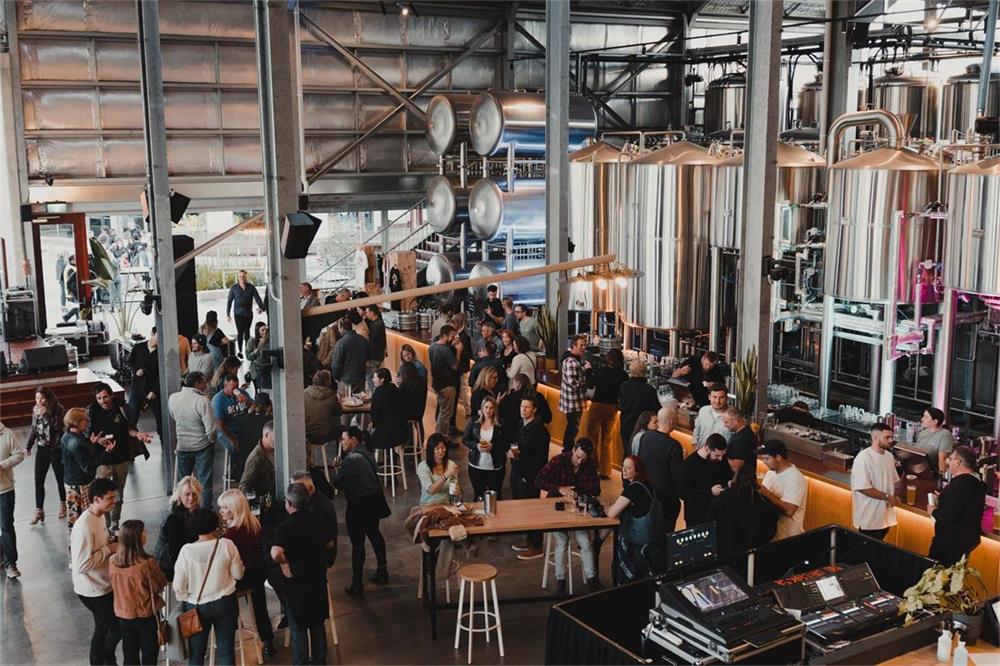
FAQ
Q: What size brewery is 5 BBL equipment suited for?
A: 5 BBL systems are optimal for very small brewpubs, taprooms or nano breweries doing pilot batches up to micro production scale.
Q: What is the cost of a 5 BBL brewhouse?
A: A complete 5 BBL brewing system costs $100,000 to $275,000 on average depending on the level of automation and accessories.
Q: What are the Differences between 3 BBL and 5 BBL systems?
A: 5 BBL has more production capacity and larger fermenters. It requires more space and storage. 3 BBL is better suited to homebrewers scaling up or brewpubs.
Q: Can 5 BBL produce canned or bottled beer?
A: Yes, a 5 BBL system allows canning and bottling capability in addition to kegging. Canning lines and labeling equipment can be added.
Q: How many fermentation tanks are needed for 5 BBL?
A: For primary fermentation, 5-10 BBL conical fermenters are recommended. Additional fermenters enable lagering, fruit additions, etc.
Q: What raw materials are needed for 5 BBL batches?
A: Approximately 400-500 lbs of grain is needed per 5 BBL batch. Hops around 2-5 lbs. 25-50 lbs of yeast depending on the beer recipe.
Q: What is the typical brewhouse efficiency for 5 BBL?
A: With a well-designed mash tun, high quality milling, and proper procedures, 75-80% mash efficiencies can be consistently achieved.
Q: How many people are required to operate a 5 BBL brewery?
A: For a very small operation, 1-2 knowledgeable brewers can handle 5 BBL production and packaging. Larger taprooms require additional bartending staff.
Q: How much beer can a 5 BBL system produce annually?
A: Full time production on a 5 BBL brewhouse equates to roughly 450-900 barrels or 15,000 to 30,000 gallons of beer output per year.
Conclusion
In summary, 5 BBL commercial brewing systems enable craft brewers to scale up all-grain wort production and packaging capabilities compared to homebrewing. Careful equipment selection, layout and integration ensures quality, efficiency and flexibility for small batch brewhouse needs. With proper procedures and maintenance, 5 BBL systems can produce consistent, high-quality beer.