1 BBL Brewing Systems
A 1 BBL brewing system brewing system is a critical piece of equipment for small to mid-size craft breweries producing 31 gallons per batch. This complete guide provides craft brewers, homebrewers, and hospitality business owners everything needed to understand 1 BBL brewing system from an unbiased perspective focused on capability analysis.
Overview of 1 BBL brewing system
A 1 barrel (BBL) brewing system produces 31 gallons per batch and is suitable for nano, micro, and brewpub operations producing up to 500 barrels annually. 1 BBL systems empower small producers to create high quality craft beer in small batches while retaining flexibility.
This guide covers key considerations when researching 1 BBL brewing systems:
- Equipment Types and Components
- Brewing Process and Batch Size
- Capacity, Dimensions, Layout, and Customization
- Suppliers and Price Range
- Installation, Operation, and Maintenance
- How to Select the Right System and Supplier
- Pros, Cons, Advantages, and Limitations
Detailed comparisons and objective recommendations are provided to help buyers make optimal equipment decisions aligned to business goals, space constraints, and budget.
An FAQ section addresses common questions on 1 BBL system selection, installation, operations, troubleshooting, upgrades, and more. Supplier references facilitate further research.
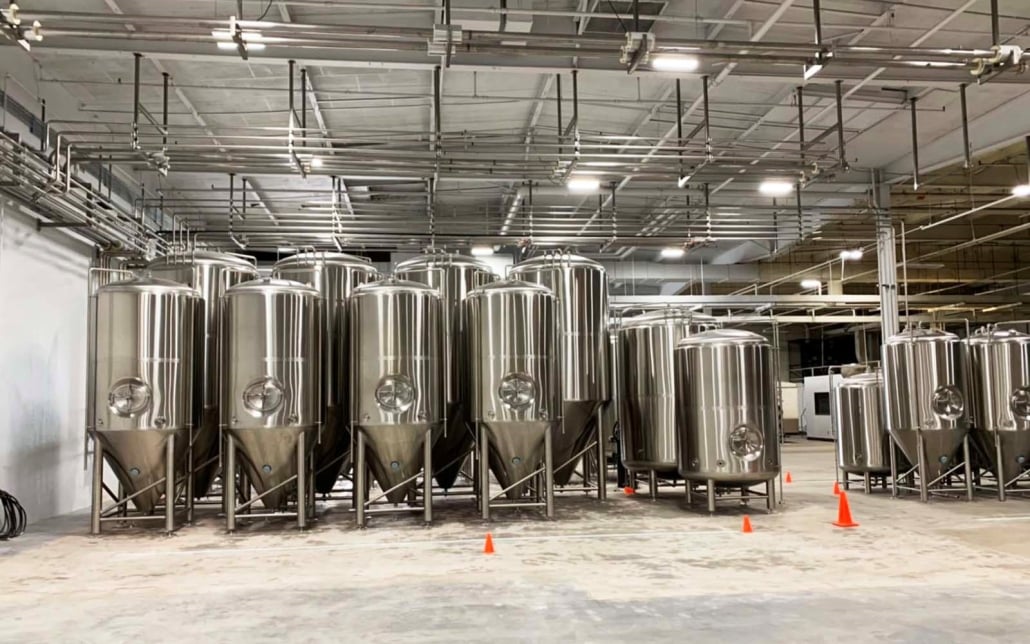
Types of 1 BBL brewing system
1 BBL brewing systems are available in manual and automated configurations from a range of suppliers. Main types include:
Table 1: Types of 1 BBL Brewing Systems
System Type | Description |
---|---|
Manual | Basic manually-operated 1 BBL system without automation |
Semi-Automated | Contains some automated features like temperature control |
Fully Automated | Fully automated operation with programmable recipes |
Turnkey | Comes with all equipment needed to start brewing professionally |
Custom Fabricated | Tailor-made system designed to customer specifications |
Within these types, there is tremendous variety in terms of layout, materials, quality, features, batch frequency, and degree of customization. Objective comparison on technical specifications is advised prior to selection.
