5 BBL Brewhouse Systems
5 BBL Stackable Fermenters are a mid-sized commercial beer brewing system with a brewing capacity of around 155 gallons (588 liters) per batch. 5 BBL systems are popular with many small to mid-size craft breweries and brewpubs, as they allow for an economical jump in production capacity beyond tiny homebrewing-scale systems.
Key Specifications of Standard 5 BBL Stackable Fermenters:
Brewing Volume | 5 Barrels, around 155 Gallons/ 588 Liters per batch |
---|---|
Mashtun Size | 200+ Gallon capacity |
Kettle Size | 200+ Gallon capacity |
Output | Estimated 180-220 Kegs per Week |
Batch Time | 4-6 Hours Typical |
Space Required | Around 1500 sq ft minimum |
Operators Required | 1-2 Persons |
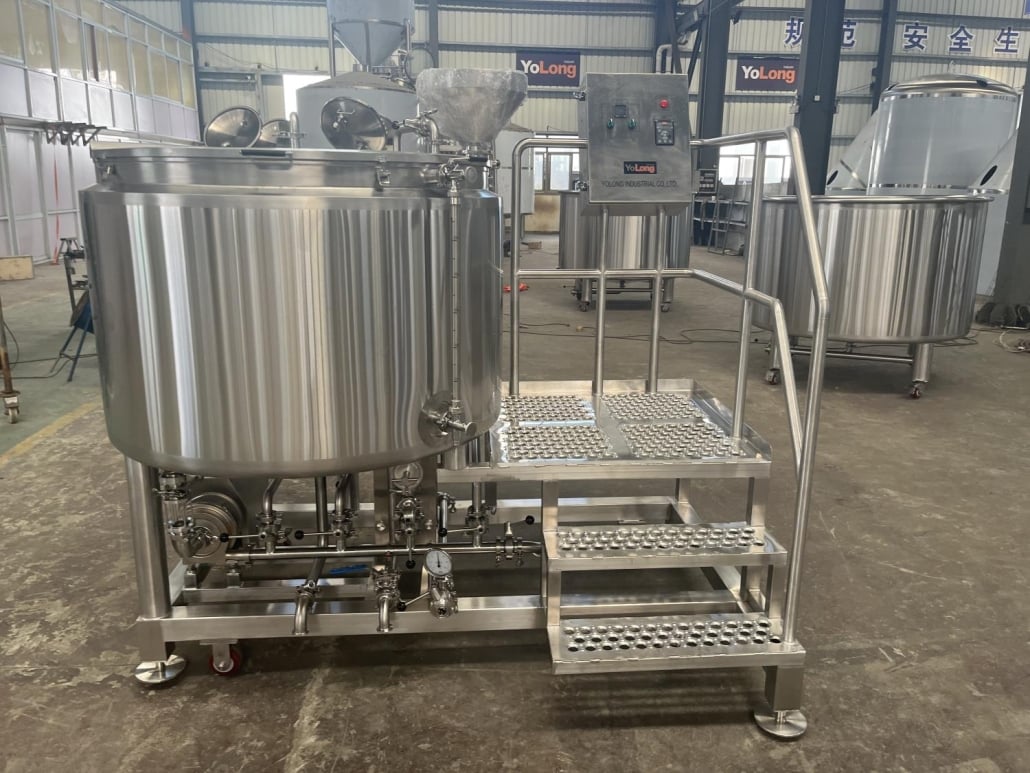
Types of 5 BBL Stackable Fermenters
5 BBL brewhouses are available in different configurations from various equipment manufacturers. Some key types include:
Table 1: Types of 5 BBL Brewhouse Equipment
Type | Features |
---|---|
Standard Manual | Economical option with manual operation at each stage. Requires active staff management of each process step. |
Automated | Fully auto, PLC-based operation with preset timers, valves, pumps for each brew stage. Allows 1-touch beer production with minimal staff. Pricier than manual units. |
Semi-Auto | Mix of manual and automatic operation where key stages like wort boiling have motorized controllers but grain handling remains manual. Provides partial automation to cut staff while keeping cost lower than full automation. |
Steam-Powered | Use steam boilers and coils instead of electric elements to heat water and wort. Especially useful when steam is available at the brewhouse location from other processes. Can be manual, semi-auto or auto config. |
Multi-Vessel | Additional vessels beyond standard mashtun and kettle provided for specialty brewing, higher gravity batches etc. Vessels may include mash filter, cereal cooker, hop dosing tanks. |
Pilot Scale | Compact brewhouse, manual operation oriented for new brewers or pilot batches, experimental brewing. Lower price and space requirement but lower automation and peak output than prod-focused options. |
5 BBL Brewhouse Standard Equipment Components:
Table 2: Components of a Standard 5 BBL Brewhouse System
Component | Details & Purpose |
---|---|
Mash Tun | Insulated stainless steel vessel that holds milled grains for barley mash. Often direct steam-heated. Mixes mash for starch conversion to fermentable sugars. |
Lauter Tun | Stainless container with false slotted bottom to separate sweet wort from grains after mash. Some systems combine mash and lauter tun into single unit. |
Brewkettle | Boils wort after lautering, allowing flavors and aromas to develop. Usually direct steam or electric heated. Has all necessary plumbing fixtures. |
Whirlpool | Swirl tank to separate trub and hop debris from clear wort after boiling. May be present as standalone tank or integrated whirlpool fittings in the brewkettle. |
Heat Exchangers | Plate heat exchangers rapidly cool boiling wort to pitching temperature for yeast inoculation, preventing contamination and preservation of flavors. |
