4 BBL Brite Tank Equipment Guide
4 BBL Brite Tank, also known as bright beer tanks, serve a key role post fermentation – clarifying and storing beer in preparation for packaging. This guide provides craft brewers an in-depth look at 4 barrel brite tanks including types, design considerations, usage guidelines and manufacturing specifications to help select the ideal solution.
Overview of 4 BBL Brite Tank
A 4 barrel or BBL brite tank has an internal capacity of 4 barrels or 124 US gallons. Brite tanks temporarily store filtered bright beer and build desirable carbonation levels through secondary conditioning before the beer gets packaged.
As a critical intermediary vessel between fermentation and packaging, brites clarify and stabilize the beer’s flavor profile. They are fabricated out of stainless steel for corrosion resistance and longevity. Two or more brite tank units are used to hold multiple batches for uninterrupted taps and packaging schedules.
Well designed brite tanks ensure more consistent beer quality and reduce losses allowing small breweries to maximize revenue from each batch.
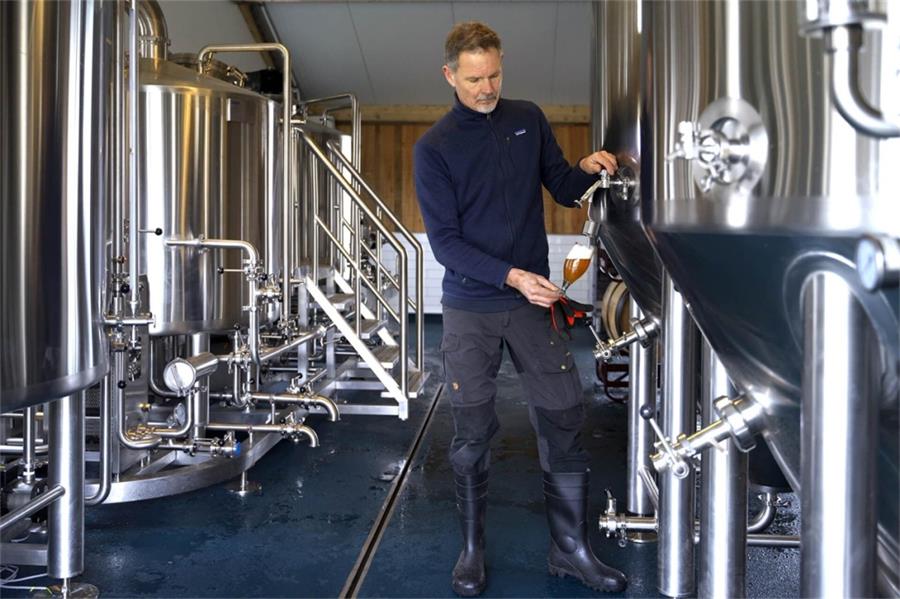
Types of 4 BBL Bright Beer Tank Configurations
Brite tanks come in different aspect ratios, vessel geometries and feature sets:
Table 1: Types of 4 BBL brite tank configurations
Type | Description |
---|---|
Vertical | Tall and slim with smaller footprint, height facilitates gravity transfers |
Horizontal | Shorter and wider, requires pumping to move beer |
Jacketed | Stainless jacket surrounds inner vessel for cooling/heating medium |
Glycol | Uses glycol circulating in jacket for precise temperature control |
Stackable | Allow compact vertical stacking to save floor space |
Conical Bottom | Forms yeast sediment cone for collection from bottom port |
Dish Bottom | Shallow beverage depth for maximizing cooling effect |
Sight Glass | Clear glass window to observe beer line level inside |
CoolFit | Tank insulation to minimize cooling loss |
Feature Sets | Pressure rated, cooling jackets, customizable valves |
Conical bottom brite tanks assist yeast sedimentation important for clean beer transfers, especially for lagers. Stackable units save costly brewery floorspace. Glycol jackets prevent temperature fluctuations – key to stable beer quality.