1 BBL brewing system Brewing Process
The typical professional brewing process followed on a 1 BBL system is outlined below. Actual steps may vary based on recipe, equipment capabilities, and brewer preferences:
Mashing – Mixing milled grains with hot water for starch conversion
Lautering – Separating sweet wort from spent grains
Boiling – Boiling wort with hops for aroma, flavor, bitterness
Whirlpooling – Swirling wort to remove trub and hops
Cooling – Rapidly cooling boiled wort prior to fermentation
Fermenting – Adding yeast for alcohol production
Maturing – Lagering or aging prior to packaging
Filtration – Removing yeast and particles for clarity
Carbonation – Injecting CO2 for desired carbonation levels
Packaging – Kegging, canning, or bottling final beer
Cleaning & Sanitation – Critical between batches
The degree of manual labor versus automation varies dramatically between basic, semi-automated, and fully automated 1 BBL systems. Buyers should assess where they fit on the automation spectrum based on production goals, budget, and desired ease-of-use.
1 BBL System Capacity, Dimensions, Layout, and Customization
When selecting a 1 BBL brewing system, available space in a brewery or taproom is often the limiting factor. Understanding equipment sizes, layout considerations, and customization options is critical.
Table 2: 1 BBL Brew House Specifications and Customization Options
Parameter | Details | Customization |
---|---|---|
Batch Size | 31 gallons or 1 barrel | Fixed at 31 gallons |
Physical Footprint | Varies, approx 5′ x 5′ minimum | Modular components allow extensive layout options |
Height | 7 to 10 feet typical | Lower heights possible with compact custom designs |
Boil Kettle Size | 40 gallons typical | Available from 30 – 50 gallons + |
Hot Liquor Tank Size | 40 gallons typical | Available from 30 – 50 gallons + |
Fermentation Tanks | Typically 3x 31 gallon units | Choose number and size of fermenters and brite tanks |
Electrical Requirements | 220V, 30 amps typical | Consult experts on electrical needs |
Grain Handling System | Various options available | Fully customize based on brewery design |
Brew Sculpture Arrangements | Many configurations possible | Completely flexible sculpting to fit available space |
Experienced brewery design consultants can assist with specialized layouts tailored to available room dimensions, desired capacity, budget, and aesthetics. Unique 1 BBL sculpting arrangements help small producers creatively maximize limited space.
1 BBL brewing system Suppliers and Price Range
Reputable 1 BBL system suppliers offer a breadth of tiered products at different price points with varying quality and features. When comparing suppliers, verify capabilities to ensure alignment with business goals.
Table 3: 1 BBL Brewing System Suppliers and Price Ranges
Brand & Model | Description | Price Range |
---|---|---|
Craftmeister Fully Automated | Fully automated, programmable tier | $100,000 to $150,000 |
Craftmeister Semi-Automated | Partial automation with smart control | $60,000 to $100,000 |
Craftmeister Manual | Basic manual operational tier | $30,000 to $60,000 |
EcoBrewPro | Mid-tier semi-automated systems | $40,000 to $80,000 |
Budget Brewhouse | Lower-end basic manual systems | $15,000 to $40,000 |
Custom 1 BBL Fabricators | Custom systems with modular components | $50,000 to $250,000+ |
Notes:
- Prices may fluctuate based on material costs and equipment margins
- Warranties, shipping, installation, training & support vary dramatically between supplier tiers
- Cheaper systems often reflect very basic function and quality
- Custom systems allow specialized features but have higher unit costs
Thoroughly vet suppliers on reputation, service history, component quality, and consultant expertise in your region prior to purchase. Visit existing breweries using the equipment if possible.
1 BBL brewing system Installation, Operations, and Maintenance
Installing and operating a 1 BBL brewing system requires reasonable competence with commercial plumbing, electricity, welding, fabrication, logistics planning, layout design, brewing process engineering, cleaning protocols, recipe formulation, quality control, troubleshooting, and preventative maintenance.
