5 BBL Brewhouse Brewing Systems
A 5 barrel (BBL) brewhouse is a medium-sized commercial brewing system with a capacity of about 155 gallons or 588 liters per batch. This system allows craft breweries to produce high-quality beer on a scale to supply a taproom and local distribution.
This guide provides brewers an in-depth look at 5 BBL brewhouse equipment. It covers types of systems, design considerations, brewing process, sizing, customization, suppliers, installation, operation, maintenance and how to select the right system for your needs.
Types of 5 BBL Brewhouse Systems
There are two main types of 5 BBL brewing systems:
System Type | Description |
---|---|
Traditional | Manual brewing system with separate mash tun, lauter tun, kettle and whirlpool. Requires more manual labor but allows customization and control. |
Automated | Integrates mashing, lautering, boiling and whirlpooling into one or two vessels for an automated process. Reduces labor but offers less customization. |
Traditional 5 BBL Systems allow brewers to control and customize the process with separate vessels and manual operation. This gives flexibility but requires more labor.
Automated 5 BBL Systems integrate the brewing operations into interconnected vessels. This reduces manual work but provides less customization. The choice depends on the brewery’s priorities.
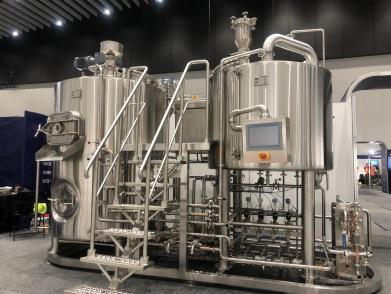
5 BBL Brewhouse Brewing Process
A typical brewing process on a 5 BBL traditional 3-vessel system involves:
Mashing: Mixing milled grains with hot water in the mash tun to convert starches to sugars. Takes 1-2 hours at temperatures around 155°F (68°C).
Lautering: Draining the sweet wort from the grains in the mash tun. Spent grains are discarded and wort is collected.
Boiling: Boiling wort with hops in the kettle for 60-90 minutes. This sterilizes, extracts flavors, coagulates proteins.
Whirlpooling: Creating a whirlpool in the wort to separate trub and hops before fermentation.
Cooling: Quickly chilling boiled wort to under 80°F (27°C) to pitch yeast.
Fermenting: Yeast ferments sugars into alcohol and CO2 for 1-2 weeks.
Maturing: Beer conditioned for flavor development before filtering and packaging.
A 5 BBL automated system combines vessels and automates transfers and temperature control to simplify the process. But the same basic brewing stages occur.
Sizing and Capacity of a 5 BBL System
Parameter | Details |
---|---|
Batch Size | 5 barrels or 155 gallons or 588 liters |
Yearly Output | 500-1000 barrels depending on schedule |
Fermentation Tanks | 2-3 tanks minimum to ferment batches |
Brite Tanks | 1-2 to condition and clarify beer |
Floor Space Needed | 400-1000 sq. ft. depending on layout |
- A standard 5 BBL batch is 155 gallons of wort produced. So this system can brew 310 gallons in a double batch.
- Typical yearly output for a small brewpub would be 500-1000 barrels if operating 1-2 times per week.
- You need enough fermentation and brite tank capacity to hold multiple batches at once. Plan for 2-3 sets minimum.
- Required floor space varies from 400 sq. ft. for a compact automated system up to 1000 sq. ft. for a more spread out traditional 3-vessel setup.
Layout and Design of a 5 BBL Brewhouse
5 BBL systems can be designed in different layouts:
Linear: Equipment in a straight line which saves space but requires more transfers.
“L” Shaped: Allows gravity flow with lower transfers. But equipment is spread out requiring more floorspace.
2-Tier: Has kettle and whirlpool up on a platform with mash tun below. Saves floorspace but needs pumping.
