30 BBL Brite Beer Tanks
30 BBL Brite Tank, also known as bright beer tanks or conditioning tanks, are pressure vessels used for storing, carbonating, clarifying and serving beer after fermentation and before packaging. 30 barrel (BBL) brite tanks allow medium-sized craft breweries to scale up production while ensuring beer quality.
Overview of 30 BBL Brite Tank
Key details about 30 BBL brite tanks:
- Capacity of 930 gallons or 30 barrels per tank
- Best for breweries aiming 5000-15000 BBL annual volumes
- Suit ale, lager and specialty beer conditioning
- Cost range from $50,000 to $150,000
- Needs temp control and CO2 injection systems
- Requires 1500-2500 sq ft of cellar space
- Flexible sizing, number of tanks customized to brewery growth plans
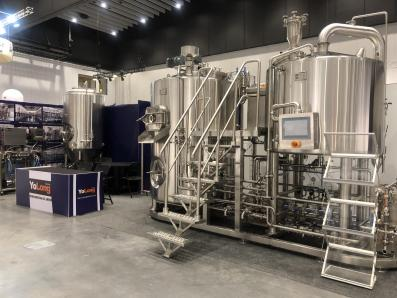
30 BBL Brite Tank Equipment Guide
The major equipment modules related to brite tank operations are:
Core Equipment
- 30 BBL stainless steel brite tanks – vertical or horizontal
- Glycol/refrigerant cooling systems
- CO2 distribution manifold and stone filters
- CIP spray balls and sight glasses
- Tank stands, ladders, piping, insulation
Monitoring & Control
- Temperature sensors and digital indicators
- Pressure sensors and relief valves
- Flow meters and valve control panels
- Automated cleaning sequencers
Transfer Mechanisms
- Centrifugal or lobe pumps
- Hoses, filters, fittings and tools
- Canning/kegging lines after tanks
Beer Maturation Process
The typical beer maturation steps utilizing 30 BBL brite tanks are:
- Transfer from fermenters to brite tank via pumps/hoses
- Yeast settling aided by cooling for 2-3 days
- Carbonating to required CO2 volumes using gas injection
- Clarifying and aging at cold temps for 1-4 weeks depending on beer type
- Periodic quality checks during conditioning phase
- Filtered beer transferred to packaging lines
30 BBL Brite Tank Specifications
Capacity & Numbers
Each 30 BBL brite tank holds one 930 gallon batch. Numbers needed are based on fermentation capacity and packaged inventory targets – typically 6 to 12 tanks.
Minimum Cellar Space
Plan for 1500 to 2500 sq ft of temp controlled cellar room to house all brite tanks, cooling systems, transfers and open work areas.
Design & Layout
Standard vertical stands allow stacking tanks in rows above others to optimize space. Horizontal mounts have ease of access. Linear pipelines simplify interconnections.
Customization
Tank number, cellaring space, cooling, carbonation, piping, automation systems are customized to suit brewery’s beer portfolio, packaging formats and future growth plans.
Suppliers & Pricing
Vendor | Price Per Tank |
---|---|
JV Northwest | $60,000 – $125,000 |
Specific Mechanical | $50,000 – $100,000 |
Sturtevant Inc | $75,000 – $140,000 |
Premier Stainless | $65,000 – $150,000 |
AAA Metal Fabrication | $55,000 – $120,000 |
Installation, Operation & Maintenance
Proper installation, operation and maintenance of brite tanks optimize performance, safety and longevity.
Activity | Key Considerations |
---|---|
Installation | Performed by tank vendors onsite over 2-3 months lead time. Involves interconnecting cooling & CO2 systems, piping between tanks and packaging lines. |
Operation | Following SOPs for filling, monitoring, quality checks and packaging line transfers. Coordinating between cellar and packaging teams. |
Maintenance | Daily/weekly cleaning protocols crucial inside tanks and pipe circuits to avoid contamination and deposits. Annual servicing contracts for cooling systems and valves. |
How to Select Brite Tank Supplier
Important criteria for selecting the brite tank vendor:
Parameter | Evaluation Aspects |
---|---|
Previous Supply Experience | 50+ tank installs for craft breweries of comparable scale |
Tank Quality | High grade stainless steel, welds and finishing to prevent corrosion |
Cooling Expertise | Glycol chilling or refrigeration system design experience needed |
Automation Capabilities | Supply of sensors, valve panels, cleaning sequencers integrated with tanks |
Customization Range | Flexibility to modify tank numbers, fittings, layouts |
Pricing | Competitive rates and component-level cost transparency |
Delivery Scheduling | Ability to deliver within 4-6 months standard lead time |
Pros of 30 BBL Brite Tank
Maturation Quality – Precise temperature and carbonation control allows achieving desired clarity, color and flavor objectives for each beer type.