While automated systems simplify many complex tasks, specialized skills are still needed for startup, cleaning, repairs, upgrades, and optimizing output. Carefully evaluate team capabilities during equipment selection.
Table 4: 1 BBL System Installation, Operation, Maintenance Requirements
Activity | Details | Personnel |
---|---|---|
Installation | Physical setup, assembly, utilities, inspections | Contractors, electricians, technicians |
Startup & Commissioning | Initial system check-out and operations | Commissioning engineers, external consultants |
Cleaning & Sanitation | Critical daily/weekly operations | Trained brewers + quality control |
Brewing Operations | Making consistent quality beer at scale | Skilled brewmaster + production team |
Preventative Maintenance | Routine upkeep for longevity | Multi-disciplinary team + external contractors |
Break-fix Troubleshooting | Diagnosing + resolving system failures | Experienced head brewer + technicians |
Upgrades & Retrofits | Enhancing systems to add capabilities | Brewery consultants + specialty vendors |
Safety Management | Compliance monitoring, training | Safety specialists + operational leadership |
As seen above, specialized personnel and partners are needed during the full equipment lifecycle. Carefully evaluate capabilities early when budgeting for a 1 BBL system. Invest in training programs, even basic ones, to build critical knowledge prior to commissioning new equipment. Thoroughly understand service and support contracts.
How to Select the Right 1 BBL brewing system
With such a wide variety of 1 BBL systems on the market from competing suppliers, the evaluation and selection process can be challenging. Use an objective methodology focused on core requirements:
Table 5: How to Choose the Right 1 BBL Brewing System
Selection Process Steps | |
---|---|
1 | Clearly define production goals and capabilities needed |
2 | Determine space available, delivery access, utility constraints |
3 | Calculate electricty loads and wastewater production |
4 | Shortlist equipment models that align with top priorities |
5 | Issue detailed RFQ to suppliers with precise specifications |
6 | Compare RFQ responses objectively on stated parameters |
7 | Ask for existing brewery references using the same equipment |
8 | Visit sites personally to inspect quality and talk to users |
9 | Validate supplier experience levels in region |
10 | Negotiate contract with commissioning & support specifics |
11 | Begin relationship with transparent communications |
By using structured competitive bidding and focusing on supplier relationships, buyers give themselves the best chance at acquiring equipment that enables their brewery vision within practical constraints.
Do not assume all systems are equivalent – extreme due diligence is required to avoid crippling disasters after purchase. This market has examples of both stellar and nightmarish supplier experiences. Protect yourself by verifying every claim.
Pros, Cons, Advantages and Limitations of 1 BBL Systems
While extremely versatile and scalable, 1 BBL brewing systems have intrinsic benefits and limitations brewers must consider before investing in the equipment.
Table 6: Pros, Cons, Advantages and Limitations of 1 BBL Brewing Systems
Parameter | Details |
---|---|
Pros | Flexible production scale, small batches enable innovation & customization, localized manufacturing |
Advantages | Lower capital investment than larger systems, taproom integration potential |
Cons | Require significant manual labor for basic systems, limit growth capacity |
Limitations | Space constraints in taprooms, restricted branding & visibility, maintenance challenges |
By understanding the trade-offs objectively from the start, brewers can create business models leveraging the pros while avoiding the cons through smart resource allocation and careful capacity planning.
With pragmatic operations strategy and personnel development, 1 BBL systems offer a launchpad for small entrepreneurial brewers to cost-effectively enter manufacturing while delighting patrons with unique high quality beers.