Design Aspect | Options and Customization |
---|---|
Batch Size | Fixed at 5 barrels or can do double batches |
Vessel Types | Traditional multi-vessel or automated combined |
Vessel Fabrication | Stainless steel, copper, hybrid materials |
Heating Options | Direct fire, steam, electric |
Level of Automation | Manual operation up to full PLC/computer controls |
Grain Handling System | Bag hoist, tilting platform, auger |
Layout | Linear, L-shaped, 2-tier, customized |
Flooring | Must withstand weight, spills, chemicals, hot liquids |
Electrical Requirements | Size panels for all motors and heating |
Utilities | Steam, CO2, compressed air, chilling |
Process Control | Manual up to digital automation |
Clean-in-Place | CIP balls/heads or automated CIP systems |
Nearly all aspects of a 5 BBL system can be customized to a brewery’s needs or adapted to an existing building’s constraints. Vessel fabrication, heating systems, level of automation, layout and utilities can be configured for operational priorities and budget.
Suppliers of 5 BBL Brewhouse Equipment
There are over 50 known suppliers of small to mid-size brewing equipment in the 5-10 BBL range. A partial list:
Brewhouse Company | Location | Price Range |
---|---|---|
SPE Ideal Stainless | USA | $100,000-$250,000 |
Ss Brewtech | USA | $150,000-$300,000 |
Premier Stainless | USA | $125,000-$275,000 |
Portland Kettleworks | USA | $100,000-$200,000 |
Specific Mechanical | Canada | $150,000-$350,000 |
Rolec Prozess | Germany | $200,000-$400,000 |
Criveller | Italy | $250,000-$450,000 |
Maverick | China | $50,000-$150,000 |
Pricing is very wide depending on level of automation, exotic metals and customization. Typical range for a basic 5 BBL system is $100k to $250k with more complex systems ranging from $150k up to $450k. Imported European equipment tends to be premium priced. Chinese systems can be half the cost but may lack support. Though quality and outputs can equal systems costing 2-3 times more from western suppliers. Select based on budgets and preferences for automation versusmanual functionality.
Purchasing and Installing a 5 BBL System
Installing a brewhouse system requires planning and coordination:
- Get quotes from multiple vendors to compare options.
- Define technical requirements and output targets.
- Understand site electrical, plumbing and ventilation needs.
- Prepare flooring and building access for equipment.
- Install glycol chilling, steam, compressed air and CO2 systems (if needed).
- Have utilities and drains roughed into place prior to delivery.
- Schedule vendor support staff for installation supervision.
- Perform integrated testing before first batch.
Purchasing through local suppliers simplifies logistics and provides service assistance. But importing systems can reduce costs dramatically. Evaluate all options fully before committing to a system and vendor.
Operating a 5 BBL Brewhouse
To operate a 5 BBL system efficiently:
- Follow manufacturer guidelines for daily and weekly cleaning.
- Inspect vessels and replace gaskets/seals regularly.
- Descaling or passivation may be needed quarterly.
- Keep precise brewing logs on malt bills, hopping and fermentation activity.
- Control fermentation temperatures carefully.
- Use airlocks and dry hopping for aroma.
- Adjust water chemistry for desired beer style.
- Fine tune brewing process for yield, clarity and flavor.
- Send beers out for lab analysis to ensure quality and consistency.
Good record keeping and consistency between batches produces the best results as brewers dial in recipes on their system.
Maintaining 5 BBL Brewhouse Equipment
A 5 BBL system involves multiple vessels, pumps, pipes, gaskets, heating elements and moving parts requiring maintenance:
System | Maintenance Frequency | Maintenance Tasks |
---|---|---|
Vessels | Weekly | Inspect, clean, sanitize |
Pumps | Monthly | Inspect, lubricate, mechanical seal check |
Valves | 6 months | Inspect, lubricate, replace gaskets |
Gauges | Annually | Calibrate pressure, temperature sensors |
Heating Elements | Annually | Descale elements, inspect wiring |
Refrigeration | 6 months | Inspect lines, check charge, service condenser |
Automation | As needed | Calibrate probes and transmitters, update software |
A maintenance log should be kept to record all inspections, calibrations and servicing tasks completed by date. Follow manufacturer maintenance schedules closely.