Glycol System | External cooling system with glycol and water mix which circulates through jackets around brew kettle, fermenters etc. to control temperatures. |
Piping | Food-grade stainless steel pipes, valves and pumps to transfer liquids between vessels and complete various brewhouse operations |
Control Panel | Houses all electrical controls, switches, automation systems like PLC to enable brewhouse operation and monitoring. |
5 BBL Stackable Fermenters Design & Layout
Key design aspects for 5 BBL brewhouse layout:
- Linear alignment allows easy transfer of mash and worts from one vessel to next using gravity, with minimal pipes.
- Keeping taller vessels to edge of space minimizes headroom required
- Easy operator access doors provided for manual cleaning
- Control panel located close to kettle for monitoring critical boiling stage
- External cooling and chilling systems placed peripherally
- Compact footprint minimizes brewhouse floorspace needs
Brewhouse layout during building planning stage is crucial to optimize material flow, staff movement, and output capacity later during brewery operations.
Customization Options for 5 BBL Brewhouses
While standard turnkey 5 BBL systems are available, many breweries seek customizations and add-ons to tailor the system to their specific goals. Some options include:
- Upgraded kettles: Installation of multi-vessel arrangements with more boiling capacity
- Advanced Automation: Touchscreen HMI, IoT connectivity, automated CIP systems
- Ergonomic improvements: Platform lifts, catwalks and stairs for vessel access, customized fittings
- Grain handling systems: Integrated roller conveyors, augers and lifts for grain transfer and milling –Special process accessories: Flavor dosing tanks, wort oxygenation addons, quality monitoring systems
When planning add-ons, brewers should evaluate benefits versus added complexity in operations and higher capital costs. Step-wise expansion options help balance costs against immediate and future production goals.
5 BBL Stackable Fermenters Pricing and Supplier Landscape
Table 3: Typical Pricing for 5 BBL Brewhouse Systems
Type | Price Range |
---|---|
Standard Manual | $80,000 to $120,000 |
Semi-Auto | $140,000 to $180,000 |
Fully Automated | $160,000+ |
Pilot Scale | Under $60,000 |
Used Systems | $50,000 to $100,000 |
In the US market, leading turnkey suppliers for 5BBL systems include:
Supplier | Starting Price | ** Offerings** |
---|---|---|
Specific Mechanical | $105,000 | Custom fabrications, manual and auto |
Portland Kettleworks | $96,500 | Quality kettles and vessels |
Stout Tanks & Kettles | $99,000 | Broad catalogue, customizations |
Premier Stainless | $125,000 | End-to-end fabrication, installation |
AAA Metal Fabrication | $98,000 | Custom unitank buildouts |
Pro Refrigeration | $140,000 | Integrated glycol chilling |
Emerson Brewing | $75,000 | Modular pilot systems |
Pricing can vary based on level of automation, custom features, vendor reputation and relationships, associated installation and shipping costs, etc. Quoting from multiple vendors is recommended.
