30 BBL Brewhouse Systems
A 30 BBL Brewhouse is a medium-sized professional beer brewing system with a capacity of 930 gallons per batch. This system allows craft breweries to increase production while retaining flexibility to brew different beer recipes.
Overview of 30 BBL Brewhouse
Some key details about 30 BBL brewhouse systems:
- Batch size: 930 gallons or 30 barrels
- Best for medium-sized craft breweries producing 4,000-10,000 barrels annually
- Requires significant brewery space – upto 5,000 sq ft
- Equipment cost from $250,000 to $1 million
- Takes 4-5 brewers to operate optimally
- Production volumes of 150-300 BBLs weekly
- Flexible enough for wide variety of beer styles
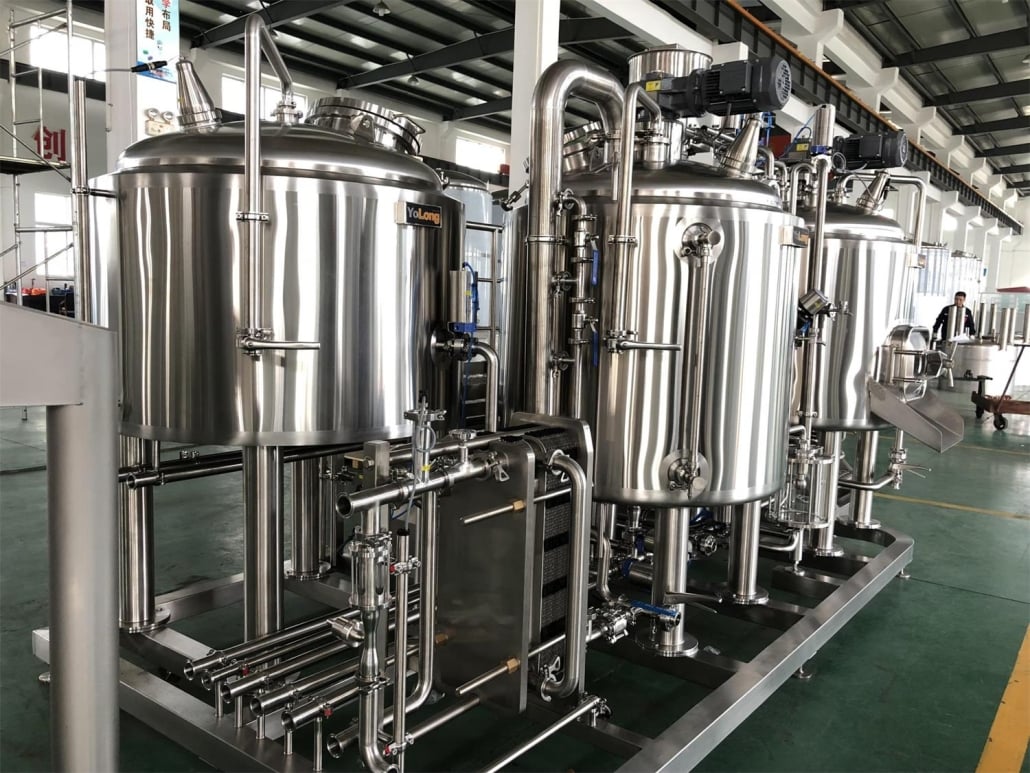
Brewhouse Equipment Guide
The 30 BBL brewhouse setup contains major equipment like:
Brewhouse Vessels
- 30 BBL Mash tun – mixes milled grains with hot water to extract sugars
- 30 BBL Lauter tun – separates sweet wort from grains
- 30 BBL Brew kettle – boils wort with hops to impart flavor
Fermentation & Maturation
- Glycol chilled 30 BBL Fermenters – stainless steel or plastic
- 30 BBL Bright Beer Tanks
- Kegging/canning equipment
Auxiliary Systems
- Grist case for milling
- Hot liquor tank for heating water
- Whirlpool for separation
- Piping, pumps, valves, controls
- Steam boiler, chillers, cooling towers
Other Infrastructure
- Grain handling system
- Ingredient storage areas
- Cleaning and sanitation equipment
- Packaging lines
- Warehouse space
30 BBL Brewhouse Process
The typical brewing process followed on a 30 BBL system is:
- Milling – The grist case mills barley malt and adjunct grains to specific sizes optimized for mashing
- Mashing – Milled grains are mixed with hot water in the mash tun to extract fermentable sugars
- Lautering – The sweet wort is separated from spent grains in the lauter tun
- Boiling – The wort is boiled in the brewkettle and hops added at different times for bitterness, flavor and aroma
- Whirlpool – Trub and hops residues are separated from clear wort
- Cooling – Wort is quickly cooled to pitching temperature before yeast is added
- Fermentation – Yeast ferments sugars into alcohol and CO2 for about 1-2 weeks
- Maturation – Green beer is conditioned for clarity, carbonation and flavor
- Packaging – Beer transferred to kegs, cans or bottles
30 BBL Brewhouse Specifications
Capacity & Batch Size
A 30 BBL brewhouse allows brewing batches of 930 gallons or 30 barrels. Larger batch sizes leads to faster production compared to smaller 10-20 barrel systems.
