30 BBL Brewing Equipment
30 BBL brewing equipments are optimized for rapidly scaling craft brewers aiming to expand distribution while retaining quality. This guide covers considerations for planning and operating 30 BBL brewhouses.
Overview of 30 BBL brewing equipments
With an annual capacity approaching 10,000 barrels, 30 BBL brewhouses position growing craft breweries for wider retail reach and added wholesale accounts.
Complete 30 BBL brewhouse package contains major equipment like:
- 30 BBL Mash Tun
- 30 BBL Lauter Tun
- 30 BBL Kettle
- Whirlpool
- Heat Exchanger
- Fermentation Tanks
- Brite Tanks
- Piping, pumps and controls
Additional equipment like grain handling, CIP, air compressors, chilling systems and wastewater are also included in turnkey configurations by reputable vendors.
When evaluating and designing 30 BBL brewhouses, key considerations include:
Production Volume
Carefully match brewhouse capacity to forecasted annual barrelage to ensure good utilization rates rather than over-building. A rule of thumb is 120-250 barrels output per batch.
Infrastructure Requirements
Larger equipment and batches drive up ancillary infrastructure needs – boiler capacity, chilling, wastewater, etc. Plan for added capital costs for these systems…
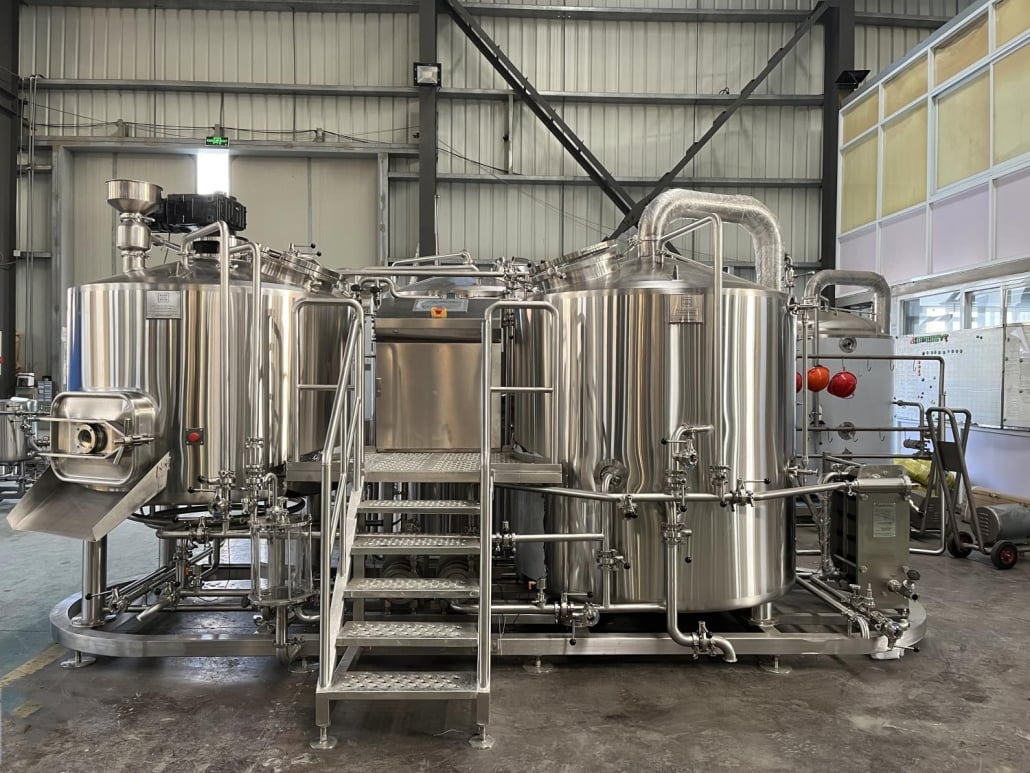
Types of 30 BBL brewing equipment
The major vessels and components in 30 BBL commercial brewing systems include:
Equipment | Description |
---|---|
Mash Tun | Mixes crushed malt with hot water for starch conversion to sugars via natural enzymes |
Lauter Tun | Separates wort from spent grains after mashing |
Kettle | Boils wort with hops for bitterness, flavor and aroma |
Whirlpool | Settles out particulates after boil for clear wort |
Heat Exchanger | Rapidly cools hot wort to pitching temperatures |
Fermenters | Ferments cooled wort into beer over 5-7 days on average |
Brite Tanks | Carbonate, clarify and store beer prior to packaging |
Piping | Food-grade stainless steel pipes transferring liquids |
Pumps | Centrifugal, rotary or piston pumps for fluid transfer |
Controls | Automated measurements, valves and record-keeping |
30 BBL Brewing Process
A typical 30 barrel four vessel brewhouse utilizes the following modular process flow:
Milling – Barley malt is dry milled with roller mills or hammer mills for grain crushing to expose starch for mashing while controlling flour.