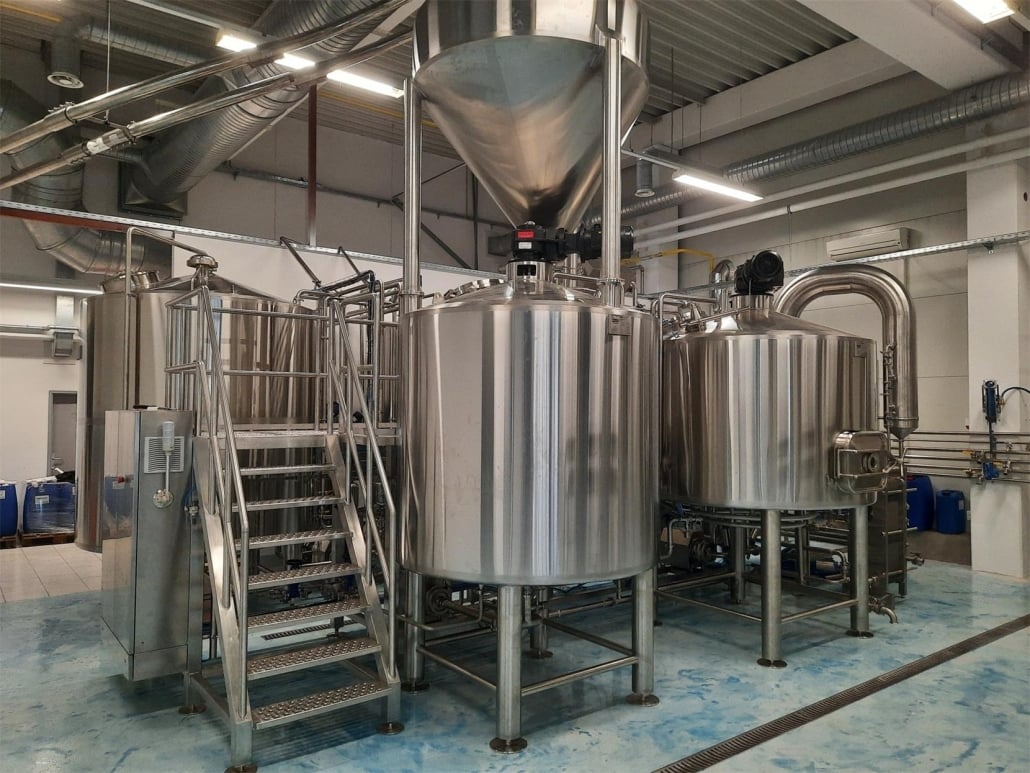
FAQ
FAQ Table 1 – 1 BBL Brewing System Installation Questions
Question | Answer |
---|---|
What contractors will I need? | Specialized trades like electricians, plumbers, refrigeration technicians, millwrights. |
What delivery logistics should I account for? | Measure all doors & corridors to plan rigging & installation. Forklifts often required. |
Who oversees contractor coordination? | Appoint project manager to coordinate teams during commissioning. |
When should I order fermentation tanks? | 3-6 month lead time typical – order early! |
FAQ Table 2 – 1 BBL Brewing System Operation Questions
Question | Answer |
---|---|
What operational training is included? | Vet supplier training capacity – should provide multi-week brewer training programs onsite. |
How many operators do I need per shift? | After initial training phase, target 2-3 skilled brewers needed per average production day. |
How much beer do I need for testing? | Make large test batches & resist temptation to sell – quality acceptance essential before official launch! |
What key metrics should I track? | Yield, rate of production, unit economics, asset utilization, maintenance cadence. |
How do I source ingredients & verify quality? | Establish supply chain early! Audit ingredient quality continually – never compromise. |
FAQ Table 3 – 1 BBL Brewing System Maintenance & Troubleshooting Questions
Question | Answer |
---|---|
What preventative maintenance is vital? | Document all PM tasks for valves, pumps, vessels, sensors, gaskets. Follow rigorously. |
What spare parts should I stock? | Common failure items – gaskets, seals, fittings, washers, fasteners, small valves. |
How much downtime is typical? | Schedule maintenance downtime windows proactively during low utilization periods. |
Who do I call for support & repairs? | Ensure supplier provides emergency response capabilities as backups. |