Brewery Floor Space Needed
Allow for at least 3000-5000 sq ft floor space for the brewhouse vessels, fermentation room and storage. This provides sufficient room for operation and future expansion.
Layout & Design
The equipment layout is customized for the available space and expansion plans. Both linear configurations or 2-tier layouts are possible. Ergonomics for material movement and operator access are key considerations.
Customization
While standard 30 BBL designs are available, it is preferable to customize vessels and layout to meet specific production goals, beer types, water chemistry and quality needs.
Brewhouse Suppliers & Pricing
Company | Price Range |
---|---|
Specific Mechanical Systems | $250,000 to $500,000 |
JV Northwest | $350,000 to $750,000 |
Premier Stainless Systems | $400,000 to $1 million |
AAA Metal Fabrication | $300,000 to $600,000 |
Brewmation | $350,000 to $850,000 |
Installation, Operation & Maintenance
Proper installation, operation and preventive maintenance are vital for efficiency, safety and longevity of a 30 BBL brewhouse system.
Activity | Details |
---|---|
Installation | Performed by equipment manufacturer. Requires 3-6 months lead time. Involves assembling vessels, piping, wiring, controls onsite as per layout. |
Operation | Brewer training needed on using the automated brewhouse control system and devices. Daily production planning and coordination between 4-5 brewers per shift. |
Maintenance | Daily cleaning protocols crucial. Preventive maintenance as per manufacturer guidelines on vessels, valves, pumps, sensors, automated sequences. Annual servicing contracts recommended. |
How to Select Brewhouse Supplier
Choosing the right brewhouse supplier for build and installation quality requires evaluating across parameters:
Criteria | Evaluation Aspects |
---|---|
Technical Expertise | Prior experience of supply to 50+ breweries, expertise across equipment modules, inhouse engineering capabilities are preferred |
Quality & Durability | Use of high grade stainless steel forcorrosion resistance, quality manufacturing processes, documented pressure tests, long equipment lifespans |
Customization Range | Custom options for vessels based on beer type plans, flexibility for future add-ons or expansion |
Cost | Competitive pricing with itemized breakdown of options |
Lead Time | Ability to deliver within schedule of 4-6 months standard |
References | Check feedback from existing customers on product and service quality |
Local Support | Installation guidance, operator training, continued maintenance support necessary |
Advantages of 30 BBL Brewhouse
Flexibility – Can produce ales, lagers, and wide variety of specialty beers. Support more innovation and experimentation.
Efficiency – Automated process increases speed, minimizes losses and manual work compared to smaller systems.
Profitability – The batch size results in good economies of scale once distribution pipelines established in local markets. Ability to supply to pubs as well as retail.
Quality – Capability for precise temperature control and measurement enables brewmasters to control repeatability between batches.
Expandability – Additional fermenters and storage can be added as market grows. Even larger brewhouse feasible later.