Inventory Buffer – Multiple tanks enable building up finished beer inventory to meet packaging line capacity and demand fluctuations.
Flexibility – Sufficient cylinders facilitate trying out new recipes, aging special releases, while regular mainstays can use dedicated tanks.
Efficiency – Automated cleaning, cooling and carbonation improve process consistency between tanks and across batches.
Scalability – Expandable by adding more tanks without needing entirely new cellar construction.
Limitations of 30 BBL Tanks
Floorspace Needs – Cellars require significant dedicated real estate within breweries along with ceiling height.
Specialized Staff – Cellar experts needed for quality assurance testing, sampling, troubleshooting issues between fermentation and packaging.
Upkeep Costs – Intensive cleaning procedures, cooling utility expenses, maintenance contracts amount to significant operating overheads.
Capital Costs – Large investment needed upfront even though cost per barrel decreases with scale. Cash flows may take 2-3 years to break even.
Process Optimization – Standardizing procedures across different beer types while retaining flexibility requires operational experience with multiple tanks.
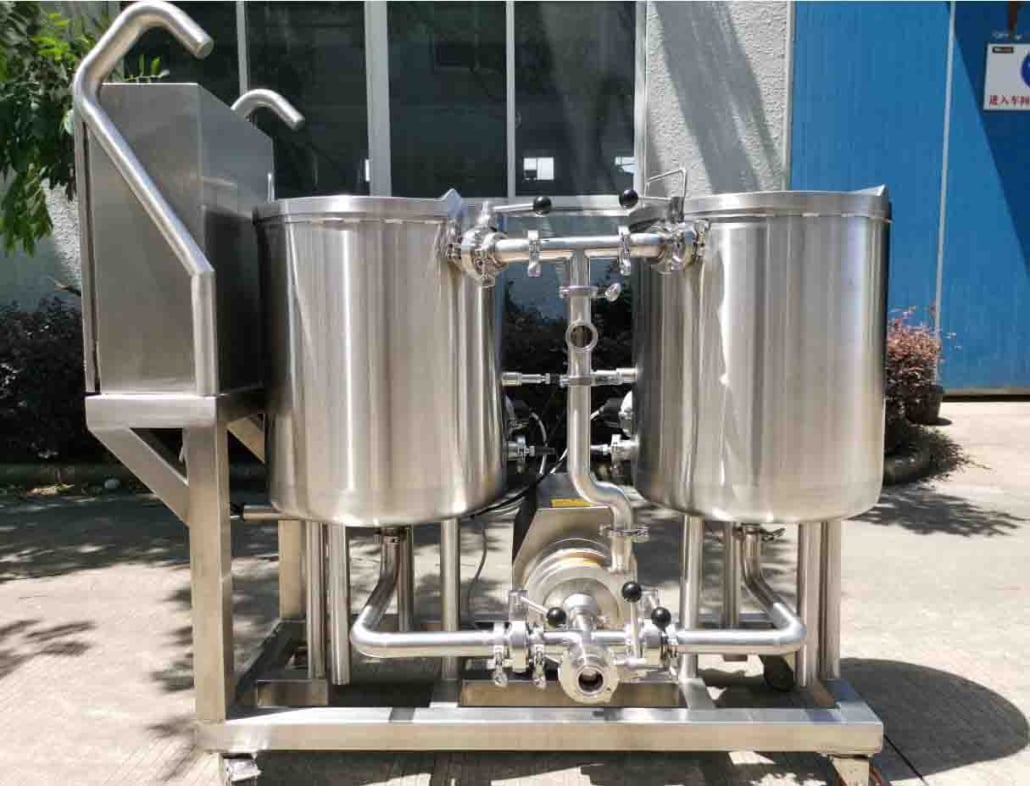
FAQ
How many 30 BBL brite tanks are ideal for a 5000 BBL/year brewery?
- Typically 8-10 tanks are recommended for flexible storage, refermentation and packaging operations supporting those volumes. This allows 3-4 turns per month per cylinder.
What types of beers can use 30 BBL brite tanks?
- Ales, lagers, and most specialty releases like imperial stouts, heavily hopped IPAs can leverage these tanks. Some sour or wild yeast beers may need dedicated barrels or rooms.
How much cellar space do 6-8 30 BBL brite tanks need?
- Allow for 2000 – 2500 square feet for the tanks plus walkways, cooling systems and transfer areas. This enables sufficient operability.
What are the cost differences between horizontal vs vertical 30 BBL brite tanks?
- Vertical tanks cost 10-15% lower than horizontal tanks. However horizontal tanks provide easier access and visual inspection during filling. Choice depends on layout constraints.
Should 30 BBL brite tanks be stacked or placed side by side?
- Both work well. Stacked layout reduces floor space needs but needs sufficient operational clearance between layers and tank tops. Side by side allows easier access but needs more linear space.