5 BBL Stackable Fermenters Operations
Table 4: 5 BBL Brewhouse Maintenance & Operation Guidelines
Activity | Frequency | Purpose |
---|---|---|
Startup review | Daily | Verify lines & vessels are clean and ready for production |
Water heating | As needed | Power up steam/electric energy to get strike water to temp |
Grain dosing | Per batch | Transfer measured milled grains to mash tun |
Sparge | 60-90 mins | Rinse grains to extract all fermentable wort over time |
Wort boiling | 60-90 mins | Develop flavors and sanitize |
Trub separation | Post-boil | Settle hops and coagulants via whirlpool |
Heat exchange | After whirlpool | Rapidly cool clean wort before fermentation |
Clean-in-place (CIP) | Weekly | Clean vessels and pipes using caustics |
Preventive maintenance | Monthly | Inspect parts for wear & calibrate sensors |
In-depth cleaning | Quarterly | Take vessels offline for deep interior scrubbing |
For reliable functioning, the brewhouse equipment must be carefully operated within supplier specifications and cleaned at regular frequencies. Production planning should account for periodic maintenance downtime.
Choosing the Right 5 BBL Stackable Fermenters Supplier
Table 5: Qualities to Evaluate in a Brewhouse Supplier
Factor | Evaluation Criteria |
---|---|
Technical Expertise | Experience with systems at desired capacity and features; engineering quality and support standards |
Equipment Quality & Range | Build quality, materials, warranty; range of integrated brewhouse equipment available |
Custom Fabrication Skills | Ability to accommodate custom sizing, fittings, accessories, integrations |
Customer Service | Responsiveness to inquiries and support calls; after-sales installation and troubleshooting services |
Industry Reputation & Reviews | Talking to their existing customers to evaluate satisfaction levels and post-purchase support |
Business Sustainability | Years in operation, financial health to be a long-term brewhouse partner |
Taking time to thoroughly evaluate technical strengths versus asking price allows brewers to find the “sweet spot” supplier offering the best long-term value.
Key Pros & Cons of 5 BBL Stackable Fermenters Scale
Table 6: Advantages and Disadvantages of 5 BBL Systems
Pros | Cons |
---|---|
Allows substantially higher peak production than homebrew scale | Smaller output than large 20-30 BBL industrial systems |
Flexibility for brewpub onsite draught needs and offsite distribution | Limitations on very high gravity (>8% ABV) brews |
Lower capital investment than larger capacity brewhouses | Significant hands-on labor still needed for brewhouse operations versus fully automated systems |
Supports a full range of craft beer styles and experimentation | Additional fermentation and storage capacity needs to be planned for peak output |
Compact footprint fits smaller spaces than massive 30 BBL+ units | May still require upgrades in 3-5 years as brewery business grows |
For many startup and regional craft breweries aiming for intermediate capacity, 5 barrel systems hit a sweet spot in balancing production flexibility, output levels, investment budgets and space requirements.