Overview of Beer Stabilization in Brite Tanks
The main goals of beer storage and conditioning in brite tanks are stabilization and clarification:
Beer stabilization involves achieving microbial and chemical stability to prevent deterioration of aroma, flavor, appearance and foam characteristics over time before packaging.
Key stabilization methods:
- Temperature adjustment – bringing beer to ideal 34-38°F equilibrium point
- Carbonation – saturation with CO2 to desired volumes
- Filtration prior to transfer if needed – membrane/DE powder filters
Beer clarification in brites is facilitated by:
- Cold conditioning – extended 2-4 week lagering for proteins to settle
- Finings additions – silica gel, bentonite clay adsorb particulates
- Biofiltration using immobilized yeast if needed
These techniques result in bright beer with substantially reduced haze and sediment yielding better appearance, foam retention and flavor stability.
Key Specifications of 4 BBL Brite Tanks
Standard 4 BBL brite tanks have the following typical target specifications:
Table 2: Typical specifications for 4 BBL brite tanks
Parameter | Typical Value | |
---|---|---|
Batch Volume | 124 gallons usable volume | |
Aspect Ratio | 1.6 – 2 times taller than wider | |
Construction | Stainless steel – grade 304 or 316L | |
Vessel Finish | Interior polish 20-50 grit | < |
Jacket | Cooling glycol, pressure rated | |
Operating Pressure | 2.5 bar (~36 psi) | |
Max Pressure | 4-6 bar (~60 psi) | |
Number of Ports | >4 – inlets, outlets, sediment, sightglass, sample | |
Controls | Glycol setpoint, level sensors | |
Materials | Stainless steel valves, fittings | |
Insulation | 1-2 inch foam insulation | |
Weight | 400 – 700 lbs |
Enhanced automation and telemetry capability allows remote tank monitoring and control – tracking real time inventory, temperature trends and packaged product rotational sequences.
4 BBL Brite Tank Design and Layout Considerations
Optimized brite tank design elements for functionality are:
Table 3: Key design factors for 4 BBL brite tanks
Section | Details |
---|---|
Vessel geometry | Height to diameter ratio for clarity; conical bottom tanks preferred |
Sidewalls | Slope for improved yeast sedimentation; sample port |
Tank bottom | 8-12° slope terminating in racking arm OCD fitting |
Manways | 12-16″ diameter sanitary hinged top manways |
Cooling jackets | Ensure 100%coverage by glycol/freon for uniformity |
Port fittings | Tri-clamp connections for durable seals, ease of assembly |
Rack arms | Rotating with 0.5-1 ft clearance from bottom |
Vents | Pressure rated DOT 400 lb cover, scrubber stone |
Level indication | External sight glass + electronic sensors |
Legs/stands | Height for gravity flow; floor mounting stands |
Ancillary equipment attached to brite tanks:
- Glycol chilling system paired to jackets
- CO2 purgeassembly and stone
- Carbonation stone
- Filtration module if needed
- CIP spray balls
Adequate access space for inspection, cleaning, maintenance activities around installed tanks should be provisioned.
Extent of Customization Possible with 4 BBL Brite Tanks
While 4 BBL brite tanks have standard functionality, custom enhancements are possible:
Table 4: Customization choices for 4 barrel brite tanks
Element | Customization Aspects |
---|---|
Automation | Advanced monitoring/controls – pressure, temps, inventory |
Fabrication | Vessel thickness, surface polish, welding standards |
Design | Manway size/numbers, fitting types and counts |
Port configuration | Number, sizing, placement of nozzles |
Finishes | Interior electropolish vs bead blasting |
Installation | Frames, fasteners, leg adjustability, cladding |
Features | Castors, cooling/heating jacket design, insulation type |
Compliance | ASME stamp if desired; export crating |
Engineered upgrades such as aseptic/CIP fittings, programmable nutrient dosing,è‡ªåŠ¨å®¡æ ¸ automated bottom draining for horizontal tanks, enable advanced functionality though cost more.