Mashing – Milled grains are mixed with hot water in the mash tun for natural enzymatic conversion of starches into fermentable sugars. Usually conducted in staggered temperature rests targeting various sugar profiles.
Lautering – The mash seperates into sweet wort and spent grain in the lauter tun. Spent grains are discharged while clear wort recirculates before transferring to the brew kettle.
Boiling – In the brew kettle, wort is sterilized and hopped for bitterness, flavor and aroma at rolling boil. Evaporation concentrates sugars and inhibits microbial growth.
Whirlpool – Coagulants help sediment settle as a cone in the whirlpool vessel when rotated after boiling, allowing transfer of clear wort to the heat exchanger.
Cooling – Plate heat exchangers rapidly cool hot wort to prevent contamination and prepare for fermentation yeast pitch.
Fermentation – Yeast converts sugars in cooled wort to CO2, alcohol and flavors over approximately one week before transferring to conditioning tanks.
Conditioning – Beer is carbonated to style specifications and clarified in conditioning tanks prior to packaging.
Packaging – Bright beer moves to bottling, canning or kegging lines for packaging final product.
30 BBL System Suppliers and Pricing
Supplier | Price Range |
---|---|
AAA Metal Fabrication | $350,000 – $1,100,000 |
MW&L | $400,000 – $1,200,000 |
Premier Stainless | $375,000 – $1,250,000 |
Psycho Brew | $450,000 – $1,400,000 |
Portland Kettlehouse | $550,000 – $1,500,000 |
JV Northwest | $425,000 – $1,350,000 |
Pricing varies based on materials (stainless vs. carbon steel), valves and automation selected along with any customization needs. Get quotes from multiple vendors.
Key Price Factors:
- Stainless adds ~30% versus steel clad carbon steel vessels
- Grain handling systems $30,000+
- Automation controls from ~$75,000+
- Installation, shipping and taxes additional..
Operation, Cleaning and Maintenance
Activity | Description | Frequency |
---|---|---|
Calibration | Ensure sensors and measurements are accurate. | Monthly |
Inspections | Check vessels, valves and pipes for damage/leaks. | Daily |
CIP | Automated clean-in-place cycles. | Each batch |
Tank purging | CO2 line clearing prevents oxidation. | Quarterly |
Preventative maintenance | Tunings, lubrication and adjustments. | Annual |
How to Choose a Brewhouse Supplier
Key factors in selecting 30 BBL brewing system partner:
Criteria | Considerations |
---|---|
Budget | Equipment pricing, installation fees, shipping costs |
Lead time | Production planning schedules, financing |
Customization | Match layout, dimensions and flow requirements |
Automation | Level desired for operation, cleaning and record-keeping |
Experience | Years in business, number of systems built |
Service | Installation help offered, maintenance contracts |
Certifications | ASME, UL, OSHA, CRN conformance to North American standards |
Warranty | Coverage terms for labor, components, vessels |
References | Feedback from existing customers |
Get quotes from at least 3 vendors to balance price, construction quality and service reputation. Prioritize suppliers accommodating custom options tailored to your brewhouse needs…
Pros and Cons of 30 BBL Systems
Pros | Cons |
---|---|
Optimized batch size for rapidly growing breweries | Larger batches risks quality control vs. smaller batches |
Enables wider production diversity | Significant infrastructure investment needed |
Economies of scale improve margins | Seasonal demand fluctuations can hurt utilization |
Headroom for continued growth before maxing out capacity | Heightened QA/QC discipline critical |
Option to sell excess capacity via contract brewing | – |
Key Takeaways
- Match 30 BBL system capabilities to production plan and expansion roadmap
- Carefully evaluate brewery infrastructure upgrades required
- Gets growing brewers to ~10,000 BBL annual capacity
FAQs
Q: What size batches can 30 BBL breweries produce?
A: With ~200 barrels per batch, 30 BBL breweries can reach nearly 10,000 barrels annual capacity operating at reasonable utilization rates.
Q: What raw materials are needed for 30 BBL brewhouses?
A: Key consumables are malt, hops and yeast. A 30 BBL system requires ~900-1500 lbs per batch plus filtration media, cleaners, lubricants etc. Proper storage space is necessary.
Q: Should breweries buy new or used equipment?
A: High quality new 30 BBL equipment ensures longevity, efficiency and ease of maintenance for rapid growth phase breweries. But used systems with upgraded components can also offer big cost savings.
Q: How many people are required to operate a 30 BBL brewery?
A: Excluding the taproom, a 30 BBL production scale brewery can be operated by head brewer plus 4-6 employees handling cellar, packaging, inventory, distribution and assistant brewing. Use contractors to assist with seasonal spikes or large expansion projects.
Q: What quality control is needed for 30 BBL batches?
A: Increased lab testing and record-keeping for raw materials, in-process metrics and finished beer become essential at this scale. Tighten SOPs and implement lean manufacturing techniques to ensure consistency.