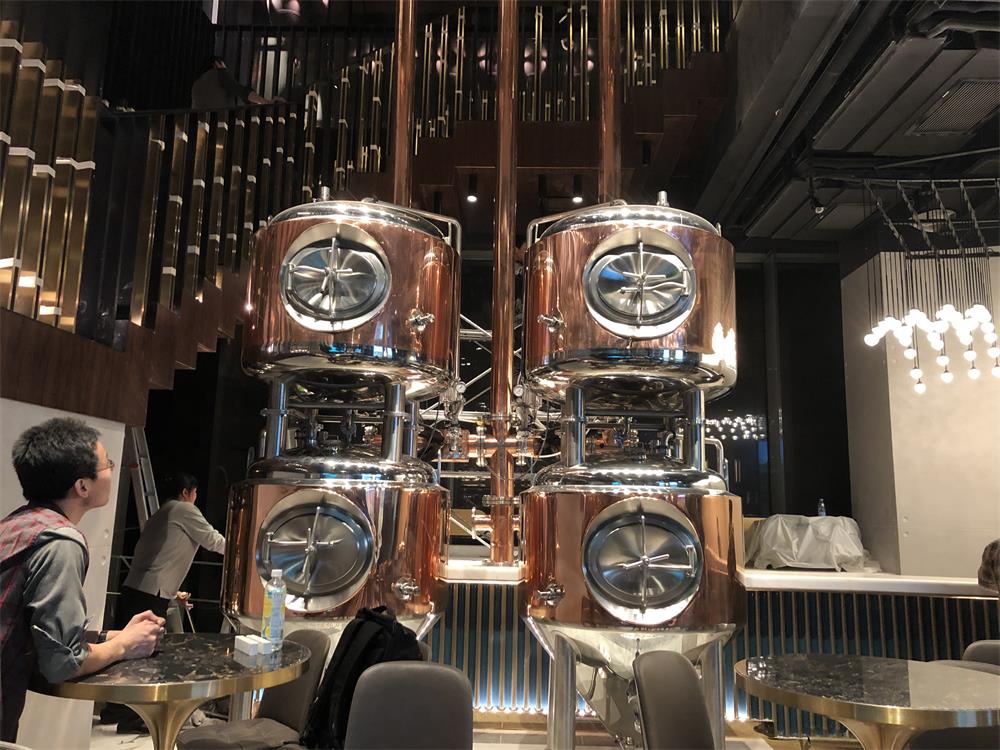
Limitations of 30 BBL System
Large Spaces – Requires at least 3000 sq ft floor space for all equipment. Height clearances also needed.
Specialized Staff – Brewers need technical expertise on operating and maintaining automated systems. Engineering support may be needed.
Capital Costs – Significant upfront investment needed for 30 BBL system compared to smaller 10-20 BBL setups.
Production Planning – Managing multiple batches per week across different beer varieties requires coordination of ingredients, schedules, inventory etc.
Maintenance – Preventive maintenance is essential but adds to overheads if done in-house. Hiring specialists has cost implications.
FAQ
How much beer can a 30 BBL brewhouse produce annually?
- At full utilization running 3 batches per week, annual production volumes around 4,500 to 10,000 barrels are feasible. This matches capacity expansion plans of many mid-sized breweries.
What types of craft breweries is a 30 BBL system best suited for?
- Typically adopted by brewpubs, microbreweries, and regional craft brewers aiming to expand distribution while retaining variety. The capacity aligns well with taproom needs plus retail keg and can sales.
What is the cost per barrel of beer produced on a 30 BBL system?
- Industry estimates indicate cost per barrel between $100 to $200 depending on scale, localization and staff productivity. Electric vs steam heating also impacts energy utilization costs.
What is the difference between 30 BBL and 20 BBL brewhouse equipment?
- While configurations are similar, a 30 BBL system has larger vessel capacities allowing 50% higher production per batch. This results in faster beer output which can cater to increasing demand.
What are the floor space needs for a 30 BBL brewhouse and fermentation room?
- Total floor space needed is between 3000 – 5000 sq ft for all equipment. The brewhouse vessels can fit in around 1000 sq ft area. Fermentation room is allocated 1200-2000 sq ft with sufficient clearance for tanks and cooling systems.
How many people are needed to operate a 30 BBL brewhouse system?
- Typically a team of 3-5 skilled brewers work together per shift to run the various brewhouse modules and transfer operations efficiently. In addition, cellarpersons handle fermentation while packaging operators work on canning lines.