Range of Costs for 4 BBL Bright Beer Tanks
As a benchmark, 4 BBL brite tanks made in North America cost between $6000 to $14000 per unit depending on specifications:
Table 5: Supplier pricing range for 4 BBL brite tanks
Vendor | Offerings | Price Range per tank |
---|---|---|
JV Northwest | Standard tanks | $6000 – $9000 |
Pioneer | Conical bottom tanks | $9000 – $12000 |
Sprinco | Glycol jackets | $7000 – 10000 |
Steel Kin | Feature rich | $10000 – $14000 |
Premier Stainless | Budget | $6000 – $8000 |
Pro Tank | Turnkey install | $7000 – $11000 |
American Beer | Custom builds | $12000 – $16000 |
Chinese manufacturers provide lower cost tanks from $4000 upwards but US-made ones provide better welding quality and after sales support.
Budget $25000+ for a packaged solution with 2 brite tanks, associated glycol chillers, instrumentation and installation assistance.
Installation Best Practices for 4 BBL Brite Tanks
Proper brite tank installation ensures safety, full functionality and ease of maintenance:
Table 6: Installation considerations for 4 BBL brite tanks
Activity | Guidelines |
---|---|
Site selection | Mezzanines, tank farm space, sturdy floor, drainage |
Tank placement | Access for cleaning, inspections, located above packaging line |
Mounting | Fasten stands to ground per local seismic code |
Alignment | Use spirit levels for horizontal and vertical precision |
Stacking | Alternate tank connections front-back to ease access |
Safety rails | Mount around elevated tank stands |
Connections | Tri-clamp fittings for quick connect/disconnect |
Glycol setup | Ensure positive chill loop with no high points |
CO2 lines | Dropout pressure regulation at > 60 psi |
Controls | Temperature and level sensors with data logging |
Testing | Pressurize and hold to verify vessel integrity |
Sufficient space between multiple tanks and clearance from walls is ensured for cleaning and maintenance access. Proper tank grounding and insulation prevents condensation accumulating on exterior surface.
Maintenance Practices for 4 BBL Brite Tanks
Post-installation, 4 BBL brite tanks need periodic cleaning and upkeep for longevity:
Table 7: Maintenance best practices for brite tanks
Activity | Frequency and Tasks |
---|---|
Incidental inspection | Visually inspect exterior when in area |
Thorough inspection | Quarterly check all fittings, seals, fasteners, instrumentation |
Tank interior CIP | After each batch transfer out; verify cleaning efficacy |
Glycol loop | Monthly glycol concentration and system pressure checks |
Replacement | Annual sight glass, gaskets, sample valves |
Overhaul | Annual – polish welds, re-passivate, replace fittings |
Calibration | RTD sensors, CO2 regulators |
Documentation | Update equipment logs with inspection data |
Common preventive maintenance parts kept in inventory – replacement sample valves, caps, fittings, gaskets, sight glass and level switches.
Staff training in troubleshooting breather/vent clogs, glycol leaks, chilling inadequacies or flat beer issues reduces equipment downtime.
How to Select the Right 4 BBL Brite Tank
Choosing an appropriately designed and sized brite tank ensures achieving beer brightness targets:
Table 8: Key selection criteria for 4 BBL brite tank manufacturing
Consideration | Evaluation Aspects |
---|---|
Design expertise | Solutions tailored to beer type and service needs |
Fabrication quality | Welding standards, surface finish, passivation |
Dimensional accuracy | Vessel capacity and fittings alignment |
Lead time | Inventory availability, production schedule |
Cost | Pricing for standardized vs custom solutions |
Features | Monitoring/safety enhancements possible |
Flexibility | Easy integration with other cellar equipment |
References | Verify vendor installation track record |
Local access | Available servicing and technical support |
Ideally finalize an equipment layout drawing with tank quantities, dimensions and interconnect piping details before procurement.
Compare capital cost, production scheduling commitments and after sales support capability between vendors before orders.