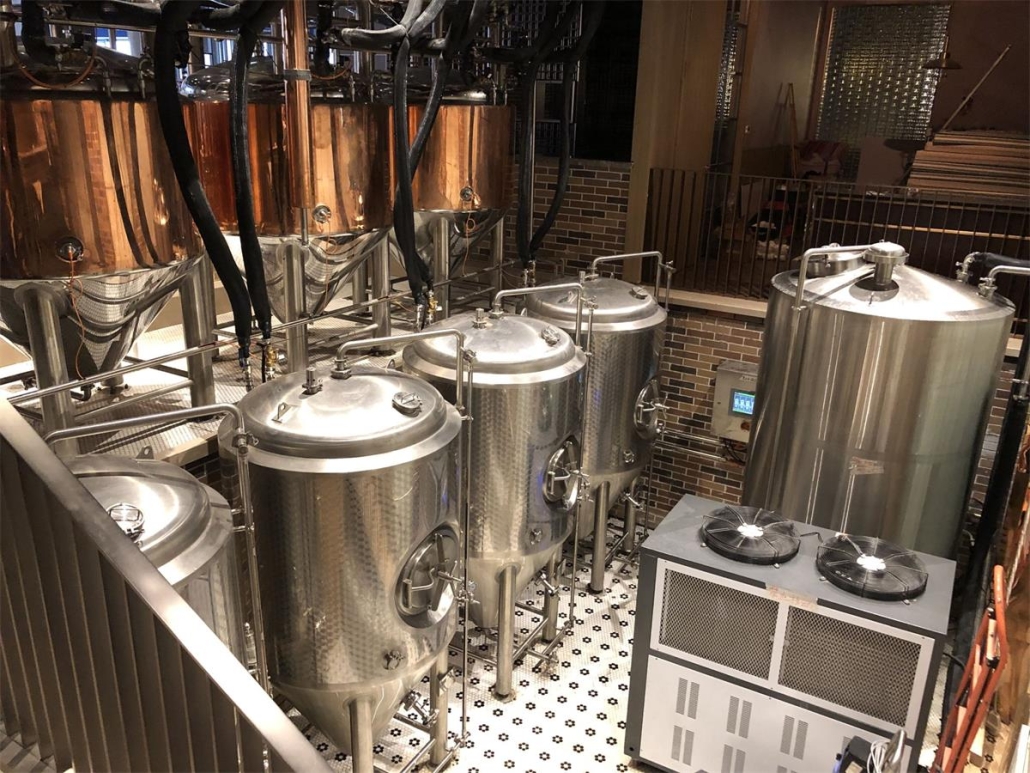
Frequently Asked Questions
Q: What is the brewhouse capacity needed for packaging 5000 barrels of beer annually?
A: To package 5000 barrels (BBLs) per year, a brewhouse capacity of around 10-15 BBL is recommended, assuming 1-2 brews per day on average to account for fermentation, filtering, storage and packaging time. So a 10 BBL or 15 BBL system could support 5000 BBL annual packaged output.
Q: What size boiler system is needed to power a 5BBL brewhouse?
A: A good benchmark is a 20 bhp (boiler horsepower) steam boiler system for powering the mash tuns, brew kettles and other heating operations of a 5 BBL brewhouse. This provides sufficient steam pressure and flow rates to quickly heat water and wort while matching the brewhouse capacity.
Q: How much floor space should I budget for a new 5 BBL brewhouse and associated utilities?
A: Ideally plan for 1500 – 2500 square feet for the 5 BBL brewhouse system including boiler room, glycol tanks, fermentation tanks and packaging area. This allows comfortable space for operations, cleaning and maintenance access around all vessels.
Q: What is the difference between 2-vessel, 3-vessel and 4-vessel brewhouse configurations?
A: 2-vessel are the simplest, with just a combined mash/lauter tun and brewkettle. 3-vessel separates the mash tun and lauter tun for greater efficiency and flexibility. 4-vessel keeps these separate and adds a whirlpool tank for settling out trub post-boil prior to fermentation. Additional vessels can be added like hop back or water deaeration unit for further complexity in multi-vessel configurations.
Q: Should I choose fully automated or manual operation for 5BBL?
A: Automated operation can improve consistency and reduce direct labor requirements but costs more upfront. For maximum flexibility at start, many brewers recommend getting semi-automated equipment that only uses automation for critical boiling stage but keeps affordability for small scale. This also develops firsthand experience before adding more automation down the road.
Q: What are the options for financing new or used brewhouse equipment purchases?
A: Beyond self-funding, options like equipment leasing, SBA small business loans and craft brewery specific financing from companies like Encore Finance group allow spreading out the capital investment over longer terms. Used equipment bought from other breweries also reduces initial purchase costs but may incur higher lifetime maintenance charges.