Tips for Selecting a 5 BBL Brewhouse
When selecting a 5 BBL brewing system, consider:
Budget Match system price to capital available. Define must-have features versus nice-to-haves.
Quality Choose reputable, proven equipment that meets brewery volume goals. Get references.
Automation Level Evaluate labor savings versus flexibility for automated versus manual systems.
Customization
Assess options to customize vessel fabrication, heating, controls, etc.
Installation Support
Confirm vendor or third party installation assistance is available.
Ongoing Service Ensure manufacturer can service equipment and provide replacement parts.
Brewing Approach Match system capabilities with brewing methods and beer types planned.
Taking time upfront to thoroughly assess 5 BBL systems, installation requirements, operating considerations, and maintenance needs will help find the right system for a brewery at the required investment level.
Pros and Cons of 5 BBL Brewing Systems
Pros | Cons |
---|---|
Enables small batch craft brewing | Requires significant upfront investment |
Flexible batch sizes up to 310 gallons | Additional fermentation tanks add cost |
Efficient scale for taprooms or local distribution | Sophisticated systems have learning curve |
Options for automation reduce labor | Maintenance can be intensive |
Customizable to meet brewery preferences | Custom builds or exotic metals increase price |
Proven equipment reliability up to 3000 batches | Lead times can exceed 6 months |
The advantages of 5 BBL systems make them ideal for brewpubs, taprooms and brands focused on local markets. Output exceeds most 3 BBL systems for higher volume without reaching scales requiring wide distribution.
The main downside is the required capital investment. Ongoing costs for maintenance and repairs should also be planned for. Lastly custom systems can mean long equipment lead times.
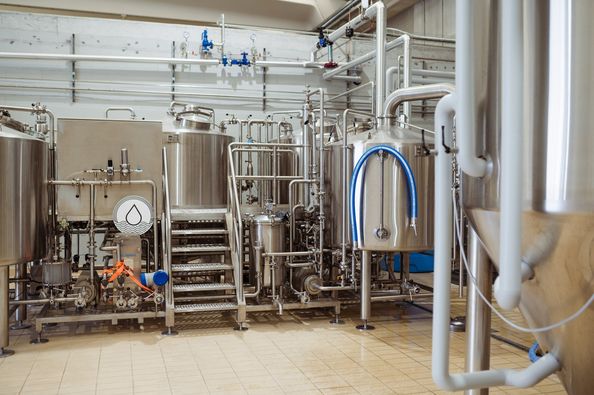
FAQ
Q: What size brewery is a 5 BBL system good for?
A: A 5 BBL brewhouse is ideal for a small brewpub, taproom or local microbrewery looking to produce 500-1000 barrels yearly. This scale is well matched to on-site sales or limited self-distribution.
Q: What is the difference between automated and traditional brewhouse systems?
A: Automated systems integrate vessels and processes like mashing and lautering to reduce manual labor. Traditional multi-vessel systems provide more customization and control but involve more hands-on work.
Q: Should I buy domestic or imported brewhouse equipment?
A: Domestic equipment from US, Canadian or European vendors provides service and support advantages. Imported Chinese systems have much lower upfront costs but may lack support. Quality is improving however to rival premium systems.
Q: How long does a 5 BBL system last?
A: With proper maintenance and part replacement, a 5 BBL system should reliably produce beer for 10-15 years and 2,000+ batches. Vessel jackets, heating elements and gaskets/seals have shorter lifespan than stainless frames.
Q: What are the most important factors in selecting a 5 BBL brewhouse?
A: Key considerations are quality of equipment, level of automation versus flexibility, installation support, ongoing serviceability, manufacturer reputation, proven reliability and matching system output and functionality to the brewery’s business goals.