Advantages and Limitations of 4 BBL Brite Tanks
Table 9: Comparison between key benefits and drawbacks of 4 barrel brite tanks
Advantages | Disadvantages |
---|---|
Optimal small batch capacity | Well matched to craft brewery weekly production |
Flexibility | Multi-use – ales, lagers; fruit, sours additions possible |
Process control | Improved beer quality consistency between batches |
Space efficiency | Stackable footprint if height available; reduced losses |
Cost | Lower capital cost than 7-15 barrel sized units |
Simplified transfer | Gravity drainage into packaging line |
Limitations | Single down tank disrupts packaging line |
Maintenance | Many consumables and parts for upkeep |
Small capacity | May need multiples for packaging demand |
Adjustability | Temperature and carbonation precision needs probes |
The ideal number of brite tank units depends on balancing packaging line scheduling flexibility versus available floorspace and capital budget.
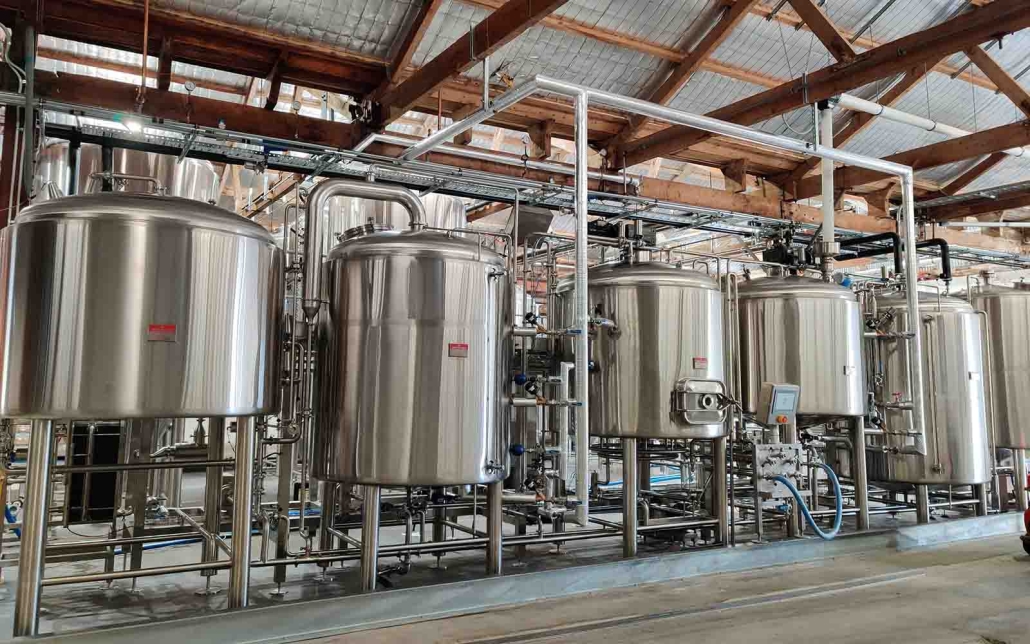
FAQs
Q: What is the purpose of a glycol jacket surrounding brite tanks?
Glycol jackets allow precise temperature control between 32-45°F by circulating chilled propylene glycol around the tank surface. This prevents temperature fluctuations that can negatively impact beer flavor stability.
Q: How many 4 barrel brite tanks are ideal for a small brewpub making ~1500 BBL annually?
For a brewpub targeting 1500 barrel annual packaged production, 4 brite tank units allow flexibility in packaging schedules. 2 brites for active beer stabilization while additional cleaned units are made ready for upcoming batches.
Q: How much CO2 should be used to carbonate beer in brite tanks prior to packaging?
For achieving desirable carbonation between 2.4-2.8 volumes CO2 in the brite tank, set the initial CO2 pressure between 15-18 PSI at 34°F. Precise volumes are tweaked using spunding valves on serving tanks.
Q: How often does passivation and electropolishing need to be redone for 4 BBL brite tanks?
The interior chromium oxide passivation layer protects tanks from corrosion and needs reapplication every 2-3 years. Electropolishing to smoothen interior welds and surface may be redone every 4-5 years when required.